Introduction aux solutions de jet de liant métallique
Le monde de la fabrication a connu des changements sismiques avec l'avènement de la fabrication additive, plus connue sous le nom d'impression 3D. Dans ce domaine, la projection de liant métallique se distingue comme l'une des technologies les plus prometteuses et les plus polyvalentes. Mais qu'est-ce qu'un solution de jet de liant métalliqueet pourquoi fait-il des vagues dans des secteurs allant de l'aérospatiale à la bijouterie ?
Le jet de liant métallique est un type de fabrication additive dans lequel un liant est déposé sélectivement sur un lit de poudre métallique, couche par couche, pour former une pièce solide. Contrairement à d'autres méthodes d'impression 3D, il n'est pas nécessaire de recourir à des températures élevées ou à des faisceaux laser pour fusionner le matériau. Elle s'appuie plutôt sur le liant et le frittage qui s'ensuit pour créer des pièces métalliques robustes. Ce processus ouvre un monde de possibilités en termes de rapidité, de rentabilité et de flexibilité des matériaux.
Dans ce guide complet, nous explorerons les nuances des solutions de jet de liant métallique, depuis les types de poudres métalliques disponibles jusqu'aux subtilités de leur composition, de leurs caractéristiques et de leurs applications. Nous nous pencherons également sur des modèles spécifiques de poudres métalliques, leurs spécifications, leurs fournisseurs et une comparaison approfondie de leurs avantages et de leurs limites. À la fin de cet article, vous comprendrez parfaitement pourquoi les solutions de jet de liant métallique sont en train de changer la donne dans la fabrication moderne.
Vue d'ensemble des solutions de jet de liant métallique
En termes simples, le jet de liant métallique est une forme d'impression 3D qui utilise de la poudre de métal et un agent liant pour créer des pièces métalliques complexes. Le processus consiste à étaler une fine couche de poudre métallique sur une plateforme de construction, après quoi une tête d'impression dépose sélectivement un liant qui colle les particules de poudre entre elles. Ce processus est répété couche par couche jusqu'à ce que la pièce soit entièrement formée. Après l'impression, la pièce subit un processus de durcissement du liant, suivi d'un frittage pour fusionner les particules de métal, produisant ainsi un composant métallique entièrement dense.
Cette technologie présente plusieurs avantages clés par rapport aux méthodes de fabrication traditionnelles, notamment la possibilité de produire des géométries complexes qu'il serait impossible ou extrêmement coûteux de créer à l'aide de techniques conventionnelles. En outre, la projection de liants métalliques est plus rapide et plus rentable pour la production de petites et moyennes séries de pièces.
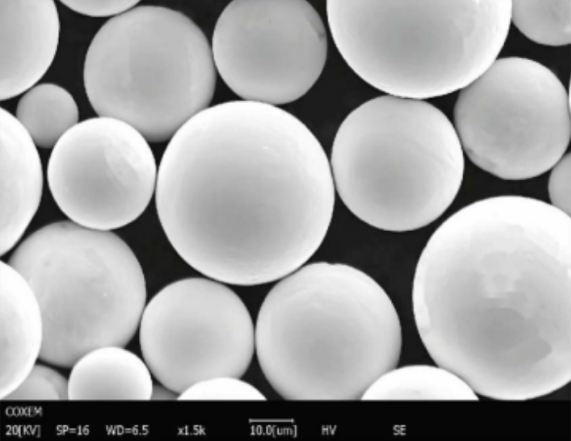
Composition des solutions de jet de liant métallique
La composition d'un solution de jet de liant métallique est cruciale pour déterminer la qualité, la résistance et la durabilité du produit final. Différents types de poudres métalliques sont utilisés, chacun ayant des propriétés spécifiques qui le rendent adapté à diverses applications. Voici une présentation détaillée des poudres métalliques couramment utilisées dans la projection de liant, de leur composition et de leurs caractéristiques.
