Qu'est-ce que Prototypage rapide au laser?
Le prototypage rapide au laser (PRL) révolutionne la façon dont les industries abordent la fabrication. Vous êtes-vous déjà demandé comment nous pouvions créer des modèles complexes à la vitesse de l'éclair ? Imaginez une technologie qui transforme les dessins numériques en objets tangibles avec une précision inégalée. C'est la magie du LRP. Dans cet article, nous allons nous pencher sur les tenants et les aboutissants du prototypage rapide au laser, depuis ses poudres métalliques de pointe jusqu'à son large éventail d'applications.
Aperçu du prototypage rapide par laser
Le prototypage rapide par laser est une technologie sophistiquée qui utilise l'énergie laser pour créer des objets en 3D couche par couche. Cette technique, qui fait partie de la catégorie plus large de la fabrication additive, est réputée pour sa capacité à produire des structures complexes et très détaillées. Que vous travailliez dans l'aérospatiale, l'automobile ou même la santé, la PRL offre des avantages inégalés en termes de vitesse, de précision et d'efficacité des matériaux. Mais comment cela fonctionne-t-il et qu'est-ce qui le rend si efficace ? Voyons cela en détail.
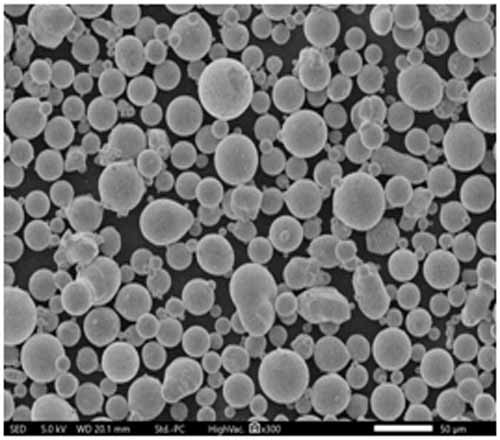
La composition des matériaux de prototypage rapide par laser
Lorsqu'il s'agit de PRL, la composition des matériaux utilisés est cruciale. Les poudres métalliques sont les vedettes du spectacle, chacune offrant des propriétés uniques qui les rendent adaptées à différentes applications. Mais que sont exactement ces poudres métalliques et comment leur composition affecte-t-elle le produit final ?
Types et caractéristiques des poudres métalliques pour le prototypage rapide par laser
Il est essentiel de comprendre les différents types de poudres métalliques disponibles pour la PRL. Vous trouverez ci-dessous une analyse détaillée des modèles de poudres métalliques spécifiques, de leur composition et de leurs caractéristiques uniques.
Poudre métallique | Composition | Caractéristiques principales | Applications |
---|---|---|---|
Acier inoxydable 316L | Fer (Fe), Chrome (Cr), Nickel (Ni), Molybdène (Mo) | Résistance élevée à la corrosion, bonne soudabilité | Implants médicaux, équipements de transformation des aliments |
AlSi10Mg | Aluminium (Al), Silicium (Si), Magnésium (Mg) | Léger, haute conductivité thermique | Pièces automobiles, composants aérospatiaux |
Inconel 718 | Nickel (Ni), Chrome (Cr), Fer (Fe), Molybdène (Mo) | Haute résistance, résistant à l'oxydation | Aubes de turbines, moteurs de fusées |
Titane Ti6Al4V | Titane (Ti), Aluminium (Al), Vanadium (V) | Rapport résistance/poids élevé, biocompatibilité | Implants médicaux, composants aérospatiaux |
Chrome cobalt (CoCrMo) | Cobalt (Co), Chrome (Cr), Molybdène (Mo) | Grande résistance à l'usure et à la corrosion | Implants dentaires, implants orthopédiques |
Acier maraging (MS1) | Fer (Fe), Nickel (Ni), Cobalt (Co), Molybdène (Mo) | Haute résistance, robustesse, facilité d'usinage | Outillage, composants aérospatiaux |
Cuivre (Cu) | Cuivre (Cu) | Excellente conductivité thermique et électrique | Échangeurs de chaleur, composants électriques |
Hastelloy X | Nickel (Ni), Chrome (Cr), Fer (Fe), Molybdène (Mo) | Résistance aux températures élevées, résistance à l'oxydation | Moteurs à turbine à gaz, fours industriels |
Acier inoxydable 316L | Fer (Fe), Chrome (Cr), Nickel (Ni), Molybdène (Mo) | Résistance élevée à la corrosion, bonne soudabilité | Implants médicaux, équipements de transformation des aliments |
Inconel 625 | Nickel (Ni), chrome (Cr), molybdène (Mo), niobium (Nb) | Excellente résistance à la fatigue, haute résistance à la traction | Traitement chimique, applications marines |
Aluminium AlSi10Mg | Aluminium (Al), Silicium (Si), Magnésium (Mg) | Léger, haute conductivité thermique | Pièces automobiles, composants aérospatiaux |
Avantages de la Prototypage rapide au laser
Pourquoi le prototypage rapide au laser prend-il d'assaut le monde de la fabrication ? Examinons quelques-uns des principaux avantages qui font de cette technologie un facteur de changement.
