Overview of Laser Metal Deposition (LMD)
レーザー金属蒸着 (LMD) is a groundbreaking additive manufacturing (AM) technology that uses a high-powered laser to melt and fuse metal powder or wire onto a substrate, layer by layer, to create three-dimensional structures. Whether you’re in the aerospace, automotive, or medical industry, LMD provides a robust solution for complex metal parts that require precision, durability, and efficiency.
Imagine needing to repair a worn-out turbine blade or create a custom implant. Traditional manufacturing methods might be too slow, too costly, or simply not precise enough. LMD swoops in like a superhero, using lasers to weld metal powders into the perfect shape, layer by meticulous layer. The result? Highly accurate and strong components that might even outshine the originals.
But how does it work? What are the materials used? And most importantly, how can it benefit your business? In this detailed guide, we’ll dive deep into LMD’s ins and outs, from the specific metal powders it uses to its pros and cons, and even a handy FAQ section to clear up any lingering questions.
So, buckle up as we explore the fascinating world of Laser Metal Deposition!
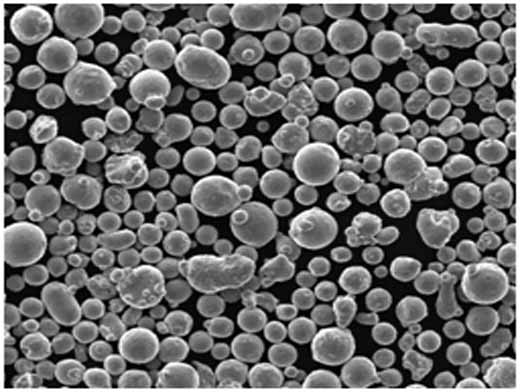
What is Laser Metal Deposition (LMD)?
LMD is a type of additive manufacturing, also known as 3D printing, where materials are added instead of removed. The process involves using a focused laser beam to melt metal powder or wire, which is then deposited onto a substrate. This technology allows for precise control over the material, enabling the creation of complex geometries and high-performance metal components.
How Does Laser Metal Deposition Work?
Laser Metal Deposition works by delivering metal powder through a nozzle into a laser beam, which melts the powder and fuses it to a base material (substrate). As the laser moves, it builds up layers of metal to form the desired shape. It’s like building a wall, but instead of bricks, you’re using tiny grains of metal, and instead of mortar, a high-energy laser binds everything together.
- Laser Source: The type and power of the laser determine how the metal powder will melt and solidify. Fiber lasers are commonly used for their efficiency and precision.
- Powder Feed System: Metal powders are fed into the laser beam via a nozzle. The consistency of the powder flow is crucial for achieving uniform layers.
- Motion Control: The motion of the laser and powder feed system is precisely controlled, often with CNC or robotic systems, to create the desired geometry.
This precision means that LMD is not just about building new parts. It can also repair existing ones by adding material where needed, which is particularly useful for expensive components in industries like aerospace.
応用例 レーザー金属蒸着 (LMD)
Laser Metal Deposition is a versatile process with a wide range of applications across various industries. From repairing high-value components to creating complex, custom-designed parts, LMD is making waves in manufacturing.
Key Applications:
産業 | 申し込み | メリット |
---|---|---|
航空宇宙 | Turbine blade repair, engine components | Reduced downtime, extended life of parts |
自動車 | Gear and crankshaft repairs, custom parts | Improved performance, cost-effective production |
メディカル | Custom implants, dental components | High precision, biocompatibility |
工具 | Mold repair, die restoration | Longer tool life, reduced lead time |
石油・ガス | Valve seats, drilling components | Resistance to harsh environments, reduced replacement cost |
発電 | Turbine repairs, component manufacturing | Improved efficiency, reduced maintenance costs |
ディフェンス | Armament components, repair of critical equipment | High strength, durability in extreme conditions |
エネルギー | 風力タービン部品、原子炉部品 | Sustainability, high performance in critical operations |
建設 | Custom structural components, heavy machinery repairs | Strength, flexibility, cost-effectiveness |
マリン | Propeller repairs, ship engine components | Corrosion resistance, longevity in marine environments |
Each of these industries has unique requirements, and LMD’s flexibility allows it to meet them all with ease. Whether it’s the high-strength materials needed for aerospace or the biocompatible metals used in medical implants, LMD can handle it.
