材料科学と工学に関して言えば、最も重要な側面のひとつは高純度粉末の調製である。これらの粉末は、その特性や性能の向上により、航空宇宙からエレクトロニクスに至るまで、様々な用途において不可欠なものです。この広範なガイドでは、高純度粉末の調製のニュアンスを掘り下げ、具体的な金属粉末のモデル、特性、用途などを探ります。また、長所と短所、サプライヤーの詳細、よくある質問にもお答えします。さあ、飛び込もう!
概要
高純度パウダーとは、不純物が極めて少ない金属や合金を細かく粉砕した粒子のことです。これらのパウダーは、積層造形、金属射出成形などの高度な製造プロセスにおいて極めて重要です。これらのパウダーを調製する主な目的は、それぞれの用途で最適な性能を確保するために、均一な粒度分布と高い化学純度を達成することです。
高純度パウダーの主な詳細
- 純度レベル:通常99.9%以上
- 粒子サイズ:ナノメートルからマイクロメートルまで可能
- 用途:航空宇宙、医療機器、エレクトロニクス、エネルギー貯蔵など
- 準備方法:化学蒸着、電解、アトマイズ、メカニカルアロイング
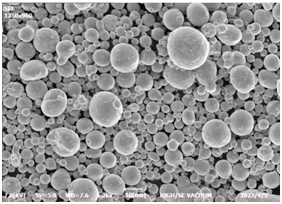
高純度金属粉末の種類
1.チタン(Ti)パウダー
チタン粉末は、その高い強度対重量比と優れた耐食性で知られています。航空宇宙、医療用インプラント、高性能自動車部品などに広く使用されています。
2.アルミニウム(Al)パウダー
アルミニウム粉末は軽量で、優れた導電性を持っている。電子機器、添加剤製造、化学反応の触媒として一般的に使用されている。
3.ニッケル(Ni)パウダー
ニッケル粉末は、その高い融点と優れた耐食性が評価されている。電池電極、超合金、コーティングなどに使用される。
4.銅(Cu)パウダー
銅粉は熱伝導性、電気伝導性に優れています。電気接点、導電性インク、ヒートシンクなどに使用されています。
5.鉄(Fe)パウダー
鉄粉はコストパフォーマンスに優れ、優れた磁気特性を持つ。磁性材料、自動車部品、様々な反応の触媒として利用されている。
6.コバルト(Co)パウダー
コバルト粉末はその耐摩耗性と高温安定性で知られている。超合金、切削工具、電池の陰極に使用される。
7.銀(Ag)パウダー
銀粉は金属の中で最も高い導電性を示す。導電性接着剤、インク、太陽電池などに使用されている。
8.金(Au)パウダー
金粉は耐食性と導電性に優れている。電子機器、医療機器、触媒として使用されている。
9.白金(Pt)パウダー
白金粉末は安定性が高く、酸化に強い。触媒コンバーター、燃料電池、センサーなどに使用されている。
10.タングステン(W)パウダー
タングステン粉末は金属の中で最も融点が高い。高温用途、電気接点、放射線遮蔽などに使用される。
組成、特性、特徴
以下は、これらの高純度金属粉末の主な特性をまとめた表である。
金属粉 | 構成 | 主要物件 | 特徴 |
---|---|---|---|
チタン(Ti) | 99.9% チタン | 高強度、耐食性 | 軽量、生体適合性 |
アルミニウム(Al) | 99.9%アル | 軽量、良好な導電性 | 高い延性、反射性 |
