El moldeo por inyección de metal (MIM) es un proceso metalúrgico utilizado para fabricar piezas pequeñas y complejas utilizando metal en polvo y plástico. El MIM combina la flexibilidad de diseño del moldeo por inyección de plástico con la resistencia e integridad de los metales mecanizados. Permite la fabricación rentable de componentes con dimensiones que oscilan entre 1 gramo y 500 gramos.
En Proceso MIM produce piezas con excelentes propiedades mecánicas, tolerancias de precisión y acabados superficiales lisos. Esto hace que el MIM sea adecuado para fabricar componentes metálicos pequeños, complejos y con forma de red en grandes volúmenes para industrias como la automovilística, médica, aeroespacial y electrónica, entre otras.
Esta guía ofrece una visión completa del proceso MIM, sus aplicaciones, ventajas, consideraciones de diseño, equipos, materiales, postprocesado, control de calidad y análisis de costes. Incluye tablas y comparaciones detalladas para ayudar a ingenieros, diseñadores de productos y responsables de compras a conocer y evaluar el proceso MIM.
Visión general del proceso MIM
El moldeo por inyección de metales combina técnicas de moldeo por inyección de plásticos con procesos pulvimetalúrgicos. Los pasos básicos del proceso MIM son:
- Mezclando: Mezcla de polvo metálico fino con un aglutinante plástico para crear una materia prima homogénea
- Moldeo por inyección: Calentar e inyectar la materia prima en un molde para formar una pieza verde moldeada.
- Debinding: Eliminación del aglutinante plástico de la pieza verde moldeada mediante procesos térmicos o con disolventes
- Sinterización: Calentamiento de la pieza desmoldeada hasta justo por debajo del punto de fusión del polvo para densificar la pieza mediante difusión atómica y formar una pieza metálica sólida.
En el siguiente cuadro se resumen las etapas clave del proceso MIM:
Escenario | Descripción |
---|---|
Mezcla | Mezcla de polvo metálico fino con aglutinantes en una materia prima homogénea |
Moldeo por inyección | Calentamiento e inyección de materia prima en un molde para formar una pieza verde |
Desbobinado | Eliminación del aglutinante mediante disolventes o procesos térmicos |
Sinterización | Calentamiento de la pieza descortezada para densificar el polvo y formar la pieza metálica |
El proceso MIM produce componentes metálicos consistentes y de alta calidad adecuados para la fabricación de grandes volúmenes. El proceso es altamente repetible y puede crear geometrías complejas con tolerancias estrechas que no son posibles con otras técnicas de fabricación.
Aplicaciones y uso industrial de las piezas MIM
El MIM se utiliza en muchos sectores para fabricar componentes metálicos pequeños, complejos y con forma de red con tolerancias muy ajustadas.
En la siguiente tabla se describen los principales ámbitos de aplicación y ejemplos de piezas fabricadas mediante MIM:
Industria | Ejemplos de aplicaciones |
---|---|
Automotor | Engranajes, piñones, balancines, bielas |
Aeroespacial | Álabes de turbina, impulsores, toberas, válvulas |
Médico | Brackets de ortodoncia, instrumentos quirúrgicos, implantes |
Electrónica | Conectores, microengranajes, pantallas, boquillas de impresora |
Armas de fuego | Gatillos, martillos, seguros, eyectores |
Relojes | Engranajes, piñones, agujas de reloj |
El MIM permite fabricar pequeñas piezas de precisión con geometrías complejas que, de otro modo, requerirían un extenso mecanizado u otras operaciones secundarias. Ofrece libertad de diseño, consolidación de piezas y reducción de peso frente a otras alternativas de fabricación.
