概要 3Dプリントタングステン
ウォルフラムとしても知られるタングステンは、高温強度に優れ、高剛性、耐摩耗性、または1000℃までの高温性能を必要とする用途に理想的な、硬くて緻密な金属です。タングステンの密度は19.3g/cm3で、鋼の2倍の密度を持ち、純ウランに近い密度を持つ。
タングステンやタングステン合金の3Dプリンティングでは、従来の製造方法では不可能だった複雑な形状の部品を製造することができます。タングステンの高い剛性と耐摩耗性は、金型工具、電極、放射線遮蔽部品、バラストウェイト、および高密度の材料特性を必要とするその他の用途の3Dプリントに適しています。
タングステンは、選択的レーザー溶融(SLM)や電子ビーム溶融(EBM)などの粉末床溶融技術を使用して3Dプリントすることができます。どちらの方法も、タングステン粉末の層を選択的に溶融して、固体の3Dパーツを構築します。の主な考慮事項 3Dプリントタングステン 部品設計、パウダー選択、印刷プロセスパラメーター、後処理、材料特性など。
この記事では、タングステンのカバーを使用した3Dプリントの完全ガイドを提供します:
- 3Dプリントタングステン部品の主な用途
- タングステン金属粉末の種類
- 選択的レーザー溶融および電子ビーム溶融プロセスの概要
- 印刷パラメータと考慮事項
- 後処理手順
- 機械的特性と微細構造
- サプライヤーとコスト分析
- 設計の原則と限界
- 代替製造プロセスとの比較
- 技術の長所と短所
3Dプリントタングステン部品の主な用途
タングステンは、高密度、高剛性、高硬度、高耐熱性を必要とする製品の3Dプリンティングに応用されています。代表的な用途は以下の通り:
申し込み | 説明 |
---|---|
放射線遮蔽 | タングステンの密度は有害なガンマ線やX線を遮断します。医療、原子力、航空宇宙分野で使用される。 |
振動減衰 | タングステンの密度が振動を効果的に減衰させます。精密機器に使用される。 |
バラスト重量 | 高密度バランスでシステムを正確に校正。 |
電極コンタクト | アーク放電に耐える。電気接点および真空遮断器に使用。 |
自動車 | 高性能自動車部品におけるタングステン合金。 |
鉱業 | 耐摩耗性炭化タングステンの採鉱および掘削工具。 |
航空宇宙 | ロケットノズル、タービンブレード、その他の高温部品。 |
ミリタリー | 運動エネルギー貫通弾、徹甲弾。 |
メディカル | 高剛性メス、歯科用工具、骨ネジ。 |
3Dプリンティングは、サブトラクティブ加工では実現不可能な複雑なタングステン部品形状を可能にし、高性能な金属特性を必要とする産業分野での用途を拡大する。
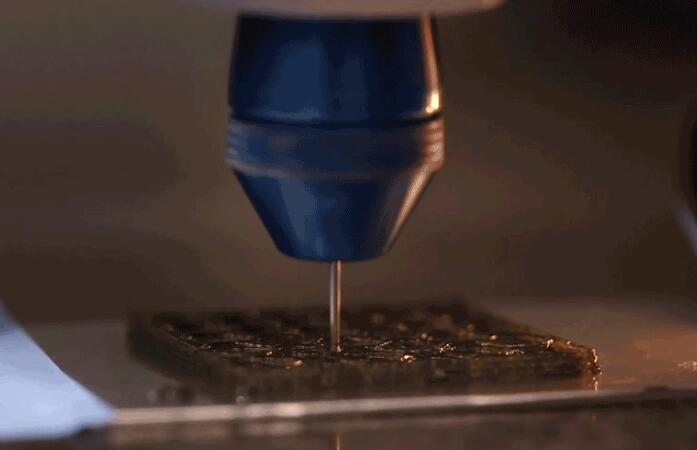
3Dプリンティング用タングステン金属粉末の種類
タングステンは、粉末床溶融3Dプリンティングプロセスで使用するために、さまざまな粉末タイプで利用可能です:
パウダータイプ | 説明 | 粒子形状 | 粒子サイズ |
---|---|---|---|
純タングステン | 元素状タングステン、純度99.9 | 球形 | 15-45ミクロン |
炭化タングステン | 炭化タングステン-コバルト・サーメット | 球形/不規則 | 45~150ミクロン |
タングステン合金 | タングステンとニッケル、鉄、銅との重合金 | 球形 | 15-45ミクロン |
純粋なタングステンは、タングステン合金に比べて、その高い溶融温度のためにレーザー粉末床溶融に適しています。炭化タングステングレードは、コバルトバインダーを含み、より硬いですが、加工がより困難です。EBMでは、150ミクロンまでの粗い粉末を使用することができます。