Vitesse et efficacité
Les méthodes de fabrication traditionnelles peuvent prendre beaucoup de temps, surtout lorsqu'il s'agit de produire des pièces complexes. Le prototypage rapide au laser, en revanche, permet de créer des modèles complexes en une fraction du temps. Imaginez que vous ayez besoin d'une pièce qu'il est presque impossible d'usiner. Avec le prototypage rapide au laser, elle peut être prête en quelques heures au lieu de plusieurs semaines.
Précision et exactitude
Le prototypage rapide au laser permet de créer des composants de haute précision. La capacité du laser à se concentrer sur des points microscopiques permet d'obtenir des détails extrêmement fins. Ceci est particulièrement important dans les industries où le moindre écart peut avoir des conséquences significatives, comme l'aérospatiale ou la fabrication d'appareils médicaux.
Polyvalence des matériaux
De l'acier inoxydable aux alliages exotiques, la gamme des matériaux pouvant être utilisés dans la PRL est vaste. Cette polyvalence signifie que la technologie peut être adaptée à un large éventail d'applications, qu'il s'agisse de produire des composants légers pour l'industrie automobile ou des implants biocompatibles pour les soins de santé.
Rentabilité pour les conceptions complexes
Pour les conceptions complexes ou personnalisées, le coût de la fabrication traditionnelle peut être prohibitif en raison de l'outillage nécessaire. Le LRP élimine la nécessité d'un outillage spécifique, ce qui en fait une option plus rentable, en particulier pour la production de faibles volumes ou pour les prototypes.
Réduction des déchets
Dans la fabrication soustractive traditionnelle, une quantité importante de matériau est gaspillée car l'excédent est coupé à partir de la matière première. Le LRP, en tant que processus additif, n'utilise que le matériau nécessaire à la création de la pièce, ce qui réduit considérablement les déchets et en fait une option plus durable.
Applications du prototypage rapide par laser
La polyvalence du prototypage rapide par laser se reflète dans son large éventail d'applications. Voici un aperçu de la manière dont différentes industries exploitent cette technologie.
