Vue d'ensemble
Dépôt d'énergie dirigée (DED) est une technologie de fabrication additive de pointe qui dépose avec précision des matériaux, couche par couche, pour créer des pièces métalliques de haute qualité. Elle utilise des sources d'énergie focalisées telles que des lasers, des faisceaux d'électrons ou des arcs de plasma pour faire fondre le matériau, qui est ensuite déposé sur un substrat ou une pièce existante. Le DED est réputé pour sa capacité à produire des géométries complexes, à réparer des composants endommagés et à créer des pièces métalliques de haute performance dotées de propriétés mécaniques supérieures.
Grâce à sa polyvalence et à son efficacité, la technologie DED est largement utilisée dans divers secteurs, notamment l'aérospatiale, l'automobile, la médecine et l'énergie. Cette technologie offre des avantages significatifs par rapport aux méthodes de fabrication traditionnelles, tels que la réduction des déchets de matériaux, des délais de production plus courts et la possibilité de créer des conceptions complexes qui sont autrement difficiles à réaliser.
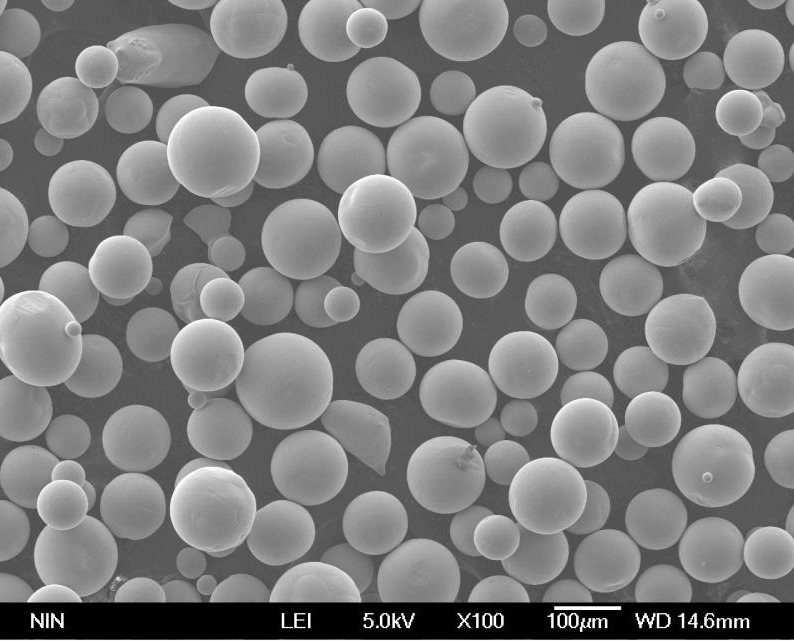
Types de poudres métalliques utilisées dans les DED
Poudres métalliques courantes pour DED
Modèle de poudre métallique | Composition | Propriétés | Applications |
---|---|---|---|
Inconel 625 | Nickel, chrome, molybdène | Haute résistance, résistant à la corrosion | Aérospatiale, marine, traitement chimique |
ti-6al-4v | Titane, aluminium, vanadium | Rapport résistance/poids élevé, biocompatible | Aérospatiale, implants médicaux, automobile |
Acier inoxydable 316L | Fer, chrome, nickel, molybdène | Résistance élevée à la corrosion, bonnes propriétés mécaniques | Agroalimentaire, dispositifs médicaux, applications marines |
Hastelloy X | Nickel, molybdène, chrome | Résistance à l'oxydation et aux hautes températures | Aérospatiale, turbines à gaz industrielles |
CoCrMo | Cobalt, chrome, molybdène | Résistant à l'usure, haute résistance | Implants médicaux, prothèses dentaires |
AlSi10Mg | Aluminium, Silicium, Magnésium | Léger, bonne conductivité thermique | Automobile, aérospatiale, électronique |
Acier maraging (18Ni-300) | Fer, nickel, cobalt, molybdène | Haute résistance, excellente ténacité | Outillage, aérospatiale, pièces de haute performance |
Cuivre | Cuivre pur | Excellente conductivité thermique et électrique | Composants électriques, échangeurs de chaleur |
