アディティブ・マニュファクチャリングは世界を席巻しているが、PBF用粉末はこの革命の重要な担い手である。この記事では、PBFで使用される金属粉末の世界に深く入り込み、その種類、組成、特性、用途などを探ります。熟練したプロであれ、好奇心旺盛な初心者であれ、この包括的なガイドは貴重な洞察と実践的な知識を提供してくれるだろう。
概要 PBFテクニック用パウダー
粉末床溶融法(PBF)は、選択的レーザー溶融法(SLM)や電子ビーム溶融法(EBM)などのさまざまな技術を含む積層造形のカテゴリーである。PBFでは、粉末材料の層を融合させて複雑で精密な部品を作ります。金属粉末の選択は、最終製品の品質、強度、性能に直接影響するため非常に重要です。
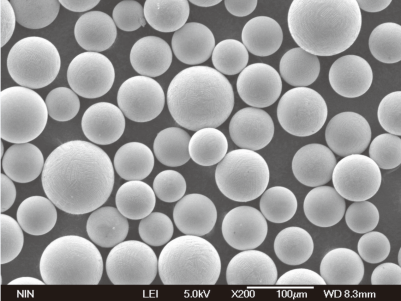
PBF用パウダーの種類
PBFに使用される金属粉末の状況をよりよく理解するために、具体的なモデルとその詳細な説明に飛び込んでみよう。
金属粉 | 構成 | プロパティ | 用途 |
---|---|---|---|
Ti-6Al-4V | チタン合金(90% Ti、6% Al、4% V) | 高強度、軽量、耐食性 | 航空宇宙、医療用インプラント、自動車 |
316Lステンレス鋼 | 鉄合金(16~18%Cr、10~14%Ni、2~3%Mo) | 耐食性、優れた機械的特性 | 医療機器、食品加工機器 |
AlSi10Mg | アルミニウム合金(90% Al、10% Si、0.3-0.5% Mg) | 軽量、優れた熱特性 | 自動車、航空宇宙、消費財 |
Inconel 718 | ニッケル合金 (50-55% Ni, 17-21% Cr, 4.75-5.5% Nb) | 高温耐性、良好な溶接性 | 航空宇宙、エネルギー、自動車 |
マルエージング鋼 1.2709 | 鉄合金(18% Ni、9% Co、5% Mo、0.2% Ti) | 高い強度、硬度、靭性 | 工具、航空宇宙、自動車 |
CoCrMo | コバルト合金(Co 60%、Cr 27~30%、Mo 5~7) | 耐摩耗性、生体適合性 | 医療用インプラント、歯科用途 |
銅 C18150 | 銅合金(99.85% Cu、0.15% Zr) | 高い熱伝導性と電気伝導性 | 電気部品、熱管理 |
AlSi12 | アルミニウム合金(87~89%Al、10~12%Si) | 高い強度重量比、優れた鋳造特性 | 自動車、航空宇宙 |
Hastelloy X | ニッケル合金 (47-50% Ni, 20-23% Cr, 8-10% Mo) | 高温での耐酸化性、耐腐食性 | 航空宇宙、化学処理 |
工具鋼 H13 | 鉄合金(0.4% C、5% Cr、1.3% Mo、1% V) | 高い耐摩耗性、熱安定性 | 金型 |
構成 PBFテクニック用パウダー
これらの金属粉末の組成を理解することは、プロジェクトに適した材料を選択するために不可欠です。各粉末の元素のユニークなブレンドは、それが異なるアプリケーションに適した特定の特性を付与します。
金属粉 | 主な要素 | 副次的要素 | 不純物 |
---|---|---|---|
Ti-6Al-4V | チタン、アルミニウム、バナジウム | 鉄、酸素 | 炭素、窒素 |
