Vue d'ensemble Impression 3d tungstène
Le tungstène, également connu sous le nom de wolfram, est un métal dur et dense qui présente une excellente résistance à haute température, ce qui le rend idéal pour les applications nécessitant une grande rigidité, une résistance à l'usure ou des performances à haute température jusqu'à 1000°C. Le tungstène a une densité de 19,3 g/cm3, ce qui le rend deux fois plus dense que l'acier et proche de l'uranium pur en termes de densité.
L'impression 3D de tungstène et d'alliages de tungstène permet de produire des pièces dans des géométries complexes impossibles à réaliser avec les méthodes de fabrication traditionnelles. La grande rigidité et la résistance à l'usure du tungstène en font un matériau idéal pour l'impression 3D d'outils de moulage, d'électrodes, de composants de protection contre les radiations, de poids de lestage et d'autres applications nécessitant des propriétés matérielles de haute densité.
Le tungstène peut être imprimé en 3D à l'aide de technologies de fusion sur lit de poudre, notamment la fusion sélective par laser (SLM) et la fusion par faisceau d'électrons (EBM). Ces deux méthodes consistent à faire fondre sélectivement des couches de poudre de tungstène pour construire une pièce solide en 3D. Les principaux éléments à prendre en compte pour l'impression 3D sont les suivants Impression 3d tungstène comprennent la conception des pièces, la sélection des poudres, les paramètres du processus d'impression, le post-traitement et les propriétés des matériaux.
Cet article fournit un guide complet sur l'impression 3D avec un revêtement en tungstène :
- Principales applications des pièces en tungstène imprimées en 3D
- Types de poudres métalliques de tungstène
- Aperçu des procédés de fusion sélective par laser et de fusion par faisceau d'électrons
- Paramètres d'impression et considérations
- Procédures de post-traitement
- Propriétés mécaniques et microstructure
- Fournisseurs et analyse des coûts
- Principes et limites de la conception
- Comparaison avec d'autres procédés de fabrication
- Avantages et inconvénients de la technologie
Principales applications des pièces en tungstène imprimées en 3D
Le tungstène est utilisé dans l'impression 3D pour les produits nécessitant une densité, une rigidité, une dureté et une résistance à la température élevées. Les applications typiques sont les suivantes :
application | Description |
---|---|
Protection contre les rayonnements | La densité du tungstène bloque les rayons gamma et les rayons X nocifs. Utilisé dans les domaines médical, nucléaire et aérospatial. |
Amortissement des vibrations | La densité du tungstène amortit efficacement les vibrations. Utilisé pour les instruments de précision. |
Poids de lestage | La haute densité permet d'équilibrer et d'étalonner les systèmes avec précision. |
Contacts avec les électrodes | Résiste à l'arc électrique. Utilisé dans les contacts électriques et les interrupteurs à vide. |
Automobile | Alliages de tungstène dans les composants automobiles de haute performance. |
Exploitation minière | Outils de forage et d'exploitation minière en carbure de tungstène résistant à l'usure. |
Aérospatiale | Tuyères de fusées, pales de turbines et autres composants à haute température. |
Militaire | Pénétrateurs à énergie cinétique, munitions perforantes. |
Médical | Bistouris à haute rigidité, outils dentaires, vis à os. |
L'impression 3D permet d'obtenir des géométries complexes de pièces en tungstène qui ne sont pas réalisables avec l'usinage soustractif, ce qui élargit les applications dans les industries qui ont besoin de propriétés métalliques à haute performance.
