Vue d'ensemble du dépôt métallique par laser (LMD)
Dépôt de métal par laser (LMD) est une technologie révolutionnaire de fabrication additive (AM) qui utilise un laser de forte puissance pour fondre et fusionner une poudre ou un fil métallique sur un substrat, couche par couche, afin de créer des structures tridimensionnelles. Que vous travailliez dans l'aérospatiale, l'automobile ou l'industrie médicale, la LMD offre une solution robuste pour les pièces métalliques complexes qui exigent précision, durabilité et efficacité.
Imaginez qu'il faille réparer une pale de turbine usée ou créer un implant sur mesure. Les méthodes de fabrication traditionnelles pourraient être trop lentes, trop coûteuses ou tout simplement pas assez précises. Le LMD intervient comme un super-héros, en utilisant des lasers pour souder des poudres métalliques afin d'obtenir la forme parfaite, couche par couche, de manière méticuleuse. Le résultat ? Des composants extrêmement précis et solides qui peuvent même surpasser les originaux.
Mais comment fonctionne-t-il ? Quels sont les matériaux utilisés ? Et surtout, comment votre entreprise peut-elle en bénéficier ? Dans ce guide détaillé, nous allons nous pencher sur les tenants et les aboutissants du LMD, des poudres métalliques spécifiques qu'il utilise à ses avantages et inconvénients, en passant par une section FAQ pratique pour répondre à toutes les questions qui subsistent.
Alors, attachez votre ceinture, nous allons explorer le monde fascinant du dépôt métallique par laser !
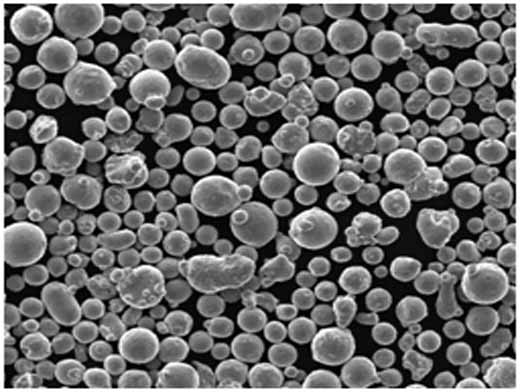
Qu'est-ce que le dépôt de métal par laser (LMD) ?
Le LMD est un type de fabrication additive, également connu sous le nom d'impression 3D, où les matériaux sont ajoutés au lieu d'être retirés. Le processus consiste à utiliser un faisceau laser focalisé pour faire fondre une poudre ou un fil métallique, qui est ensuite déposé sur un substrat. Cette technologie permet un contrôle précis du matériau, ce qui permet de créer des géométries complexes et des composants métalliques de haute performance.
Comment fonctionne le dépôt de métal par laser ?
Le dépôt de métal par laser consiste à envoyer de la poudre de métal à travers une buse dans un faisceau laser, qui fait fondre la poudre et la fusionne avec un matériau de base (substrat). Au fur et à mesure que le laser se déplace, il accumule des couches de métal pour former la forme souhaitée. C'est comme construire un mur, mais à la place des briques, on utilise de minuscules grains de métal, et à la place du mortier, un laser à haute énergie lie le tout.
- Source laser : Le type et la puissance du laser déterminent la manière dont la poudre métallique va fondre et se solidifier. Les lasers à fibre sont couramment utilisés pour leur efficacité et leur précision.
- Système d'alimentation en poudre : Les poudres métalliques sont introduites dans le faisceau laser par une buse. La régularité du flux de poudre est cruciale pour obtenir des couches uniformes.
- Contrôle du mouvement : Le mouvement du laser et du système d'alimentation en poudre est contrôlé avec précision, souvent à l'aide de systèmes CNC ou robotiques, afin de créer la géométrie souhaitée.
Cette précision signifie que la technologie LMD ne se limite pas à la construction de nouvelles pièces. Elle permet également de réparer des pièces existantes en ajoutant de la matière là où c'est nécessaire, ce qui est particulièrement utile pour les composants coûteux dans des industries telles que l'aérospatiale.