L'industrie | application | Avantages |
---|---|---|
Aérospatiale | Aubes de turbines, composants structurels | Pièces légères et très résistantes ; réduction des délais d'exécution |
Automobile | Composants de moteur, pièces sur mesure | Rentabilité pour la production de faibles volumes, amélioration des performances |
Médical | Implants, prothèses | Personnalisation pour les patients individuels, biocompatibilité |
Électronique grand public | Composants du boîtier, conceptions complexes | Fabrication précise, itération rapide |
Bijoux | Modèles personnalisés, motifs complexes | Haute précision, temps de production réduit |
L'énergie | Échangeurs de chaleur, composants de turbines | Résistance aux températures élevées, utilisation efficace des matériaux |
Défense | Composants d'armes, armures légères | Conceptions personnalisées, prototypage rapide pour les essais |
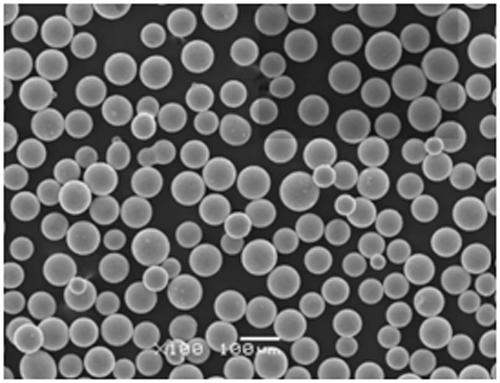
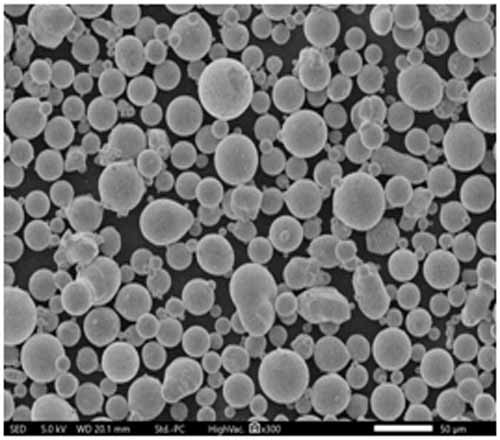
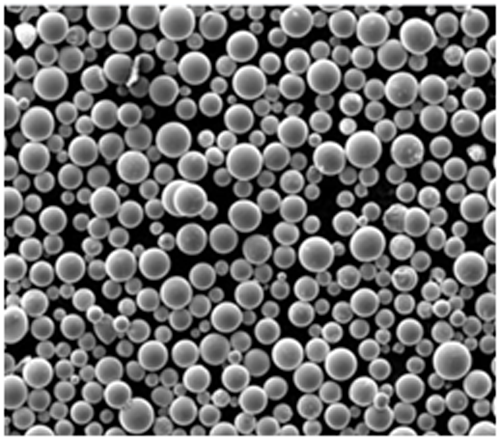
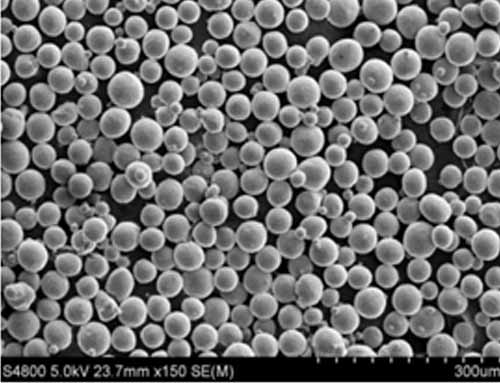
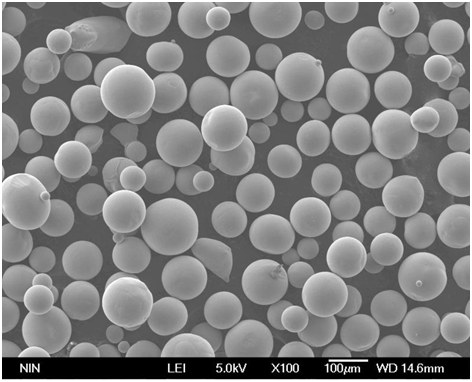
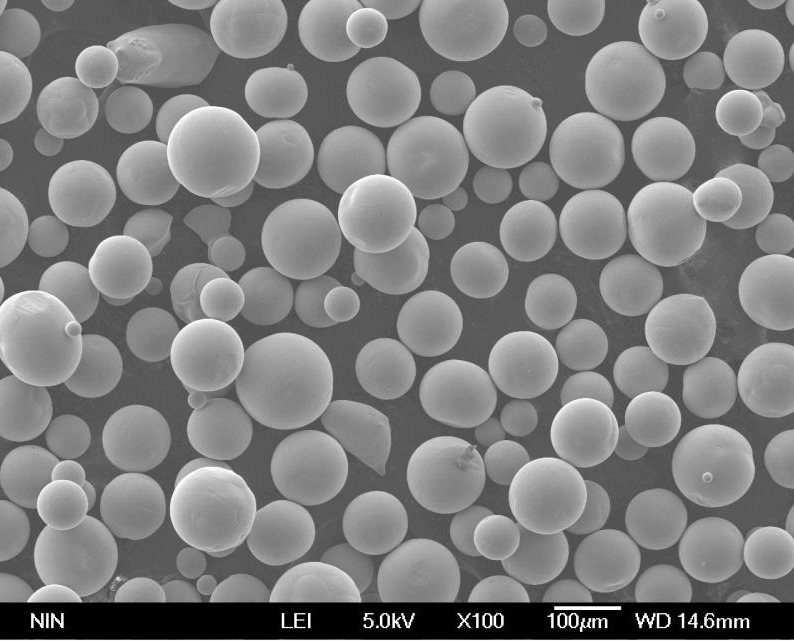
Spécifications, tailles, qualités et normes dans le domaine du prototypage rapide par laser
Il est essentiel de comprendre les spécifications, les dimensions et les qualités des matériaux utilisés dans les PRL pour sélectionner les matériaux adéquats pour votre projet. Vous trouverez ci-dessous un tableau détaillé décrivant certaines des normes et spécifications les plus courantes.
Matériau | Standard | Grade | Taille Disponibilité |
---|---|---|---|
Acier inoxydable 316L | ASTM F138, ISO 5832-1 | 1.4404 | Taille des poudres : 15-45 µm, 45-100 µm |
AlSi10Mg | ISO 3522 | 3.2371 | Taille des poudres : 20-63 µm, 63-150 µm |