ニッケル(Ni) | 99.9%ニ | 高融点、耐食性 | 磁気、良好な機械的強度 |
銅(Cu) | 99.9%銅 | 優れた導電性 | 延性、高熱伝導性 |
鉄(Fe) | 99.9%鉄 | 費用対効果の高い磁気式 | 高強度、合金化が容易 |
コバルト | 99.9%株式会社 | 耐摩耗性、高温安定性 | 磁性、高硬度 |
銀(Ag) | 99.9% Ag | 最高の導電性 | 延性、反射性 |
金(Au) | 99.9%金 | 優れた導電性、耐食性 | 可鍛性、生体適合性 |
プラチナ (Pt) | 99.9% 白金 | 高い安定性、耐酸化性 | 高密度、高融点 |
タングステン(W) | 99.9% W | 最高融点 | 緻密、非常に硬い |
高純度粉末の用途
高純度パウダーは、その優れた特性により様々な産業で利用されています。ここに、その用途を示す詳細な表を示します。
金属粉 | 用途 |
---|---|
チタン(Ti) | 航空宇宙部品、医療用インプラント、自動車部品 |
アルミニウム(Al) | エレクトロニクス、積層造形、化学触媒 |
ニッケル(Ni) | 電池電極、超合金、コーティング |
銅(Cu) | 電気接点、導電性インク、ヒートシンク |
鉄(Fe) | 磁性材料、自動車部品、触媒 |
コバルト | 超合金、切削工具、電池カソード |
銀(Ag) | 導電性接着剤、インク、光電池 |
金(Au) | エレクトロニクス、医療機器、触媒 |
プラチナ (Pt) | 触媒コンバーター、燃料電池、センサー |
タングステン(W) | 高温用途、電気接点、放射線遮蔽 |
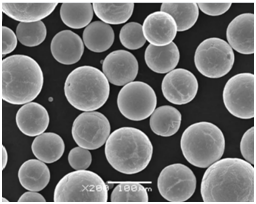
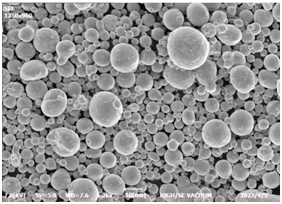

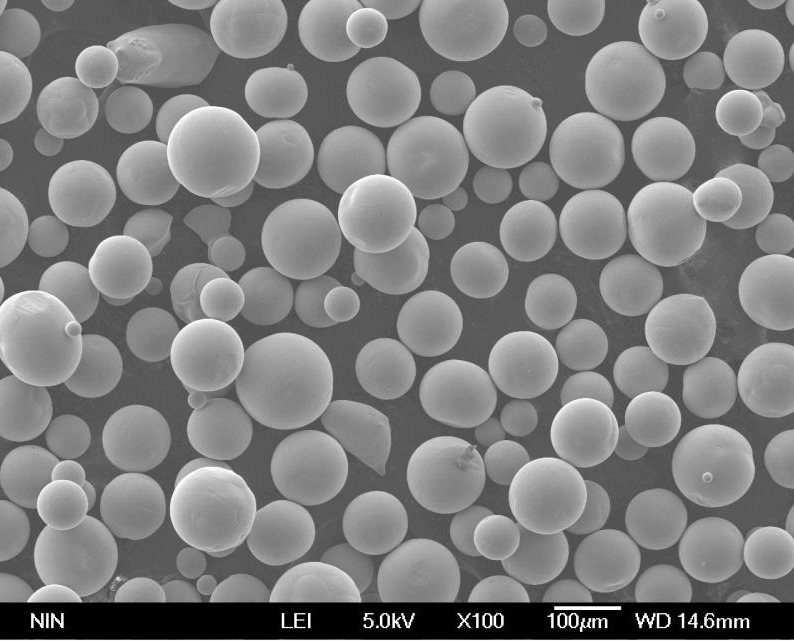
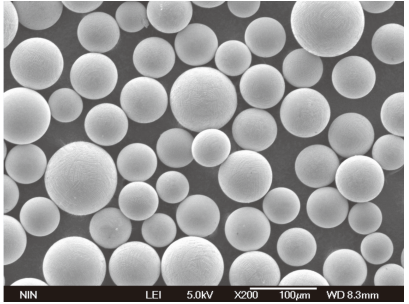
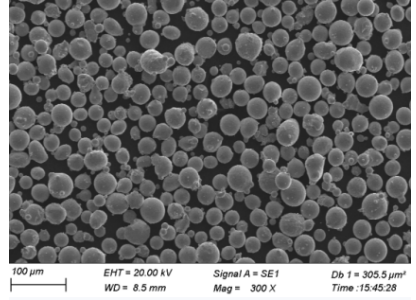
仕様、サイズ、等級、規格
高純度粉末を選ぶ際には、その仕様、サイズ、グレード、規格を理解することが極めて重要です。以下の表はこの情報を提供するものである。
金属粉 | 仕様 | サイズ | グレード | 規格 |
---|---|---|---|---|
チタン(Ti) | ASMB348、AMS4902 | 1-100マイクロメートル | グレード1、グレード2 | ASTM、AMS |
アルミニウム(Al) | ASMB221、AMS4068 | 1~200マイクロメートル | 1100, 2024 | ASTM、AMS |
ニッケル(Ni) | ASMB160、AMS5564 | 1~150マイクロメートル | ニッケル200、ニッケル201 | ASTM、AMS |
銅(Cu) | ASMB187、AMS4500 | 1-120マイクロメートル | C10100、C11000 | ASTM、AMS |
鉄(Fe) | A848, AMS 5030 | 1-180マイクロメートル | 鉄 99.9、鉄 99.95 | ASTM、AMS |
