Alliage CuCrZr (C18150) est un alliage durcissant par précipitation, connu pour ses propriétés mécaniques, thermiques et électriques élevées. Cet alliage est largement utilisé dans les dispositifs d'échange de chaleur et dans le domaine de la fusion nucléaire.
Alliage CuCrZr est un alliage très intéressant qui peut remplacer le cuivre pur dans de nombreuses applications, avec un taux de Cr compris entre 0,5 et 1,2 % en poids et un taux de Zr compris entre 0,03 et 0,3 % en poids. Il est en outre plus facile à fabriquer que le cuivre pur, grâce à la technologie de fabrication additive basée sur le laser, qui présente des propriétés mécaniques supérieures et garantit une conductivité thermique suffisamment élevée pour être considérée comme une alternative efficace au cuivre pur dans de nombreuses applications.
Pour les forgés Alliage CuCrZrle recuit de mise en solution et le durcissement par vieillissement sont les principaux traitements thermiques qui peuvent être effectués, tandis que le recuit de mise en solution peut être omis dans le cas des alliages LPBF CuCrZr.
Recuit en solution: Ce traitement est effectué en chauffant le matériau dans une atmosphère inerte protectrice (généralement Ar) au-dessus de 900°C pendant 30 minutes ou plusieurs heures. Le matériau est ensuite rapidement refroidi dans l'eau ou l'air pour sursaturer la matrice de cuivre en Cr et Zr. Dans le cas des pièces LPBF, ce traitement est déjà terminé pendant le processus LPBF car le bain de fusion se refroidit suffisamment vite pour agir comme une trempe et produire une microstructure sursaturée. Les pièces recuites par mise en solution sont très souples et leurs propriétés mécaniques sont trop faibles pour être considérées comme un traitement thermique distinct.
Durcissement par l'âge: Généralement, ce traitement suit le recuit de mise en solution et est effectué à des températures plus basses pendant une période plus longue (typiquement de 400°C à 600°C, jusqu'à 6 heures dans un environnement inerte (Ar, vide, N2 et parfois aussi dans une atmosphère H2). Ce traitement est conçu pour permettre la précipitation contrôlée de phases intermétalliques dures dans des matériaux sursaturés afin de produire des composés binaires ou ternaires de Cu, Cr et Zr.
Dans ce travail, seuls les le durcissement par l'âge est étudié avec une température fixée à 550°C, trois durées différentes ont été vérifiées. L'objectif était de comprendre comment la durée du traitement thermique affecte le matériau et si le traitement de durcissement par vieillissement est applicable pour répondre aux exigences mécaniques du CuCrZr en utilisant la fabrication additive pour les composants des réacteurs de fusion.
Les la composition chimique, la distribution de la taille des particules (DTS) et la forme des particules des poudres utilisée dans cette étude est présentée dans le certificat ci-dessous :
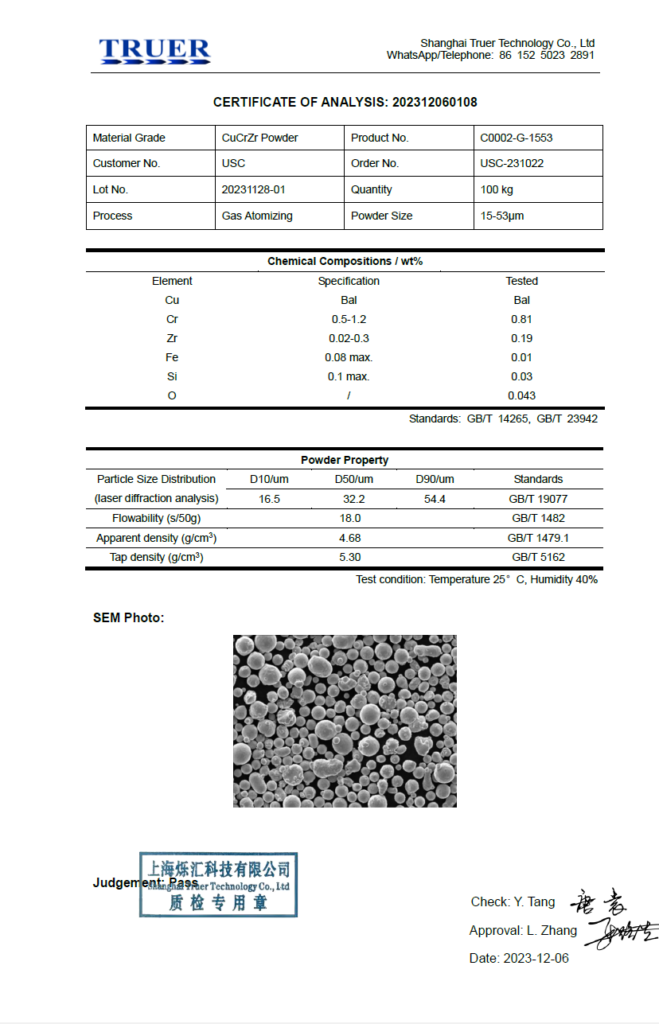
Dans cette étude, les échantillons utilisés pour l'enquête ont été imprimés dans des géométries proches de la forme d'un filet. L'échantillon est ensuite usiné afin d'éliminer la peau rugueuse et d'obtenir la géométrie correcte pour les essais de dureté.