Inconel 718 | AMS 5662, ASTM B637 | 2.4668 | Taille des poudres : 15-53 µm |
Titane Ti6Al4V | ASTM F1472, ISO 5832-3 | 3.7165 | Taille des poudres : 15-45 µm |
Chrome cobalt (CoCrMo) | ISO 5832-4, ASTM F1537 | 2.4778 | Taille des poudres : 10-45 µm |
Acier maraging (MS1) | AMS 6514 | 1.2709 | Taille des poudres : 15-45 µm |
Cuivre (Cu) | ASTM B170 | C10100 | Taille des poudres : 10-45 µm |
Hastelloy X | AMS 5754, ASTM B435 | 2.4665 | Taille des poudres : 15-45 µm |
Fournisseurs et détails des prix pour Prototypage rapide au laser Matériaux
Il est essentiel de choisir le bon fournisseur pour vos matériaux LRP afin de garantir la qualité et la rentabilité. Vous trouverez ci-dessous une liste de fournisseurs réputés et un aperçu des tarifs pratiqués.
Fournisseur | Matériau | Fourchette de prix (par kg) | Localisation | Délai d'exécution |
---|---|---|---|---|
Technologie des charpentiers | Acier inoxydable 316L | $100 – $150 | ÉTATS-UNIS | 2-4 semaines |
EOS GmbH | AlSi10Mg | $120 – $170 | Allemagne | 3-5 semaines |
Hoganas AB | Inconel 718 | $250 – $300 | Suède | 4-6 semaines |
Arcam AB | Titane Ti6Al4V | $300 – $400 | Suède | 3-5 semaines |
Sandvik | Chrome cobalt (CoCrMo) | $200 – $250 | Suède | 3-5 semaines |
GKN Additive | Acier maraging (MS1) | $180 – $220 | ROYAUME-UNI | 3-5 semaines |
Technologie LPW | Cuivre (Cu) | $90 – $120 | ROYAUME-UNI | 2-4 semaines |
Kennametal | Hastelloy X | $270 – $320 | ÉTATS-UNIS | 4-6 semaines |
Comparaison des avantages et des inconvénients du prototypage rapide par laser
Aucune technologie n'est exempte de compromis. Pesons le pour et le contre du prototypage rapide au laser pour vous donner une vision équilibrée de ce à quoi vous pouvez vous attendre.