Acier à outils (H13) | Fer, chrome, molybdène, vanadium | Dureté élevée, bonne résistance à la fatigue thermique | Outillage, moulage sous pression, moulage par injection |
Alliage de nickel 718 | Nickel, chrome, fer | Haute résistance, résistant à la corrosion | Aérospatiale, production d'électricité, pétrole et gaz |
Applications du DED
Applications courantes de la technologie DED
application | L'industrie | Avantages |
---|---|---|
Réparation des composants | Aérospatiale, Automobile | Rentable, prolonge la durée de vie des pièces |
Prototypage | Toutes les industries | Itération rapide de la conception, réduction du délai d'exécution |
Géométries complexes | Médical, aérospatial | Permet des conceptions complexes et des structures légères |
Parties fonctionnelles | Industrie manufacturière, industrielle | Composants performants et personnalisés |
Outillage et moules | Automobile, Fabrication | Outils durables et de haute précision |
Recherche sur les matériaux | Universitaire, Industriel | Propriétés des matériaux sur mesure, études expérimentales |
Spécifications et normes pour le DED
Spécifications des poudres métalliques courantes dans les DED
Modèle de poudre métallique | Taille des particules (μm) | Densité (g/cm³) | Point de fusion (°C) | Norme ASTM |
---|---|---|---|---|
Inconel 625 | 15-45 | 8.44 | 1290-1350 | ASTM B443 |
ti-6al-4v | 15-45 | 4.43 | 1604-1660 | ASTM B348 |
Acier inoxydable 316L | 15-45 | 7.99 | 1375-1400 | ASTM A276 |
Hastelloy X | 15-45 | 8.22 | 1260-1355 | ASTM B435 |
CoCrMo | 15-45 | 8.29 | 1330-1390 | ASTM F75 |
AlSi10Mg | 15-45 | 2.67 | 570-580 | ISO 3522 |
Acier maraging (18Ni-300) | 15-45 | 8.00 | 1413 | ASTM A538 |
Cuivre | 15-45 | 8.96 | 1083 | ASTM B216 |
Acier à outils (H13) | 15-45 | 7.80 | 1426 | ASTM A681 |
Alliage de nickel 718 | 15-45 | 8.19 | 1260-1336 | ASTM B637 |
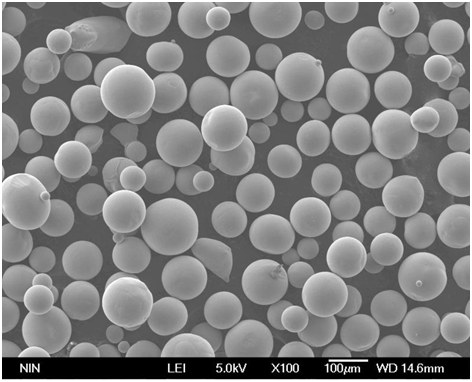
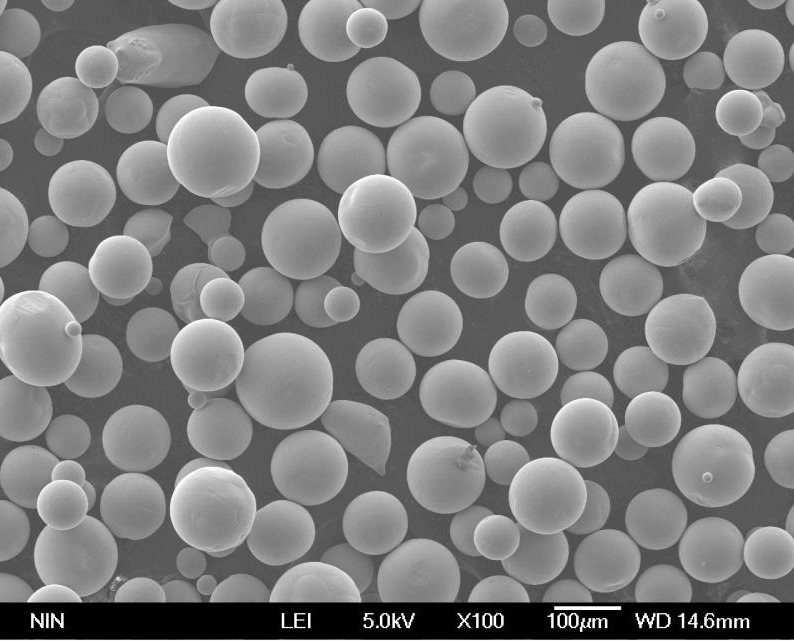
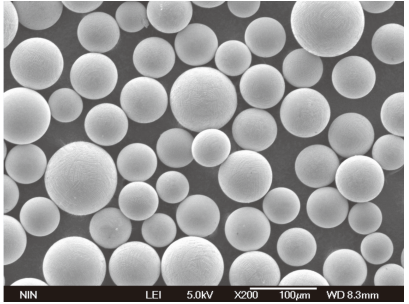
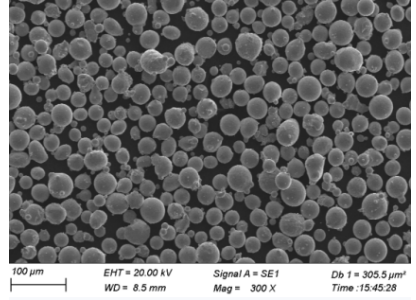
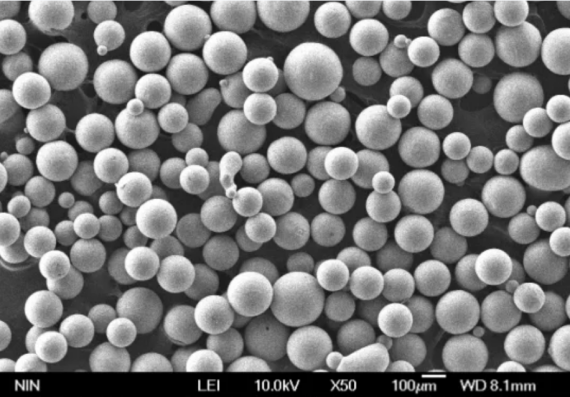
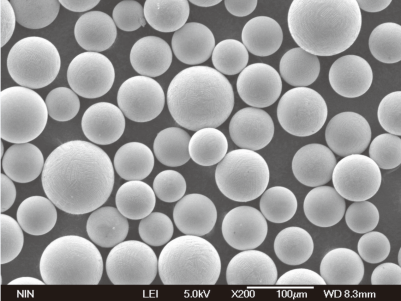
Fournisseurs et détails des prix
Fournisseurs et prix des poudres métalliques dans la DED
Fournisseur | Modèle de poudre métallique | Prix par kg (USD) | Localisation | Contact |
---|---|---|---|---|
Technologie des charpentiers | Inconel 625 | $100 | ÉTATS-UNIS | www.carpentertechnology.com |
Arcam AB | ti-6al-4v | $200 | Suède | www.arcam.com |