コバルト | アストレムF75、アムス4778 | 1-160マイクロメートル | Co 99.9、Co 99.95 | ASTM、AMS |
銀(Ag) | ASMB700、AMS4764 | 1-100マイクロメートル | 銀 99.9、銀 99.95 | ASTM、AMS |
金(Au) | ASMB488、AMS4787 | 1~50マイクロメートル | 金99.9、金99.95 | ASTM、AMS |
プラチナ (Pt) | ASMB493、AMS4897 | 1-100マイクロメートル | 白金99.9、白金99.95 | ASTM、AMS |
タングステン(W) | アストレムB777、アムス7875 | 1~150マイクロメートル | W 99.9, W 99.95 | ASTM、AMS |
サプライヤーと価格詳細
高純度パウダーの適切なサプライヤーを見つけることは、品質と費用対効果を確保するために不可欠です。ここでは、注目すべきサプライヤーとその価格詳細の表をご紹介します。
金属粉 | サプライヤー | 価格(kgあたり) | コメント |
---|---|---|---|
チタン(Ti) | アメリカの要素 | $300 | カスタマイズ可能な粒子径 |
アルミニウム(Al) | アルファ・エーザー | $150 | 高純度、各種サイズ |
ニッケル(Ni) | グッドフェロー | $250 | さまざまなグレードで利用可能 |
銅(Cu) | シグマ・アルドリッチ | $100 | 高純度微粉末 |
鉄(Fe) | ヘガネス | $50 | バルク可用性 |
コバルト | マテリオン | $400 | プレミアム品質、安定供給 |
銀(Ag) | エイムズ・ゴールドスミス | $1000 | 高導電性、各種サイズ |
金(Au) | 田中貴金属 | $5000 | 超高純度、カスタマイズ可能 |
プラチナ (Pt) | ジョンソン・マッセイ | $3000 | 高い安定性、様々なサイズ |
タングステン(W) | バッファロー・タングステン | $500 | 高融点、大量入手可能 |
高純度粉末の利点と欠点
高純度粉末の利点と欠点を理解することは、十分な情報に基づいた意思決定に役立ちます。以下の表は、長所と短所を比較したものです。
金属粉 | メリット | デメリット |
---|---|---|
チタン(Ti) | 高強度、耐食性 | 高価で加工が難しい |
アルミニウム(Al) | 軽量、良好な導電性 | 酸化しやすく、強度が低い |
ニッケル(Ni) | 高融点、耐食性 | 高価、限られたサプライヤー |
銅(Cu) | 優れた導電性、延性 | 酸化しやすく、それほど強くない |
鉄(Fe) | コストパフォーマンス、磁気特性 | 錆びやすく、耐食性が低い |
コバルト | 耐摩耗性、高温安定性 | 高価、限られたサプライヤー |
銀(Ag) | 高い導電性、延性 | 非常に高価、変色しやすい |
金(Au) | 優れた導電性、耐食性 | 非常に高価で柔らかい金属 |
プラチナ (Pt) | 高い安定性、耐酸化性 | 非常に高価、高密度 |
タングステン(W) | 最高融点、非常に硬い | 加工が難しく、高価 |