Poudre métallique | Composition | Caractéristiques | Applications |
---|---|---|---|
Acier inoxydable 316L | Fer, chrome, nickel, molybdène | Résistant à la corrosion, bonne résistance, ductilité | Aérospatiale, dispositifs médicaux, composants automobiles |
Inconel 625 | Nickel, chrome, molybdène, niobium | Résistance aux hautes températures, résistance à la corrosion | Aérospatiale, traitement chimique, industries marines |
Cuivre | Cuivre | Excellente conductivité électrique et thermique | Composants électriques, échangeurs de chaleur, articles de décoration |
Titane Ti6Al4V | Titane, aluminium, vanadium | Rapport résistance/poids élevé, résistant à la corrosion | Aérospatiale, implants médicaux, pièces de course automobile |
Acier à outils M2 | Fer, tungstène, molybdène, chrome, vanadium | Dureté élevée, résistance à l'usure, ténacité | Outils de coupe, moules, matrices |
Cobalt-Chrome | Cobalt, chrome, molybdène | Biocompatibilité, résistance à la corrosion, résistance à l'usure | Implants médicaux, appareils dentaires, pales de turbines |
Alliage de nickel 718 | Nickel, chrome, fer, molybdène | Haute résistance, résistance à l'oxydation, soudabilité | Moteurs à réaction, turbines de production d'énergie, réacteurs nucléaires |
Aluminium AlSi10Mg | Aluminium, Silicium, Magnésium | Légèreté, bonne résistance, usinabilité | Pièces automobiles, composants aérospatiaux, électronique grand public |
Bronze | Cuivre, étain | Bonne résistance à l'usure, usinabilité, esthétique | Paliers, coussinets, sculptures, instruments de musique |
Le fer | Le fer | Haute résistance, propriétés magnétiques, rentabilité | Composants structurels, pièces automobiles, dispositifs magnétiques |
Chacune de ces poudres apporte quelque chose d'unique, qu'il s'agisse de la résistance à la corrosion de l'acier inoxydable ou de la légèreté de l'aluminium. Le choix de la poudre métallique dépend largement des exigences spécifiques de l'application, telles que la nécessité d'une résistance élevée, d'une stabilité thermique ou d'une biocompatibilité.
Caractéristiques des solutions de jet de liant métallique
Il est essentiel de comprendre les caractéristiques de la projection de liants métalliques pour en exploiter tout le potentiel. Le processus comprend plusieurs étapes, chacune d'entre elles pouvant être affinée pour produire des pièces aux propriétés spécifiques. Décortiquons ces caractéristiques.
Épaisseur de la couche
Dans la projection de liant métallique, l'épaisseur de la couche joue un rôle crucial dans la détermination de l'état de surface et de la précision de la pièce finale. En règle générale, l'épaisseur de la couche varie de 50 à 200 microns. Des couches plus fines permettent d'obtenir des surfaces plus lisses et des détails plus précis, mais peuvent augmenter le temps d'impression.
Vitesse d'impression
Le jet de liant métallique est connu pour sa vitesse d'impression élevée par rapport à d'autres techniques de fabrication additive. En effet, elle n'implique pas la fusion de la poudre métallique au cours du processus d'impression, ce qui permet un dépôt plus rapide des couches.
Finition de la surface
L'état de surface des pièces produites par projection de liant métallique est généralement bon, mais peut nécessiter un post-traitement, tel que le polissage ou l'usinage, pour obtenir une finition miroir. Le type de liant et de poudre, ainsi que l'épaisseur de la couche, influencent la qualité de la surface.
Propriétés des matériaux
Les propriétés des matériaux des pièces produites par jet de liant sont comparables à celles des pièces fabriquées traditionnellement, en particulier après le frittage. Les propriétés telles que la résistance à la traction, la dureté et la conductivité thermique sont largement déterminées par la poudre métallique utilisée et le processus de frittage.