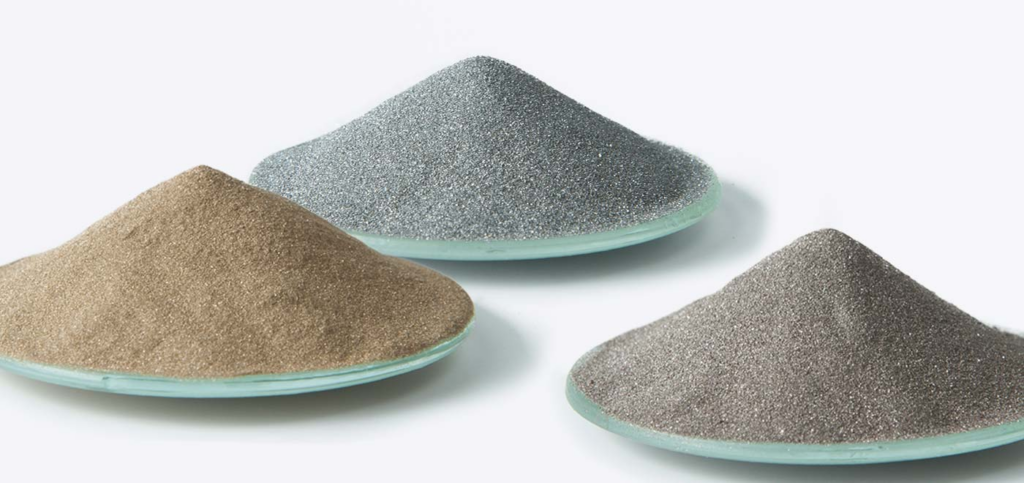
Ventajas y beneficios del MIM
El MIM ofrece varias ventajas con respecto a otros procesos de fabricación de piezas metálicas pequeñas:
Libertad de diseño
- Se pueden moldear geometrías y formas complejas en 3D que resultan difíciles o imposibles con otros métodos.
- En los diseños MIM pueden incorporarse fácilmente elementos complejos como roscas, cavidades y orificios.
- Permite la consolidación de piezas y la reducción del ensamblaje frente al mecanizado de múltiples componentes.
Precisión y tolerancias
- El MIM permite mantener una precisión dimensional constante y tolerancias de hasta ±0,1%.
- Se pueden conseguir detalles finos con buenos acabados superficiales de hasta 0,5 μm Ra.
Propiedades de los materiales
- Las piezas MIM sinterizadas suelen alcanzar entre el 95 y el 99% de las densidades de los metales forjados.
- Puede utilizarse una amplia gama de materiales, como acero inoxidable, acero para herramientas, aleaciones de titanio y aleaciones de tungsteno.
- Excelentes propiedades mecánicas con la rigidez, resistencia, dureza y resistencia al desgaste de los metales moldeados.
Productividad y costes
- Altas tasas de producción posibles con tiempos de ciclo rápidos utilizando MIM.
- Costes de pieza inferiores al mecanizado CNC para volúmenes medios y altos.
- Costes inferiores a los de la fundición a la cera perdida para diseños complejos de varios componentes.
- Elimina las operaciones de mecanizado secundarias necesarias para los componentes metálicos fabricados.
Sostenibilidad
- Mínimo desperdicio de material, ya que el MIM utiliza un procesamiento cercano a la forma de red.
- Proceso pulvimetalúrgico con menor consumo de energía que el mecanizado o la fundición de metales.
- Permite aligerar el peso optimizando las geometrías, lo que reduce la huella medioambiental.
La siguiente tabla resume las principales ventajas del MIM y las compara con otros procesos:
Ventaja | Comparación con otros procesos |
---|---|
Libertad de diseño | Más flexibilidad que el mecanizado o la fundición de metales |
Precisión | Muy superior a la fundición en arena o a presión |
Propiedades de los materiales | Enfoques de los metales forjados a diferencia de la pulvimetalurgia |
Productividad | Mayores volúmenes que el mecanizado CNC |
Relación coste-eficacia | Costes inferiores a los del mecanizado CNC o la fundición a la cera perdida para volúmenes medios o superiores |
Sostenibilidad | Menos residuos que los procesos sustractivos como el mecanizado CNC |
El MIM combina la libertad geométrica del moldeo por inyección de plástico con propiedades de los materiales cercanas a las de los metales totalmente densos. Esto permite a los diseñadores de productos consolidar ensamblajes, optimizar componentes y fabricar piezas metálicas complejas de gran valor a costes competitivos.
Consideraciones sobre el diseño de piezas MIM
El diseño adecuado de la pieza es fundamental para aprovechar al máximo las ventajas del proceso MIM. Algunas consideraciones clave del diseño son:
Grosores de pared - Se recomiendan espesores de pared moderados, entre 0,8 mm y 5 mm. Las secciones excesivamente gruesas o finas pueden provocar defectos.