球状パウダーは優れた流動性と充填密度を提供します。45ミクロン以下の小さな粒子径は、解像度、表面仕上げ、焼結を向上させます。しかし、非常に微細な粉末の取り扱いには、粉末の燃焼性に注意が必要です。
タングステンの選択的レーザー溶融プロセスの概要
選択的レーザー溶融(SLM)は、レーザービームを使用して、タングステン粉末層の領域を選択的に融合させ、3Dオブジェクトを層ごとに構築する。このプロセスは、酸化を防ぐために酸素濃度が0.1%以下の不活性ガス・チャンバー内で行われる。
SLMプロセスのステップ:
- タングステン粉末は、リコーターアームを使ってビルドプレート上に薄く広げられる。
- レーザービームは各層をトレースし、粉末を融点以上に加熱して溶融固体領域を形成する。
- ビルドプレートが少し下がり、新しいパウダー層が前の層の上に広がる。
- タングステン金属粉末から完全な部品が作り上げられるまで、この手順を繰り返す。
- 未溶融パウダーは、印刷中のオーバーハングやアンダーカットをサポートし、印刷後にリサイクルされる。
- 局所的な粉末スポットをレーザーで溶かすことで、最高3000℃の高温が発生する。
- その後、部品はパウダーケーキから取り出され、後処理される。
SLMは、鋳造や機械加工では不可能な複雑な形状を、3D CADモデルから直接プリントすることができます。0.02~0.05mmの微細な解像度と滑らかな表面が得られます。
タングステンの主なSLM印刷プロセスパラメータ
微細構造と機械的特性を制御した高密度タングステン部品を実現するには、SLMプリント・パラメーターの最適化が重要である。
印刷パラメータ | 典型的な範囲 | 役割 |
---|---|---|
レーザー出力 (W) | 100-400 W | パウダーを効率よく溶かすパワーが高いほどビルドレートが向上する。 |
スキャン速度(mm/s) | 100-1000 mm/s | 各層を横切るレーザーの速度。エネルギー入力に影響する。 |
ハッチ間隔(μm) | 50-200 μm | スキャンライン間の距離。重なりと密度に影響する。 |
層厚(μm) | 20-100 μm | 薄いレイヤーは解像度を向上させるが、ビルドは遅くなる。 |
フォーカスオフセット(mm) | 0~-2 mm | より広いメルトプールとより良いレイヤーボンディングのためにスポットをデフォーカスする。 |
予熱温度 (°C) | 100-400 °C | パウダーベッドを加熱して熱応力を低減。層の結合を改善します。 |
これらのパラメータは、急峻な熱勾配による残留応力を最小限に抑えながら、溶融に十分なエネルギーを供給するためにバランスされなければならない。
SLMタングステン部品の後処理方法
SLM造形工程の後、完成したタングステン部品を得るためには、さらに後処理が必要である:
- パウダーベッドからの取り出し – 部品は周囲の固まらない粉から慎重に掘り出される。
- サポート解除 – サポートは手作業で切断されるか、化学的に溶解される。
- 熱応力緩和 – 1000-1500℃のアニール処理により残留応力が緩和され、延性が向上する。
- 熱間静水圧プレス – 2000℃以上でのHIP処理は、微細構造をさらに緻密化する。
- 機械加工 CNCフライス加工は、より厳しい公差と表面仕上げを実現します。
- 表面処理 – 金属コーティングや研磨は、表面特性を向上させることができます。
必要な寸法精度、微細構造、材料特性を印刷後の状態で達成するためには、適切な後処理が鍵となる。
SLMタングステンの機械的特性
選択的レーザー溶融は、溶製材に近い特性を持つ、ほぼ完全な高密度のタングステン部品を製造します:
プロパティ | SLMタングステン | 鍛造タングステン |