Géométries complexes
L'une des principales caractéristiques de la projection de liant métallique est sa capacité à produire des géométries très complexes qu'il serait impossible ou trop coûteux de réaliser à l'aide de méthodes de fabrication conventionnelles. Il s'agit notamment de canaux internes complexes, de structures en treillis et de porte-à-faux sans qu'il soit nécessaire de recourir à des structures de soutien.
Rentabilité
Le jet de liant métallique est plus rentable pour les petites et moyennes séries que les méthodes traditionnelles telles que l'usinage CNC ou le moulage. L'absence d'outillage et la possibilité de produire plusieurs pièces en un seul travail d'impression réduisent encore les coûts.
Caractéristique | Détails |
---|---|
Épaisseur de la couche | 50-200 microns |
Vitesse d'impression | Élevé, pas de fonte nécessaire |
Finition de la surface | Bon, peut nécessiter un post-traitement |
Propriétés des matériaux | Comparable à la fabrication traditionnelle, elle dépend de la poudre et du frittage. |
Géométries complexes | Excellente capacité, aucune structure de soutien n'est nécessaire |
Rentabilité | Élevée, en particulier pour les petites et moyennes séries |
Avantages des solutions de jet de liant métallique
La projection de liant métallique présente plusieurs avantages, ce qui en fait une option intéressante pour de nombreuses industries. Examinons ces avantages plus en détail.
Vitesse et efficacité
L'un des principaux avantages du jet de liant métallique est sa rapidité. Contrairement aux autres méthodes d'impression 3D de métaux qui nécessitent la fusion et la solidification de chaque couche, la technique du binder jetting permet d'imprimer des couches entières en une seule fois. Cela réduit considérablement les temps d'impression, ce qui permet une rotation plus rapide des pièces.
Flexibilité des matériaux
La projection de liant métallique est compatible avec une large gamme de poudres métalliques, ce qui permet aux fabricants de choisir le matériau le mieux adapté à leurs besoins spécifiques. Qu'il s'agisse d'acier inoxydable pour la résistance à la corrosion ou de cuivre pour la conductivité électrique, il existe une poudre métallique adaptée.
Une production rentable
Pour les petites et moyennes séries, le jet de liant métallique est plus rentable que les méthodes de fabrication traditionnelles. La possibilité d'imprimer plusieurs pièces en un seul lot sans avoir recours à un outillage ou à des moules coûteux réduit encore les coûts.
Détail et précision élevés
La projection de liant métallique permet de produire des pièces aux détails complexes et d'une grande précision. Ceci est particulièrement utile pour les applications où la précision est critique, comme dans les composants aérospatiaux ou les appareils médicaux.
Respect de l'environnement
Par rapport aux méthodes de fabrication soustractives, la projection de liant métallique produit moins de déchets. Comme il s'agit d'un processus additif, le matériau n'est utilisé que là où il est nécessaire, ce qui réduit la consommation globale de ressources.