316Lステンレス鋼 | 鉄、クロム、ニッケル | モリブデン、マンガン、シリコン | リン、硫黄 |
AlSi10Mg | アルミニウム、シリコン、マグネシウム | 鉄、銅 | チタン、亜鉛 |
Inconel 718 | ニッケル、クロム、ニオブ | モリブデン、チタン、アルミニウム | カーボン、コバルト |
マルエージング鋼 1.2709 | 鉄、ニッケル、コバルト、モリブデン | チタン、アルミニウム | カーボン、シリコン |
CoCrMo | コバルト、クロム、モリブデン | ニッケル、鉄 | マンガン、シリコン |
銅 C18150 | 銅、ジルコニウム | – | 鉄、鉛 |
AlSi12 | アルミニウム、シリコン | 鉄、銅 | マンガン、亜鉛 |
Hastelloy X | ニッケル、クロム、モリブデン | 鉄、コバルト | マンガン、シリコン |
工具鋼 H13 | 鉄、クロム、モリブデン、バナジウム | 炭素、ケイ素、マンガン | リン、硫黄 |
の特徴 PBFテクニック用パウダー
PBFに使用される金属粉末の種類はそれぞれ、特定の用途に適した明確な特性を持っている。ここでは、これらの特性について詳しく説明する。
金属粉 | 密度 (g/cm³) | 融点 (°C) | 引張強さ (MPa) | 伸び(%) | 硬度(HV) |
---|---|---|---|---|---|
Ti-6Al-4V | 4.43 | 1660 | 900-1100 | 10-15 | 330 |
316Lステンレス鋼 | 7.99 | 1375-1400 | 480-620 | 30-40 | 200 |
AlSi10Mg | 2.68 | 570-580 | 300-350 | 5-10 | 120 |
Inconel 718 | 8.19 | 1260-1336 | 965-1241 | 10-20 | 330 |
マルエージング鋼 1.2709 | 8.0 | 1413 | 2000-2500 | 5-10 | 500 |
CoCrMo | 8.29 | 1330-1390 | 900-1300 | 10-20 | 500 |
銅 C18150 | 8.96 | 1083 | 350-410 | 20-30 | 110 |
AlSi12 | 2.68 | 570-580 | 200-300 | 5-10 | 80 |
Hastelloy X | 8.22 | 1260-1350 | 700-1000 | 30-40 | 200 |
工具鋼 H13 | 7.80 | 1425-1530 | 1000-1200 | 10-15 | 600 |
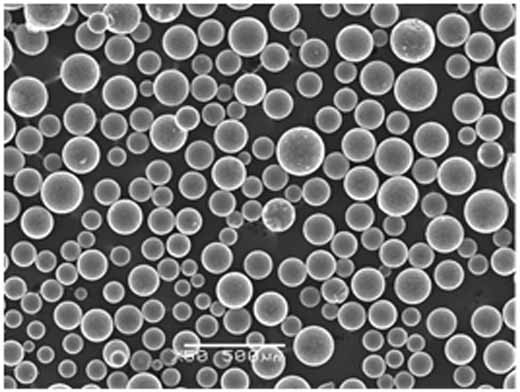
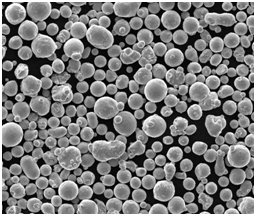
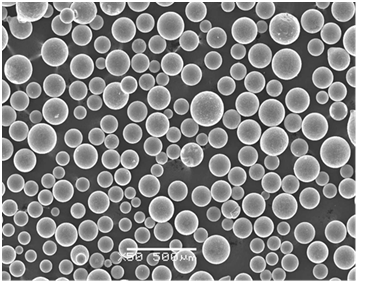
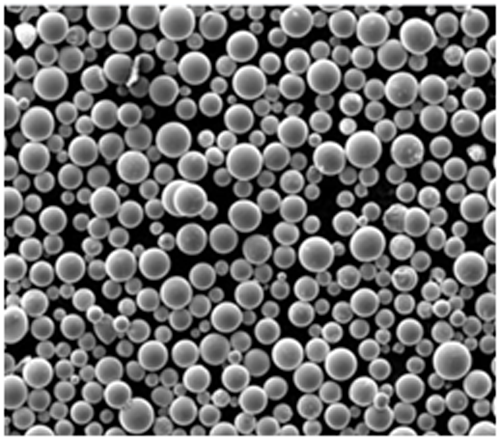
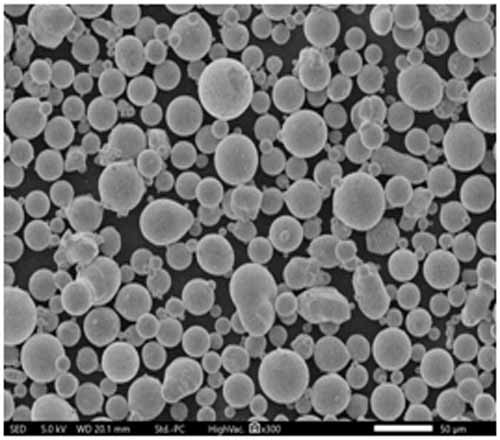
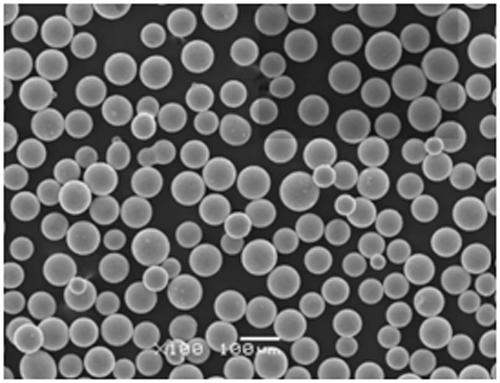
PBF用パウダーの用途