Applications de la Dépôt de métal par laser (LMD)
Le dépôt de métal par laser est un procédé polyvalent qui offre un large éventail d'applications dans diverses industries. Qu'il s'agisse de réparer des composants de grande valeur ou de créer des pièces complexes et personnalisées, le LMD fait des vagues dans l'industrie manufacturière.
Applications clés :
L'industrie | application | Avantages |
---|---|---|
Aérospatiale | Réparation d'aubes de turbines, composants de moteurs | Réduction des temps d'arrêt et prolongation de la durée de vie des pièces |
Automobile | Réparation d'engrenages et de vilebrequins, pièces sur mesure | Amélioration des performances, production rentable |
Médical | Implants sur mesure, composants dentaires | Haute précision, biocompatibilité |
Outillage | Réparation des moules, restauration des matrices | Durée de vie plus longue de l'outil, réduction du temps de production |
Pétrole et gaz | Sièges de soupapes, éléments de perçage | Résistance aux environnements difficiles, réduction des coûts de remplacement |
Production d'électricité | Réparation de turbines, fabrication de composants | Amélioration de l'efficacité, réduction des coûts de maintenance |
Défense | Composants d'armement, réparation d'équipements critiques | Haute résistance, durabilité dans des conditions extrêmes |
L'énergie | Composants d'éoliennes, pièces de réacteurs nucléaires | Durabilité, haute performance dans les opérations critiques |
La construction | Composants structurels sur mesure, réparation de machines lourdes | Solidité, flexibilité, rentabilité |
Marine | Réparation d'hélices, composants de moteurs de navires | Résistance à la corrosion, longévité en milieu marin |
Chacune de ces industries a des exigences uniques, et la flexibilité de LMD lui permet de les satisfaire aisément. Qu'il s'agisse des matériaux à haute résistance nécessaires à l'aérospatiale ou des métaux biocompatibles utilisés dans les implants médicaux, LMD peut s'en charger.
Poudres métalliques spécifiques utilisées dans les LMD
Le choix de la poudre métallique est crucial en LMD, car il affecte directement la qualité, la durabilité et la fonctionnalité du produit final. Nous examinons ici quelques-unes des poudres métalliques spécifiques couramment utilisées en LMD, ainsi que leurs compositions et leurs caractéristiques.
Les 10 meilleures poudres métalliques pour le LMD :
Poudre métallique | Composition | Propriétés | Caractéristiques |
---|---|---|---|
Inconel 625 | Alliage nickel-chrome-molybdène-niobium | Haute résistance, excellente résistance à la corrosion | Utilisé dans l'aérospatiale, la marine et les industries chimiques |
Titane Ti-6Al-4V | Alliage de titane, d'aluminium et de vanadium | Rapport résistance/poids élevé, biocompatibilité | Idéal pour les implants médicaux, l'aérospatiale |
Acier inoxydable 316L | Alliage fer-chrome-nickel-molybdène | Résistance à la corrosion, bonnes propriétés mécaniques | Courant dans les industries médicales et alimentaires |
Cobalt-Chrome (Co-Cr) | Alliage cobalt-chrome | Résistance à l'usure, biocompatibilité | Utilisé dans les implants dentaires et orthopédiques |
Aluminium AlSi10Mg | Alliage aluminium-silicium-magnésium | Léger, bonnes propriétés thermiques | Populaire dans les applications automobiles et aérospatiales |
Hastelloy X | Alliage nickel-chrome-fer-molybdène | Résistance à la chaleur, résistance à l'oxydation | Convient aux environnements à haute température |
Acier maraging 18Ni300 | Alliage nickel-cobalt-molybdène-titane | Très haute résistance, bonne ténacité | Utilisé dans l'outillage, l'aérospatiale |
Nickel 718 | Alliage nickel-chrome-fer | Haute résistance à la traction, résistance au fluage | Largement utilisé dans les moteurs à turbine, l'aérospatiale |
Acier à outils H13 | Alliage chrome-molybdène-vanadium | Dureté élevée, résistance à l'usure | Idéal pour l'outillage, les moules de coulée sous pression |
Cuivre-CrZr | Alliage cuivre-chrome-zirconium | Excellente conductivité thermique, résistance | Utilisé dans les échangeurs de chaleur, les composants électriques |
Ces poudres métalliques sont soigneusement sélectionnées en fonction des exigences spécifiques de l'application, y compris des facteurs tels que la solidité, la résistance à la corrosion et la biocompatibilité.