GKN Hoeganaes | Acier inoxydable 316L | $50 | ÉTATS-UNIS | www.gknpm.com |
HC Starck | Hastelloy X | $150 | Allemagne | www.hcstarck.com |
Sandvik | CoCrMo | $120 | Suède | www.materials.sandvik |
Technologie LPW | AlSi10Mg | $80 | ROYAUME-UNI | www.lpwtechnology.com |
Aubert & Duval | Acier maraging (18Ni-300) | $180 | France | www.aubertduval.com |
Tekna | Cuivre | $60 | Canada | www.tekna.com |
Hoganas AB | Acier à outils (H13) | $90 | Suède | www.hoganas.com |
VSMPO-AVISMA | Alliage de nickel 718 | $170 | Russie | www.vsmpo.ru |
Comparaison des avantages et des inconvénients de la technologie DED
Avantages et limites de la technologie DED
Aspect | Avantages | Limites |
---|---|---|
Efficacité des matériaux | Déchets minimes, utilisation élevée des matériaux | Coût initial élevé des matériaux |
Géométries complexes | Capacité à créer des motifs complexes | Limitée par la résolution et la précision de la machine |
Capacités de réparation | Réparation efficace de composants de grande valeur | Nécessite des opérateurs qualifiés et un contrôle précis |
Vitesse de production | Production plus rapide que les méthodes traditionnelles | Plus lent que d'autres méthodes de fabrication additive |
Propriétés mécaniques | Propriétés performantes et personnalisables | Potentiel de contraintes résiduelles et de défauts |
Polyvalence | Une large gamme de matériaux peut être utilisée | Limité par la disponibilité des matières premières |
Analyse détaillée des poudres métalliques pour DED
Inconel 625
L'Inconel 625 est un superalliage à base de nickel connu pour ses excellentes propriétés mécaniques et sa résistance à la corrosion, même à des températures élevées. Sa composition comprend des quantités importantes de nickel, de chrome et de molybdène, qui contribuent à sa solidité et à sa stabilité. Ce matériau est idéal pour les applications aérospatiales, marines et de traitement chimique, où les composants doivent résister à des environnements difficiles et à des contraintes élevées.
ti-6al-4v
Le Ti-6Al-4V, également connu sous le nom de titane de grade 5, est un choix populaire pour le DED en raison de son rapport résistance/poids élevé et de sa biocompatibilité. Composé de titane, d'aluminium et de vanadium, cet alliage offre d'excellentes propriétés mécaniques et une bonne résistance à la corrosion, ce qui le rend adapté à l'aérospatiale, aux implants médicaux et aux composants automobiles.