PBF用金属粉末は、様々な産業分野で多様な用途があります。それぞれの粉末がどのような用途に適しているのか、詳しくご紹介します。
金属粉 | 産業 | 具体的な用途 |
---|---|---|
Ti-6Al-4V | 航空宇宙、医療 | 航空機部品、インプラント |
316Lステンレス鋼 | 医療、食品 | 手術器具、食品加工機器 |
AlSi10Mg | 自動車、航空宇宙 | 軽量部品、プロトタイプ |
Inconel 718 | 航空宇宙、エネルギー | タービンブレード、ロケットエンジン |
マルエージング鋼 1.2709 | 工具、航空宇宙 | 高強度工具、構造部品 |
CoCrMo | 医療、歯科 | 人工関節、歯科補綴 |
銅 C18150 | 電気、熱 | 電気コネクター、熱交換器 |
AlSi12 | 自動車、航空宇宙 | エンジン部品、ブラケット |
Hastelloy X | 航空宇宙、化学 | 燃焼室、化学反応器 |
工具鋼 H13 | 金型、成形 | 射出成形金型、ダイカスト金型 |
グレード PBFテクニック用パウダー
金属粉末にはさまざまなグレードがあり、特定の用途に適した材料が選択されます。ここでは、一般的に使用される粉末のグレードをご紹介します。
金属粉 | グレード | 説明 |
---|---|---|
Ti-6Al-4V | 5年生, 23年生 | 標準および超低空間バージョン |
316Lステンレス鋼 | 316L、316LVM | 低炭素および真空溶解バージョン |
AlSi10Mg | スタンダード | 一般的なグレード |
Inconel 718 | 午前5662、午前5663 | 航空宇宙および高温グレード |
マルエージング鋼 1.2709 | スタンダード | 一般的なグレード |
CoCrMo | F75, F1537 | 医療用インプラントのグレード |
銅 C18150 | スタンダード | 一般的なグレード |
AlSi12 | スタンダード | 一般的なグレード |
Hastelloy X | AMS 5754、UNS N06002 | 高温耐食グレード |
工具鋼 H13 | 標準、H13 ESR | 一般仕様とエレクトロスラグ精製仕様 |
仕様、サイズ、規格
金属粉末の種類にはそれぞれ、業界の要件を満たすための特定の規格とサイズがある。
金属粉 | 粒子径(µm) | 規格 | サプライヤー | 価格(kgあたり) |
---|---|---|---|---|
Ti-6Al-4V | 15-45 | アストレムB348、アストレムF2924 | EOS、Arcam、AP&C | $300 – $500 |
316Lステンレス鋼 | 15-45 | アストレムA276、アストレムF138 | GKN、サンドビック、カーペンター | $100 – $150 |
AlSi10Mg | 20-63 | DIN EN 1706、ASM B361 | SLMソリューションズ、EOS | $80 – $120 |
Inconel 718 | 15-45 | 午前5662、午前5663 | プラクセア、サンドビック、LPW | $150 – $250 |
マルエージング鋼 1.2709 | 15-45 | AMS 6512 | カーペンター、サンドビック | $200 – $300 |