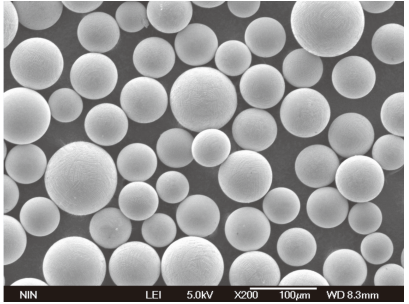
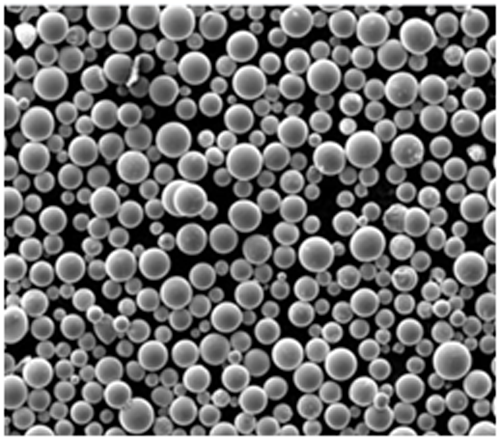
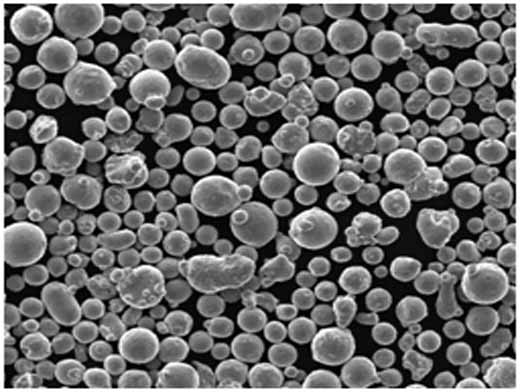
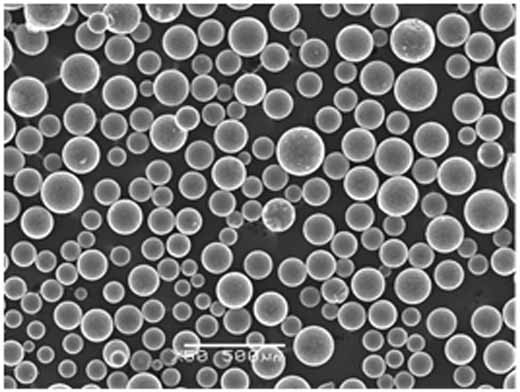
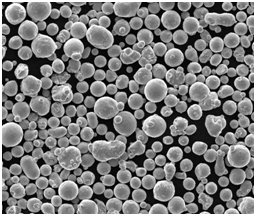
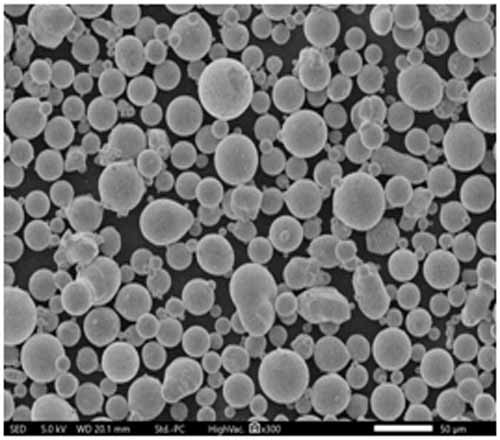
Propriétés et caractéristiques des Dépôt de métal par laser (LMD)
Il est essentiel de comprendre les propriétés et les caractéristiques de la technologie LMD pour apprécier pleinement ses capacités et ses limites potentielles. Décortiquons ces aspects afin d'obtenir une image plus claire de ce qui fait le succès de la LMD.