Avantage | Explication |
---|---|
Vitesse et efficacité | Imprime des couches entières en une seule fois, réduisant ainsi le temps d'impression |
Flexibilité des matériaux | Compatible avec diverses poudres métalliques |
Une production rentable | Pas besoin d'outils ou de moules coûteux |
Détail et précision élevés | Production de pièces complexes avec une grande précision |
Respect de l'environnement | Moins de déchets produits par rapport aux méthodes soustractives |
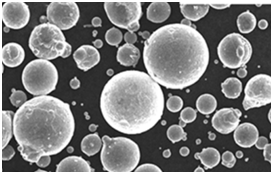
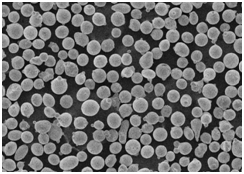
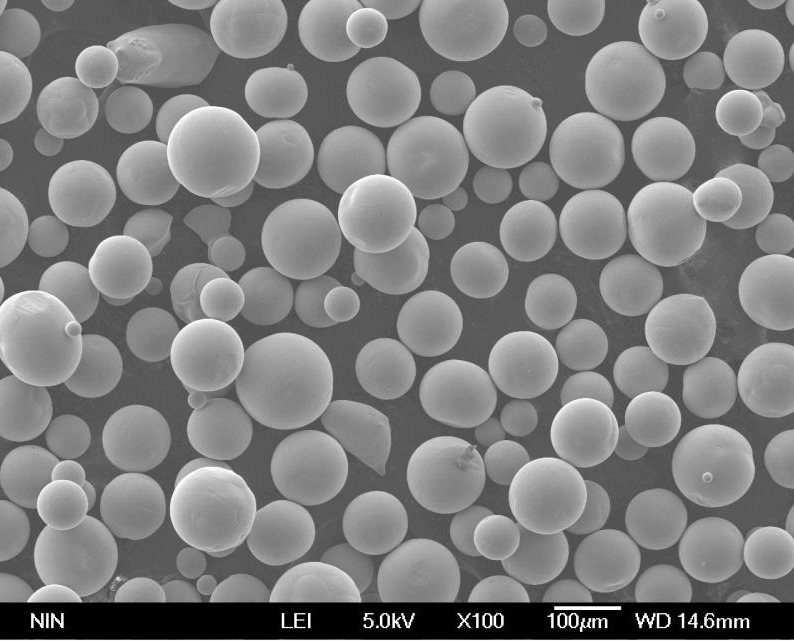
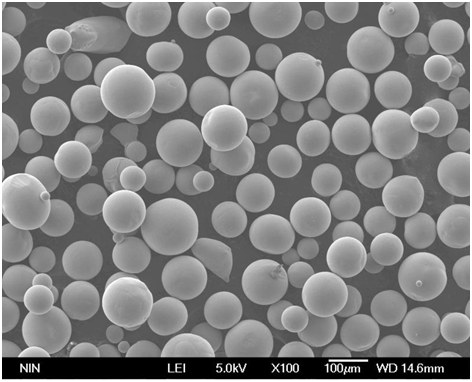

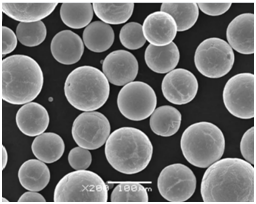
Applications des solutions de jet de liant métallique
La polyvalence de la projection de liants métalliques lui permet de s'adapter à un large éventail d'applications dans diverses industries. Voici un aperçu de quelques-uns des secteurs clés où cette technologie a un impact significatif.
L'industrie | application | Avantages |
---|---|---|
Aérospatiale | Composants structurels légers, pièces de moteur complexes | Rapport résistance/poids élevé, géométries complexes |
Automobile | Prototypes, pièces sur mesure, petites séries | Rentabilité, rapidité d'exécution, polyvalence des matériaux |
Médical | Implants, instruments chirurgicaux, prothèses sur mesure | Biocompatibilité, haute précision, solutions spécifiques au patient |
Bijoux | Modèles complexes, pièces sur mesure, petites séries | Haute précision, rentabilité, options de matériaux comme l'or et l'argent |
L'énergie | Aubes de turbines, tuyères de carburant, échangeurs de chaleur | Résistance aux hautes températures, géométries complexes |
Industrie | Outillage, moules, gabarits, montages | Durabilité, résistance à l'usure, économies |
Les applications de solutions de jet de liant métallique sont vastes, allant de la création de composants légers pour les avions à la production de bijoux personnalisés aux motifs complexes. La capacité de créer des pièces complexes avec une grande précision rend cette technologie indispensable à la fabrication moderne.
