概要 Atomisation Plant
Atomisation plants are industrial facilities that specialize in producing metal powders through the atomisation process. This process involves the disintegration of molten metal into fine droplets, which solidify into powders. These metal powders are crucial in various industries, including aerospace, automotive, electronics, and additive manufacturing.
Key Components of an Atomisation Plant
- Melting Furnace: Heats the metal to a molten state.
- Atomisation Nozzle: Breaks the molten metal into fine droplets.
- Cooling Chamber: Solidifies the droplets into powder.
- Collection System: Gathers the metal powder.
- Sieving and Classification Unit: Sorts the powder by particle size.
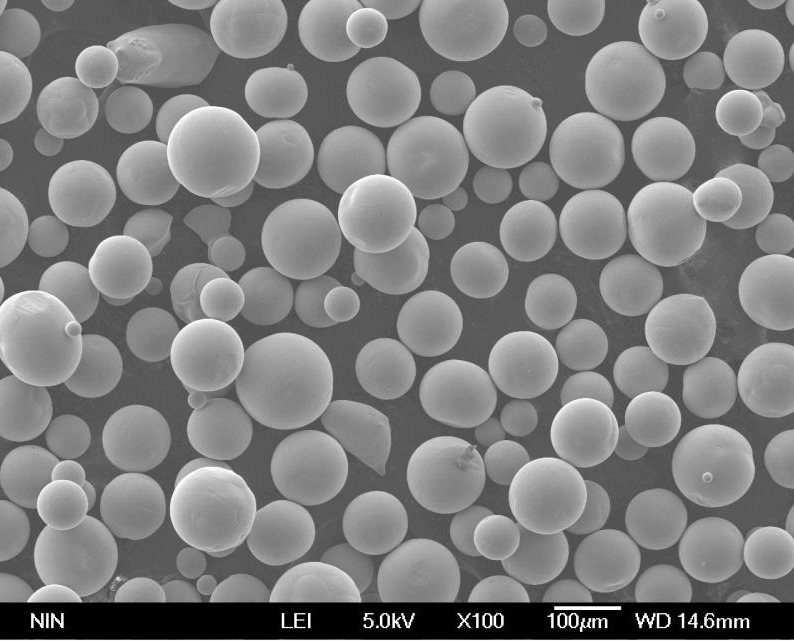
Types of Metal Powders Produced
1. Stainless Steel Powder
Stainless steel powders are known for their corrosion resistance and strength. They are used in industries like aerospace, medical devices, and food processing.
2. Titanium Powder
Titanium powders are lightweight and possess excellent strength and corrosion resistance. They are essential in aerospace, medical implants, and sporting goods.
3. Aluminum Powder
Aluminum powders are light, strong, and have good corrosion resistance. They are widely used in the automotive and aerospace sectors.
4. Copper Powder
Copper powders are highly conductive and used in electrical and electronic applications, including conductive inks and coatings.
5. Nickel Powder
Nickel powders are used in superalloys and batteries, offering high strength and resistance to oxidation and corrosion.
6. Cobalt Powder
Cobalt powders are crucial in high-temperature and wear-resistant applications, such as in cutting tools and aerospace engines.
7. Iron Powder
Iron powders are used in a variety of applications, including automotive parts, magnetic materials, and sintered components.
8. Zinc Powder
Zinc powders are primarily used for galvanizing and in the production of zinc-rich paints.
9. Tungsten Powder
Tungsten powders are used for their high melting point and density, making them ideal for heavy-duty applications like radiation shielding and high-performance tools.
10. Bronze Powder
Bronze powders, a blend of copper and tin, are used in decorative items, bearings, and electrical contacts.
