鉄粉 鉄粉は、その磁気特性、高強度、延性、幅広い粉末サイズにより、様々な産業および商業用途に使用される汎用性の高い鉄系材料です。このガイドでは、鉄粉の種類、仕様、製造方法、用途、価格、比較、よくある質問について詳しく説明しています。
鉄粉の概要
鉄粉とは、金属鉄の微粒子を指し、通常500ミクロン以下の大きさである。高い透磁率を示し、磁気特性や構造特性を改良するために、ケイ素、ニッケル、モリブデン、銅などの合金元素を少量含むことが多い。
鉄粉を各産業分野で有用なものにしている主な特性:
- 高純度鉄含有率(>98%)
- 制御された粉末形態と粒径
- 電気抵抗値の範囲
- 調整可能な磁気特性
- 良好な加工性と圧縮性
- 機械的強度を調整する能力
- 商業的に大量に入手可能
- ソリッド鉄よりも低い製造コスト
- スクラップ/廃棄物粉末のリサイクル性
世界の鉄粉需要は年間800キロ・トンに達すると予測されており、鉄粉の生産量と種類は自動車、電気、ろう付け産業用途に牽引されて増加の一途をたどっている。
鉄粉の種類
鉄粉は一般に、組成、製造工程、粒子形状、粉末サイズ、粉末密度によって分類される:
表1: 鉄粉の主な種類
タイプ | 説明 |
---|---|
カルボニル鉄 | 鉄ペンタカルボニル分解による超微粒子高純度粉体 |
霧化された水 | ノズルから送り込まれた溶鉄の霧化によって作られる。 |
電解 | 鉄塩水溶液からカソードに析出 |
還元鉄 | ミルスケールを400~700℃でH2/CO還元して製造 |
アニール | 電解/水アトマイズ粉末をアニールして生成したソフトパウダー |
合金 | 粉末特性を改良するためのSi、Al、Cu、Moの少量添加 |
絶縁鉄 | 無機絶縁層で被覆された各粒子 |
砂鉄 | 鋳鉄を破砕・粉砕して作られた不規則な塊 |
形状:主に球状、樹枝状、粒状、不規則な塊状の粒子が見られる。
サイズ:10ミクロンから1ミリの間で、小さいほど高価。
見かけ密度2gr/ccの薄力粉、4gr/ccの圧粉。
組成だけでなく、特性は粉末の製造方法や、アニール、コーティング、潤滑剤添加などの後処理によっても決まる。
主な特徴と特性 鉄粉末
市販されている鉄粉は、物理的、化学的、電気的、磁気的特性において幅広いスペクトルを示す:
表2: 鉄粉の特性と試験測定法
プロパティ | 代表値 | 試験方法 |
---|---|---|
化学組成 | 98%鉄、0.8%酸素、0.1%窒素、0.1%C | 燃焼分析、蛍光X線分析 |
見かけ密度 | 2-4 gr/cc | ホール流量計 |
タップ密度 | 最大6.5 gr/cc | 結合分率 |
流量 | 凝集力は重力下での粉体の流れに影響する | ホール流量計 |
圧縮性 | グリーン圧縮率35~65%(一般的 | プレス金型テスト |
