ヒップ・メタル・パウダー とは、股関節インプラントや人工関節用の新しい金属積層造形技術で使用される特殊な球状粉末のことである。このガイドでは、一般的な合金、特性、用途、仕様、サプライヤーについて説明します。
ヒップメタルパウダーの概要
人工股関節パウダーとも呼ばれるこれらの先端材料は、複雑な形状と従来のインプラントを凌ぐ機械的性能を持つ、患者固有の人工股関節コンポーネントの3Dプリントを可能にする。
ヒップメタルパウダーの主な特徴は以下の通り:
プロパティ | 特徴 |
---|---|
合金 | チタン、コバルトクロム、ステンレススチール |
粒子形状 | 球形度が高い |
サイズ分布 | 標準15-45ミクロン |
密度 | 展延性とパッキングの最適化 |
主な属性 | 生体適合性、高強度、耐食性、生体内で実証された性能 |
製造工程 | 積層造形 – バインダ噴射、DED、PBF |
用途 | ヒップカップ、ステム、寛骨臼ライナーおよびシェル |
ヒップパウダーは、3Dプリント整形外科インプラントの性能、寿命、生体適合性を高めるために進歩し続けている。
合金の種類
一般的なヒップメタルパウダーには以下のようなものがある:
合金 | 構成 | プロパティ |
---|---|---|
チタン Ti64 | チタン、アルミニウム、バナジウム | 高強度対重量、生体不活性 |
コバルト・クローム | コバルト、クロム、モリブデン | 耐摩耗性、耐食性 |
ステンレス鋼 | 鉄、クロム、ニッケル、モリブデン | 費用対効果、加工性 |
新興合金
TMZF®チタン-モリブデン-ジルコニウム-鉄のような新しい合金は、選択的レーザー溶融によって機械的性能と骨統合能力を調整する。
機械的特性
ヒップメタル粉末は、積層造形時に以下のASTM規格の特性を達成することが可能です:
プロパティ | 共通の価値観 |
---|---|
引張強さ | 750-1300 MPa |
降伏強度 | 450-1150 MPa |
破断伸度 | 8-25% |
硬度 | 280-550 HV |
表面粗さ(Ra) | 骨の成長に最適化 |
機械的性能は、AM印刷中の層厚、レーザー出力、スキャン速度などのパラメーターに依存する。
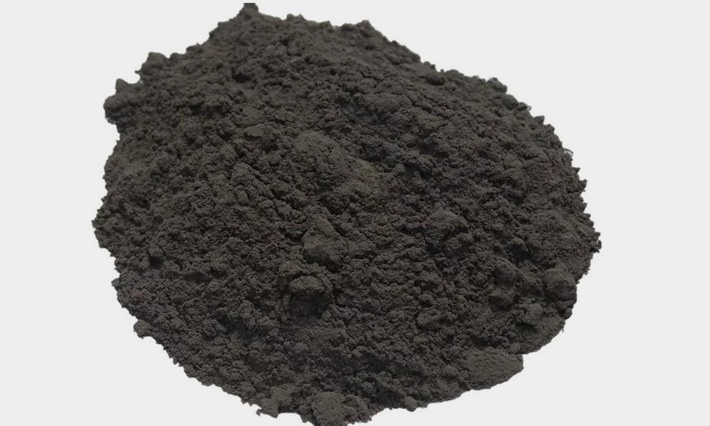
用途
ヒップメタルパウダーの代表的な用途は多岐にわたる:
コンポーネント | 詳細 |
---|---|
ヒップカップ | 骨との一体化のために半球形状とテクスチャー加工が施された臼蓋コンポーネント |
大腿骨ステム | 大腿骨内に伸展し、ヒップカップコンポーネントに固定される |
ライナーとシェル | ライナーはアウターシェルに固定され、超低着圧の関節面を提供する。 |
メリット
カスタム・マッチングされた股関節パウダー・コンポーネントは、最適化されることで寿命を向上させ、人工股関節置換術を遅らせたり予防したりする:
- 骨の固定と成長
- 摩耗粉の発生が少ない
- セメント界面の弱点の除去
仕様
ヒップ・メタル・パウダー は、ISOおよびASTM規格に基づく以下の最低仕様を満たさなければならない:
属性 | 仕様制限 |
---|---|
合金組成 | 等級規格(AMS/UNS)に基づく |
粒子径 | 10~45ミクロン |
見かけ密度 | ≥ 合金の80%以上 |
流量 | 25~50秒/50g |
球形度 | ≥ 0.9 以上が望ましい |
特殊なヒップパウダーは、粒子形状、内部構造、表面化学を最適化することで、印刷時の完璧な展延性、充填性、焼結挙動を実現し、これらをさらに一歩進めます。
サプライヤー
股関節用金属粉末の世界的な大手サプライヤーには、以下のようなものがある:
サプライヤー | 共通グレード | 価格見積もり |
---|---|---|
AP&C | Ti64, CoCr, スチール | 500~1500ドル/kg |
カーペンター添加剤 | Ti64、CoCrMo | 800~2000ドル/kg |
プラクセア | Ti64、CoCr、SS316L | 600~1800ドル/kg |
サンドビック・オスプレイ | Ti6AL4V ELI、CoCr ASTM F75 | 750~2500ドル/kg |
価格は注文量、粉末の仕様、選択した合金によって異なります。AM用にカスタマイズされたヒップパウダーの中には、1kgあたり3000~5000ドル以上するものもあります。
長所と短所
長所 | 短所 |
---|---|
複雑なカスタマイズ形状 | 現在高いハードウェアコスト |
最適化された機械的特性 | 長期臨床データが限られている |
新しい多孔質構造を可能にする | 新たなオプションの保険料負担が制限される |
失敗したインプラントの再手術を簡素化 | 必要な後処理工程 |
手術ロジスティクスの合理化 | 償還経路をめぐる不確実性 |
要点
- 大手金属メーカーがバインダージェットとレーザーベースの印刷に最適化したヒップパウダーを提供開始
- 新しい合金と構造により、従来のインプラントより性能が向上する
- 安全性と有効性に関する臨床エビデンスが構築され続けている
よくある質問
Q: 現在、整形外科用インプラントで金属3Dプリンターを使用しているものはどのくらいありますか?
A: 現在、股関節、膝関節、脊椎インプラントなどの整形外科用器具の4~5%が、高級金属粉末から付加製造されていると推定される。しかし、採用は飛躍的に増加すると予想されます。
Q: プリントインプラントによる金属腐食やイオンの懸念はありますか?
A: すべての金属インプラントには腐食や破片の可能性がありますが、合金、製造管理、表面処理の進歩により、現在では従来の鋳造/鍛造ベースのインプラントと同程度にリスクを最小限に抑えています。
Q:パンデミックによって、メタルプリントオプションを含む人工関節置換術へのアクセスはどのように阻害されましたか?
A: 人工股関節置換術と人工膝関節置換術の一時的な中断により、人工股関節置換術と人工膝関節置換術は大幅に制限された。しかし、3Dプリンターによるアプローチの利点に対する外科医の意識の高まりとともに、アクセスは回復しつつある。
Q:3Dプリンターによるインプラントは、従来の人工股関節置換術に比べてコストを削減できるのでしょうか?
A: 現在、プリント・インプラントは、ジェネリック・インプラントよりも割高な価格設定となっているが、臨床的性能の利点を考慮すれば、価値ベースの価格設定が可能である。さらに普及が進めば、製造のスケールメリットにより費用対効果が高まる可能性がある。