について 回転電極法 (REP)は、高品質の金属粉末を製造するために使用される高度な方法である。このプロセスは、均一性に優れた球状粒子を生成できることから、様々な産業で高く評価されています。回転電極プロセスの世界を深く知りたいとお考えなら、このガイドが最適です!このガイドブックでは、基本的なことから細かなことまで、REPを完全に理解するために必要なことを説明します。
回転電極プロセスの概要
回転電極プロセスでは、回転する金属電極を電気アークまたはプラズマで溶かす。金属が溶融すると、遠心力によって微細な液滴に分散し、球状の粒子に凝固する。このプロセスは、サイズと形状が均一な金属粉末の製造に特に効果的で、積層造形、溶射、粉末冶金など、さまざまな用途に最適です。
重要なポイント
- プロセス 回転する金属電極を電気アークやプラズマで溶かすこと。
- 成果だ: 微細な球状の金属粉末粒子。
- アプリケーション 積層造形、溶射、粉末冶金など。
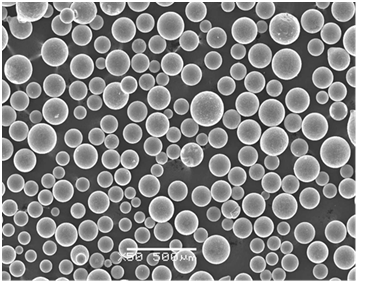
回転電極法で製造される金属粉末の種類
ここでは、回転電極プロセスで製造される金属粉末の具体的なモデルをいくつか紹介するが、それぞれがユニークな特性と用途を持っている:
金属粉モデル | 構成 | プロパティ | 用途 |
---|---|---|---|
チタン合金 (Ti-6Al-4V) | Ti-6%Al-4%V | 高強度、軽量、優れた耐食性 | 航空宇宙、医療用インプラント |
ニッケル合金(インコネル718) | Ni-52%Cr-19-5%Nb-3%Mo | 高温強度、耐酸化性 | タービンブレード、ロケットエンジン |
ステンレススチール(316L) | Fe-17%Cr-12%Ni-2.5%Mo | 耐食性、優れた機械的特性 | 医療機器、海洋アプリケーション |
コバルトクロム合金(Co-Cr-Mo) | Co-28%Cr-6%Mo | 高い耐摩耗性、生体適合性 | 歯科および整形外科用インプラント |
銅合金(Cu-Ni-Sn) | Cu-90%Ni-10%Sn | 優れた熱伝導性と電気伝導性 | 電気部品、熱交換器 |
アルミニウム合金(Al-Si10Mg) | Al-10%Si-0.3%Mg | 軽量、優れた機械的特性 | 自動車部品、航空宇宙 |
タンタル (Ta) | 純タンタル | 高融点、優れた耐食性 | 医療用インプラント、エレクトロニクス |
モリブデン (Mo) | 純モリブデン | 高温での高強度、優れた熱伝導性 | エレクトロニクス、航空宇宙 |
タングステン(W) | 純タングステン | 最高融点、高密度 | 放射線遮蔽、航空宇宙 |
マグネシウム合金(AZ91D) | Mg-9%Al-1%Zn | 軽量、良好なキャスタビリティー | 自動車部品、エレクトロニクス |
の組成と特徴 回転電極プロセス 粉類
回転電極プロセスによって製造される金属粉末の組成と特性を理解することは、特定の用途に適した材料を選択するために極めて重要である。
構成:
REPで製造される金属粉末の組成は、母材と希望する合金によって大きく異なることがあります。例えば、Ti-6Al-4Vのようなチタン合金は、チタン、アルミニウム、バナジウムで構成されており、それぞれが材料全体の特性に寄与しています。
特徴
- 粒子の形状: 良好な流動性と充填密度を保証する球状。