水素ロス | アニーリングで150ppm以下 | 不活性ガス融解法 |
透過性 | 70-150(焼きなまし鉄 | ヒステリシスグラフ検査 |
抵抗率 | 10-18 μΩ・cm;合金化により減少 | 4プローブ方式 |
損失係数 | 10 kHzで15 kW/m3以下 | ヒステリシスグラフ |
硬度 | 焼結後90HRBまで | ロックウェル硬度 |
産業用途への適合性を決定する主な要因:
- フロー特性
- 密度の一貫性
- 磁気ポテンシャル
- 製造適応性
- 純度
- 粒度分布
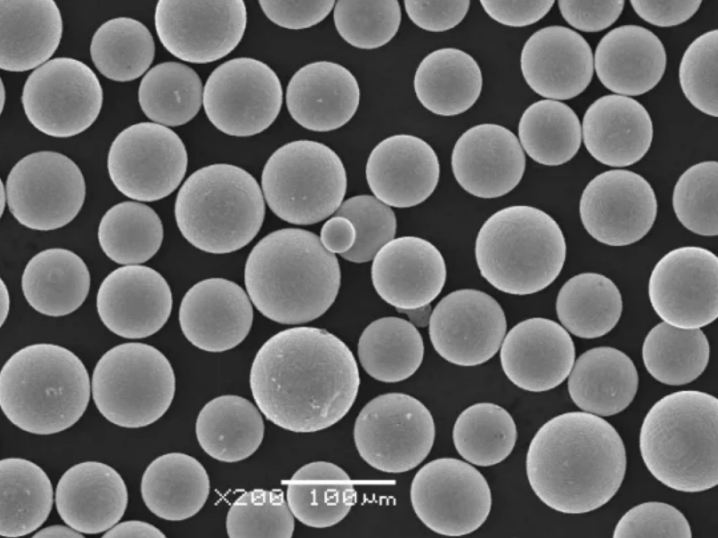
鉄粉の製造工程
さまざまなグレードの鉄粉を製造する主なルートは以下の通りである:
表3: 主要鉄粉製造プロセスの概要
方法 | 説明 | 典型的な出力 |
---|---|---|
ガス噴霧 | 窒素/アルゴンジェットで溶けた鉄の流れを分解 | 微細球状粉末 |
水の霧化 | 高圧水が鉄の溶融物を粒状に砕く | 不規則な樹枝状粉末 |
電解 | 正極にめっきされた水溶液中の鉄イオン | 軽いスポンジ状の堆積物 |
カルボニル分解 | 鉄ペンタカルボニルの熱分解 | 超微粉高純度パウダー |
機械的粉砕 | 鋳鉄・銑鉄の破砕・粉砕 | 大粒粉末 |
水素還元 | 水素雰囲気中で還元された酸化鉄粉 | 多孔質で密度の低いパウダー |
電着 | 溶解性陽極から陰極への鉄の電気めっき | 密度の高い付着性粉末 |
アニール、粉砕、分級、コーティング、潤滑などの製造後の二次工程は、粒径、形状、密度、流動特性などの粉末特性をさらに変化させることができる。
表4:鉄粉製造装置とシステムの業界プロバイダー
会社概要 | お供え物 |
---|---|
BASF | ガス噴霧装置 |
サンドビック・オスプレイ | 水噴霧ターンキーシステム |
イタルプロセス | 水素還元装置 |
ECKA顆粒 | アニール、粉砕、分級 |
ヘガネス | 完全な粉体製造ソリューション |
カストウェル | 粉体処理装置 |
ガス、水、水素ベースの還元プラントでは、200~2000kg/時の生産能力が一般的である。
鉄粉の用途と使用
鉄粉の主な工業用途と商業利用には、以下のようなものがある:
表5: 鉄粉の主な用途
産業 | 用途 |
---|---|
自動車 | 粉末冶金歯車、エンジンベアリング、オイルポンプ部品、ブレーキパッド、摩擦部品 |
電気 | フェライト、インダクター、電磁シールド、接点 |
建設 | 金属下地仕上げ用粉体塗料原料 |
製造業 | 複雑なネットシェイプ部品の粉末射出成形 |
ろ過 | 鉄媒体を用いたヒ素、クロム汚染物質除去のための水処理 |
印刷 | コピー機、レーザープリンター用トナーパウダー |
溶接 | 発熱を伴う溶接フラックス混合物のバインダー |
冶金学 | 鉄粉添加による焼結鋼の機械的性質の向上 |