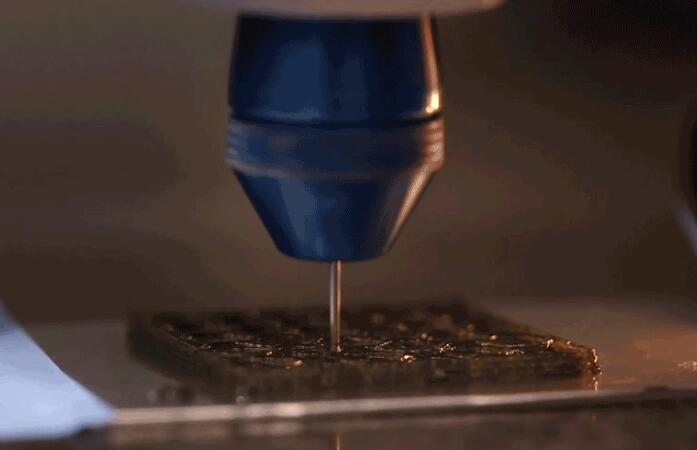
Types de poudres métalliques de tungstène pour l'impression 3D
Le tungstène est disponible en différents types de poudres pour les procédés d'impression 3D par fusion sur lit de poudre :
Type de poudre | Description | Forme des particules | Taille des particules |
---|---|---|---|
Pure tungstène | Tungstène élémentaire, pureté de 99,9%. | Sphérique | 15-45 microns |
Carbure de tungstène | Cermet de carbure de tungstène et de cobalt | Sphérique/irrégulier | 45-150 microns |
Alliages de tungstène | Alliages lourds de tungstène avec du nickel, du fer ou du cuivre | Sphérique | 15-45 microns |
Le tungstène pur est préféré pour la fusion laser sur lit de poudre en raison de sa température de fusion plus élevée que celle des alliages de tungstène. Les qualités de carbure de tungstène contiennent un liant de cobalt et sont plus dures mais plus difficiles à traiter. Pour la fusion sur lit de poudre, des poudres plus grossières allant jusqu'à 150 microns peuvent être utilisées.
Les poudres sphériques offrent un meilleur écoulement et une meilleure densité d'emballage. Les particules de taille inférieure à 45 microns améliorent la résolution, l'état de surface et le frittage. Toutefois, la manipulation de poudres très fines nécessite des précautions en raison de l'inflammabilité des poudres.
Aperçu du processus de fusion sélective par laser pour le tungstène
La fusion sélective par laser (SLM) utilise un faisceau laser pour fusionner sélectivement des zones d'un lit de poudre de tungstène afin de construire des objets en 3D couche par couche. Le processus se déroule dans une chambre à gaz inerte avec des niveaux d'oxygène inférieurs à 0,1 % pour éviter l'oxydation.
Étapes du processus SLM :
- La poudre de tungstène est étalée en fines couches sur une plaque de construction à l'aide d'un bras de recouvrement.
- Le faisceau laser trace chaque couche, chauffant la poudre au-dessus du point de fusion pour créer des régions solides fondues.
- La plaque de construction s'abaisse légèrement et une nouvelle couche de poudre est étalée sur la couche précédente.
- Les étapes sont répétées jusqu'à ce que la pièce entière soit construite à partir de poudre de tungstène.
- La poudre non fondue soutient les surplombs et les contre-dépouilles pendant l'impression et est recyclée par la suite.
- Des températures élevées allant jusqu'à 3000°C sont générées par la fusion au laser de points de poudre localisés.
- Les pièces sont ensuite retirées du gâteau de poudre et post-traitées.
Le SLM permet d'imprimer des géométries complexes directement à partir d'un modèle CAO 3D, ce qui n'est pas possible avec le moulage ou l'usinage. On obtient une résolution fine de 0,02-0,05 mm et des surfaces lisses.
Paramètres clés du processus d'impression SLM pour le tungstène
L'optimisation des paramètres d'impression SLM est essentielle pour obtenir des pièces en tungstène de haute densité avec une microstructure et des propriétés mécaniques contrôlées.
Paramètres d'impression | Gamme typique | Rôle |
---|---|---|
Puissance du laser (W) | 100-400 W | Fait fondre la poudre efficacement. Une puissance plus élevée augmente le taux de construction. |
Vitesse de balayage (mm/s) | 100-1000 mm/s | Vitesse du laser traversant chaque couche. Affecte l'apport d'énergie. |
Espacement des hachures (μm) | 50-200 μm | Distance entre les lignes de balayage. Affecte le chevauchement et la densification. |
Épaisseur de la couche (μm) | 20-100 μm | Les couches minces améliorent la résolution mais ralentissent la construction. |
Décalage de la mise au point (mm) | 0 à -2 mm | Défocalise le spot pour un bain de fusion plus large et un meilleur collage des couches. |
Température de préchauffage (°C) | 100-400 °C | Chauffe le lit de poudre pour réduire les contraintes thermiques. Améliore l'adhérence des couches. |
Ces paramètres doivent être équilibrés afin de fournir suffisamment d'énergie pour la fusion tout en minimisant les contraintes résiduelles dues aux gradients thermiques élevés.
