概要 3Dプリンティング金属粉末
金属粉末の3Dプリンティングは、金属積層造形(AM)とも呼ばれ、デジタル設計から複雑な金属部品を直接作成できる革新的な技術である。材料を削り取る従来の減法的製造とは異なり、3Dプリンティングは金属粉末を原料として、層ごとに部品を作り上げます。
3Dプリント用金属粉末の主な特徴には、以下のようなものがある:
テクノロジー | 説明 |
---|---|
パウダーベッド・フュージョン | レーザーまたは電子ビームが、パウダーベッドの各領域を融合し、パーツを層ごとに形成する。 |
直接エネルギー蒸着 | 集束された熱源が金属粉末やワイヤーを溶かしながら堆積させ、部品を作り上げる |
バインダー・ジェット | 液体接合剤が各層の金属粉末粒子を選択的に接合する |
従来の製造に比べ、3Dプリンティング金属は可能にする:
- 複雑で有機的な形状をより自由にデザイン
- 専用工具不要のオンデマンドカスタマイズ部品
- 減算法による廃棄物の削減
- 1つの部品として印刷された連結アセンブリ
- トポロジー最適化による軽量化
技術が成熟するにつれ、金属3Dプリンティングは、航空宇宙、自動車、医療、エネルギーなどの業界において、プロトタイプから生産へと移行しつつある。
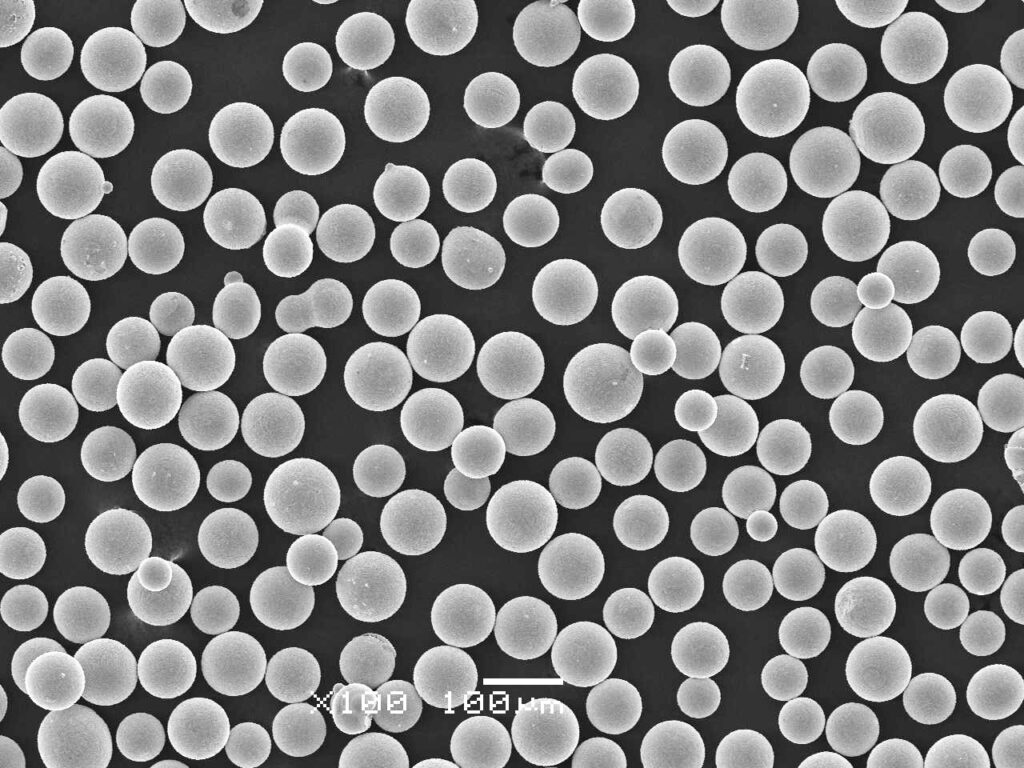
応用例 3Dプリンティング金属粉末
金属粉末を使用した3Dプリンティングは、業界を問わず多様な用途があります。主な用途には次のようなものがある:
産業 | 用途 |
---|---|
航空宇宙 | エンジン部品、機体部品、ターボ機械 |
自動車 | 軽量化部品、カスタム金型、パフォーマンス部品 |
メディカル | 歯科用コーピング、インプラント、外科用器具 |
インダストリアル | 最終生産部品、コンフォーマル冷却、工具 |
この技術は、カスタム形状の複雑で高価値な金属部品の少量生産に最適である。従来の製造と比較した主な利点は以下の通り:
- 部品の統合 – 多くの組み立て部品を 1 つの統合部品として印刷できる
- マス・カスタマイゼーション – パーソナライズされた金属部品をオンデマンドで製造可能
- ラピッドプロトタイピング – デザインを素早く反復し、検証できる
- 廃棄物の削減 – 各パーツに必要な金属粉のみを使用
- 軽量化 – 格子と薄い壁を持つ有機的な形状が軽量化を実現
プリントされた金属部品の品質と再現性が向上するにつれて、3Dプリントはプロトタイプから最終用途の生産用途へと移行しつつある。
3Dプリンティング用金属粉末
粉末床溶融法および指向性エネルギー堆積法3Dプリンティングでは、さまざまな金属を使用できます。一般的な合金は以下の通りです:
合金 | 特徴 | 用途 |
---|---|---|
ステンレス | 耐食性、高強度 | 航空宇宙、自動車、工業 |
アルミニウム | 軽量、高強度、機械加工可能 | 航空宇宙、自動車 |