---|---|---|
密度 | 理論値99%以上 | 99.9% |
引張強さ | 450~650MPa | 550 MPa |
降伏強度 | 400~500MPa | 500 MPa |
伸び | 3~8 | 10% |
硬度 | 300~400 HV | 340 HV |
熱伝導率 | 140~180 W/mK | 174 W/mK |
急速凝固による超微細組織は、非常に高い硬度と強度をもたらします。しかし、亀裂に敏感なタングステンは、延性を向上させるために熱間静水圧プレスと焼鈍が必要です。
SLMタングステンの微細構造
製造されたままのSLMタングステンの微細構造は、幅5~10ミクロン、長さ数百ミクロンの微細な柱状のβ-タングステン粒で構成されている。
カラム内では、レーザー走査中の複雑な熱サイクルの結果、最大幅500nmのセル状サブグレイン構造が観察される。微細構造には、ナノスケールの細孔と粒界間の未溶融粒子を伴う高い転位密度が含まれる。
ポストプロセス焼鈍は、この柱状構造を再結晶させ、内部応力と転位密度を低減した幅50ミクロン以上の均一で粗いタングステン粒にします。
選択的レーザー溶融と電子ビーム溶融の比較
電子ビーム溶解(EBM)は、レーザーの代わりに電子ビーム熱源を使用する代替粉末溶融プロセスである。
比較 | SLM | EBM |
---|---|---|
熱源 | レーザー | 電子ビーム |
雰囲気 | アルゴン | 真空 |
ビーム制御 | ガルボスキャナー | 電磁コイル |
最大ビルドサイズ | 250 x 250 x 300 mm | 200 x 200 x 350 mm |
決議 | 50 μm | 70 μm |
精度 | ±100 μm | ±150 μm |
表面仕上げ | 粗削り、加工後は滑らか | ざらざらした質感 |
SLMの高速ビーム走査は、より微細な分解能と表面仕上げを可能にします。EBMの利点は、造形速度が速く、真空中での粉末の取り扱いが簡単なことです。
3Dプリンティング用タングステンパウダーのサプライヤー
様々なメーカーが、粉末床溶融3Dプリンティング用のタングステン粉末を供給している:
サプライヤー | パウダーの種類 | 粒子サイズ | 価格 |
---|---|---|---|
バッファロー・タングステン | 純タングステン、タングステンカーバイド | 10-44 μm | 100~200ドル/kg |
中西部タングステン | 純タングステン | 10-40 μm | kgあたり80~250ドル |
H.C.スタルク | 純タングステン、タングステン合金 | 15-45 μm | 150~350ドル/kg |
南京タングステン | 純タングステン | 15-45 μm | 100~250ドル/kg |
ティラナ・リソース | 純タングステン | 45μm以下 | 250~400ドル/kg |
パウダーのコストは、低純度のもので80ドル/kgから、高精度グレードでは400ドル/kgを超える。製造中に未溶融の粉末としてかなりの材料が無駄になる。
3Dプリントタングステン部品のコスト分析
タングステン部品のSLM製造コストの内訳は以下の通り:
コスト・コンポーネント | 一般的な見積もり |
---|---|
タングステン粉 | kgあたり100~250ドル |
その他の原材料 | 1体あたり2~10ドル |
機械使用料 | 1時間あたり50~150ドル |
労働 | 時給40~100ドル |
後処理 | 1部品につき20~50ドル |
部品コスト合計 | 100gあたり100ドルから、複雑な大型部品の場合は5000ドルまで |
100g以下の小さな部品であれば、1個あたり100ドルのコストがかかると予想される。より大型で複雑な部品では、製造時間が長く、原材料を大量に消費するため、最大5000ドルかかることもある。