Méthodes de post-traitement pour les pièces en tungstène obtenues par SLM
Après le processus de fabrication SLM, un post-traitement supplémentaire est nécessaire pour obtenir une pièce en tungstène finie :
- Retrait du lit de poudre – ; Les pièces sont extraites avec précaution de la poudre non consolidée environnante.
- Suppression du support – ; Les supports sont coupés de la pièce manuellement ou dissous chimiquement.
- Soulagement des contraintes thermiques – ; Le recuit à 1000-1500°C soulage les contraintes résiduelles et améliore la ductilité.
- Pressage isostatique à chaud – ; La trempe à plus de 2000°C densifie encore la microstructure.
- Usinage – ; Le fraisage CNC permet d'obtenir des tolérances et des finitions de surface plus étroites.
- Traitements de surface – ; Le revêtement ou le polissage des métaux peut améliorer les propriétés de la surface.
Un post-traitement adéquat est essentiel pour obtenir la précision dimensionnelle, la microstructure et les propriétés matérielles requises après l'état d'impression.
Propriétés mécaniques du tungstène SLM
La fusion sélective au laser permet de produire des pièces en tungstène presque entièrement denses, dont les propriétés sont proches de celles des pièces corroyées :
Propriété | SLM Tungstène | Tungstène corroyé |
---|---|---|
Densité | Plus de 99% théorique | 99.9% |
Résistance à la traction | 450 à 650 MPa | 550 MPa |
Limite d'élasticité | 400 à 500 MPa | 500 MPa |
Élongation | 3 à 8 | 10% |
Dureté | 300 à 400 HV | 340 HV |
Conductivité thermique | 140 à 180 W/mK | 174 W/mK |
La microstructure ultrafine résultant d'une solidification rapide permet d'obtenir une dureté et une résistance très élevées. Cependant, le tungstène sensible aux fissures doit être pressé isostatiquement à chaud et recuit pour améliorer sa ductilité.
Microstructure du tungstène SLM
La microstructure du tungstène SLM tel qu'il est construit consiste en de fins grains de tungstène β colonnaires le long de la direction de construction, mesurant 5 à 10 microns de large et s'allongeant sur plusieurs centaines de microns de long.
Dans les colonnes, on observe des structures cellulaires à sous-grains d'une largeur allant jusqu'à 500 nm, résultant d'un cycle thermique complexe pendant le balayage laser. La microstructure présente une forte densité de dislocations, des pores à l'échelle nanométrique et des particules non fondues entre les joints de grains.
Le recuit post-processus recristallise cette structure en colonnes en grains de tungstène plus uniformes et plus grossiers, d'une largeur de plus de 50 microns, avec des contraintes internes et une densité de dislocation réduites.
Fusion sélective par laser et fusion par faisceau d'électrons
La fusion par faisceau d'électrons (EBM) est un procédé alternatif de fusion en lit de poudre qui utilise une source de chaleur par faisceau d'électrons au lieu d'un laser.
Comparaison | slm | EBM |
---|---|---|
Source de chaleur | Laser | Faisceau d'électrons |
Atmosphère | Argon | Le vide |
Contrôle du faisceau | Scanner Galvo | Bobines électromagnétiques |
Taille maximale de construction | 250 x 250 x 300 mm | 200 x 200 x 350 mm |
Résolution | 50 μm | 70 μm |
Précision | +/- 100 μm | +/- 150 μm |
Finition de la surface | Brut de décoffrage, lisse après usinage | Texture rugueuse |
Le balayage rapide du faisceau de la SLM permet une résolution et une finition de surface plus fines. L'avantage de l'EBM est une vitesse de construction plus élevée et une manipulation plus simple des poudres dans le vide.