Composition and Properties of Metal Powders
金属粉 | 構成 | プロパティ |
---|---|---|
ステンレス鋼粉末 | Fe、Cr、Ni、Mo | 耐食性、高強度 |
チタン粉末 | Ti | 軽量、高強度、耐食性 |
アルミニウムパウダー | Al | Lightweight, good corrosion resistance |
銅粉末 | 銅 | High electrical conductivity |
ニッケル粉末 | Ni | 高強度、耐酸化性 |
コバルト粉末 | Co | Wear resistance, high temperature stability |
鉄粉末 | Fe | High magnetic properties |
亜鉛パウダー | 亜鉛 | Corrosion resistance, used in galvanizing |
タングステン粉末 | W | High density, high melting point |
Bronze Powder | 銅、錫 | Good conductivity, wear resistance |
Applications of Metal Powders
金属粉 | 用途 |
---|---|
ステンレス鋼粉末 | Aerospace, medical devices, food processing |
チタン粉末 | Aerospace, medical implants, sporting goods |
アルミニウムパウダー | 自動車、航空宇宙 |
銅粉末 | Electrical, electronics |
ニッケル粉末 | Superalloys, batteries |
コバルト粉末 | Cutting tools, aerospace engines |
鉄粉末 | Automotive parts, magnetic materials |
亜鉛パウダー | Galvanizing, zinc-rich paints |
タングステン粉末 | Radiation shielding, high-performance tools |
Bronze Powder | Decorative items, bearings, electrical contacts |
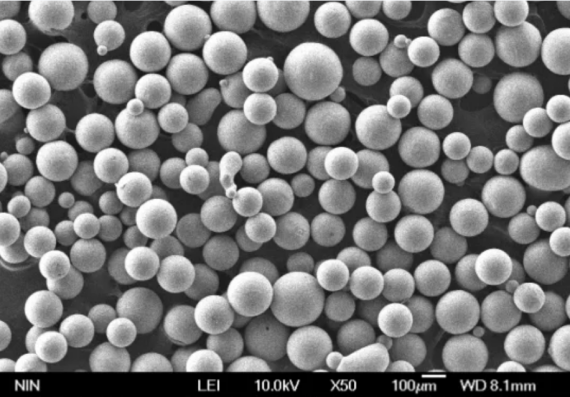
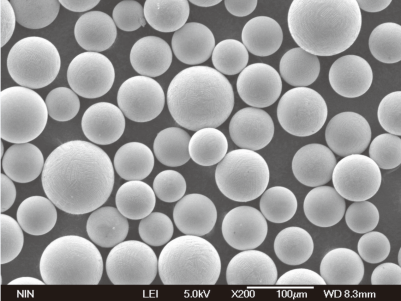
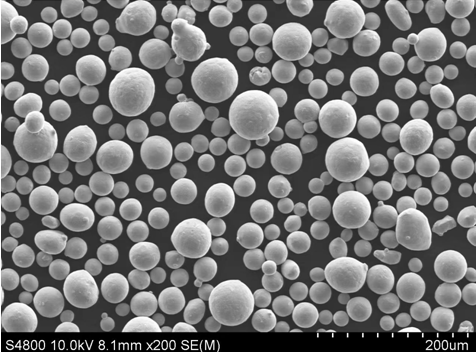
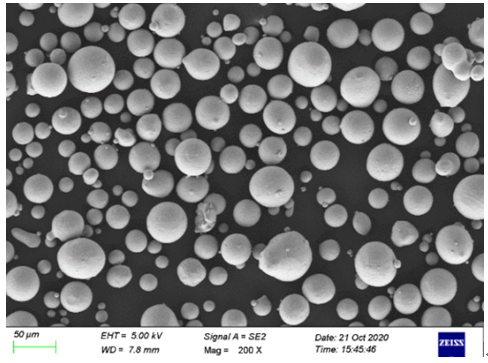
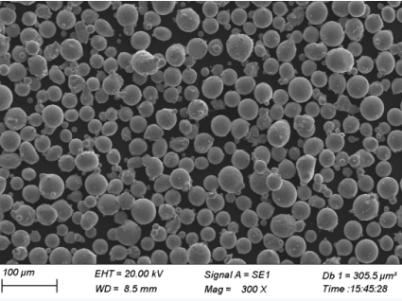
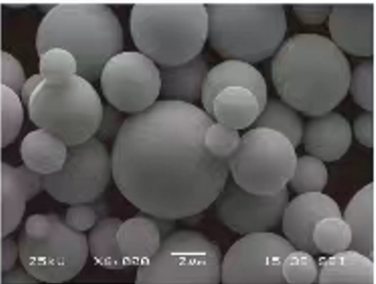
Specifications and Standards for Metal Powders
金属粉 | 仕様 | Sizes (µm) | グレード | 規格 |
---|---|---|---|---|
ステンレス鋼粉末 | ASTM B214 | 1-150 | 304L、316L | ASTM、ISO |
チタン粉末 | ASTM F67, F1580 | 15-45 | CP-Ti, Ti-6Al-4V | ASTM、ISO |
アルミニウムパウダー | ASTM B212 | 10-100 | 1100, 7075 | ASTM、ISO |
銅粉末 | ASTM B833 | 5-100 | C11000 | ASTM、ISO |
ニッケル粉末 | ASTM B330 | 5-100 | Ni 200, Ni 201 | ASTM、ISO |
コバルト粉末 | ASTM B330 | 10-100 | Co-27, Co-28 | ASTM、ISO |
鉄粉末 | ASTM B213 | 1-150 | Fe-99, Fe-100 | ASTM、ISO |
亜鉛パウダー | ASTM B852 | 5-100 | Zn-1, Zn-2 | ASTM、ISO |
タングステン粉末 | ASTM B777 | 1-50 | W-1, W-2 | ASTM、ISO |
Bronze Powder | ASTM B213 | 5-100 | CuSn8, CuSn10 | ASTM、ISO |
Suppliers and Pricing of Metal Powders
サプライヤー | 金属粉末 | 価格帯(kgあたり) | 地域 |
---|---|---|---|
ヘガネスAB | Stainless Steel, Iron | $10 – $100 | Europe, Americas |
GKNホエガネス | チタン、アルミニウム | $50 – $500 | グローバル |
サンドビック・オスプレイ | Nickel, Cobalt | $30 – $400 | グローバル |
アメテック | Copper, Bronze | $20 – $150 | Americas |
カーペンター | タングステン、亜鉛 | $100 – $1000 | グローバル |
Advantages and Limitations of Metal Powders
金属粉 | メリット | 制限事項 |
---|---|---|
ステンレス鋼粉末 | High strength, corrosion resistance | 高い、重い |
チタン粉末 | Lightweight, biocompatible | 高コスト、加工が難しい |
アルミニウムパウダー | 軽量、優れた熱特性 | Lower strength compared to steel |
銅粉末 | 優れた導電性 | 高価、酸化しやすい |
ニッケル粉末 | High temperature stability, strength | Costly, difficult to machine |
コバルト粉末 | Wear resistance, high temperature capability | Expensive, hard to process |
鉄粉末 | Cost-effective, magnetic properties | Susceptible to corrosion |
亜鉛パウダー | Corrosion resistance, low cost | Low strength, not suitable for high-load applications |