- 粒度分布: アプリケーションで安定したパフォーマンスを発揮するために不可欠な均一性。
- 純粋さ: 管理された環境で生産されるため、高い。
- 機械的特性: 合金にもよるが、高強度、高靭性から優れた熱伝導性、電気伝導性まで様々である。
回転電極プロセス粉末の用途
REPパウダーのユニークな特性は、幅広い用途に適しています。主な用途をいくつかご紹介します:
申し込み | 説明 |
---|---|
付加製造 | REPパウダーの均一性と高品質は、精度と材料特性が重要な3Dプリンティング用途に理想的である。 |
溶射 | REPパウダーは溶射に使用され、耐摩耗性や耐食性などの表面特性を向上させるコーティングを形成する。 |
粉末冶金 | これらの粉末は粉末冶金において、高精度で優れた機械的特性を持つ複雑な部品を作るために使用される。 |
医療用インプラント | その生体適合性と優れた機械的特性から、REPパウダーは整形外科用インプラントや歯科用インプラントなどの医療用インプラントの製造に使用されている。 |
航空宇宙部品 | REPが製造する高性能合金は、強度対重量比と高温性能が重要な航空宇宙用途で使用されている。 |
エレクトロニクス | REPで生産されるタンタルやモリブデンのような材料は、その優れた電気伝導性と熱伝導性により、電子部品に使用されている。 |
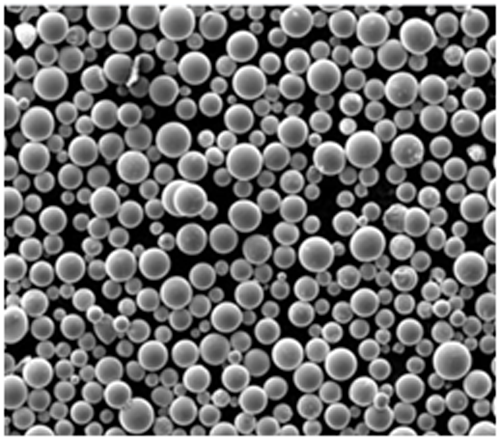
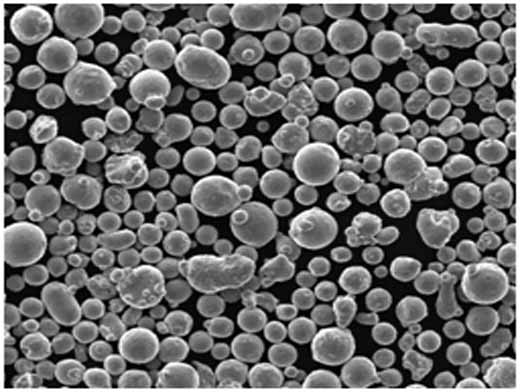
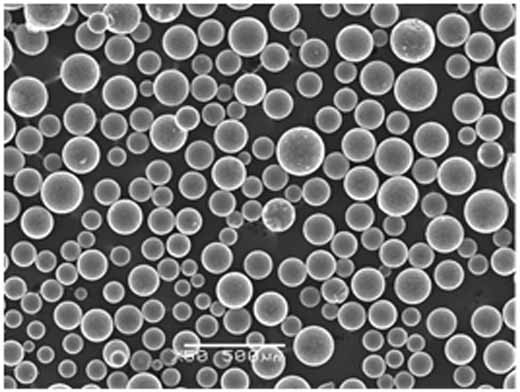
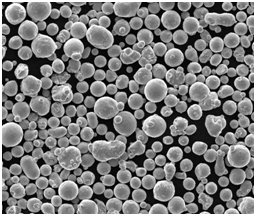
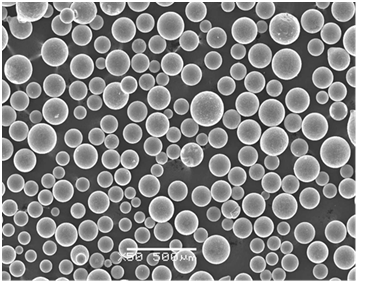
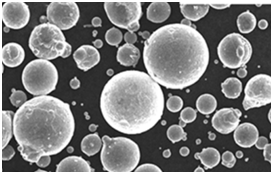
回転電極プロセス粉末の仕様、サイズ、グレード
REPパウダーが特定の用途に適していることを確認するためには、その仕様、サイズ、等級を考慮することが重要である。
仕様
- 純粋さ: 通常99.9%以上。
- 粒度分布: 用途によって異なるが、一般的には10~150ミクロン。
- 流動性: 球形で優れている。
- 密度が高い: タングステンのような金属は密度が高く、アルミニウム合金は軽量である。
サイズと等級:
素材 | グレード | サイズ範囲(ミクロン) | 規格 |
---|---|---|---|
チタン合金 (Ti-6Al-4V) | グレード5 | 15-45, 45-90 | ASTM F136 |
ニッケル合金(インコネル718) | UNS N07718 | 15-45, 45-106 | AMS 5662 |
ステンレススチール(316L) | AISI 316L | 20-63, 45-150 | ASTM F138 |
コバルトクロム合金(Co-Cr-Mo) | ASTM F75 | 15-45, 45-90 | ISO 5832-4 |
銅合金(Cu-Ni-Sn) | C70600 | 20-63, 45-106 | ASTM B122 |
アルミニウム合金(Al-Si10Mg) | EN AC-43000 | 20-63, 45-106 | ISO 3522 |