ケミカル | 触媒および顔料の原料として使用 |
潤滑油 | ブレーキ液、トランスミッションオイルへの摩擦制御添加剤 |
電子レンジ | 電磁波吸収用鉄系損失性材料 |
このうち、粉末冶金と摩擦部品製造が現在、鉄粉消費量の50%以上を占めている。
鉄粉の仕様
鉄粉は、粒度、形状、密度、組成によって定義された様々な標準グレードで市販されている:
表6: 鉄粉グレードの代表的な仕様
属性 | レンジ |
---|---|
サイズ範囲(ミクロン) | 10~500 |
形状 | 球状、粒状、樹枝状 |
合金元素 | Cu:1-4%, Mo: 0.2-5%, Si: 0.1-6 |
見掛け密度(g/cc) | 2-4.5 |
タップ密度(g/cc) | 最大6.5 |
最小鉄アッセイ | 98% |
最大酸素 | 0.8% |
最大窒素 | 0.1% |
含水率 | 0.1 wt |
流量 | 凝集力は重力下での粉体の流れに影響する |
このほか、浸炭と絶縁鉄粉には、独自の用途に合わせた特別なグレードのサブセットがある。
鉄粉の国際規格
世界的に取引されている鉄粉は、工業規格に従って確立された品質パラメーターに適合している:
表7: 主な国際鉄粉グレード規格
スタンダード | 重要な側面の定義 |
---|---|
ISO 4491 | ホール流量計を用いて経験的に粉体流量を決定する方法 |
ISO 4490 | 嵩密度とタップ密度の測定手順 |
ISO 4497 | 粒度分布を測定するふるい分け技術 |
ASTM B831M | ふるい分けによる金属粉末の粒度分布の標準試験方法 |
JIS Z 2508 | 圧縮およびグリーン密度特性の測定方法を規定する日本規格 |
DIN 51733 | 粉体流動特性評価のためのドイツ標準試験手順 |
評判の良いメーカーは、ISO9001のような品質認証とともに、生産中およびユーザー受入のための化学的、機能的、物理的特性を検証するための設備の整った研究所を持っている。
サプライヤーと価格
鉄粉は、大手金属粉メーカーが大量生産する汎用製品であるため、現在の価格は以下のように変動している。 キログラム当たり1.5~5ドル をベースにした:
表8: 鉄粉の価格決定要因
パラメータ | 価格への影響 |
---|---|
生産工程 | 電解とカルボニルが最も高価 |
純度 | より高い純度がプレミアムを生む |
粉末密度 | 圧縮性が高いほど増加する |
粒子径 | より細かいパウダーはより高い |
購入数量 | 大量注文による割引 |
製品の一貫性 | 厳しい流通公差がコストを押し上げる |
合金元素 | ほとんどの合金グレードは追加料金 |
所在地 | 地域別運賃と関税 |
表9: 世界の主要サプライヤーと鉄粉の代表的な価格帯
会社概要 | 製品フォーム | 価格帯 |