L'optimisation des paramètres est effectuée afin d'obtenir la plus grande densité d'échantillons avec la combinaison de l'espacement de balayage (dans la plage de 0,06-0,1 mm), la vitesse du laser (de 350 à 650 mm/s) et la puissance du laser maintenue à 370 W, la largeur de la bande fixée à 5 mm et l'épaisseur de la couche fixée à 0,03 mm pour toutes les couches. À chaque couche, la direction des bandes change avec une rotation de 67°. Dans ce projet, l'orientation verticale est la même que celle du bâtiment. Diagramme en Figure 1:
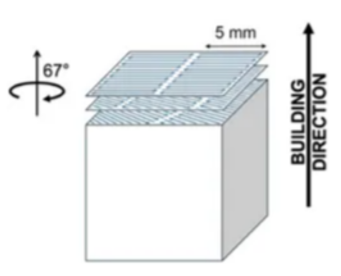
Figure 1. Schéma du processus de fabrication additive
Quarante cubes (10 mm x 10 mm x 10 mm) ont été fabriqués avec différentes combinaisons d'espacement et de vitesse de balayage. Leur densité est ensuite mesurée par la méthode d'Archimède.
Les échantillons tels que construits ont été traités par trois vieillissement durcissement à 550 °C pendant 1 h, 3 h et 6 h dans une atmosphère d'azote avec une pente de chauffage et de refroidissement de 150 °C/h (refroidissement dans un four et dans une atmosphère protectrice).
L'histogramme en Figure 2 montre la densité relative moyenne de toutes les combinaisons des paramètres du processus d'étude, mesurée par la méthode d'Archimède. La densité de référence est égale à 8,8869 g/cm3. Cette valeur est ensuite utilisée pour calculer la densité relative de l'échantillon fabriqué additivement.
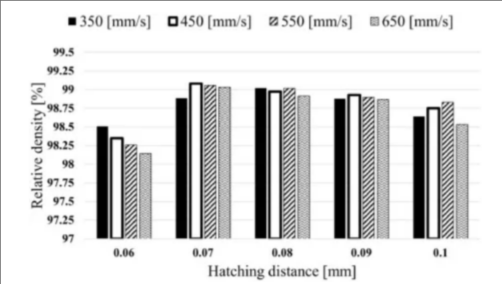
Figure 2. Densité relative des échantillons en fonction des paramètres du processus
La densité relative la plus élevée (99,15 %) a été obtenue en utilisant l'ensemble des paramètres suivants : puissance du laser 370 W, espacement de balayage (distance de hachurage) 0,07 mm, vitesse de balayage 450 mm/s et largeur de bande 5 mm. Pour un espacement de balayage de 0,07 mm, il n'y a pas eu de changement significatif de la densité relative en fonction de la vitesse de balayage.
Un espacement de balayage de 0,06 mm n'est pas bon pour la densité, ce qui donne des valeurs de densité comprises entre 98 et 98,5 %. Cela peut être dû à une accumulation de chaleur entraînant une surchauffe qui réduit la densité finale.