CoCrMo | 20-63 | アストレムF75、アストレムF1537 | カーペンター、EOS | $200 – $400 |
銅 C18150 | 15-45 | アストレムB124、アストレムB152 | サンドビック、カーペンター | $50 – $100 |
AlSi12 | 20-63 | DIN EN 1706 | EOS、SLMソリューション | $70 – $110 |
Hastelloy X | 15-45 | AMS 5754、UNS N06002 | プラクセア、サンドビック | $200 – $300 |
工具鋼 H13 | 20-63 | ASTM A681 | カーペンター、サンドビック | $100 – $200 |
PBFテクニックにおけるパウダーの長所と短所
適切な金属粉末を選択する際には、各選択肢の長所と短所を比較検討することが不可欠である。
金属粉 | 長所 | 短所 |
---|---|---|
Ti-6Al-4V | 高い強度対重量比、耐食性 | 高価で加工が難しい |
316Lステンレス鋼 | 優れた耐食性、生体適合性 | いくつかの合金に比べて強度が低い |
AlSi10Mg | 軽量、良好な熱伝導性 | 強度と硬度が低い |
Inconel 718 | 高温耐性、良好な溶接性 | 高価、機械加工が難しい |
マルエージング鋼 1.2709 | 極めて高い強度、優れた切削性 | 高価、熱処理が必要 |
CoCrMo | 高い耐摩耗性、生体適合性 | 高価で加工が難しい |
銅 C18150 | 優れた熱伝導性と電気伝導性 | 柔らかく、摩耗しやすい |
AlSi12 | 良好な鋳造特性、軽量 | 強度と硬度が低い |
Hastelloy X | 優れた耐酸化性と耐食性 | 高価、機械加工が難しい |
工具鋼 H13 | 高い耐摩耗性、熱安定性 | 高価、熱処理が必要 |
PBFに適したパウダーの選択
適切なパウダーを選択するには、材料特性、用途要件、コストなど、いくつかの要素を考慮する必要があります。以下はその比較です。
ファクター | Ti-6Al-4V | 316Lステンレス鋼 | AlSi10Mg | Inconel 718 | マルエージング鋼 1.2709 | CoCrMo | 銅 C18150 | AlSi12 | Hastelloy X | 工具鋼 H13 |
---|---|---|---|---|---|---|---|---|---|---|
強さ | 高い | ミディアム | ミディアム | 高い | 非常に高い | 高い | ミディアム | ミディアム | 高い | 高い |
重量 | 低い | ミディアム | 低い | ミディアム | ミディアム | 高い | 高い | 低い | 高い | ミディアム |
耐食性 | 高い | 非常に高い | ミディアム | 高い | ミディアム | 非常に高い | 低い | ミディアム | 非常に高い | ミディアム |
熱伝導率 | ミディアム | 低い | 高い | ミディアム | 低い | 低い | 非常に高い | 高い | ミディアム | 低い |