Acier inoxydable 316L
L'acier inoxydable 316L est un acier inoxydable austénitique connu pour sa grande résistance à la corrosion et ses bonnes propriétés mécaniques. L'ajout de molybdène améliore sa résistance à la corrosion, en particulier contre les chlorures et autres solvants industriels. Il est couramment utilisé dans l'industrie alimentaire, les appareils médicaux et les applications marines.
Hastelloy X
L'Hastelloy X est un superalliage à base de nickel qui présente une résistance à l'oxydation et une résistance à haute température exceptionnelles. Sa composition comprend du nickel, du molybdène et du chrome, qui lui confèrent d'excellentes propriétés mécaniques à des températures élevées.
Ce matériau est largement utilisé dans l'aérospatiale et les turbines à gaz industrielles.
CoCrMo
Le CoCrMo, ou alliage de cobalt-chrome-molybdène, est connu pour sa résistance exceptionnelle à l'usure et sa grande solidité. Ce matériau est couramment utilisé dans les implants médicaux et les prothèses dentaires en raison de sa biocompatibilité et de sa durabilité.
AlSi10Mg
AlSi10Mg est un alliage d'aluminium doté d'une bonne conductivité thermique et de propriétés de légèreté. L'ajout de silicium et de magnésium améliore ses propriétés mécaniques, ce qui le rend adapté aux applications automobiles, aérospatiales et électroniques.
Acier maraging (18Ni-300)
L'acier maraging (18Ni-300) est un alliage d'acier à haute résistance doté d'une excellente ténacité et d'une grande dureté. Il est composé de fer, de nickel, de cobalt et de molybdène et est utilisé dans l'outillage, l'aérospatiale et les pièces de haute performance.
Cuivre
Le cuivre est réputé pour son excellente conductivité thermique et électrique. En DED, le cuivre pur est utilisé pour les composants électriques, les échangeurs de chaleur et d'autres applications nécessitant une conductivité élevée.
Acier à outils (H13)
L'acier à outils H13 est un acier au chrome-molybdène-vanadium d'une grande dureté et d'une bonne résistance à la fatigue thermique. Il est largement utilisé dans les applications d'outillage, de moulage sous pression et de moulage par injection.
Alliage de nickel 718
L'alliage de nickel 718 est un alliage de nickel et de chrome connu pour sa grande solidité et sa résistance à la corrosion. Il est couramment utilisé dans l'aérospatiale, la production d'électricité et les industries du pétrole et du gaz.
Avantages du DED
Pourquoi choisir Dépôt d'énergie dirigée?
- Efficacité matérielle : La méthode DED utilise les matériaux de manière efficace, en minimisant les déchets et en optimisant l'utilisation. Contrairement aux méthodes soustractives traditionnelles, qui entraînent souvent une perte importante de matériaux, la méthode DED n'ajoute des matériaux que là où c'est nécessaire, ce qui en fait une option plus durable.
- Géométries complexes : Cette technologie permet de créer des dessins et des géométries complexes qui sont difficiles, voire impossibles, à réaliser avec les méthodes de fabrication traditionnelles. Cela ouvre de nouvelles possibilités pour des conceptions innovantes et des structures légères.
- Capacités de réparation : Le DED est très efficace pour réparer les composants de grande valeur, tels que les pales de turbines et les pièces aérospatiales. Il permet de prolonger considérablement la durée de vie de ces composants, réduisant ainsi les coûts et les temps d'arrêt.
- Vitesse de production : Par rapport à la fabrication traditionnelle, le DED permet de produire des pièces plus rapidement, en particulier pour les composants de petite et moyenne taille. Cela réduit les délais d'exécution et permet un prototypage et une itération rapides.
- Propriétés mécaniques : Les pièces DED présentent souvent des propriétés mécaniques supérieures, telles qu'une résistance et une durabilité accrues, en raison du contrôle précis du processus de dépôt des matériaux. Il en résulte des pièces très performantes qui répondent aux normes industrielles les plus strictes.
- Polyvalence : Le DED peut travailler avec une large gamme de matériaux, y compris les métaux, les céramiques et les composites. Cette polyvalence lui permet de s'adapter à diverses applications dans plusieurs secteurs d'activité.