Spécifications et normes pour les solutions de jet de liant métallique
Lors de la sélection d'une solution de jet de liant métallique, il est essentiel de comprendre les spécifications et les normes qui régissent la qualité et les performances des matériaux et des processus. Vous trouverez ci-dessous un tableau décrivant certaines des principales spécifications, tailles, qualités et normes associées à la projection de liant métallique.
Spécification/Norme | Détails |
---|---|
ASTM F2924 | Spécification standard pour la fabrication additive Titane-6 Aluminium-4 Vanadium avec fusion en lit de poudre |
ASTM F3055 | Spécification standard pour la fabrication additive d'alliages de nickel par fusion sur lit de poudre |
ISO/ASTM 52900 | Terminologie standard pour la fabrication additive |
Épaisseur de la couche | 50-200 microns, en fonction du matériau et de l'application |
Densité de la pièce | Généralement 95-99% de matériaux corroyés après frittage |
Rugosité de surface | Typiquement 5-15 µm, en fonction du post-traitement |
Précision dimensionnelle | ±0,1-0,3 mm, en fonction de la taille et de la géométrie de la pièce |
Taille des particules de poudre | Typiquement 15-45 µm, affecte la fluidité et la densité de tassement. |
Ces spécifications et normes garantissent que le processus de projection de liant métallique produit des pièces qui répondent aux exigences de qualité et de performance nécessaires. Il est important de choisir une solution conforme à ces normes pour garantir la fiabilité et la durabilité du produit final.
Comparaison des solutions de jet de liant métallique
Lorsque vous envisagez de recourir à la projection de liants métalliques pour vos besoins de fabrication, il est essentiel de comparer les différentes solutions disponibles. Vous trouverez ci-dessous une analyse comparative des différentes poudres métalliques et de leur adéquation aux différentes applications.
Poudre métallique | Avantages | Limites | Mieux adapté pour |
---|---|---|---|
Acier inoxydable 316L | Résistance à la corrosion, bonnes propriétés mécaniques | Plus cher que certaines alternatives | Aérospatiale, appareils médicaux, environnements marins |
Inconel 625 | Résistance aux hautes températures, excellente résistance à la corrosion | Coût élevé, difficile à usiner | Moteurs à réaction, traitement chimique, réacteurs nucléaires |
Cuivre | Excellente conductivité électrique et thermique, malléabilité | Résistance moindre par rapport aux aciers, tendance à l'oxydation | Composants électriques, échangeurs de chaleur, plomberie |
Titane Ti6Al4V | Rapport résistance/poids élevé, biocompatibilité | Coûteux, nécessite une manipulation soigneuse | Implants médicaux, composants aérospatiaux, pièces de course automobile |
Acier à outils M2 | Dureté élevée et résistance à l'usure, ténacité | Nécessite un post-traitement tel qu'un traitement thermique | Outils de coupe, moules, matrices |
Cobalt-Chrome | Biocompatibilité, résistance à l'usure, résistance élevée | Coût élevé, difficile à usiner | Implants médicaux, prothèses dentaires, pales de turbines |
Alliage de nickel 718 | Haute résistance, résistance à l'oxydation, soudabilité | Coûteux, difficile à traiter | Moteurs à réaction, production d'électricité, pétrole et gaz |
Aluminium AlSi10Mg | Légèreté, bonne résistance, facilité d'usinage | Résistance moindre par rapport aux aciers, nécessite une anodisation pour la résistance à la corrosion. | Pièces automobiles, électronique grand public, structures légères |
Bronze | Bonne résistance à l'usure, usinabilité, esthétique | Tendance au ternissement, propriétés mécaniques inférieures à celles de l'acier | Roulements, bagues, articles décoratifs |
Le fer | Haute résistance, propriétés magnétiques, faible coût | Sensible à la corrosion, résistance à la fatigue inférieure à celle des alliages | Composants structurels, pièces automobiles, dispositifs magnétiques |
Cette comparaison permet d'identifier la meilleure poudre métallique pour des applications spécifiques, en tenant compte de facteurs tels que le coût, les propriétés des matériaux et la facilité de traitement.
