En matière d'alliages à hautes performances, peu de matériaux peuvent rivaliser avec les capacités exceptionnelles des alliages suivants Poudre d'Inconel 939. Cette poudre métallique polyvalente fait partie de la famille des superalliages à base de nickel et est réputée pour sa résistance exceptionnelle à la chaleur, à l'oxydation et à la corrosion. La poudre d'inconel 939 joue un rôle essentiel dans les industries où les conditions environnementales extrêmes sont constantes, telles que l'aérospatiale, la production d'énergie et l'automobile. Mais qu'est-ce qui la rend si spéciale ? Plongeons dans le monde de la poudre d’inconel 939 pour comprendre sa composition, ses propriétés, ses applications et bien plus encore.
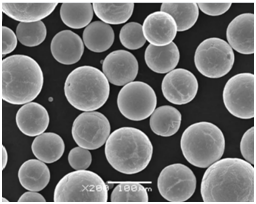
Aperçu de la poudre d'Inconel 939
L'Inconel 939 est un alliage de nickel-chrome durci par précipitation, conçu pour les applications exigeant une résistance aux températures élevées et à la corrosion. Ce superalliage est unique en raison de sa haute résistance à la traction, de son excellente stabilité thermique et de sa capacité à résister à l'oxydation à des températures allant jusqu'à 900°C. Mais ce n'est pas tout. La forme de poudre de l'Inconel 939 permet une plus grande flexibilité dans les applications, en particulier dans la fabrication additive et l'impression 3D, où la demande de matériaux de haute performance est en constante augmentation.
Caractéristiques principales de la poudre d'Inconel 939
- Résistance aux températures élevées: Capable de fonctionner à des températures élevées sans perdre sa résistance.
- Résistance à la corrosion et à l'oxydation: Protège les composants des environnements difficiles, réduisant ainsi les coûts de maintenance.
- Durabilité: L'Inconel 939 conserve ses propriétés mécaniques sur de longues périodes, même sous l'effet des contraintes et de la chaleur.
- Soudabilité: Excellente compatibilité avec diverses techniques de fabrication, y compris le soudage et l'impression 3D.
Maintenant que nous avons effleuré la surface, explorons plus en détail sa composition spécifique, ses propriétés, ses applications et ses caractéristiques.
Composition des Poudre d'Inconel 939
La particularité de l'Inconel 939 réside dans sa composition. Comprenant un équilibre entre le nickel, le chrome et d'autres éléments tels que le titane et le molybdène, cet alliage a été mis au point pour offrir des performances optimales dans des environnements extrêmes.
Répartition de la composition
Élément | Pourcentage |
---|---|
Nickel (Ni) | 47-51% |
Chrome (Cr) | 18-23% |
Cobalt (Co) | 17-21% |
Molybdène (Mo) | 1.2-2% |
Titane (Ti) | 2-3% |
Aluminium (Al) | 1-1.5% |
Carbone (C) | ≤ 0.10% |
Bore (B) | ≤ 0.006% |
Comment la composition améliore la performance
- Nickel et chrome offrent une excellente résistance à l'oxydation et à la corrosion.
- cobalt améliore les performances à haute température, tandis que Molybdène offre une solidité et une résistance au fluage accrues.
- Titane et aluminium contribuent au durcissement par précipitation, ce qui augmente considérablement la résistance de l’alliage.
- Les faibles niveaux de Carbone et Bore permettent d'améliorer la ductilité sans compromettre la stabilité thermique.
Propriétés de la poudre d'Inconel 939
Il est essentiel de comprendre les propriétés de la poudre d'Inconel 939 pour comprendre pourquoi elle est privilégiée dans les applications critiques et soumises à de fortes contraintes. Cet alliage est conçu pour conserver son intégrité mécanique même dans les environnements les plus difficiles.
Propriétés physiques et mécaniques
Propriété | Valeur |
---|---|
Point de fusion | 1350°C - 1375°C |
Densité | 8.0 g/cm³ |
Résistance à la traction | 950 MPa |
Limite d'élasticité | 650 MPa |
Conductivité thermique | 14 W/m-K à 900°C |
Résistance à l'oxydation | Excellent jusqu'à 900°C |
Allongement à la rupture | 18-25% |
Dureté | 220-240 HB |
Des caractéristiques qui sortent de l'ordinaire
- Conductivité thermique: Bien que l'Inconel 939 soit principalement apprécié pour sa résistance à la chaleur, il possède également une bonne conductivité thermique, ce qui lui permet de rester stable sans se déformer ni se fissurer.
- Haute résistance à la traction: Ce matériau peut supporter des contraintes importantes avant de se déformer, ce qui en fait un matériau de choix pour les pales de turbines et d'autres composants critiques.