コスト | 高い | ミディアム | 低い | 高い | 高い | 高い | 低い | 低い | 高い | ミディアム |
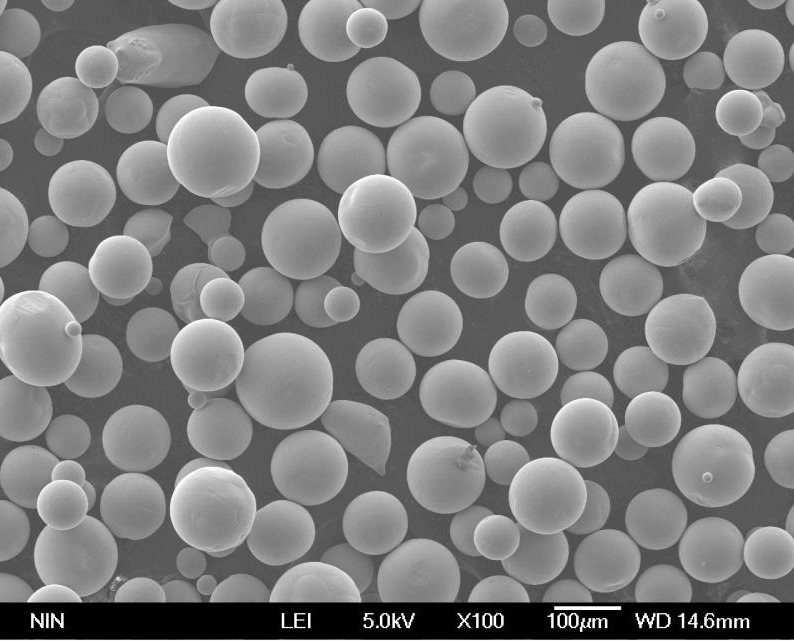
よくある質問
質問 | 回答 |
---|---|
積層造形におけるPBFとは? | PBF(Powder Bed Fusion)とは、レーザーや電子ビームなどの熱源によって粉末材料を層ごとに融合させ、3Dオブジェクトを作成する積層造形の一種である。 |
PBFの主な種類は? | PBFの主な種類は、選択的レーザー溶解(SLM)と電子ビーム溶解(EBM)である。SLMはレーザーを熱源として使用し、EBMは電子ビームを使用する。 |
なぜパウダーの選択が重要なのか? | パウダーの選択は、機械的特性、表面仕上げ、印刷部品全体の品質に影響します。パウダーの種類によって、強度、熱伝導性、耐食性、その他特定の用途に重要な特性が異なります。 |
粉体の品質管理はどのように行われているのですか? | パウダーの品質は、粒度分布、化学組成、純度など、さまざまな尺度を通して管理されます。製造業者はASTMやISOのような規格を使用し、パウダーの一貫性と信頼性を確保しています。 |
異なるパウダーを混ぜることはできますか? | 一般的に、異なる粉末を混合することは推奨されない。しかし、一部の研究や実験セットアップでは、特定の特性を達成するために調整されたブレンドが使用されることがあります。 |
PBFの一般的な課題は何ですか? | 一般的な課題には、粉末のリサイクル、気孔率の制御、一貫した層結合の達成、残留応力の管理などがある。これらの課題を克服するには、高度な技術と慎重な工程管理が不可欠です。 |
PBFで粉体はどのようにリサイクルされるのですか? | 未使用のパウダーは回収し、次回以降の製造に再利用することができるが、慎重にふるいにかけ、品質基準を満たしていることを確認しなければならない。リサイクルパウダーは時間の経過とともに劣化する可能性があり、品質を維持するためには新しいパウダーを混ぜる必要があります。 |
環境への影響は? | PBF技術は、材料廃棄物の削減や粉体のリサイクルが可能なため、従来の製造方法よりも持続可能である。しかし、機械のエネルギー消費と(場合によっては)不活性ガス環境の必要性により、管理すべき環境への影響が生じる可能性がある。 |
PBFの恩恵を最も受けるのはどの業界か? | 航空宇宙、医療、自動車産業は、従来の製造方法では困難または不可能な複雑で高強度、軽量な部品を製造できるため、PBFから大きな恩恵を受けている。 |
自分のプロジェクトに適したパウダーを選ぶには? | 機械的特性、熱伝導性、耐食性、コストなど、用途に特有の要件を考慮する。材料データシートを検討し、粉体サプライヤーや専門家に相談して、十分な情報を得た上で決定してください。 |
結論
PBF技術のための金属粉末の世界をナビゲートすることは複雑ですが、これらの粉末の種類、組成、特性、およびアプリケーションを理解することは非常に重要です。長所と短所を比較検討し、プロジェクトの具体的なニーズを考慮することで、付加製造の試みを確実に成功させるための情報に基づいた決定を下すことができます。PBF技術と金属粉末開発の絶え間ない進歩により、製造業の未来は間違いなく明るい。