Specific Metal Powders Used in LMD
The choice of metal powder is crucial in LMD, as it directly affects the quality, durability, and functionality of the final product. Here, we explore some of the specific metal powders commonly used in LMD, along with their compositions and characteristics.
Top 10 Metal Powders for LMD:
金属粉 | 構成 | プロパティ | 特徴 |
---|---|---|---|
Inconel 625 | Nickel-chromium-molybdenum-niobium alloy | High strength, excellent corrosion resistance | Used in aerospace, marine, chemical industries |
チタン Ti-6Al-4V | Titanium-aluminum-vanadium alloy | 高い強度対重量比、生体適合性 | Ideal for medical implants, aerospace |
ステンレススチール316L | Iron-chromium-nickel-molybdenum alloy | 耐食性、優れた機械的特性 | Common in medical, food processing industries |
Cobalt-Chrome (Co-Cr) | Cobalt-chromium alloy | 耐摩耗性、生体適合性 | Used in dental, orthopedic implants |
アルミニウム AlSi10Mg | Aluminum-silicon-magnesium alloy | 軽量、優れた熱特性 | Popular in automotive, aerospace applications |
Hastelloy X | Nickel-chromium-iron-molybdenum alloy | Heat resistance, oxidation resistance | 高温環境に適している |
Maraging Steel 18Ni300 | Nickel-cobalt-molybdenum-titanium alloy | Ultra-high strength, good toughness | Used in tooling, aerospace |
Nickel 718 | Nickel-chromium-iron alloy | High tensile strength, creep resistance | Widely used in turbine engines, aerospace |
工具鋼 H13 | Chromium-molybdenum-vanadium alloy | 高硬度、耐摩耗性 | Ideal for tooling, die casting molds |
Copper-CrZr | Copper-chromium-zirconium alloy | Excellent thermal conductivity, strength | Used in heat exchangers, electrical components |
These metal powders are carefully chosen based on the specific requirements of the application, including factors such as strength, corrosion resistance, and biocompatibility.
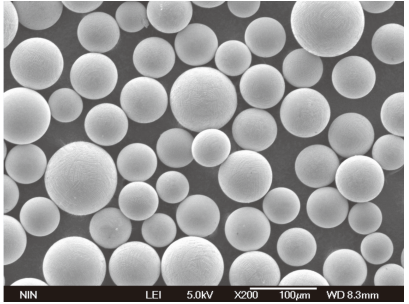
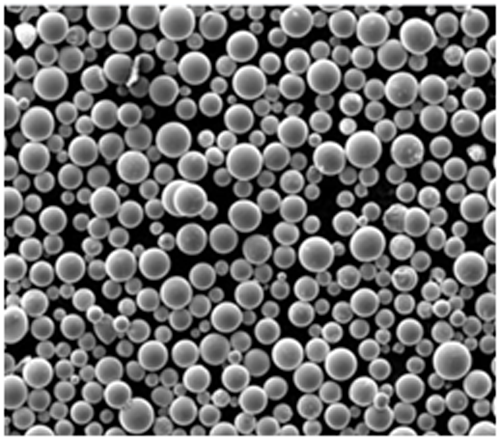
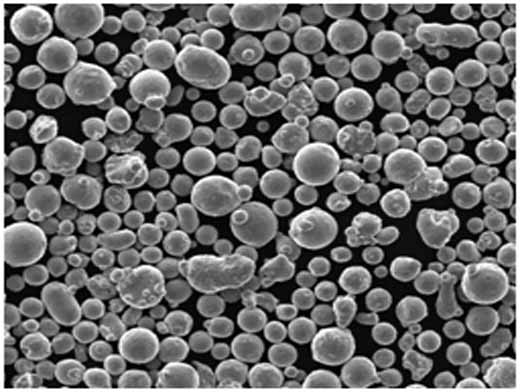
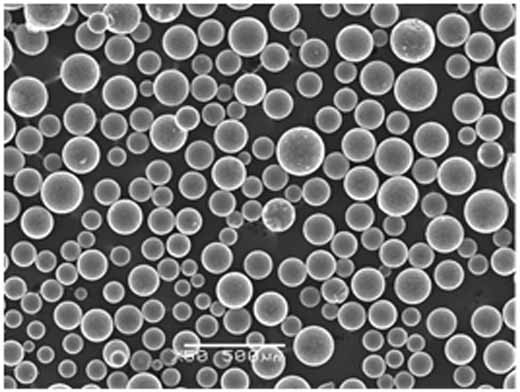
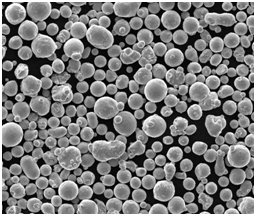
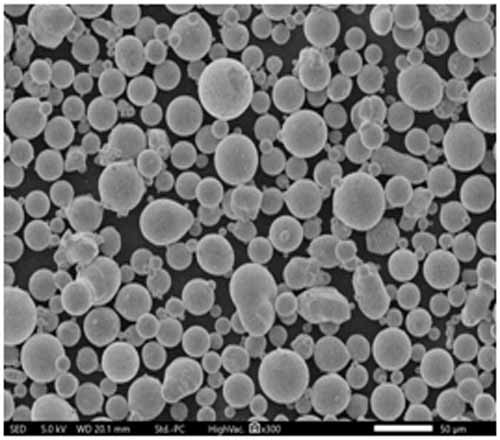
Properties and Characteristics of レーザー金属蒸着 (LMD)
Understanding the properties and characteristics of LMD is essential to fully appreciate its capabilities and potential limitations. Let’s break down these aspects to get a clearer picture of what makes LMD tick.
Material Properties:
プロパティ | 説明 |
---|---|
密度 | LMD components typically have high density, comparable to forged parts. |
微細構造 | Fine microstructures can be achieved, leading to high strength and toughness. |
表面仕上げ | The surface finish can vary depending on the powder and process parameters, often requiring post-processing. |