- Allongement et ductilité: Malgré sa résistance, l'Inconel 939 peut subir un allongement important sans se rompre, ce qui est idéal pour les applications nécessitant de la flexibilité.
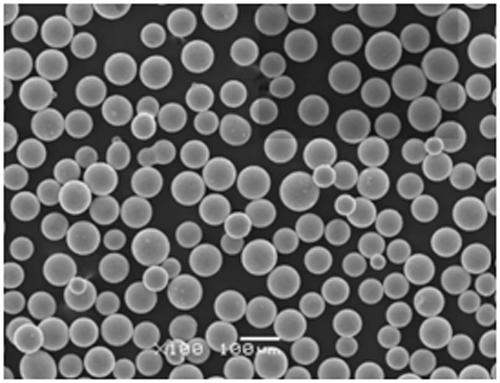
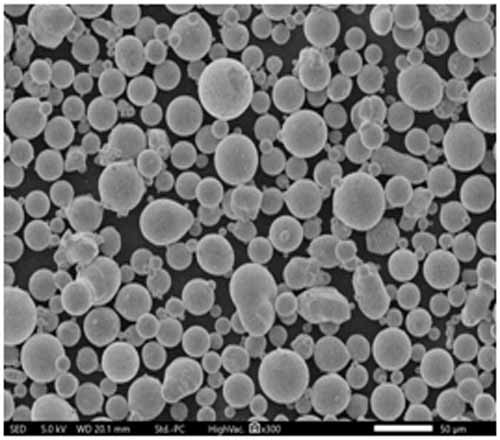
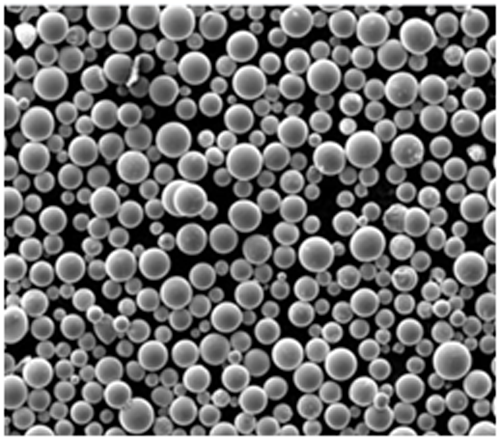
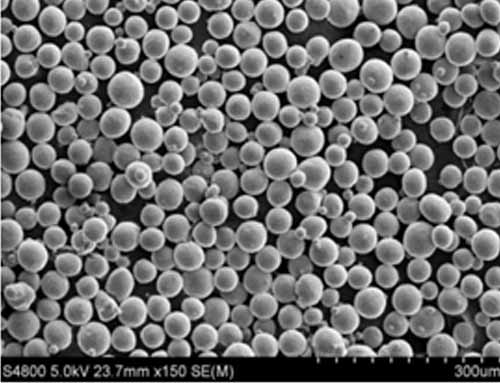
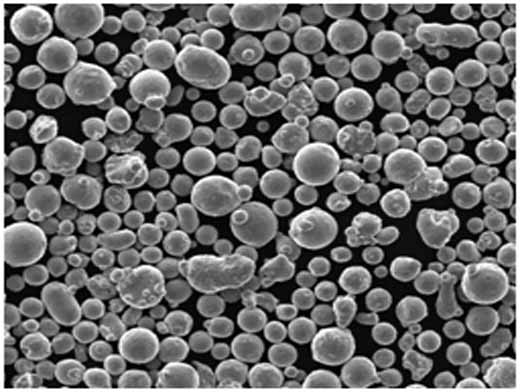
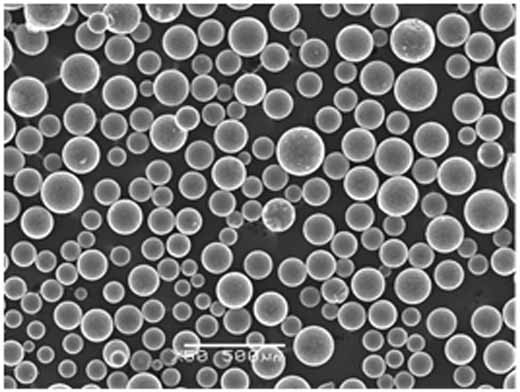
Caractéristiques de la poudre d'Inconel 939
La poudre d'Inconel 939 possède une combinaison unique de caractéristiques qui la rendent indispensable dans de nombreuses industries. Examinons plus en détail certaines de ses caractéristiques.
Caractéristiques principales
- Résistance exceptionnelle à la chaleur: Avec un point de fusion supérieur à 1300°C, l'Inconel 939 est conçu pour des applications à haute température où d'autres métaux seraient défaillants.