Fournisseurs de poudre de tungstène pour l'impression 3D
Divers fabricants fournissent des poudres de tungstène pour l'impression 3D par fusion sur lit de poudre :
Fournisseur | Types de poudre | Taille des particules | Tarification |
---|---|---|---|
Buffalo Tungstène | tungstène pur, carbure de tungstène | 10-44 μm | 100 à 200 $/kg |
Midwest Tungsten | Pure tungstène | 10-40 μm | 80-250 $/kg |
H.C. Starck | Tungstène pur, alliages de tungstène | 15-45 μm | 150 à 350 $/kg |
Tungstène de Nanjing | Pure tungstène | 15-45 μm | 100-250 $/kg |
Ressources de Tyranna | Pure tungstène | Inférieur à 45 μm | 250-400 $/kg |
Le coût de la poudre varie de 80 $/kg pour les poudres de faible pureté à plus de 400 $/kg pour les poudres de haute précision. Une grande partie de la matière est perdue sous forme de poudre non fondue lors de la fabrication.
Analyse des coûts des pièces en tungstène imprimées en 3D
Voici une ventilation des coûts pour la production SLM de pièces en tungstène :
Élément de coût | Estimation typique |
---|---|
poudre de tungstène | 100-250 dollars par kg |
Autres matières premières | 2 à 10 dollars par construction |
Frais de machine | 50 à 150 dollars par heure |
Travail | 40 à 100 $ de l'heure |
Post-traitement | 20 à 50 dollars par pièce |
Coût total de la pièce | 100 $ par 100 g jusqu'à 5 000 $ pour les grandes pièces complexes |
Pour les petites pièces de moins de 100 g, il faut compter 100 dollars par pièce. Les pièces plus grandes et plus complexes peuvent coûter jusqu'à 5 000 dollars en raison des longs délais de fabrication et de la consommation importante de matières premières.
Par rapport à l'usinage, l'impression 3D en tungstène a un coût plus élevé, mais elle permet d'obtenir des géométries de pièces jusqu'alors impossibles.
Principes de conception des pièces en tungstène obtenues par SLM
Une conception optimale des pièces est essentielle pour exploiter les capacités de l’impression 3D et éviter les défauts lors de l’utilisation du tungstène :
- Utiliser des parois plus épaisses et des structures de plus de 2 mm pour éviter les fissures dues aux contraintes résiduelles.
- Réduire au minimum les géométries en surplomb nécessitant des structures de soutien.
- Inclure des trous de décharge, des arrondis ou des congés pour éviter les concentrations de contraintes.
- Concevoir des volumes fermés comme des structures en treillis pour améliorer l'élimination des poudres.
- Orienter les pièces de manière à minimiser les porte-à-faux non soutenus et à éviter les longues sections minces susceptibles de se déformer.
- Tenez compte d'une tolérance d'impression de ~100 μm et mettez les pièces à l'échelle en conséquence.
- Concevoir les surfaces d'accouplement pour le post-usinage afin d'obtenir un ajustement de précision.
- Tirez parti de la liberté de conception – ; consolidez les assemblages en pièces uniques complexes.
Effectuer des simulations thermiques et structurelles pour identifier les zones à forte contrainte résiduelle lors de la conception. Éviter les caractéristiques délicates susceptibles d'être endommagées lors du post-traitement.
Limites de l'impression 3D avec du tungstène
Malgré ses avantages, le tungstène pose également des problèmes pour les procédés de fusion sur lit de poudre :
- Le tungstène à haute densité réfléchit l'énergie du laser, ce qui limite les taux d'absorption et de construction.
- Une faible conductivité thermique entraîne une accumulation de chaleur qui déforme les pièces.
- Températures élevées et réactivité avec l'oxygène/l'azote pendant le traitement.
- Les pièces présentent des microstructures fragiles, susceptibles de se fissurer.
- Un post-traitement important est nécessaire pour obtenir des propriétés proches du corroyage.
- La taille maximale des pièces est limitée par le volume de construction de l'imprimante.