---|---|---|
ヘガネス | 水噴霧、プレアロイ | 1.8~3.5ドル/kg |
BASF | カルボニル、電解、水アトマイズ | 2~4.8ドル/kg |
リオ・ティント | 水アトマイズ、アニール、水素還元 | 1.7~3ドル/kg |
中国石油天然気集団公司 | 電解、合金グレード | 1.5~2.5ドル/kg |
JFEスチール | カルボニル、合金化アトマイズ | 2~5ドル/kg |
サンドビック・オスプレイ | ガス噴霧 | 3.5~5ドル/kg |
アメテック | ファイン・ステンレス・スチール・クラッド | 5~7ドル/kg |
価格は年間契約量と保証される仕様の幅によって異なります。鉄粉の調達においては、単に最低価格水準を追い求めるよりも、品質の一貫性と認証を優先してください。
長所と短所 鉄粉末
表10: 鉄粉の利点と限界の比較
メリット | デメリット |
---|---|
経済的な素材と加工 | 鋳造/鍛造の特性とは一致しない場合がある |
ネット状に成形しやすい | スチール合金より強度が低い |
透磁率の範囲 | 保護加工を施さないと錆びやすい |
他のフェライトよりも高い延性 | シートメタル加工用の限られた成形性 |
リサイクル可能なスクラップの処理 | 粉体の取り扱いに関する注意事項 |
加工によって調整可能な均一性 | ロット間における特性のばらつきの可能性 |
スプロケットやギヤのような小さな複雑部品の場合、粉末冶金ル ートは、機械的強度が低いことを考慮しても、コスト面で大きな利点を もたらす。しかし、大型の構造物には、従来の鋳造や鋼の変形加工が適している。
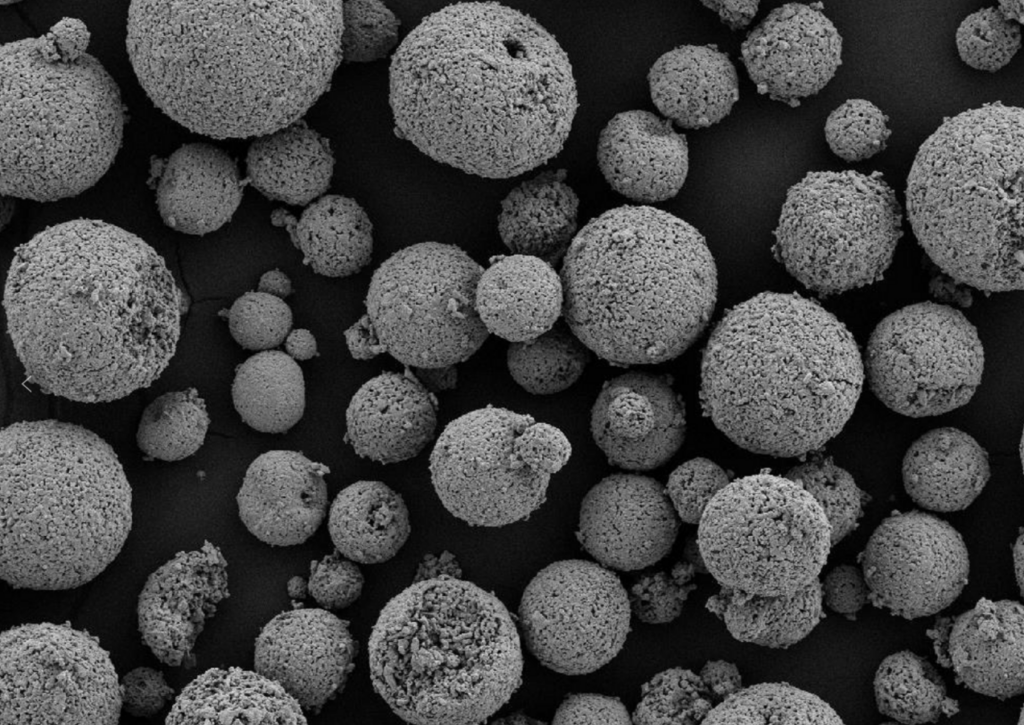
よくある質問
Q.鉄粉は粒度によってどのように分類されますか?
鉄粉は、メッシュサイズによって商業的に次のように分類される:
- 粗目等級 – 100 メッシュサイズ (149 ミクロン) 未満
- ファイングレード – 100 から 400 メッシュ (37 から 149 ミクロン)
- ウルトラファイングレード – 400メッシュ以上、37ミクロン以下
Q.最も純度の高い鉄粉はどのグレードですか?
カルボニル鉄粉や電解鉄粉では99.5%以上の純度が可能です。アトマイズ法では、純度98%以上。
Q.見かけ密度とタップ密度の違いは何ですか?
見掛け密度とは、穏やかに攪拌した後に測定されるルースパッキンのことであり、タップ密度とは、荷重をかけた測定シリンダーを機械的にタッピングした後に達成される圧縮度の増加のことである。
Q.なぜ流量は重要な鉄粉パラメータなのですか?
良好なパウダーフローは、金属射出成形のような、材料が重力下で金型に自由に流れ込まなければならない部品成形や冶金プロセスにおいて、容易性、一貫性、自動化適性を保証する。