多孔性 | Minimal porosity is achievable with optimized parameters, though this can vary based on the material and application. |
Residual Stresses | LMD can introduce residual stresses, which may need to be relieved through heat treatment. |
Process Characteristics:
特徴 | 詳細 |
---|---|
層の厚さ | Typically ranges from 50 to 500 microns, depending on the application. |
Deposition Rate | Ranges from 0.5 to 3 kg/hour, influenced by the material and laser power. |
精度 | High precision with tolerances in the range of ±0.1 mm or better. |
Flexibility | Capable of handling complex geometries and multiple materials in a single build. |
スケーラビリティ | Suitable for both small and large components, from prototypes to production. |
The combination of these properties and characteristics makes LMD a powerful tool for manufacturing and repairing high-performance metal components.
Advantages and Limitations of Laser Metal Deposition (LMD)
Like any manufacturing process, LMD has its strengths and weaknesses. Here’s a breakdown of the advantages and limitations to help you determine if LMD is the right fit for your needs.
メリット
メリット | 説明 |
---|---|
精度と正確さ | LMD can produce highly detailed components with tight tolerances. |
材料効率 | Minimal waste is generated, making it a cost-effective option. |
汎用性 | Capable of processing a wide range of materials, including metals that are difficult to machine. |
Repair Capabilities | LMD excels at repairing high-value components, extending their life and reducing downtime. |
カスタマイズ | Easily customizable for small production runs or bespoke parts. |
制限:
制限 | 説明 |
---|---|
High Initial Costs | Equipment and setup costs can be significant, making it a considerable investment. |
表面仕上げ | Often requires post-processing to achieve a smooth surface. |
Complexity of Operation | Requires skilled operators and precise control of parameters. |
Heat Affected Zones | The laser can introduce heat affected zones that may alter the material properties. |
材料の制限 | Not all materials are suitable for LMD, especially those with low laser absorptivity. |
Understanding these pros and cons will help you make an informed decision when considering LMD for your manufacturing needs.
Process Parameters Influencing Laser Metal Deposition (LMD)
The quality of components produced via Laser Metal Deposition is highly dependent on several process parameters. These parameters must be carefully controlled to ensure the desired mechanical properties, surface finish, and overall performance of the final product.
