はじめに
金属霧化技術 は、溶融金属をガスまたは水を使用して非常に微細な液滴に分解することにより、金属を液体から粉末状に変換するプロセスである。液滴は急速に凝固し、粒径5 &8211; 500 μmの粉末粒子になります。アトマイズ技術は、精密な粒度分布、組成、形態を持つ金属粉末の製造を可能にしました。金属粉末は、粉末冶金、溶射、金属積層造形などの部品製造に応用されています。この記事では、アトマイズの様々な方法、アトマイズされた粉末の特性、そして様々な産業における応用について概観する。
金属アトマイズ技術
金属の霧化には主に2つの技術がある:
ガス噴霧
ガスアトマイズでは、溶融金属流は通常窒素またはアルゴンの高速ガスジェットによって分解される。ガスアトマイズ装置は、溶融物供給システム、アトマイズチャンバー、および粉末回収システムから構成される。メルトデリバリーシステムはタンディッシュまたはルツボで、底部にノズルがあり、そこから溶融金属が流出する。ノズルを出た金属流は、溶融流に対して放射状または平行に配置された高圧ガスジェットによって衝突される。ガスジェットによって溶融金属は微細な液滴に分解され、この液滴は凝固しながら捕集室へと流下する。
ガスアトマイズの主な利点は以下の通り:
- 平均粒径20μmまでの微粉末が製造可能。粒度分布が狭い。
- ガスアトマイズ粉末は、焼結用途に理想的な丸みを帯びた粒子形態をしています。
- 不活性雰囲気で処理するため、チタンやアルミニウムのような反応性金属もアトマイズできる。
- 複数のガスジェットにより、大量の粉体を連続的に生産することができる。
しかし、ガス噴霧は高い設備投資を必要とし、ガス消費量が多いためランニングコストも高い。
水の霧化
水アトマイズでは、ノズルから出る溶融金属流は、上方または側面から噴射される水によって分解される。水アトマイズは不活性ガスを必要とせず、より単純なプロセスである。しかし、粒子径の範囲は100 – 500 μmであり、粉末粒子の形態は不規則である。主な用途は、金属部品の粉体塗装です。
水アトマイズ粉末は微粉末にできないため、粉末冶金での用途は限られている。しかし、水アトマイズはガスアトマイズに比べて経済的である。
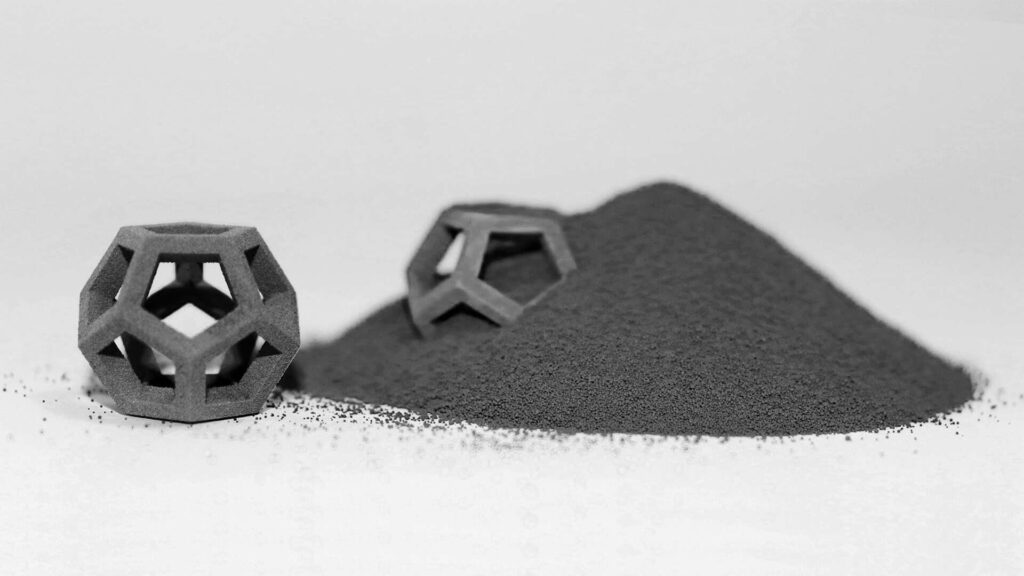
アトマイズ粉の特徴
アトマイズされた金属粉末の特性は、金属合金の組成とアトマイズプロセスパラメータに依存する。プロセスパラメーターを最適化することにより、所望の特性を持つ粉末を製造することができる。
粒子径と形状
- ガスアトマイズ粉末の粒径は、水アトマイズ粉末(100–500μm)に比べて5–150μmと小さい。
- 水アトマイズ粒子は不規則な形状をしているが、ガスアトマイズ粉末はより球状の形態をしている。
- 粒度分布は重要なパラメータである。金属積層造形のような用途では、分布が狭い方が好ましい。
純度
- 制御された雰囲気下で行われるガスアトマイズは、粉末中に合金の化学的性質を保持する。
- 水噴霧パウダーは、酸素吸収によるコンタミネーションが発生する可能性がある。
- 微粉末は表面積が大きく、空気中で扱うと容易に酸化する。酸化を防ぐために不動態化処理が施される。
密度
- アトマイズ中の急速な凝固により、微細構造が洗練される。粉末粒子の気孔率が低い。
- ガスアトマイズ粉末は、水アトマイズ粉末よりも密度が高い。
- アトマイズ粉末の閉鎖気孔は、圧縮時の圧縮性を向上させる。
流動性
- 不規則な粒子形状と広い粒度分布は、水噴霧粉末の流動不良を引き起こす。
- ガスアトマイズで製造された微細な球状粉末は流動性が良い。
コスト
- ガスアトマイズ粉は水アトマイズ粉より10倍高い。
- すなわち、チタンのような反応性の合金はコストが高い。
- 粉が細かいほどコストは高くなる。非常に微細なパウダーほど、コストは指数関数的に上昇する。
アトマイズ金属粉の用途
アトマイズパウダーのユニークな特性は、製造業全般での利用を可能にしてきた。
粉末冶金
アトマイズパウダーは、ベアリング、ギア、マグネットなどの精密部品を製造するために圧縮・焼結されます。重要な要件は以下の通りです:
- 球形で粒度分布が狭いため、高密度で均一な成形が可能。
- 焼結密度を高める微粉末(<100μm)
- 焼結後の気孔率を最小化する低酸素含有量
金属積層造形
3Dプリンティングとしても知られ、アトマイズパウダーの最も急速に成長している用途のひとつである。主な材料要件
- 良好な流動性のための球状粉末形態
- 粒子径15~45μmで精度と表面仕上げを実現
- 均一な層堆積と密度のための狭いサイズ分布
- 優れた機械的特性のための低酸素含有量
チタンとニッケルの超合金がよく使われる。
溶射コーティング
プラズマ溶射、フレーム溶射などの溶射プロセスでは、噴霧化した粉末を加熱して溶融させ、部品表面に溶射する。コーティングは耐摩耗性と耐食性を提供する。パウダーの特徴
- スプレー技術に適した粒子径範囲 (10 &8211; 100 μm)
- 酸素含有量が低いため、コーティング密度と接着強度が高い
- コストが重要なので、一般的に使用されている水噴霧式パウダー
金属射出成形(MIM)
MIMは、プラスチック射出成形と粉末冶金の長所を組み合わせて、小型で複雑な金属部品を製造する。原料準備では、微細な金属粉末とバインダーを混合する。必要条件
- バインダーと均一に混合するための20μm以下の粒子径
- 成形時の流れを改善する球状形態
- 狭いサイズ分布
霧化技術の進歩
継続的な研究により、カスタマイズされた特性や新しい合金を持つ粉末を製造するための噴霧化技術が開発されてきた。主なトレンドは以下の通り:
- より微粒化された粉体を製造するための複数のガスノズル構成
- チタン、アルミニウムのような反応性合金への密着噴霧の使用
- ガス霧化と水霧化を組み合わせたハイブリッド霧化
- 水アトマイズ時の酸化を制御して粉体特性を改善
- 遠心霧化、超音波霧化技術による霧化
- 微粒化プロセスを最適化するための液滴凝固のコンピュータシミュレーション
新しい軽量高強度合金の開発も、アトマイズ粉末の応用分野を広げている。
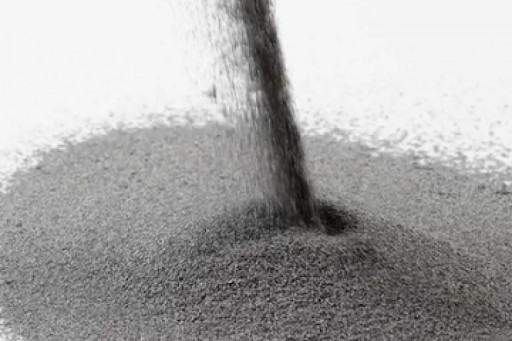
結論
金属微粒化技術は、高度な粉末ベースの製造工程に適した、微細で精密な形状の金属粉末を製造します。粉末の特性を制御する能力により、アトマイズ粉末は自動車、航空宇宙、生物医学、その他の産業にわたる高性能部品への応用が拡大している。現在進行中の進歩により、アトマイズ粉末を使用したテーラーメイド材料の製造が可能になる。
よくある質問
金属の霧化にはどのような方法がありますか?
主な方法は、ガスアトマイズと水アトマイズの2つである。ガスアトマイズでは、溶融金属は窒素やアルゴンなどの不活性ガスの高速ジェットによって微細な液滴に分解される。水アトマイズでは、水の噴流がノズル先端から出る溶融金属の流れに衝突する。
アトマイズできる金属は?
アルミニウム、銅、鉄、ニッケルなどをベースとする合金のほとんどは、容易にアトマイズできる。チタンやマグネシウムのような反応性合金も、ガスアトマイズ装置で制御された雰囲気を使用してアトマイズすることができます。例えば、アルミニウム合金、ステンレス鋼、ニッケル超合金、チタン合金などです。
アトマイズ金属粉の主な用途は?
重要な用途は、粉末冶金部品製造、3Dプリンティングによる金属積層造形、溶射コーティング、小型精密部品の金属射出成形、粉末鍛造、金属フレークやペーストの製造などである。
ガスアトマイズは、水アトマイズに比べてどのように粉体を細かくするのですか?
ガスアトマイズでは、高速のガスジェットが金属流を5~50ミクロン程度の非常に微細な液滴に分解するのに十分な運動量を持つ。また、ガスアトマイズでは冷却速度が速いため、より微細な液滴への分解が容易です。水アトマイズでは、ウォータージェットの速度が低いため、100ミクロン以上の粗い粉末になります。
ガス噴霧式と水噴霧式の粉体の典型的なコストの違いは何ですか?
ガスアトマイズ粉体は、水アトマイズ粉体よりも約10倍高価である。これは、ガスアトマイズが非常に高い設備投資とガス消費による高い運転コストを必要とするためである。それに比べ、水アトマイズ装置は設置も運転も安価である。