Limites du DED
Quels sont les défis posés par le dépôt d'énergie dirigée ?
- Coûts initiaux élevés : L'investissement initial dans l'équipement et les matériaux DED peut être élevé, ce qui peut constituer un obstacle pour certaines entreprises. Toutefois, les avantages à long terme l'emportent souvent sur ces coûts, en particulier pour les applications de grande valeur.
- Résolution et précision de la machine : Si le DED permet de créer des géométries complexes, il est limité par la résolution et la précision des machines. Il peut être difficile d'obtenir des détails fins et des tolérances serrées.
- Opérateurs qualifiés requis : L'exploitation des systèmes DED nécessite des opérateurs qualifiés capables de contrôler avec précision le processus de dépôt. Cela peut augmenter les coûts d'exploitation et la complexité.
- Contraintes résiduelles potentielles : Les cycles de chauffage et de refroidissement rapides du DED peuvent entraîner des contraintes résiduelles et des défauts potentiels dans les pièces. Un contrôle adéquat du processus et des techniques de post-traitement sont nécessaires pour atténuer ces problèmes.
- Disponibilité des matières premières : Bien que le DED puisse fonctionner avec une large gamme de matériaux, la disponibilité de matières premières spécifiques peut être limitée. Cela peut restreindre le choix des matériaux pour certaines applications.
- Plus lent que certaines méthodes additives : Par rapport à d'autres méthodes de fabrication additive, telles que la fusion sur lit de poudre, la DED peut être plus lente pour certaines applications. Cela peut nuire à sa capacité à produire des volumes importants.
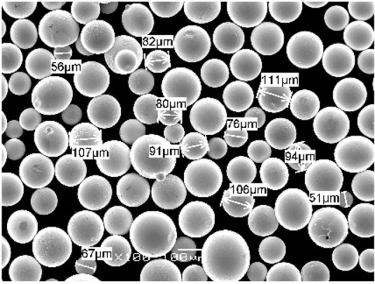
FAQ
Question | Réponse |
---|---|
Qu'est-ce que le dépôt d'énergie dirigée (DED) ? | Le dépôt par énergie dirigée (DED) est un procédé de fabrication additive qui utilise une énergie ciblée pour faire fondre et déposer des matériaux, couche par couche, afin de créer des pièces. |
Quels sont les matériaux qui peuvent être utilisés dans le cadre du DED ? | Le DED peut travailler avec une grande variété de matériaux, y compris les métaux, les céramiques et les composites. Les métaux les plus courants sont l'Inconel 625, le Ti-6Al-4V, l'acier inoxydable 316L, etc. |
Quels sont les avantages du DED ? | Les avantages du DED comprennent l'efficacité des matériaux, la capacité de créer des géométries complexes, des capacités de réparation efficaces, des vitesses de production rapides et des pièces de haute performance. |
Quelles sont les limites du DED ? | Les limites sont notamment les coûts initiaux élevés, les contraintes de résolution et de précision des machines, la nécessité d'opérateurs qualifiés, les contraintes résiduelles potentielles et la disponibilité des matières premières. |
Quelles sont les industries qui utilisent le DED ? | Les industries qui utilisent le DED sont, entre autres, l'aérospatiale, l'automobile, la médecine, l'énergie et l'industrie manufacturière. |
Comment le DED se compare-t-il aux autres méthodes de fabrication additive ? | Le DED offre des avantages en termes d'efficacité des matériaux et de capacités de réparation, mais il peut être plus lent et plus coûteux que d'autres méthodes additives telles que la fusion sur lit de poudre. |
La DED peut-elle réparer les composants existants ? | Oui, le DED est très efficace pour réparer les composants existants de grande valeur, prolonger leur durée de vie et réduire les coûts. |
La DED est-elle adaptée à la production à grande échelle ? | Si le DED est excellent pour le prototypage, les composants de petite et moyenne taille et les réparations, il peut être moins adapté à la production en grande série que d'autres méthodes. |
Quel est l'avenir de la technologie DED ? | L'avenir de la technologie DED est prometteur, les progrès constants en matière de matériaux, de contrôle des processus et de capacités des machines favorisant son adoption dans diverses industries. |
Comment choisir la bonne poudre métallique pour le DED ? | Le choix de la bonne poudre métallique dépend des exigences spécifiques de l'application, telles que les propriétés mécaniques, la résistance à la corrosion et la compatibilité avec le procédé DED. La consultation de fournisseurs et d'experts peut aider à faire le meilleur choix. |