Fournisseurs et détails des prix pour Metal Binder Jet Solutions
Il est essentiel de trouver le bon fournisseur pour obtenir des poudres métalliques de haute qualité et un équipement de projection de liant fiable. Vous trouverez ci-dessous un tableau répertoriant quelques-uns des principaux fournisseurs de l'industrie, ainsi que les tarifs de leurs produits.
Fournisseur | Poudres métalliques disponibles | Fourchette de prix (par kg) | Localisation | Site web |
---|---|---|---|---|
Hoganas AB | Acier inoxydable, cuivre, bronze, fer | $50-$200 | Suède | hoganas.com |
GKN Additive | Inconel, aluminium, titane, acier à outils | $100-$400 | Allemagne | gknpm.com |
Technologie des charpentiers | Alliages de nickel, cobalt-chrome, acier à outils | $150-$500 | ÉTATS-UNIS | cartech.com |
Fabrication additive Sandvik | Acier inoxydable, titane, cuivre, fer | $70-$300 | Suède | additif.sandvik.com |
Epson Atmix | Aluminium, bronze, acier inoxydable | $60-$250 | Japon | epson.jp |
AP&C (une société de GE Additive) | Titane, aluminium, alliages de nickel | $200-$600 | Canada | advancedpowders.com |
Les prix peuvent varier en fonction de facteurs tels que le type de poudre métallique, la quantité requise et la localisation du fournisseur. Il est conseillé de demander des devis à plusieurs fournisseurs pour s'assurer de la compétitivité des prix et de la disponibilité.
Avantages et inconvénients des solutions de jet de liant métallique
Comme toute technologie de fabrication, la projection de liant métallique a ses avantages et ses inconvénients. Les comprendre peut vous aider à décider en connaissance de cause si cette méthode est adaptée à vos besoins de production.
Pour | Cons |
---|---|
Vitesse d'impression élevée | Imprime rapidement des couches sans qu'il soit nécessaire de les fondre ou de les fusionner |
Polyvalence des matériaux | Compatible avec une large gamme de poudres métalliques |
Rentabilité | Plus abordable pour les petites et moyennes séries |
Géométries complexes | Capacité à produire des dessins et des structures internes complexes |
Respect de l'environnement | Moins de déchets produits, les matériaux ne sont utilisés que là où ils sont nécessaires |
Résistance moindre par rapport aux méthodes traditionnelles | Peut nécessiter un post-traitement pour obtenir les propriétés mécaniques souhaitées |
L'état de surface peut nécessiter un traitement ultérieur. | Des étapes supplémentaires telles que le polissage ou l'usinage peuvent être nécessaires. |
Disponibilité limitée du matériel | Tous les métaux ne conviennent pas à la projection de liant |
En pesant le pour et le contre, les fabricants peuvent déterminer si le jet de liant métallique correspond à leurs objectifs de production, qu'il s'agisse de la vitesse, du coût ou de la capacité à produire des pièces complexes.