タンタル (Ta) | R05200 | 20-63, 45-106 | ASTM F560 |
モリブデン (Mo) | R03620 | 20-63, 45-106 | ASTM B386 |
タングステン(W) | R09010 | 20-63, 45-106 | ASTM B777 |
マグネシウム合金(AZ91D) | ASTM B93/B93M | 20-63, 45-106 | ASTM B93 |
サプライヤーと価格詳細
ここでは、REPパウダーの主要サプライヤーとその価格詳細をご紹介します。価格は純度、粒度、注文量によって異なります。
サプライヤー | 素材 | 価格(USD/kg) | 注文数量 |
---|---|---|---|
ヘガネスAB | チタン合金 (Ti-6Al-4V) | $300 – $500 | 最低10kg |
カーペンター・テクノロジー | ニッケル合金(インコネル718) | $400 – $600 | 最低5kg |
GKN粉末冶金 | ステンレススチール(316L) | $50 – $100 | 最低25kg |
サンドビック | コバルトクロム合金(Co-Cr-Mo) | $200 – $400 | 最低10kg |
プラクセア・サーフェス・テクノロジー | 銅合金(Cu-Ni-Sn) | $30 – $70 | 最低20kg |
テクナ | アルミニウム合金(Al-Si10Mg) | $100 – $150 | 最低15kg |
コーティング | タンタル (Ta) | $1000 – $1500 | 最低1kg |
プランゼー | モリブデン (Mo) | $150 – $300 | 最低10kg |
グローバルタングステン&パウダー社 | タングステン(W) | $200 – $400 | 最低5kg |
マグネシウム・エレクトロン | マグネシウム合金(AZ91D) | $60 – $120 | 最低20kg |
の長所と短所を比較する 回転電極プロセス 粉類
自分のニーズに合った金属粉を選ぶには、それぞれの利点と限界を比較検討することが重要だ。
素材 | メリット | 制限事項 |
---|---|---|
チタン合金 (Ti-6Al-4V) | 高い強度対重量比、優れた耐食性 | 高価、機械加工が難しい |
ニッケル合金(インコネル718) | 高温強度、耐酸化性 | 高コスト、限られた利用可能性 |
ステンレススチール(316L) | 耐食性、優れた機械的特性 | 他の金属に比べて重い |
コバルトクロム合金(Co-Cr-Mo) | 高い耐摩耗性、生体適合性 | 高価で加工が難しい |
銅合金(Cu-Ni-Sn) | 優れた熱伝導性と電気伝導性 | 他の合金に比べて強度が低い |
アルミニウム合金(Al-Si10Mg) | 軽量、優れた機械的特性 | チタン合金に比べて強度が低い |
タンタル (Ta) | 高融点、優れた耐食性 | 非常に高価、用途が限られる |
モリブデン (Mo) | 高温での高強度、優れた熱伝導性 | 脆い、高価 |
タングステン(W) | 最高融点、高密度 | 非常に重く、加工が難しい |
マグネシウム合金(AZ91D) | 軽量、良好なキャスタビリティー | 他の合金に比べて強度や耐食性が低い。 |
回転電極プロセスを詳しく理解する
回転電極プロセスはどのように機能するのか?