Key Process Parameters:
パラメータ | 説明 | Influence on Final Product |
---|---|---|
Laser Power | The amount of energy provided by the laser, typically measured in watts. | Higher power increases deposition rate but may cause overheating. |
Scan Speed | The speed at which the laser moves across the substrate. | Faster speeds can reduce heat input but may lead to incomplete fusion. |
Powder Feed Rate | The rate at which metal powder is delivered to the melt pool. | Higher rates increase deposition efficiency but can lead to porosity if not controlled. |
Shielding Gas Flow | The flow rate of inert gas used to protect the molten pool from oxidation. | Adequate shielding prevents oxidation and contamination. |
Laser Spot Size | The diameter of the laser beam on the substrate. | A smaller spot size improves precision but can slow the process. |
Overlap Ratio | The degree of overlap between adjacent laser passes. | Higher overlap ensures uniformity but can increase processing time. |
Substrate Preheating | The temperature of the substrate before deposition begins. | Preheating reduces residual stresses and cracking. |
Each of these parameters plays a critical role in determining the quality and consistency of the LMD process. For instance, improper laser power or scan speed can result in defects such as porosity, cracking, or poor adhesion between layers.
Optimizing LMD Parameters for Best Results
To achieve the best results with LMD, it’s crucial to optimize these parameters for each specific application and material. This often involves a combination of experimentation and simulation to find the sweet spot where the process is both efficient and produces high-quality parts.
For example, when working with a high-strength alloy like Inconel 625, controlling the laser power and scan speed is essential to avoid overheating, which can lead to undesirable microstructural changes. Conversely, when using a more forgiving material like stainless steel 316L, the focus might be more on optimizing the powder feed rate and shielding gas flow to maximize deposition efficiency.
Advanced Materials Used in Laser Metal Deposition
Beyond the common metal powders listed earlier, LMD can also work with more specialized materials. These advanced materials are used in applications where standard metals might not meet the necessary performance criteria, such as extreme temperatures, corrosive environments, or specific mechanical requirements.
Additional Advanced Metal Powders for LMD:
金属粉 | 構成 | プロパティ | 特徴 |
---|---|---|---|
Nickel Alloy 263 | Nickel-chromium-cobalt-molybdenum alloy | 高温強度、耐酸化性 | Ideal for turbine blades, combustion liners |
ヘインズ 282 | Nickel-iron-chromium-molybdenum-titanium alloy | High creep resistance, excellent weldability | Used in aerospace, power generation |
タンタル (Ta) | Pure tantalum | Excellent corrosion resistance, biocompatibility | Suitable for chemical processing, medical devices |
ニオブ | Pure niobium | High melting point, good superconducting properties | Used in superconductors, aerospace components |
タングステン(W) | 純タングステン | Extremely high melting point, high density | Ideal for high-temperature applications |
インコネル738 | Nickel-chromium-cobalt-aluminum alloy | Exceptional oxidation resistance, high strength | Used in hot-section gas turbine components |
ルネ 41 | Nickel-chromium-cobalt-aluminum alloy | Superior high-temperature strength, oxidation resistance | Common in aerospace, gas turbines |
Ti-5553 | Titanium-aluminum-molybdenum-vanadium-chromium alloy | High strength, toughness, good corrosion resistance | Used in aerospace, military applications |
Cobalt Alloy Stellite 6 | Cobalt-chromium-tungsten-carbon alloy | Excellent wear resistance, good corrosion resistance | Ideal for valve seats, cutting tools |
Ni-Cr-B-Si (Colmonoy 88) | Nickel-chromium-boron-silicon alloy | Hardness, wear resistance, good corrosion resistance | Used in surface coating, repair applications |
These advanced materials are chosen for their unique properties that make them suitable for highly demanding applications. For example, Tantalum’s excellent corrosion resistance makes it ideal for chemical processing equipment, while Tungsten’s extreme melting point makes it a top choice for components exposed to very high temperatures.
Comparison of Advanced Materials
Comparing these advanced materials reveals how specific alloys can outperform others in certain conditions, making them more suitable for particular applications.
素材 | 強さ | 耐熱温度 | 耐食性 | 耐摩耗性 | Application Suitability |
---|---|---|---|---|---|
Nickel Alloy 263 | 高い | 素晴らしい | 中程度 | グッド | Turbines, high-temperature components |
タンタル | 中程度 | 高い | 素晴らしい | 中程度 | Chemical processing, medical devices |
タングステン | Extremely High | Outstanding | 中程度 | 素晴らしい | High-temp applications, aerospace |
Cobalt Alloy Stellite 6 | 中程度 | グッド | グッド | 素晴らしい | Cutting tools, valve seats |
インコネル738 | 非常に高い | 素晴らしい | グッド | 中程度 | Gas turbine components, aerospace |
These comparisons can help manufacturers choose the right material based on their specific needs, balancing factors like strength, temperature resistance, and cost.