Propriétés du matériau :
Propriété | Description |
---|---|
Densité | Les composants LMD ont généralement une densité élevée, comparable à celle des pièces forgées. |
Microstructure | Il est possible d'obtenir des microstructures fines, ce qui se traduit par une résistance et une ténacité élevées. |
Finition de la surface | L'état de surface peut varier en fonction de la poudre et des paramètres du processus, ce qui nécessite souvent un post-traitement. |
Porosité | Une porosité minimale peut être obtenue avec des paramètres optimisés, bien que cela puisse varier en fonction du matériau et de l'application. |
Contraintes résiduelles | Le LMD peut introduire des contraintes résiduelles qu'il peut être nécessaire de soulager par un traitement thermique. |
Caractéristiques du processus :
Caractéristique | Détails |
---|---|
Épaisseur de la couche | Elle est généralement comprise entre 50 et 500 microns, en fonction de l'application. |
Taux de dépôt | Gamme de 0,5 à 3 kg/heure, influencée par le matériau et la puissance du laser. |
Précision | Haute précision avec des tolérances de l'ordre de ±0,1 mm ou mieux. |
Flexibilité | Capable de gérer des géométries complexes et des matériaux multiples en une seule fois. |
Évolutivité | Il convient pour les petites et les grandes pièces, des prototypes à la production. |
La combinaison de ces propriétés et caractéristiques fait du LMD un outil puissant pour la fabrication et la réparation de composants métalliques de haute performance.
Avantages et limites du dépôt métallique par laser (LMD)
Comme tout processus de fabrication, le LMD a ses forces et ses faiblesses. Voici une analyse des avantages et des limites de ce procédé pour vous aider à déterminer s'il est adapté à vos besoins.
Avantages :
Avantage | Explication |
---|---|
Précision et exactitude | La technologie LMD permet de produire des composants très détaillés avec des tolérances serrées. |
Efficacité des matériaux | La production de déchets est minime, ce qui en fait une option rentable. |
Polyvalence | Capable de traiter une large gamme de matériaux, y compris des métaux difficiles à usiner. |
Capacités de réparation | Le LMD excelle dans la réparation de composants de grande valeur, prolongeant leur durée de vie et réduisant les temps d'arrêt. |
Personnalisation | Facilement personnalisable pour les petites séries ou les pièces sur mesure. |
Limites :
Limitation | Explication |
---|---|
Coûts initiaux élevés | Les coûts d'équipement et d'installation peuvent être importants, ce qui en fait un investissement considérable. |
Finition de la surface | Nécessite souvent un post-traitement pour obtenir une surface lisse. |
Complexité de l'opération | Nécessite des opérateurs qualifiés et un contrôle précis des paramètres. |
Zones affectées par la chaleur | Le laser peut introduire des zones affectées par la chaleur qui peuvent modifier les propriétés du matériau. |
Limites matérielles | Tous les matériaux ne conviennent pas au LMD, en particulier ceux dont l'absorptivité laser est faible. |
Comprendre ces avantages et ces inconvénients vous aidera à prendre une décision éclairée lorsque vous envisagerez d'utiliser la technologie LMD pour vos besoins de fabrication.
Paramètres de processus influençant le dépôt de métal par laser (LMD)
La qualité des composants produits par dépôt métallique au laser dépend fortement de plusieurs paramètres du processus. Ces paramètres doivent être soigneusement contrôlés pour garantir les propriétés mécaniques, l'état de surface et les performances globales du produit final.