Figure 3 montre la microstructure des échantillons après 1h et 6h de traitement de vieillissement. Elle montre qu'une durée de durcissement plus longue n'a pas altéré les caractéristiques microstructurales qui peuvent être observées à faible grossissement, durée de 1h comparée à la durée de 6h.
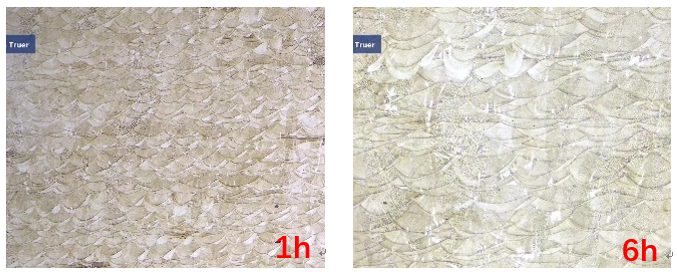
Figure 3. Microstructures des échantillons de 1h et 6h
Figure 4 montre des micrographies SEM de l'échantillon 6h. De nombreuses particules circulaires peuvent être observées (en particulier dans la figure 5c) dans les grains colonnaires, qui peuvent être des particules nanodurcies. Un examen plus approfondi par EDS de ces précipités de taille nanométrique a montré qu'il s'agissait de petits précipités de Cr ou de Zr de quelques nanomètres à 50 nanomètres uniformément dispersés à l'intérieur du matériau.
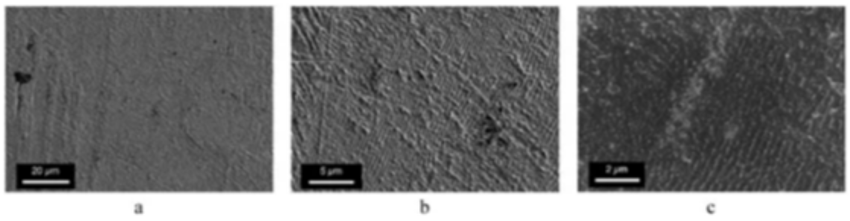
Figure 4 Images d'électrons secondaires MEB à différents grossissements après vieillissement à 550 °C pendant 6 h
Des défauts ont également été observés dans les échantillons étudiés. Figure 5 présente certains défauts typiques des pièces obtenues par AM, tels que l'absence de fusion et la porosité créée principalement par le piégeage de gaz.
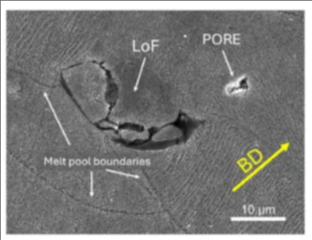
Figure 5 Défauts constatés dans la section transversale de l'échantillon LPBF tel qu'il a été construit
Figure 6 est la valeur de la microdureté Vickers pour les échantillons tels que construits et traités thermiquement. Il est facile de comprendre que la dureté est plus faible dans les conditions de construction que dans les échantillons vieillis : un vieillissement de 1 heure à 550 °C améliore considérablement cette dureté (165 HV, soit le double de la valeur de 84 HV des échantillons construits). Après 3 heures de vieillissement, la dureté de l'échantillon a commencé à diminuer (144 HV en moyenne) et après 6 heures de traitement, le matériau s'est encore ramolli, mais dans ce cas, il y a également eu une amélioration par rapport à l'état de construction. Cela signifie que la durée de 6 heures est trop longue, ce qui entraîne un grossissement des précipités. On peut constater qu'une heure est déjà efficace pour augmenter la dureté du matériau par rapport aux conditions de construction. Cela signifie que le matériau a subi un vieillissement excessif après 1 heure.
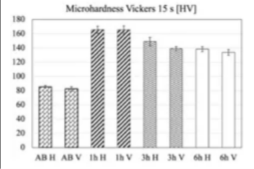
Figure 6 Valeurs de microdureté Vickers pour les échantillons tels que construits et vieillis
En résumé, d'un point de vue mécanique, le traitement de vieillissement est prometteur pour l'amélioration des propriétés mécaniques de l'alliage LPBF CuCrZr. Mais il est nécessaire d'effectuer des recherches pour trouver la combinaison optimale des propriétés de la poudre, des paramètres LPBF et du processus de vieillissement.