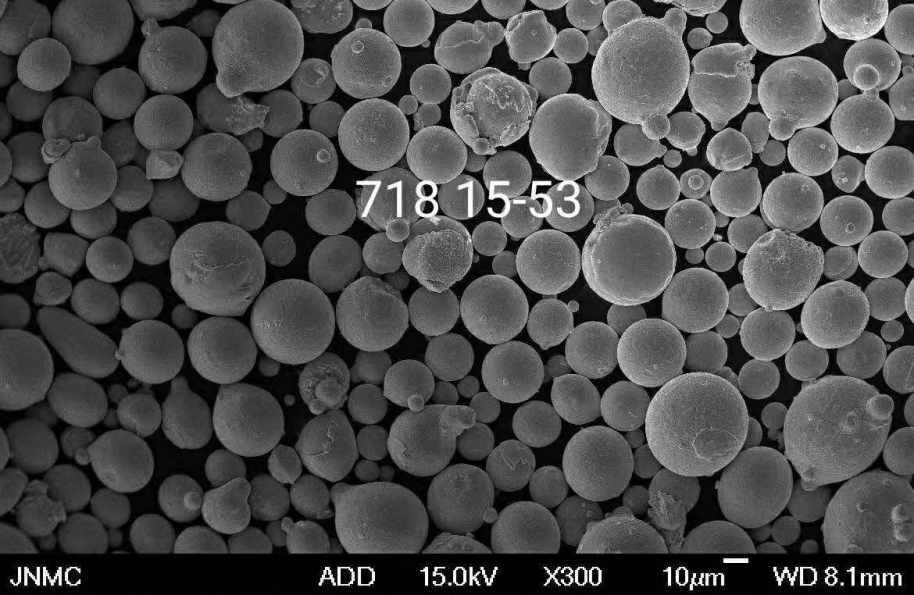
FAQ
Voici quelques questions fréquemment posées sur solutions de jet de liant métalliqueet leurs réponses afin de dissiper les doutes qui subsistent.
Question | Réponse |
---|---|
Qu'est-ce que la projection de liant métallique ? | Le jet de liant métallique est un processus de fabrication additive qui utilise un liant pour fusionner la poudre de métal en pièces solides. |
En quoi le jet de liant métallique diffère-t-il des autres méthodes d'impression 3D ? | Contrairement à d'autres méthodes, le jet de liant métallique ne nécessite pas de faire fondre la poudre. Elle utilise plutôt un liant et un processus de frittage, ce qui permet une impression plus rapide et un plus grand nombre d'options de matériaux. |
Quels métaux peuvent être utilisés dans la projection de liant ? | Les métaux courants sont l'acier inoxydable, le titane, l'Inconel, le cuivre et l'aluminium. Le choix du métal dépend des propriétés souhaitées pour la pièce finale. |
Un post-traitement est-il nécessaire dans le cas de la projection de liant métallique ? | Oui, des étapes de post-traitement telles que le frittage, le polissage ou l'usinage sont souvent nécessaires pour obtenir les propriétés mécaniques et l'état de surface souhaités. |
Quelle est la résistance des pièces fabriquées par projection de liant métallique ? | La résistance des pièces obtenues par projection de liant est comparable à celle des pièces fabriquées traditionnellement, en particulier après le frittage. Toutefois, elles peuvent nécessiter un traitement thermique supplémentaire pour atteindre une résistance optimale. |
Quelles sont les industries qui bénéficient le plus de la projection de liants métalliques ? | Les industries telles que l'aérospatiale, l'automobile, la médecine et la joaillerie bénéficient de cette technologie en raison de sa capacité à produire des pièces complexes et de haute précision. |
La projection de liant métallique est-elle respectueuse de l'environnement ? | Oui, elle est considérée comme plus respectueuse de l'environnement que la fabrication soustractive traditionnelle car elle produit moins de déchets. |
Quel est le coût de la projection de liant métallique par rapport à d'autres méthodes de fabrication ? | Le jet de liant métallique est généralement plus rentable pour les petites et moyennes séries, en particulier par rapport à des méthodes telles que l'usinage CNC ou le moulage. |
La projection de liant métallique permet-elle de produire des pièces de grande taille ? | Alors que le jet de liant métallique est généralement utilisé pour les pièces de petite et moyenne taille, les progrès technologiques permettent d'élargir le potentiel de fabrication de pièces plus grandes. |
Conclusion
Le jet de liant métallique représente une avancée significative dans la fabrication additive, offrant un mélange de vitesse, de flexibilité des matériaux et de capacité à produire des géométries complexes. Alors que les industries continuent d'explorer son potentiel, cette technologie est en passe de devenir une pierre angulaire de la fabrication moderne, stimulant l'innovation et l'efficacité dans divers secteurs.