機械加工に比べ、タングステンの3Dプリンティングは部品コストが高いが、これまで不可能だった部品形状が可能になる。
SLMタングステン部品の設計原則
3Dプリンティングの能力を活用し、タングステンを使用する際の欠陥を回避するには、最適な部品設計が重要です:
- 残留応力によるひび割れを防ぐため、2mm以上の厚い壁や構造を使用する。
- 支持構造を必要とする張り出した形状を最小限に抑える。
- 応力集中を避けるため、逃がし穴、丸穴、フィレットを設ける。
- 密閉された容積を格子構造として設計し、粉体除去を改善する。
- 支持されていない張り出しを最小限にし、変形しやすい細長い部分を避けるように、部品の向きを決める。
- 印刷公差を100μm程度とし、それに応じてパーツのスケールを調整する。
- 精密な嵌合を達成するために、機械加工後の嵌合面を設計する。
- 設計の自由度を活用 – アセンブリを単一の複雑な部品に統合します。
熱および構造シミュレーションを実行し、設計中に残留応力の高い領域を特定。後処理で損傷を受けやすいデリケートなフィーチャーを回避。
タングステンで3Dプリントする場合の限界
タングステンはその長所にもかかわらず、粉末床溶融プロセスには課題もある:
- 高密度のタングステンはレーザーエネルギーを反射し、吸収率とビルドレートを制限する。
- 熱伝導率が低いと、熱がこもって部品が歪む。
- 高温と、加工中の酸素/窒素との反応性。
- 部品は、割れやすい脆いアズプリント微細構造に悩まされる。
- 錬金に近い特性を得るためには、かなりの後処理が必要である。
- 最大部品サイズは、プリンタの造形量によって制限されます。
- 垂直面は仕上げが悪く、機械加工が必要。
- 比較的高価な粉末材料がコストを押し上げる。
高品質のタングステン部品の印刷を成功させるには、入念な工程管理が必要である。
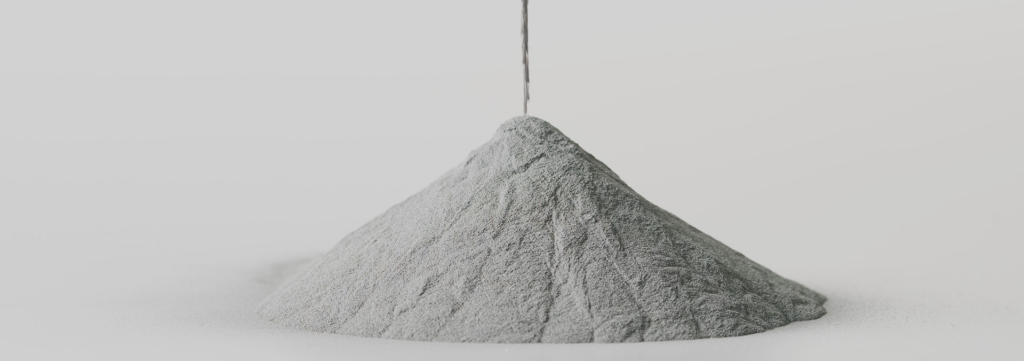
の利点 3Dプリントタングステン 部品
タングステンによる積層造形の主な利点は以下の通り:
- 複雑な形状 タングステンの鋳造や機械加工では不可能な複雑なデザインが可能です。
- 連結アセンブリ – 複数のコンポーネントを1つのプリント部品に統合する。
- マス・カスタマイゼーション アプリケーションごとに設計を簡単に変更および最適化できます。
- 軽量化 – 減算法では実現不可能な軽量格子や内部構造を作成する。
- 高い硬度 アズプリント部品は、最高400HVの硬度を達成。
- 迅速なターンアラウンド – 従来のツーリング方法と比較して、開発時間を短縮。
- パート統合 – アセンブリを単一の複雑なコンポーネントに結合します。
- 廃棄物ゼロ – 未溶融の粉末は、廃棄されるのではなく、再利用される。
3Dプリンティングは、高性能の金属特性を必要とするあらゆる産業において、タングステンの革新的な新用途を切り開きます。
3dプリントタングステンの欠点と限界
- 高コスト タングステンパウダーは高価である。タングステン粉は高価です。
- 低延性 – プリントしたままのタングステンは、後処理をしないと割れやすい。
- 限定サイズ – プリンタのビルドボリュームにより、部品の最大寸法が制限されます。
- 粗い表面 – 垂直面の仕上げが悪く、機械加工が必要。
- 長いプロセス – 印刷と後処理にかかる時間は、生産量に対して遅い。
- パラメーター感度 欠陥のないビルドを達成するには、大規模な微調整が必要です。
- 安全上の問題 タングステン粉末の取り扱いには、引火性に対する保護具が必要である。
3dプリントタングステンは、性能がコストを上回る複雑で高価な部品の少量生産に最適です。