高純度粉末の調製法
高純度粉末の調製にはいくつかの方法が用いられ、それぞれに利点と限界があります。ここでは、一般的な調製方法について詳しく説明する。
1.化学気相成長法(CVD)
化学気相成長法では、気体状の前駆物質を化学反応させて固体材料を形成する。この方法は、粒径の揃った高純度の粉末を製造するのに理想的です。
メリット:
- 高純度レベル
- 均一な粒度分布
- 複雑な形状の製造が可能
デメリット:
- 高価な設備
- 反応条件の正確なコントロールが必要
2.電解
電解は、金属を含む溶液に電流を流し、金属を粉末として析出させる。この方法は、銅やニッケルなどの金属によく使われる。
メリット:
- 高純度
- 簡単なセットアップ
- 特定の金属に対する費用対効果
デメリット:
- 導電性材料に限る
- 生産速度の低下
3.霧化
アトマイズは、溶融金属の流れを微細な液滴に分解し、固化させて粉末にする。この方法はアルミニウム、チタン、鋼鉄などの金属に使用される。
メリット:
- 大量生産が可能
- 粒子径のコントロールが容易
- 幅広い金属に対応
デメリット:
- 高エネルギーの投入が必要
- 環境からの汚染の可能性
4.機械的合金化
メカニカルアロイングは、高エネルギーのボールミルで金属粉末を繰り返し破砕し、溶接する。この方法は、複雑な合金や複合粉末を製造するために使用される。
メリット:
- ユニークな合金の製造が可能
- 高いエネルギー効率
- コンポジションのコントロールが良い
デメリット:
- 処理時間が長い
- 粉砕媒体による汚染の可能性
用途に応じた準備方法
用途によっては、望ましい粉体特性を得るために特定の調製方法が必要になる場合があります。ここでは、用途に特化した方法をいくつかご紹介します。
航空宇宙
航空宇宙用途では、チタンやニッケルなどの高純度粉末をアトマイズやCVDで調製し、高い強度と耐食性を確保している。
医療機器
医療機器には、生体適合性と耐摩耗性を達成するために、電解や機械的合金化によって調製されたチタンやコバルトの粉末が使用されることが多い。
エレクトロニクス
エレクトロニクス分野では、アルミニウムや銅の粉末は通常、高い導電性と微細な粒子径を確保するために、電解と霧化を用いて調製される。
エネルギー貯蔵
電池のようなエネルギー貯蔵用途では、高性能と安定性のために、機械的合金化と電解によって調製されたニッケルやコバルトの粉末が使用される。
準備方法の比較
どの準備方法を使うべきかを決めるために、主要なパラメーターに基づく方法の比較を以下に示す。
準備方法 | 純度 | 粒子径コントロール | コスト | スピード | 適切な金属 |
---|---|---|---|---|---|
CVD | 高い | 素晴らしい | 高い | 中程度 | チタン、タングステン、プラチナ |
電解 | 高い | グッド | 中程度 | 遅い | 銅、ニッケル、銀 |
霧化 | 中程度 | 素晴らしい | 中程度 | 速い | アルミニウム、チタン、スチール |
機械的合金化 | 高い | グッド | 低い | 遅い | 複合合金、複合材料 |
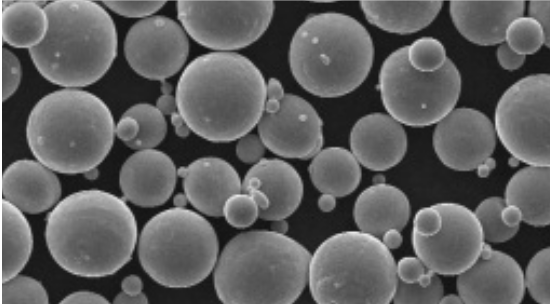