タングステン粉末 | High density, high melting point | Extremely hard, difficult to process |
Bronze Powder | Good conductivity, aesthetic appeal | Moderate strength, can tarnish |
Composition of Atomisation Plant
The composition of an atomisation plant varies depending on the specific needs and the type of metal powders being produced. However, the core components typically include:
- Melting Furnaces: These can be induction furnaces, arc furnaces, or gas-fired furnaces, chosen based on the melting point and characteristics of the metal.
- Atomisation Chambers: Designed to withstand high temperatures and pressures, usually made of stainless steel or other heat-resistant materials.
- Cooling Systems: These can be water-cooled, gas-cooled, or air-cooled, depending on the cooling rate required for the specific metal powder.
- Collection Systems: Often involve cyclones, bag filters, and hoppers to efficiently gather the fine powders.
- Sieving and Classification Units: Use vibrating screens or centrifugal classifiers to sort powders by particle size.
Characteristics of Atomisation Plant
Atomisation plants are characterized by several key attributes:
- 生産能力: Ranges from small batch production to large-scale industrial output.
- Flexibility: Capable of producing a wide range of metal powders.
- 効率性: High yield with minimal waste.
- 精密: Produces powders with consistent particle size and distribution.
- 安全性: Equipped with advanced safety features to handle high temperatures and pressures.
の利点 Atomisation Plant
Efficiency and Yield
Atomisation plants are designed for high efficiency, ensuring maximum yield from the raw material. This means more metal powder produced with less waste.
汎用性
These plants can produce a wide variety of metal powders, catering to different industrial needs. Whether you need stainless steel for aerospace applications or copper for electrical components, an atomisation plant can handle it.
High Quality
The powders produced are of high quality, with uniform particle size and excellent purity. This makes them suitable for demanding applications in various high-tech industries.
スケーラビリティ
From small-scale production for research and development to large-scale industrial manufacturing, atomisation plants can be scaled to meet different production requirements.
Cost-Effective
While the initial setup cost might be high,
the long-term benefits and efficiency make atomisation plants a cost-effective solution for metal powder production.
Disadvantages of Atomisation Plant
High Initial Investment
Setting up an atomisation plant requires significant capital investment. The cost of equipment, installation, and infrastructure can be substantial.
Complex Operation
The operation of an atomisation plant is complex and requires skilled personnel. Proper training and experience are essential to ensure efficient and safe operation.