- Résistance à la corrosion: Cet alliage forme une couche d'oxyde protectrice qui lui permet de résister à la corrosion, même dans des environnements chargés de sels, d'acides ou d'eau de mer.
- Durcissement par précipitation: Grâce à un traitement thermique, l'Inconel 939 atteint une dureté et une durabilité remarquables, ce qui le rend idéal pour les composants soumis à de fortes contraintes, tels que les pales de turbines et les fixations aérospatiales.
- Polyvalence sous forme de poudre: Sous forme de poudre, il est idéal pour les techniques de fabrication additive comme l'impression 3D, où la précision et la performance sont cruciales.
Applications de la poudre d'Inconel 939
Maintenant que nous avons abordé la composition et les propriétés de la poudre d’inconel 939, parlons de ses applications. L'Inconel 939 est utilisé dans certains des domaines les plus exigeants en raison de sa capacité à supporter des conditions intenses.
Applications industrielles
L'industrie | Cas d'utilisation | Pourquoi l'Inconel 939 ? |
---|---|---|
Aérospatiale | Aubes de turbines, systèmes d'échappement | Résistance à la chaleur, résistance à la fatigue |
Production d'électricité | Turbines à gaz, turbines à vapeur | Longue durée de vie, stabilité thermique |
Automobile | Soupapes d'échappement, rotors de turbocompresseur | Résistance à l'oxydation et à la chaleur |
Pétrochimie | Échangeurs de chaleur, récipients sous pression | Résistance à la corrosion, capacités de cyclage thermique |
Fabrication additive | impression 3D de pièces complexes | Précision, excellentes propriétés de post-traitement |
Fours industriels | Eléments de chauffage, composants | Capacité à résister à des températures extrêmes |
Génie maritime | Arbres de pompes, hélices | Résistance à la corrosion de l'eau de mer |
Pourquoi cela change-t-il la donne dans ces secteurs ?
Dans des secteurs tels que aérospatiale et la production d'électricitél'équipement de l'entreprise fonctionne souvent à la limite des matériaux - des vitesses élevées, des températures extrêmes et des environnements corrosifs sont la norme. L'Inconel 939 ne se contente pas de survivre dans ces conditions, il prospère. C'est pourquoi vous le trouverez dans les produits suivants aubes de turbine, systèmes d'échappementet récipients sous pression.
Avantages de la poudre d'Inconel 939
L'Inconel 939 a gagné sa place parmi les alliages de haute performance grâce à ses nombreux avantages. Soulignons quelques-uns des principaux avantages qui en font un choix privilégié pour les applications critiques.
Avantages principaux
- Résistance à haute température: Capable de conserver son intégrité mécanique à des températures supérieures à 900°C, l'Inconel 939 surpasse la plupart des autres alliages à cet égard.
- Résistance à l'oxydation: Protège contre la dégradation de l'environnement, prolonge la durée de vie des composants et réduit la fréquence des réparations.
- Résistance à la corrosion: Gère l'exposition à divers environnements corrosifs, y compris le sel, la vapeur et les gaz.
- Durabilité: Connu pour sa capacité à résister à des contraintes à long terme sans usure ou dommages significatifs.
- Avantages de la poudre: Idéal pour les méthodes de fabrication avancées, en particulier l'impression 3D, où des géométries complexes et des détails fins sont nécessaires.
Modèles de poudre Inconel 939
Il existe plusieurs modèles spécifiques de poudre d'Inconel 939, chacun étant conçu pour des applications différentes. Examinons quelques-uns des principaux modèles :
Modèles notables de poudre d'Inconel 939
Nom du modèle | Composition | Applications |
---|---|---|
Poudre Inconel 939 AM | Composition standard de l'Inconel 939 | Fabrication additive pour les pièces aérospatiales |
Poudre Inconel 939 EBM | Optimisation de la fusion par faisceau d'électrons (EBM) | Impression 3D EBM, composants de précision pour turbines |
Poudre Inconel 939 L-PBF | Compatible avec la fusion laser-poudre (L-PBF) | composants automobiles et aérospatiaux imprimés en 3D |
Inconel 939 GAS Atomisé | Atomisation du gaz pour une plus grande pureté | Implants médicaux, applications de haute pureté |
Inconel 939 Formage par pulvérisation | Application de formage par pulvérisation | Rotors de turbines à gaz, pièces pour la production d'énergie lourde |
Inconel 939 traité HIP | Pressage isostatique à chaud | Pièces à haute résistance nécessitant une structure sans vide |
Inconel 939 qualité fine | Granulation de poudre fine | Pièces de haute précision nécessitant des détails complexes |
Inconel 939 qualité grossière | Granulation de poudres grossières | Composants de grande taille avec des exigences modérées en matière d'état de surface |
Poudre pré-alliée Inconel 939 | Poudre pré-alliée pour plus de cohérence | Cohérence des processus de fabrication |
Inconel 939 PM (métallurgie des poudres) | Version métallurgie des poudres | Composants structuraux pour l'aérospatiale et turbines à gaz |
Chaque modèle présente de légères variations dans sa formulation ou son processus de fabrication afin de répondre aux besoins spécifiques des différentes applications.