Paramètres clés du processus :
Paramètres | Description | Influence sur le produit final |
---|---|---|
Puissance du laser | La quantité d'énergie fournie par le laser, généralement mesurée en watts. | Une puissance plus élevée augmente la vitesse de dépôt mais peut provoquer une surchauffe. |
Vitesse de balayage | La vitesse à laquelle le laser se déplace sur le substrat. | Des vitesses plus élevées peuvent réduire l'apport de chaleur mais peuvent conduire à une fusion incomplète. |
Taux d'alimentation en poudre | La vitesse à laquelle la poudre de métal est envoyée dans le bain de fusion. | Des taux plus élevés augmentent l'efficacité du dépôt mais peuvent entraîner une porosité s'ils ne sont pas contrôlés. |
Débit de gaz de protection | Débit de gaz inerte utilisé pour protéger le bain de fusion de l'oxydation. | Un blindage adéquat empêche l'oxydation et la contamination. |
Taille du spot laser | Diamètre du faisceau laser sur le substrat. | Une taille de spot plus petite améliore la précision mais peut ralentir le processus. |
Taux de chevauchement | Le degré de chevauchement entre les passes laser adjacentes. | Un chevauchement plus important garantit l'uniformité mais peut augmenter le temps de traitement. |
Préchauffage du substrat | La température du substrat avant le début du dépôt. | Le préchauffage réduit les contraintes résiduelles et les fissures. |
Chacun de ces paramètres joue un rôle essentiel dans la détermination de la qualité et de la cohérence du processus LMD. Par exemple, une puissance laser ou une vitesse de balayage inadéquates peuvent entraîner des défauts tels que la porosité, la fissuration ou une mauvaise adhérence entre les couches.
Optimisation des paramètres LMD pour de meilleurs résultats
Pour obtenir les meilleurs résultats avec le LMD, il est essentiel d'optimiser ces paramètres pour chaque application et matériau spécifique. Cela implique souvent une combinaison d'expérimentation et de simulation pour trouver le point idéal où le processus est à la fois efficace et produit des pièces de haute qualité.
Par exemple, lorsqu'on travaille avec un alliage à haute résistance comme l'Inconel 625, le contrôle de la puissance du laser et de la vitesse de balayage est essentiel pour éviter la surchauffe, qui peut entraîner des modifications indésirables de la microstructure. À l'inverse, lorsqu'on utilise un matériau plus tolérant comme l'acier inoxydable 316L, il faut plutôt se concentrer sur l'optimisation du taux d'alimentation en poudre et du débit du gaz de protection pour maximiser l'efficacité du dépôt.
Matériaux avancés utilisés pour le dépôt métallique par laser
Outre les poudres métalliques courantes énumérées ci-dessus, le LMD peut également travailler avec des matériaux plus spécialisés. Ces matériaux avancés sont utilisés dans des applications où les métaux standard risquent de ne pas répondre aux critères de performance nécessaires, tels que les températures extrêmes, les environnements corrosifs ou les exigences mécaniques spécifiques.
Poudres métalliques avancées supplémentaires pour le LMD :
Poudre métallique | Composition | Propriétés | Caractéristiques |
---|---|---|---|
Alliage de nickel 263 | Alliage nickel-chrome-cobalt-molybdène | Résistance aux températures élevées, résistance à l'oxydation | Idéal pour les aubes de turbines, les chemises de combustion |
Haynes 282 | Alliage nickel-fer-chrome-molybdène-titane | Haute résistance au fluage, excellente soudabilité | Utilisé dans l'aérospatiale, la production d'énergie |
Tantale (Ta) | Tantale pur | Excellente résistance à la corrosion, biocompatibilité | Convient au traitement chimique, aux dispositifs médicaux |
Niobium (Nb) | Niobium pur | Point de fusion élevé, bonnes propriétés supraconductrices | Utilisé dans les supraconducteurs, les composants aérospatiaux |
Tungstène (W) | Pure tungstène | Point de fusion extrêmement élevé, haute densité | Idéal pour les applications à haute température |
Inconel 738 | Alliage nickel-chrome-cobalt-aluminium | Résistance exceptionnelle à l'oxydation, haute résistance | Utilisé dans les composants de turbines à gaz à section chaude |
René 41 | Alliage nickel-chrome-cobalt-aluminium | Résistance supérieure à haute température, résistance à l'oxydation | Courant dans l'aérospatiale, les turbines à gaz |
Ti-5553 | Alliage titane-aluminium-molybdène-vanadium-chrome | Haute résistance, ténacité, bonne résistance à la corrosion | Utilisé dans les applications aérospatiales et militaires |
Alliage de cobalt Stellite 6 | Alliage cobalt-chrome-tungstène-carbone | Excellente résistance à l'usure, bonne résistance à la corrosion | Idéal pour les sièges de soupapes, les outils de coupe |
Ni-Cr-B-Si (Colmonoy 88) | Alliage nickel-chrome-bore-silicium | Dureté, résistance à l'usure, bonne résistance à la corrosion | Utilisé pour les revêtements de surface et les applications de réparation |
Ces matériaux avancés sont choisis pour leurs propriétés uniques qui les rendent adaptés à des applications très exigeantes. Par exemple, l'excellente résistance à la corrosion du tantale en fait un matériau idéal pour les équipements de traitement chimique, tandis que le point de fusion extrême du tungstène en fait un choix de premier ordre pour les composants exposés à des températures très élevées.