Applications of Advanced Materials in LMD
The use of advanced materials in LMD extends its applicability to highly specialized fields where traditional manufacturing methods or materials would fail. These materials can meet stringent requirements, offering enhanced performance, longevity, and reliability in critical applications.
Specialized Applications:
産業 | 申し込み | 使用素材 | メリット |
---|---|---|---|
航空宇宙 | Combustion chamber liners, turbine blades | Nickel Alloy 263, Haynes 282 | High-temperature resistance, excellent mechanical properties |
メディカル | Custom implants, surgical tools | Tantalum, Cobalt-Chrome (Co-Cr) | 生体適合性、耐食性 |
エネルギー | Nuclear reactor components, wind turbine shafts | Tungsten, Rene 41 | Radiation resistance, strength under stress |
ディフェンス | Armored vehicles, military-grade hardware | Ti-5553, Tungsten | High strength, toughness, weight reduction |
自動車 | High-performance engine components, heat exchangers | Inconel 738, Titanium Ti-6Al-4V | Heat resistance, strength, reduced weight |
石油・ガス | Downhole tools, valve seats | Cobalt Alloy Stellite 6, Ni-Cr-B-Si | Wear resistance, durability in harsh environments |
エレクトロニクス | Semiconductor components, heat sinks | Niobium, Tungsten | Thermal conductivity, high-temperature capability |
Each application benefits from the specific properties of the advanced materials used. For instance, in the aerospace industry, the high-temperature resistance of Nickel Alloy 263 ensures that turbine blades maintain their integrity even under extreme operating conditions.
Standards and Specifications for LMD Materials
When selecting materials for レーザー金属蒸着, adherence to industry standards and specifications is essential to ensure quality, performance, and safety. Different industries have specific requirements that materials must meet, and these standards guide the selection process.
Industry Standards for LMD Materials:
素材 | 規格/仕様 | 産業 | 主な要件 |
---|---|---|---|
Inconel 625 | ASTM B443, AMS 5599 | Aerospace, Oil & Gas | High temperature, corrosion resistance, mechanical properties |
チタン Ti-6Al-4V | アストレムF136、アムス4911 | Medical, Aerospace | Biocompatibility, mechanical strength, fatigue resistance |
ステンレススチール316L | A240, ISO 5832-1 | Medical, Food Processing | Corrosion resistance, mechanical properties |
Cobalt-Chrome (Co-Cr) | ASTM F75、ISO 5832-4 | メディカル | 耐摩耗性、生体適合性 |
タングステン(W) | ASTM B777, MIL-T-21014 | Defense, Aerospace | High density, high-temperature resistance |
アルミニウム AlSi10Mg | ASTM B209, EN 485 | Automotive, Aerospace | 軽量、良好な熱伝導性 |
Nickel Alloy 263 | AMS 5872, ASTM B637 | 航空宇宙 | Oxidation resistance, high strength at elevated temperatures |
ルネ 41 | AMS 5545, ASTM B435 | 航空宇宙 | High-temperature mechanical properties |
ニオブ | ASTM B392, AMS 7850 | Electronics, Aerospace | Superconductivity, thermal stability |
タンタル (Ta) | ASTM B708, AMS 7831 | Medical, Chemical Processing | Corrosion resistance, biocompatibility |
These standards ensure that the materials used in LMD are of consistent quality and meet the necessary performance criteria for their intended applications. For example, ASTM F136 ensures that Titanium Ti-6Al-4V used in medical implants is safe and effective for long-term use in the human body.
Choosing the Right Metal Powder for Laser Metal Deposition
Selecting the right metal powder is a critical step in the LMD process. The choice of powder directly affects the quality, performance, and cost of the final product. Factors such as material properties, application requirements, and cost considerations all play a role in this decision-making process.
Factors to Consider:
ファクター | 説明 | Impact on Selection |
---|---|---|
Application Requirements | The specific needs of the final product, including mechanical properties, environmental conditions, and lifespan. | Dictates material selection based on performance criteria. |
材料特性 | Properties like melting point, thermal conductivity, and strength. | Determines process parameters and final part quality. |
粉体の形態 | The shape and size distribution of the powder particles. | Affects flowability, packing density, and layer uniformity. |
Cost Considerations | The cost of the metal powder relative to the project’s budget. | Balances material performance with economic feasibility. |
Supplier Availability | The availability of the metal powder from reliable suppliers. | Ensures consistent supply and quality for production. |
Standards Compliance | Adherence to industry standards and specifications. | Ensures quality and safety of the final product. |
Making an informed decision about the metal powder requires a balance between technical requirements and cost. For instance, while Tungsten offers superior temperature resistance, it is also more expensive than other options like Stainless Steel 316L, making it more suitable for high-end applications where performance justifies the cost.