Pour | Cons |
---|---|
Fabrication de précision: Le LRP offre une précision inégalée, ce qui le rend idéal pour les dessins complexes. | Coût initial élevé: L'équipement et le matériel peuvent être coûteux, ce qui n'est pas toujours possible pour les petites entreprises. |
Vitesse: Le processus est beaucoup plus rapide que les méthodes traditionnelles, en particulier pour les pièces complexes. | Limites matérielles: Tous les matériaux ne conviennent pas à la PRL et certains peuvent nécessiter un post-traitement. |
Polyvalence: Peut être utilisé dans plusieurs secteurs et pour une variété d'applications. | Contraintes de taille: La taille des pièces pouvant être créées est limitée par le volume de construction de la machine. |
Réduction des déchets: En tant que processus additif, le LRP minimise les déchets de matériaux, ce qui le rend plus durable. | Finition de la surface: En fonction du matériau et du processus, les pièces peuvent nécessiter une finition supplémentaire. |
Tendances futures du prototypage rapide par laser
À l'avenir, le prototypage rapide par laser est appelé à faire encore plus partie intégrante des processus de fabrication. Les tendances émergentes comprennent le développement de nouveaux matériaux, l'intégration de l'intelligence artificielle pour l'optimisation de la conception et l'amélioration de la vitesse et de l'efficacité des processus. En outre, avec la baisse des coûts, nous pouvons nous attendre à ce que le prototypage rapide au laser devienne accessible aux petites entreprises, ce qui élargira encore son impact.
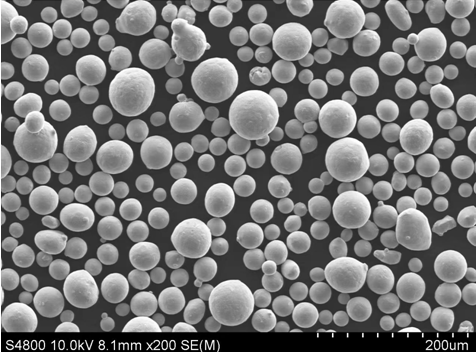
FAQ
Question | Réponse |
---|---|
Qu'est-ce que le prototypage rapide par laser ? | Le prototypage rapide au laser est une technique de fabrication additive qui utilise des lasers pour créer des objets en 3D à partir de dessins numériques en superposant des matériaux. |
Quels sont les secteurs d'activité qui utilisent la PRL ? | Le LRP est utilisé dans diverses industries, notamment l'aérospatiale, l'automobile, la médecine et l'électronique grand public. |
Quels sont les avantages de la PRL par rapport à la fabrication traditionnelle ? | Le LRP offre des délais de production plus courts, une plus grande souplesse de conception et une réduction des déchets de matériaux par rapport aux méthodes de fabrication traditionnelles. |
Quels matériaux peuvent être utilisés dans le cadre de la PRL ? | Une large gamme de matériaux peut être utilisée, y compris l'acier inoxydable, les alliages d'aluminium, le titane, etc. |
La LRP est-elle adaptée à la production de masse ? | Le PRL est généralement plus adapté au prototypage et à la production de faibles volumes, mais les progrès réalisés le rendent de plus en plus viable pour la production de masse. |
Quel est le coût du PRL ? | Bien que le coût initial du LRP soit plus élevé, il peut être plus rentable pour les conceptions complexes ou les petites séries en raison de l'élimination des coûts d'outillage. |
Quelles sont les limites de la PRL ? | Les limites sont notamment les coûts initiaux élevés, les contraintes matérielles et les limites de taille des pièces pouvant être produites. |
Conclusionn
Prototypage rapide au laser est plus qu'un simple mot à la mode ; il s'agit d'une technologie transformatrice qui est en train de remodeler les industries. Que vous cherchiez à créer des pièces très complexes, à réduire les déchets ou simplement à commercialiser un produit plus rapidement, le LRP offre une multitude d'avantages qu'il est difficile d'ignorer. Au fur et à mesure que la technologie évolue, ses applications ne feront que s'étendre, ce qui en fait un outil essentiel pour l'avenir de la fabrication.