チタン | 生体適合性、高強度対重量 | 航空宇宙、医療 |
コバルト・クローム | 耐摩耗性、生体適合性 | 医療、歯科 |
ニッケル合金 | 耐熱性、耐食性 | 航空宇宙、エネルギー |
パウダーは直径10-100ミクロンの球状である。主な特徴は以下の通り:
- 粒度分布 – 充填密度、表面仕上げに影響
- モルフォロジー – 表面が滑らかな球状粒子が最もよく融合する
- 流動性 – 均一な層と材料供給を保証
- 見掛け密度 – 密度が高いほど機械的特性が向上する
- 再利用 – 粉末を回収して再利用することで、材料コストを削減できる
ほとんどの金属は、酸化を防ぐために不活性な印刷環境を必要とする。ビルドチャンバーは印刷中、アルゴンまたは窒素ガスで満たされる。
金属3Dプリンタの仕様
金属粉末用3Dプリンターは、24時間365日稼働するように設計された産業用システムです。代表的な仕様は以下の通り:
パラメータ | 典型的な範囲 |
---|---|
ビルド・ボリューム | 100-500 mm x 100-500 mm x 100-500 mm |
レイヤーの厚さ | 20-100ミクロン |
レーザー出力 | 100-500 W |
スキャン速度 | 最大10 m/s |
ビーム径 | 50~100ミクロン |
不活性ガス | アルゴン、窒素 |
パウダーハンドリング | クローズド・ループ・リサイクル・システム |
完全なワークフローには、粉末回収システムや後処理装置のような他の付属品が必要になる場合がある。システム要件は、印刷される金属合金や最終用途によって異なります。
金属3Dプリンティングの規格と設計
高品質のプリントパーツを確保するために、金属3Dプリントにはいくつかの重要な設計基準があります:
スタンダード | 説明 |
---|---|
STLファイル形式 | 3Dモデル形状を表現するための標準ファイルフォーマット |
壁厚 | 故障を避けるため、最低肉厚は0.3~0.5mmとする。 |
対応アングル | オーバーハングでは、30~45°以上の角度をサポートする必要がある。 |
エスケープホール | 内部チャンネルから余分なパウダーを取り除くのに必要 |
表面仕上げ | 印刷したままの表面は粗く、後加工で仕上がりを改善 |
設計者は、残留応力、異方性材料特性、粉末除去などの要因を考慮して、金属印刷部品を作成する必要があります。シミュレーションソフトウェアは、印刷前にデジタルで設計を検証するのに役立ちます。
金属3Dプリンティングシステムのサプライヤー
産業用金属3Dプリンティング装置の主なサプライヤーは以下の通り:
会社概要 | モデル | コスト範囲 |
---|---|---|
イーオーエス | FORMIGA, EOS Mシリーズ | $100,000 – $1,000,000+ |
3Dシステムズ | ProX、DMPシリーズ | $100,000 – $1,000,000+ |