- Les surfaces verticales ont une mauvaise finition et doivent être usinées.
- Le coût des poudres, comparativement élevé, fait grimper les coûts.
Un contrôle minutieux du processus est nécessaire pour réussir à imprimer des composants en tungstène de haute qualité.
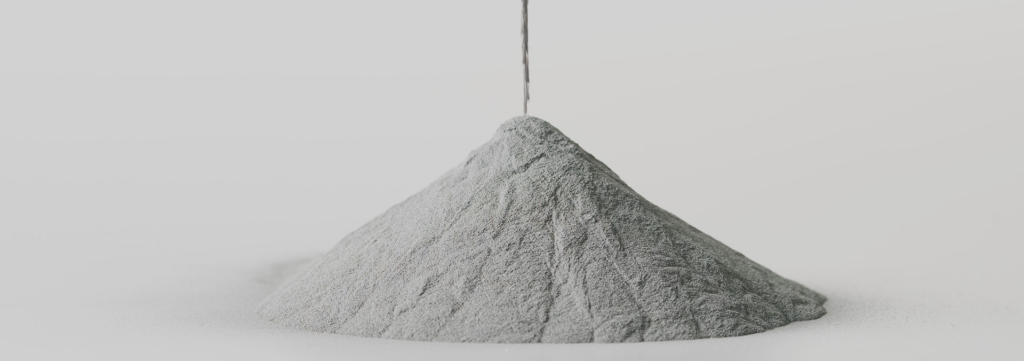
Avantages de la Impression 3d tungstène pièces
Les principaux avantages de la fabrication additive avec le tungstène sont les suivants :
- Géométries complexes – ; Produire des dessins complexes impossibles à réaliser avec le tungstène coulé ou usiné.
- Assemblages consolidés – ; Intégrer plusieurs composants dans une seule pièce imprimée.
- Personnalisation de masse – ; Modifier et optimiser facilement les conceptions pour chaque application.
- Réduction du poids – ; Créer des treillis légers et des structures internes impossibles à réaliser avec des méthodes soustractives.
- Dureté élevée – ; Les pièces imprimées atteignent une dureté de 400 HV.
- Délai d'exécution rapide – ; Réduction du temps de développement par rapport aux méthodes d'outillage traditionnelles.
- Consolidation partielle – ; Combiner des assemblages en composants complexes uniques.
- Zéro déchet – ; La poudre non fusionnée est réutilisée au lieu d'être mise au rebut.
L'impression 3D ouvre la voie à de nouvelles applications innovantes pour le tungstène dans les secteurs exigeant des propriétés métalliques de haute performance.
Inconvénients et limites de l'impression 3D en tungstène
- Coût élevé – ; La poudre de tungstène est chère. Une grande partie de la poudre non utilisée est gaspillée dans les constructions.
- Ductilité plus faible – ; Le tungstène imprimé est susceptible de se fissurer en l'absence de post-traitement.
- Taille limitée – ; Les volumes de construction de l'imprimante limitent les dimensions maximales des pièces.
- Surfaces rugueuses – ; Les faces verticales ont une mauvaise finition et doivent être usinées.
- Processus long – ; Le temps d'impression et de post-traitement est lent pour les volumes de production.
- Sensibilité des paramètres – ; La réalisation de constructions sans défaut nécessite une mise au point approfondie.
- Questions de sécurité – ; La manipulation de la poudre de tungstène nécessite un équipement de protection contre l'inflammabilité.
Le tungstène imprimé en 3D convient mieux à la production en faible volume de pièces complexes de grande valeur où la performance l'emporte sur le coût.
L'avenir de l'impression 3D en tungstène
La fabrication additive à base de tungstène connaîtra une nouvelle croissance dans les années à venir :
- Élargissement de la gamme d'alliages et de composites de tungstène disponibles.
- Des machines de plus grande taille permettent d'imprimer des pièces plus grandes.
- Amélioration de la réutilisation et du recyclage des poudres, ce qui réduit les coûts des matériaux.
- Fabrication hybride combinant l'impression et l'usinage.