Suppliers and Pricing for LMD Metal Powders
Sourcing the right metal powder from a reliable supplier is crucial for successful LMD. Suppliers offer a wide range of powders with varying prices depending on factors like material composition, purity, and particle size distribution.
Leading Suppliers and Pricing:
サプライヤー | 金属粉 | 価格帯(kgあたり) | 特集 |
---|---|---|---|
カーペンター・テクノロジー | Nickel Alloy 263, Haynes 282 | $300 – $500 | High-quality aerospace-grade powders, consistent particle size. |
ヘガネスAB | Stainless Steel 316L, Inconel 625 | $50 – $200 | Wide range of alloys, excellent flowability. |
LPWテクノロジー | Titanium Ti-6Al-4V, Aluminum AlSi10Mg | $250 – $450 | Custom powders, strict quality control for additive manufacturing. |
エリコン・メトコ | Cobalt Alloy Stellite 6, Rene 41 | $400 – $600 | High-performance powders, optimized for wear resistance. |
AP&C(GEアディティブ) | Ti-5553, Tantalum | $500 – $800 | Aerospace and medical grade powders, biocompatibility. |
サンドビック | Inconel 738, Tungsten | $200 – $700 | High-temperature alloys, extensive testing and certification. |
Praxis Powder Technology | Niobium, Cobalt-Chrome (Co-Cr) | $300 – $600 | Specialized powders for medical and electronic applications. |
GKNアディティブ | Nickel Alloy 263, Haynes 282 | $300 – $500 | Customized powder blends, excellent oxidation resistance. |
テクナ | アルミニウムAlSi10Mg、ステンレス鋼316L | $50 – $150 | Spherical powders, optimized for additive manufacturing. |
ヴィーガ | Tantalum, Tungsten | $500 – $900 | High-purity powders, tailored for specific applications. |
Prices vary widely depending on the material and supplier, reflecting differences in purity, production method, and market demand. For example, Tantalum and Tungsten powders are on the higher end of the price spectrum due to their complex processing and high demand in specialized industries.
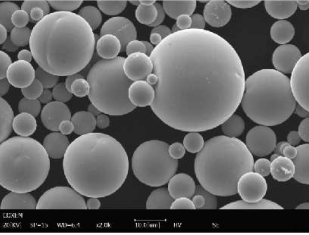
比較 レーザー金属蒸着 to Other Additive Manufacturing Techniques
Laser Metal Deposition is just one of many additive manufacturing techniques available today. Understanding how LMD compares to other methods can help you choose the best process for your specific needs.
Comparison with Other Additive Manufacturing Techniques:
Technique | 素材の柔軟性 | 表面仕上げ | スピード | 精密 | コスト | 用途 |
---|---|---|---|---|---|---|
レーザー金属蒸着 | 高い | 中程度 | ミディアム | 高い | 高い | Aerospace, repair, complex geometries |
Selective Laser Sintering (SLS) | 高い | 中程度 | ミディアム | 高い | 中程度 | Prototyping, small batch production |
電子ビーム溶解(EBM) | ミディアム | 中程度 | ミディアム | 高い | 高い | 航空宇宙、医療用インプラント |
Fused Deposition Modeling (FDM) | 低い | 低い | 高い | 低い | 低い | Prototyping, consumer products |
ダイレクトメタルレーザー焼結(DMLS) | 高い | 高い | ミディアム | 非常に高い | 高い | Medical, aerospace, intricate parts |
バインダー・ジェット | ミディアム | 低い | 高い | ミディアム | 中程度 | Large parts, casting molds |
指向性エネルギー蒸着(DED) | 高い | 中程度 | ミディアム | 高い | 高い | Repair, large components, aerospace |
LMD stands out for its ability to work with a wide range of materials and its precision in creating complex geometries. However, it tends to be more expensive and slower compared to other techniques like FDM, which is more suited for rapid prototyping with less demanding material requirements.