Spécifications et qualités de la poudre d'inconel 939
Lorsque l'on sélectionne Poudre d'Inconel 939 pour votre projet, il est essentiel de comprendre les spécifications et les qualités disponibles. Voici un guide des qualités les plus courantes et des normes correspondantes.
Spécifications et normes
Spécification/Norme | Détails |
---|---|
AMS 5393 | Couvre la composition des alliages et le traitement des poudres |
UNS N09319 | Définit la composition chimique de l'Inconel 939 |
ASTM B637 | Présentation des propriétés mécaniques de l'Inconel 939 |
ISO 6208 | Spécifie les normes de taille de la granulation de la poudre |
DIN 17744 | Spécification européenne pour les alliages résistants à la chaleur |
Avantages et inconvénients de la poudre d'inconel 939
Comme tous les matériaux, la poudre Inconel 939 a ses forces et ses faiblesses. En voici un aperçu :
Avantages
Avantage | Pourquoi c'est important |
---|---|
Résistance aux hautes températures | Idéal pour les applications extrêmes telles que les turbines à gaz |
Résistance à l'oxydation et à la corrosion | Durabilité à long terme dans des environnements difficiles |
Compatibilité avec l'impression 3D | Précision et flexibilité dans la fabrication additive |
Longue durée de vie | Réduction des coûts de maintenance au fil du temps |
Inconvénients
Inconvénient | Pourquoi cela peut être préoccupant |
---|---|
Coût | Plus cher que les alliages traditionnels |
Usinabilité | Plus difficile à usiner que les matériaux plus tendres |
Fragilité à basse température | Peut être moins efficace dans les applications cryogéniques |
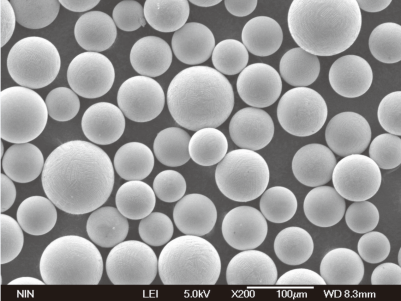
Fournisseurs et prix de la poudre d'Inconel 939
Il existe plusieurs fournisseurs clés de poudre d'Inconel 939, chacun proposant des formulations ou des modèles légèrement différents pour diverses industries.
Informations sur le fournisseur
Nom du fournisseur | Région | Prix (par kg) | Délai d'expédition |
---|---|---|---|
Technologie des charpentiers | ÉTATS-UNIS | $450 - $600 | 4-6 semaines |
Technologie des matériaux Sandvik | L'Europe | $400 - $550 | 3-5 semaines |
Kennametal Inc. | Mondial | $425 - $600 | 4-7 semaines |
Additive Manufacturing Ltd. | Asie | $470 - $620 | 5-8 semaines |
ATI Metals | Mondial | $450 - $580 | 3-6 semaines |
Les prix peuvent varier en fonction du modèle, de la quantité et du lieu d'expédition.
FAQ
Question | Réponse |
---|---|
Quelles sont les industries qui utilisent généralement la poudre d'Inconel 939 ? | Aérospatiale, production d'énergie, automobile et pétrochimie. |
Pourquoi la poudre d'Inconel 939 est-elle idéale pour l'impression 3D ? | Sa résistance à la chaleur et sa durabilité le rendent parfait pour les pièces de précision. |
L'Inconel 939 peut-il être soudé ? | Oui, il est hautement soudable et compatible avec diverses techniques de fabrication. |
Comment se compare-t-il aux autres superalliages ? | L'Inconel 939 offre des performances supérieures dans les environnements à haute température. |
Quelle est la différence entre l'Inconel 939 et l'Inconel 718 ? | L'Inconel 939 a une meilleure stabilité thermique mais est plus cher que l'Inconel 718. |
Conclusion
Poudre d'Inconel 939 est un matériau remarquable, offrant un mélange parfait de solidité, de résistance à la chaleur et de durabilité. Ses applications dans l'aérospatiale, la production d'énergie et la fabrication de pointe démontrent sa polyvalence et ses capacités dans des environnements exigeants. Que vous cherchiez à produire des pales de turbine à haute performance ou des pièces de précision pour l'impression 3D, la poudre d'Inconel 939 est un excellent choix à considérer. Bien que son prix soit élevé, sa longue durée de vie et ses performances dans des conditions extrêmes valent l'investissement.