Comparaison des matériaux avancés
La comparaison de ces matériaux avancés révèle comment des alliages spécifiques peuvent être plus performants que d'autres dans certaines conditions, ce qui les rend plus adaptés à des applications particulières.
Matériau | La force | Résistance à la température | Résistance à la corrosion | Résistance à l'usure | Adéquation de l'application |
---|---|---|---|---|---|
Alliage de nickel 263 | Haut | Excellent | Modéré | Bon | Turbines, composants à haute température |
Tantale | Modéré | Haut | Excellent | Modéré | Traitement chimique, dispositifs médicaux |
Tungstène | Extrêmement élevé | Remarquable | Modéré | Excellent | Applications à haute température, aérospatiale |
Alliage de cobalt Stellite 6 | Modéré | Bon | Bon | Excellent | Outils de coupe, sièges de soupape |
Inconel 738 | Très élevé | Excellent | Bon | Modéré | Composants de turbines à gaz, aérospatiale |
Ces comparaisons peuvent aider les fabricants à choisir le bon matériau en fonction de leurs besoins spécifiques, en tenant compte de facteurs tels que la solidité, la résistance à la température et le coût.
Applications des matériaux avancés en LMD
L'utilisation de matériaux avancés dans la technologie LMD permet d'étendre son application à des domaines hautement spécialisés où les méthodes de fabrication ou les matériaux traditionnels échoueraient. Ces matériaux peuvent répondre à des exigences strictes et offrir des performances, une longévité et une fiabilité accrues dans des applications critiques.
Applications spécialisées :
L'industrie | application | Matériau utilisé | Avantages |
---|---|---|---|
Aérospatiale | Chemises de chambre de combustion, aubes de turbine | Alliage de nickel 263, Haynes 282 | Résistance aux hautes températures, excellentes propriétés mécaniques |
Médical | Implants sur mesure, outils chirurgicaux | Tantale, cobalt-chrome (Co-Cr) | Biocompatibilité, résistance à la corrosion |
L'énergie | Composants de réacteurs nucléaires, arbres d'éoliennes | Tungstène, René 41 | Résistance aux radiations, résistance aux contraintes |
Défense | Véhicules blindés, matériel militaire | Ti-5553, Tungstène | Haute résistance, ténacité, réduction du poids |
Automobile | Composants de moteurs à haute performance, échangeurs de chaleur | Inconel 738, Titane Ti-6Al-4V | Résistance à la chaleur, solidité, poids réduit |
Pétrole et gaz | Outils de fond de puits, sièges de vannes | Alliage de cobalt Stellite 6, Ni-Cr-B-Si | Résistance à l'usure, durabilité dans les environnements difficiles |
Électronique | Composants semi-conducteurs, dissipateurs de chaleur | Niobium, Tungstène | Conductivité thermique, résistance aux hautes températures |
Chaque application bénéficie des propriétés spécifiques des matériaux avancés utilisés. Par exemple, dans l'industrie aérospatiale, la résistance aux températures élevées de l'alliage de nickel 263 permet aux pales de turbine de conserver leur intégrité même dans des conditions de fonctionnement extrêmes.
Normes et spécifications pour les matériaux LMD
Lors de la sélection des matériaux pour les Dépôt de métal par laserLe respect des normes et spécifications industrielles est essentiel pour garantir la qualité, la performance et la sécurité. Les différentes industries ont des exigences spécifiques auxquelles les matériaux doivent répondre, et ces normes guident le processus de sélection.