3dプリント用タングステンの未来
タングステンを使った積層造形は、今後さらに成長するだろう:
- 利用可能なタングステン合金と複合材料の範囲を拡大。
- より大きなマシンビルドサイズが、より大きなプリントパーツを可能にする。
- 粉体の再利用とリサイクルを改善し、材料コストを削減。
- 印刷と機械加工を組み合わせたハイブリッド製造。
- プロセス-微細構造-物性の関係の理解を深める。
- 航空宇宙、防衛、自動車、医療分野での新たな応用。
- 大きなニアネットシェイプ部品を印刷するためのDED(Directed Energy Deposition)プロセス。
- 印刷パラメータ、資格、認証の標準化。
普及が進めば、3Dプリンターで作られたタングステン製の部品は、プロトタイプから幅広い生産用途へと移行するだろう。
結論
3Dプリンティングは、従来の技術では実現不可能な複雑な形状の高性能タングステン部品を製造する革新的な方法を提供します。放射線遮蔽やバラストウェイトから、電極や航空宇宙部品まで、幅広い用途があります。
選択的レーザー溶融プロセスでは、粉末層からほぼ完全な高密度のタングステン部品を製造することができますが、特性と性能には、印刷パラメータと後処理を慎重に最適化することが重要です。コストはまだ制限事項ですが、3Dプリントタングステンは、産業界全体で斬新なデザインとカスタマイズの可能性を解き放ちます。
プロセスが改善され続け、新しいタングステン合金が開発されるにつれて、積層造形は、超高密度、剛性、硬度、耐熱性が要求される部品にますます使用されるようになるだろう。
よくある質問
ここでは、タングステンを使った3Dプリントに関するよくある質問にお答えします:
の主な利点は何か? 3Dプリントタングステン 部品?
3Dプリンティングの主な利点は、設計の自由度、マスカスタマイゼーション、連結アセンブリ、軽量ラティス、ラピッドプロトタイピング、機械加工や鋳造では不可能な複雑な形状の実現などである。
タングステンを加工できる金属3Dプリント方法は?
現在、タングステンの印刷には、選択的レーザー溶融(SLM)と電子ビーム溶融(EBM)粉末床融合プロセスが使用されている。
どのような産業で3Dプリントタングステン部品が使用されていますか?
航空宇宙、防衛、自動車、医療、エレクトロニクス、原子力産業は、3Dプリントタングステン部品を使用しています。
3Dプリントに使用できるタングステンパウダーの種類は?
純タングステン、タングステンカーバイド-コバルト、タングステン重合金の10-45ミクロンサイズの粉末。球状の粉末が最良の結果をもたらします。
プリントタングステンは後処理が必要ですか?
延性、高密度化、公差、表面仕上げを改善するには、応力除去、熱間静水圧プレス、機械加工などの後工程が必要である。
印刷タングステンの特性は、従来のタングステンと比べてどうですか?
慎重に処理されたプリントタングステンは、99%の密度を達成し、ほぼ錬成材の強度と硬度に匹敵することができます。延性は若干劣ります。
タングステンを3Dプリントした最終用途の部品にはどのような例がありますか?
ノズルインサート、電極、放射線シールド、カウンターウェイト、高密度バラスト、バランス部品、タングステン重合金を使用した金属切削工具。
3Dプリントできるタングステン部品のサイズは?
現在のパウダーベッドシステムでは、最大250×250×300mmまでの部品が使用可能だが、より大型のシステムも開発中である。
3Dプリンターで作られたタングステンは、生産用に手頃な価格なのか?
中程度の大きさの部品であれば、タングステンでの印刷は100~5000ドルかかる。大量生産は、高いパウダーコストによってまだ制限されています。