GEアディティブ | コンセプトレーザーM2、Xライン | $400,000 – $1,500,000+ |
トランプ | TruPrint 1000、5000、7000シリーズ | $500,000 – $1,500,000+ |
SLMソリューション | SLM500、SLM800 | $400,000 – $1,500,000+ |
システムは、小型のエントリーレベルの金属プリンターから、大判の産業用機械まで幅広い。コストは、造形量、材料、生産性によって異なる。追加費用には、設置、トレーニング、保守契約、粉体材料などが含まれる。
金属3Dプリンティングサプライヤーの選択
産業用金属3Dプリントシステムを選択する際、考慮すべき主な要素には以下が含まれます:
ファクター | 説明 |
---|---|
ビルド・ボリューム | 予想される部品サイズに合わせ、支持構造に余裕を持たせる |
材料 | 対応する金属と合金の範囲 |
生産性 | 建設率、稼働率、総事業費 |
パウダーハンドリング | クローズド・ループ、リサイクル機能 |
ソフトウェア | サポート、シミュレーション、最適化のための機能 |
後処理 | 自動と手動のサポート除去、表面仕上げ |
トレーニング | 設置サポート、オペレーター・トレーニング、メンテナンス手順 |
サービス | 保守契約、応答時間、信頼性 |
パイロットビルド、現場視察、顧客リファレンスは、意図された用途におけるプリンター性能の検証に役立ちます。総所有コストモデルでは、システムの耐用年数にわたるすべての費用を考慮します。
金属3Dプリンティングと従来の製造の比較
3Dプリント金属部品は、CNC機械加工、鋳造、金属射出成形などの従来の製造プロセスと比較して、利点と限界があります:
3Dプリンティング・メタル | 伝統的製造業 | |
---|---|---|
部品単価 | 少量では高いが、量が増えると低下する | 大量生産では低く、初期金型費用は高い |
パート・コンプレックス | 複雑な形状でも追加コストなし | 複雑なCNCプログラムや金型のコスト増 |
ビルドレート | 部品サイズとプリンターにより異なる | 通常、製造速度は速い |
材料 | 限られた材料オプション、等方的特性 | 幅広い材料選択、多くの場合異方性 |
後処理 | サポート除去、機械加工、仕上げがしばしば必要 | 仕上げ工程が必要な場合がある |
スケーラビリティ | 少ない製造量ではスケーリングが制限される | 数量制限のない大量生産 |
デザインの自由度 | 幾何学的な複雑さは無限 | プロセスの制限に基づく設計上の制約 |
理想的な生産シナリオでは、アプリケーションの要件に基づいて、3Dプリンティングと従来の製造の両方を相乗的に使用することが多い。
金属プリント部品の後処理方法
印刷後、3D金属部品は通常、所望の仕上げと公差を達成するための後処理を必要とする:
方法 | 説明 |
---|---|
サポート解除 | 支持構造の化学的溶解または機械的除去 |
ストレス解消 | 印刷時の残留応力を緩和する熱処理 |
熱間静水圧プレス | 熱と圧力を加えて部品を緻密化する |
表面仕上げ | 機械加工、研削、研磨、ブラストによる表面仕上げの改善 |
メッキ | 腐食保護または耐摩耗性向上のための電気めっき |
3Dプリントされた金属部品用に調整された自動サポート除去、CNC機械加工、表面仕上げシステムは、後処理を合理化するのに役立ちます。これらのステップは、最終部品アプリケーションの要件を満たすために不可欠です。
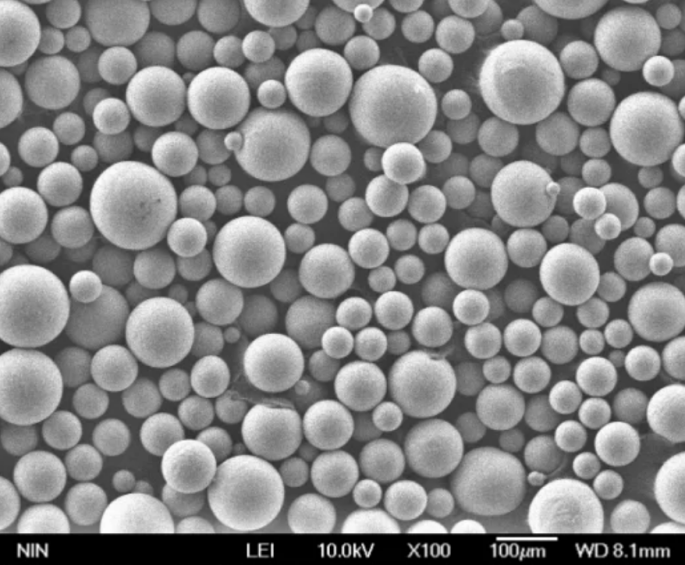
金属3Dプリンタの操作とメンテナンス
金属積層造形で堅牢な生産を維持するには、適切な運用と予防保守が重要です:
アクティビティ | 説明 |
---|---|
粉の充填 | PPEを使用して、粉体ホッパーを慎重に計量し、補充する。 |
ビルドプレートのレベリング | 均一なレイヤーのために、プリント前にビルドプレートが水平であることを確認する。 |
プリントのモニタリング | 火薬の飛散、発煙、部品の歪みなどのエラーをチェックする。 |
パラメータの最適化 | レーザー出力、速度、ハッチ間隔などの設定を調整し、密度を高める |
フィルターの交換 | 使用間隔に基づき、ガスフィルターおよびパーティクルフィルターを交換 |
クリーニングとテスト | 定期的に埃やゴミを取り除き、レーザーのパワーメーターをテストする。 |
磨耗部品の交換 | リコーターブレード、ワイパー、シールが摩耗したら交換すること |
スタッフトレーニングや予防保守契約により、プリンターの稼働時間を最大化し、プロダクションアプリケーションの活用を支援します。
よくある質問
質問 | 回答 |
---|---|
金属3Dプリントの精度は? | 寸法精度は約±0.1~0.2%で、フィーチャーの精度は±50ミクロンである。後処理により公差はさらに向上します。 |
どのような表面仕上げが可能ですか? | 印刷したままの表面は5~15ミクロンRaとかなり粗い。機械加工と研磨により、1ミクロンRa以下の仕上げが可能です。 |
3Dプリントできる金属は? | 一般的な合金は、ステンレス鋼、アルミニウム、チタン、ニッケル合金、コバルトクロムである。新しい合金は絶えず導入されている。 |
金属プリント部品の多孔性は? | 適切なパラメータを用いれば、ほとんどの金属で密度は99%以上に達します。熱間静水圧プレスは部品をさらに高密度化します。 |
どのようなサポート体制が必要か? | 支持格子は必要な場所に印刷され、印刷後に取り除かれる。戦略的な設計により、その使用は最小限に抑えられている。 |
どのような後処理が必要ですか? | サポート除去、応力除去、表面仕上げ、検査が一般的に必要とされるステップである。 |