Normes industrielles pour les matériaux LMD :
Matériau | Norme/spécification | L'industrie | Exigences clés |
---|---|---|---|
Inconel 625 | ASTM B443, AMS 5599 | Aérospatiale, Pétrole et gaz | Haute température, résistance à la corrosion, propriétés mécaniques |
Titane Ti-6Al-4V | ASTM F136, AMS 4911 | Médical, aérospatial | Biocompatibilité, résistance mécanique, résistance à la fatigue |
Acier inoxydable 316L | ASTM A240, ISO 5832-1 | Médical, Agroalimentaire | Résistance à la corrosion, propriétés mécaniques |
Cobalt-Chrome (Co-Cr) | ASTM F75, ISO 5832-4 | Médical | Résistance à l'usure, biocompatibilité |
Tungstène (W) | ASTM B777, MIL-T-21014 | Défense, aérospatiale | Haute densité, résistance aux températures élevées |
Aluminium AlSi10Mg | ASTM B209, EN 485 | Automobile, aérospatiale | Léger, bonne conductivité thermique |
Alliage de nickel 263 | AMS 5872, ASTM B637 | Aérospatiale | Résistance à l'oxydation, haute résistance à des températures élevées |
René 41 | AMS 5545, ASTM B435 | Aérospatiale | Propriétés mécaniques à haute température |
Niobium (Nb) | ASTM B392, AMS 7850 | Électronique, aérospatiale | Supraconductivité, stabilité thermique |
Tantale (Ta) | ASTM B708, AMS 7831 | Médical, Traitement chimique | Résistance à la corrosion, biocompatibilité |
Ces normes garantissent que les matériaux utilisés dans les LMD sont de qualité constante et répondent aux critères de performance nécessaires pour les applications prévues. Par exemple, la norme ASTM F136 garantit que le titane Ti-6Al-4V utilisé dans les implants médicaux est sûr et efficace pour une utilisation à long terme dans le corps humain.
Choisir la bonne poudre métallique pour le dépôt métallique par laser
La sélection de la bonne poudre métallique est une étape critique du processus LMD. Le choix de la poudre affecte directement la qualité, la performance et le coût du produit final. Des facteurs tels que les propriétés du matériau, les exigences de l'application et les considérations de coût jouent tous un rôle dans ce processus de prise de décision.
Facteurs à prendre en compte :
Facteur | Description | Impact sur la sélection |
---|---|---|
Exigences en matière de candidature | Les besoins spécifiques du produit final, y compris les propriétés mécaniques, les conditions environnementales et la durée de vie. | Dicte la sélection des matériaux sur la base de critères de performance. |
Propriétés des matériaux | Propriétés telles que le point de fusion, la conductivité thermique et la résistance. | Détermine les paramètres du processus et la qualité de la pièce finale. |
Morphologie des poudres | La forme et la distribution des particules de poudre. | Affecte la fluidité, la densité de tassement et l'uniformité de la couche. |
Considérations relatives aux coûts | Le coût de la poudre métallique par rapport au budget du projet. | Équilibre entre la performance des matériaux et la faisabilité économique. |
Disponibilité des fournisseurs | La disponibilité de la poudre métallique auprès de fournisseurs fiables. | Assurer la cohérence de l'approvisionnement et de la qualité de la production. |
Respect des normes | Respect des normes et des spécifications de l'industrie. | Assurer la qualité et la sécurité du produit final. |
Pour prendre une décision éclairée concernant la poudre métallique, il faut trouver un équilibre entre les exigences techniques et le coût. Par exemple, si le tungstène offre une résistance supérieure à la température, il est aussi plus cher que d'autres options comme l'acier inoxydable 316L, ce qui le rend plus adapté aux applications haut de gamme où la performance justifie le coût.
Fournisseurs et prix des poudres métalliques LMD
Il est essentiel de s'approvisionner en poudre métallique auprès d'un fournisseur fiable pour assurer la réussite du LMD. Les fournisseurs proposent une large gamme de poudres dont les prix varient en fonction de facteurs tels que la composition du matériau, la pureté et la distribution de la taille des particules.