高速で回転する金属棒を想像してほしい。電気アークやプラズマが棒の先端を溶かすと、遠心力によって溶けた金属が小さな液滴となって飛び散る。この液滴が冷えて固まり、細かい球状の粒子になる。これが回転電極法の本質である。その有効性の鍵は、制御された環境と、均一な粒子サイズと形状を保証する高速回転にある。
回転電極プロセスを選ぶ理由
回転電極プロセスが好まれる理由はいくつかある。第一に、得られる粉末は流動性と充填密度が優れており、積層造形や粉末冶金などの用途に極めて重要である。第二に、粒子の高純度と均一性が優れた材料特性をもたらし、航空宇宙、医療、エレクトロニクス産業における高性能アプリケーションに適している。
回転電極プロセスでよく使用される機器
回転電極プロセスにはいくつかの種類の装置が不可欠であり、それぞれが製造される粉末の効率と品質に貢献している。
設備 | 説明 | REPにおける役割 |
---|---|---|
回転電極機 | 金属電極を高速回転させる装置 | 遠心力を発生させて溶融金属を分散させる |
電気アーク炉 | 電気アークを発生させて金属を溶かす炉 | 電極を溶かすのに必要な熱を供給する |
プラズマトーチ | 高温プラズマアークを発生させる装置 | 金属を溶かすための代替熱源 |
冷却室 | 液滴が粒子に凝固する囲い | 急速な冷却と凝固を確保 |
粉体回収システム | 製造された粉体を収集・保管するシステム | 金属微粒子を集め、選別する |
回転電極プロセスにおける品質管理の維持
回転電極プロセスでは、製造された粉末が要求される基準を満たすことを保証するために、品質管理が最も重要です。品質管理の主要な側面は以下の通りです:
- 粒度分析: 粒度分布を測定するためにレーザー回折のような技術を使用する。
- 化学組成試験: 蛍光X線分析(XRF)のような方法で合金の組成を確認する。
- 形態素解析: 走査型電子顕微鏡(SEM)を使って、粒子の形状と表面特性を調べる。
- 密度の測定: 粉末のバルク密度とタップ密度を測定し、その充填挙動を評価する。
における挑戦と革新 回転電極プロセス
他の製造工程と同様に、回転電極工程も多くの課題に直面している。安定した品質の維持、高コストの管理、生産規模の拡大などである。しかし、現在進行中の技術革新により、これらの課題に対処しています。自動化、リアルタイムのモニタリング、マテリアルハンドリングの改善などの進歩により、REPの効率性と拡張性が向上している。
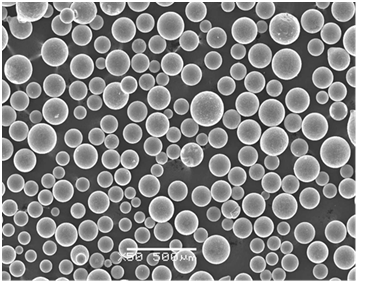
よくある質問
質問 | 回答 |
---|---|
回転電極プロセスを使用する主な利点は何ですか? | 主な利点は、均一な粒子径と優れた純度を持つ高品質の球状金属粉末の製造であり、要求の厳しい用途に最適である。 |
REPパウダーが最も恩恵を受ける産業は? | REPパウダーの優れた材料特性により、航空宇宙、医療、エレクトロニクスなどの産業が大きな恩恵を受けている。 |
REPパウダーのコストは、他のパウダー製造方法と比べてどうですか? | REPパウダーは一般に、製造工程に精密さと品質管理が必要なため高価である。しかし、その性能上の利点は、しばしば高いコストを正当化する。 |
回転電極プロセスは、あらゆる種類の金属に使用できますか? | REPは汎用性が高いが、特に高融点で特定の材料特性を持つ金属や合金から粉末を製造するのに効果的である。 |
回転電極プロセスにおける環境への配慮とは? | REPは材料を効率的に使用し、廃棄物の発生を最小限に抑えるため、環境に優しいと考えられている。しかし、高温を必要とするため、エネルギー消費は考慮しなければならない。 |
回転電極法はどのようにして粒子の均一性を確保するのですか? | 高い回転速度と制御された溶解環境により、溶融金属は均一な液滴に分散し、凝固して一貫した球状粒子になる。 |
回転電極プロセスには、今後どのような進歩が期待されるのだろうか? | 将来の進歩には、自動化の改善、リアルタイム・モニタリングの強化、効率性と拡張性をさらに最適化するためのマテリアルハンドリングの革新などが含まれる可能性がある。 |
結論
回転電極プロセスは、金属粉末を製造するための魅力的で非常に効果的な方法です。均一で高品質な粒子を作り出すその能力により、航空宇宙から医療用インプラントまで、様々な産業がその重要な用途にREPパウダーを利用しているのも不思議ではありません。この包括的なガイドブックでは、プロセス自体の理解、製造される金属粉の種類の探求、アプリケーションと仕様の掘り下げなど、どのようなご要望にもお応えします。技術と革新が進歩し続ける中、回転電極プロセスの未来はこれまで以上に明るく、より高い効率と幅広い用途が期待されます。