メンテナンス
Regular maintenance is crucial to keep the plant running smoothly. This can add to the operational costs and requires a dedicated maintenance team.
Energy Consumption
Atomisation processes, especially those involving high melting point metals like tungsten or titanium, are energy-intensive. This can lead to high operational costs.
Comparing Metal Powders: Pros and Cons
金属粉 | 長所 | 短所 |
---|---|---|
ステンレス鋼粉末 | Strong, corrosion-resistant | 高い、重い |
チタン粉末 | 軽量、高強度 | Very expensive, hard to process |
アルミニウムパウダー | Light, good corrosion resistance | Weaker compared to other metals |
銅粉末 | 優れた導電性 | Costly, prone to oxidation |
ニッケル粉末 | Strong, high temp resistance | High cost, hard to machine |
コバルト粉末 | Durable, heat-resistant | 高価で処理が難しい |
鉄粉末 | Affordable, magnetic | Corrosion-prone |
亜鉛パウダー | Cheap, corrosion-resistant | Weak, unsuitable for high-stress uses |
タングステン粉末 | Very dense, high melting point | Extremely hard, tough to process |
Bronze Powder | Good conductivity, aesthetic | Moderate strength, can tarnish |
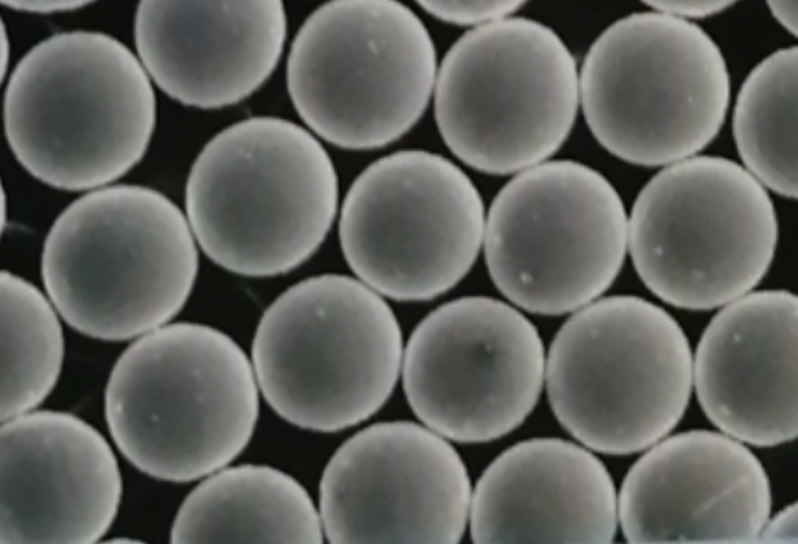
よくある質問
What is an atomisation plant?
An atomisation plant is an industrial facility that produces metal powders by breaking down molten metal into fine droplets which then solidify into powder form.
What are the key components of an atomisation plant?
Key components include melting furnaces, atomisation nozzles, cooling chambers, collection systems, and sieving and classification units.
Which industries use metal powders produced by atomisation plants?
Industries such as aerospace, automotive, electronics, and additive manufacturing heavily rely on metal powders.
What are the advantages of using atomisation plants?
Advantages include high efficiency, versatility in powder production, high quality of powders, scalability, and cost-effectiveness in the long run.
What are the main types of metal powders produced?
Main types include stainless steel, titanium, aluminum, copper, nickel, cobalt, iron, zinc, tungsten, and bronze powders.
How are metal powders classified in an atomisation plant?
Metal powders are classified using sieving and classification units which sort the powders by particle size.
What are the challenges of operating an atomisation plant?
Challenges include high initial investment, complex operation, maintenance needs, and high energy consumption.
How does the atomisation process work?
The atomisation process involves melting the metal, then disintegrating the molten metal into fine droplets using an atomisation nozzle, followed by cooling and solidifying the droplets into powder form.
Can atomisation plants be used for all metals?
While atomisation plants can produce a wide variety of metal powders, the process parameters need to be adjusted based on the specific properties of each metal.
What is the cost range for metal powders produced in atomisation plants?
The cost can vary widely depending on the type of metal powder, ranging from $10 to $1000 per kilogram.
結論
Atomisation plants play a crucial role in modern manufacturing by producing high-quality metal powders essential for various industries. Despite the high initial investment and operational complexities, the benefits of efficiency, versatility, and scalability make them a valuable asset. Whether you’re in aerospace, automotive, or electronics, the powders produced in these plants are integral to your products and innovations.