Principaux fournisseurs et prix :
Fournisseur | Poudre métallique | Fourchette de prix (par kg) | Caractéristiques spéciales |
---|---|---|---|
Technologie des charpentiers | Alliage de nickel 263, Haynes 282 | $300 – $500 | Poudres de haute qualité aérospatiale, taille des particules constante. |
Hoganas AB | Acier inoxydable 316L, Inconel 625 | $50 – $200 | Large gamme d'alliages, excellente fluidité. |
Technologie LPW | Titane Ti-6Al-4V, aluminium AlSi10Mg | $250 – $450 | Poudres personnalisées, contrôle de qualité strict pour la fabrication additive. |
Oerlikon Metco | Alliage de cobalt Stellite 6, Rene 41 | $400 – $600 | Poudres haute performance, optimisées pour la résistance à l'usure. |
AP&C (GE Additive) | Ti-5553, Tantale | $500 – $800 | Poudres de qualité aérospatiale et médicale, biocompatibilité. |
Sandvik | Inconel 738, Tungstène | $200 – $700 | Alliages à haute température, essais approfondis et certification. |
Technologie des poudres Praxis | Niobium, cobalt-chrome (Co-Cr) | $300 – $600 | Poudres spécialisées pour les applications médicales et électroniques. |
GKN Additive | Alliage de nickel 263, Haynes 282 | $300 – $500 | Mélanges de poudres personnalisés, excellente résistance à l'oxydation. |
Tekna | Aluminium AlSi10Mg, Acier inoxydable 316L | $50 – $150 | Poudres sphériques, optimisées pour la fabrication additive. |
VIGA | Tantale, tungstène | $500 – $900 | Poudres de haute pureté, adaptées à des applications spécifiques. |
Les prix varient considérablement en fonction du matériau et du fournisseur, reflétant les différences de pureté, de méthode de production et de demande du marché. Par exemple, les poudres de tantale et de tungstène se situent à l'extrémité supérieure du spectre des prix en raison de leur traitement complexe et de leur forte demande dans les industries spécialisées.
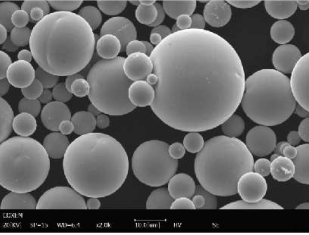
Comparaison Dépôt de métal par laser à d'autres techniques de fabrication additive
Le dépôt de métal au laser n'est que l'une des nombreuses techniques de fabrication additive disponibles aujourd'hui. Comprendre comment le LMD se compare aux autres méthodes peut vous aider à choisir le meilleur processus pour vos besoins spécifiques.
Comparaison avec d'autres techniques de fabrication additive :
Technique | Flexibilité des matériaux | Finition de la surface | Vitesse | Précision | Coût | Applications |
---|---|---|---|---|---|---|
Dépôt de métal par laser | Haut | Modéré | Moyen | Haut | Haut | Aérospatiale, réparation, géométries complexes |
Frittage sélectif par laser (SLS) | Haut | Modéré | Moyen | Haut | Modéré | Prototypage, production en petites séries |
Fusion par faisceau d'électrons (EBM) | Moyen | Modéré | Moyen | Haut | Haut | Aérospatiale, implants médicaux |
Modélisation par dépôt en fusion (FDM) | Faible | Faible | Haut | Faible | Faible | Prototypage, produits de consommation |
Frittage direct de métaux par laser (DMLS) | Haut | Haut | Moyen | Très élevé | Haut | Médical, aérospatial, pièces complexes |
Jetting de liant | Moyen | Faible | Haut | Moyen | Modéré | Grandes pièces, moules de coulée |
Dépôt d'énergie dirigée (DED) | Haut | Modéré | Moyen | Haut | Haut | Réparation, grands composants, aérospatiale |
Le LMD se distingue par sa capacité à travailler avec une large gamme de matériaux et par sa précision dans la création de géométries complexes. Cependant, elle tend à être plus coûteuse et plus lente que d'autres techniques comme la FDM, qui convient mieux au prototypage rapide avec des exigences moins élevées en matière de matériaux.