- Meilleure compréhension des relations processus-microstructure-propriété.
- Nouvelles applications dans les secteurs de l'aérospatiale, de la défense, de l'automobile et de la médecine.
- Procédés de dépôt d'énergie dirigée (DED) pour l'impression de grandes pièces de forme quasi-nette.
- Normalisation des paramètres d'impression, des qualifications et des certifications.
Avec une adoption accrue, les composants en tungstène imprimés en 3D passeront du prototypage à des cas d'utilisation en production plus large.
Conclusion
L'impression 3D offre une méthode innovante pour fabriquer des composants en tungstène de haute performance avec des géométries complexes qui ne sont pas réalisables avec les techniques conventionnelles. Les applications vont du blindage contre les radiations et des poids de lestage aux électrodes et aux composants aérospatiaux.
Le processus de fusion sélective par laser peut produire des pièces de tungstène presque entièrement denses à partir de couches de poudre, mais l'optimisation minutieuse des paramètres d'impression et du post-traitement est cruciale pour les propriétés et les performances. Bien que le coût soit encore une limitation, le tungstène imprimé en 3D ouvre la voie à de nouvelles conceptions et à des possibilités de personnalisation dans tous les secteurs d'activité.
Avec l'amélioration continue des procédés et le développement de nouveaux alliages de tungstène, la fabrication additive sera de plus en plus utilisée pour des pièces exigeant des propriétés de densité, de rigidité, de dureté et de résistance à la chaleur très élevées.
FAQ
Voici les réponses à quelques questions courantes sur l'impression 3D avec du tungstène :
Quels sont les principaux avantages de Impression 3d tungstène pièces ?
Les principaux avantages de l'impression 3D sont la liberté de conception, la personnalisation de masse, les assemblages consolidés, les treillis légers, le prototypage rapide et la possibilité d'obtenir des géométries complexes impossibles à réaliser par usinage ou moulage.
Quelles méthodes d'impression 3D de métaux peuvent traiter le tungstène ?
Les procédés de fusion sélective par laser (SLM) et de fusion par faisceau d'électrons (EBM) sur lit de poudre sont actuellement utilisés pour imprimer le tungstène.
Quelles sont les industries qui utilisent des pièces en tungstène imprimées en 3D ?
Les industries de l'aérospatiale, de la défense, de l'automobile, de la médecine, de l'électronique et du nucléaire utilisent des composants en tungstène imprimés en 3D.
Quels types de poudre de tungstène peuvent être utilisés pour l'impression 3D ?
Poudres de tungstène pur, de carbure de tungstène-cobalt et d'alliages lourds de tungstène d'une taille comprise entre 10 et 45 microns. Les poudres sphériques donnent les meilleurs résultats.
Le tungstène imprimé nécessite-t-il un post-traitement ?
Des post-traitements tels que le détensionnement, le pressage isostatique à chaud et l'usinage sont nécessaires pour améliorer la ductilité, la densification, les tolérances et l'état de surface.
Comment les propriétés du tungstène imprimé se comparent-elles à celles du tungstène conventionnel ?
Le tungstène imprimé soigneusement traité peut atteindre une densité de 99 % et correspondre presque à la résistance et à la dureté d'un matériau forgé. La ductilité est légèrement inférieure.
Quels sont les exemples d'utilisation finale des pièces en tungstène imprimées en 3D ?
Inserts de tuyères, électrodes, protections contre les radiations, contrepoids, lest de haute densité, composants d'équilibrage et outils de coupe des métaux utilisant des alliages lourds de tungstène.
Quelles sont les dimensions des pièces en tungstène qui peuvent être imprimées en 3D ?
Les systèmes actuels à lit de poudre permettent d'obtenir des composants d'une taille maximale d'environ 250 x 250 x 300 mm, mais des systèmes plus grands sont en cours de développement.
Le tungstène imprimé en 3D est-il abordable pour une utilisation en production ?
Pour des pièces de taille moyenne, l'impression en tungstène coûte entre 100 et 5 000 dollars. La production de volumes plus importants est encore limitée par le coût élevé de la poudre.