結論
高純度粉末の調製には、適切な金属の選択、特性と用途の理解、適切な調製方法の選択、信頼できるサプライヤーを見つけることが必要です。航空宇宙、エレクトロニクス、医療機器、エネルギー貯蔵のいずれの分野においても、粉末の品質は最終製品に大きな影響を与えます。本ガイドに記載されている詳細な比較と洞察を考慮することで、製造工程と製品性能を向上させるための十分な情報に基づいた決定を下すことができます。
よくある質問
1.金属粉末における高純度の重要性とは?
金属粉末の高純度は、精密な化学組成と優れた物理的特性を必要とする用途において最適な性能を保証するため、極めて重要です。不純物は材料の強度、導電性、耐食性に大きな影響を与えます。
2.用途に合った金属粉末を選ぶには?
適切な金属粉末の選択は、希望する特性(例:強度、導電性)、調製方法の適合性、およびコストの考慮事項など、特定の用途要件によって異なります。本ガイドの詳細な特性および用途の表を参照し、十分な情報に基づいた決定を下しましょう。
3.高純度パウダーを調製する最も一般的な方法は?
最も一般的な方法には、化学蒸着法(CVD)、電解法、アトマイズ法、メカニカルアロイング法などがある。それぞれの方法には利点と限界があり、その点については調製法のセクションで説明する。
4.高純度パウダーはカスタマイズできますか?
高純度パウダーは、粒度、組成、形状をカスタマイズすることができます。カスタマイズオプションを提供している信頼できるサプライヤーと協力することが重要です。
5.高純度の粉末を扱う際に、安全上の懸念はありますか?
高純度粉末の取り扱いには、吸入、摂取、皮膚接触を避けるための適切な安全対策が必要です。常に製造者の安全ガイドラインに従い、保護具を使用し、換気の良い場所で作業してください。
6.調製方法は粉末の最終的な特性にどのような影響を与えますか?
調製法は粉末の純度、粒度分布、形態、潜在的な汚染レベルに影響する。調製法の比較表に詳述されているように、それぞれの方法には長所があり、異なる用途に適しています。
7.高純度金属粉末はどこで購入できますか?
高純度金属粉末は、American Elements、Alfa Aesar、Goodfellow、Sigma-Aldrichなどの専門業者から購入することができる。本ガイドのサプライヤー・テーブルには、サプライヤーと価格の詳細が記載されている。
8.製造業で高純度パウダーを使用する利点は何ですか?
製造に高純度パウダーを使用することで、最終製品の性能、信頼性、寿命が向上します。高純度パウダーは、材料特性をよりよく制御し、不純物による欠陥のリスクを低減します。
9.高純度パウダーは積層造形に使用できるか?
そう、高純度パウダーは、優れた機械的特性と微細な形状解像度を持つ高性能部品を製造するための積層造形で広く使用されている。このプロセスでは、チタンやアルミニウムなどの金属が一般的に使用されます。
10.高純度粉末を保管する際に考慮すべき点は?
高純度パウダーを保管する際には、湿度管理、温度管理、汚染防止などの要素を考慮する。粉体の品質を維持するためには、気密性の高い容器を使用し、乾燥した環境で保管し、清潔な道具で取り扱うこと。