Tolerancias - Son posibles tolerancias de precisión de ±0,1% de las dimensiones, pero hay que tener en cuenta la contracción por sinterización.
Acabados superficiales - Es posible obtener acabados superficiales finos por debajo de 1 μm Ra en función de la superficie de la herramienta, las geometrías y las operaciones de postmoldeo.
Geometría - Es importante evitar geometrías demasiado delicadas y mantener la integridad estructural para prevenir defectos. Se prefieren ángulos de inclinación mínimos superiores a 1-2°.
Características - Se pueden incorporar al diseño MIM orificios de hasta 0,5 mm de diámetro, roscas y características internas complejas.
Tamaño de la pieza - Los componentes más pequeños, de entre 0,5 y 500 gramos, son ideales para el procesamiento MIM. Las piezas más grandes pueden requerir mecanizado CNC.
Montaje - Diseño para la consolidación de piezas mediante la combinación de componentes y ensamblajes complejos en piezas MIM únicas.
Un diseño adecuado de los componentes MIM optimiza la fabricabilidad, minimiza los defectos y aprovecha las principales ventajas del proceso MIM. Es muy recomendable consultar a los proveedores de MIM durante la fase de diseño.
Equipos y herramientas MIM
En las fases de preparación de la materia prima, moldeo, desbobinado y sinterización del proceso MIM se utilizan equipos especializados:
Mezcla y preparación de la materia prima
- Mezcladoras - Mezcladoras de alta intensidad para la homogeneidad de la materia prima
- Molinos - Molinos de cestas o de rodillos para la reducción de partículas finas
- Reguladores de temperatura - Para regular la temperatura de las materias primas
- Desgasificación - Unidades de vacío para eliminar las burbujas de aire atrapadas
Moldeo por inyección
- Máquinas de moldeo por inyección - Máquinas modificadas para manipular materias primas MIM
- Moldes - Fabricados normalmente con aceros para herramientas/inoxidables tratados térmicamente para resistir la sinterización.
- Controles de temperatura del molde - Para regular la temperatura del molde durante el moldeo
Desbobinado
- Cámaras de desaglomerado con disolventes - Para la extracción de aglutinantes con disolventes
- Autoclaves de descortezado por vapor - Para procesos de descortezado por vapor
- Hornos térmicos de desaglomerado - Para eliminar aglutinantes mediante procesos térmicos
Sinterización
- Hornos de sinterización - Hornos de vacío, de hidrógeno o de nitrógeno
- Sistemas de control de la atmósfera - Para regular la atmósfera de los hornos
- Controles de perfilado de temperatura - Para ejecutar ciclos de sinterización optimizados
La correcta configuración y calibración de los equipos de MIM es vital para obtener componentes sin defectos y de alta calidad. La fase de moldeo por inyección requiere el equipo más especializado, como moldes de alta temperatura.
Materiales MIM
La tecnología MIM permite procesar una amplia gama de metales, aleaciones y cerámicas. Algunos de los materiales MIM más comunes son:
Metales
- Aceros inoxidables (316L, 17-4PH, 410)
- Aceros para herramientas (H13, P20, D2)
- Aceros de baja aleación (4140)
- Aleaciones magnéticas
- Aleaciones de cobre
- Aleaciones de titanio
- Aleaciones pesadas de wolframio
Cerámica
- Alúmina
- Zirconia
- Nitruro de silicio
- Carburos
La selección del material depende de factores como la temperatura de sinterización, el coste, las propiedades mecánicas y físicas y las necesidades de procesamiento secundario. El acero inoxidable 316L es el material MIM más común debido a su excelente sinterizabilidad.
La tabla siguiente muestra los materiales MIM más comunes y sus aplicaciones típicas:
Material | Aplicaciones |
---|---|
Acero inoxidable 316L | Instrumental quirúrgico, bombas, válvulas |
Acero para herramientas H13 | Moldeo por inyección, extrusión, matrices |
Titanio Ti-6Al-4V | Aeroespacial, implantes médicos |
Aleaciones pesadas de wolframio | Protección contra radiaciones, amortiguación de vibraciones |
Aleaciones de cobre | Contactos eléctricos, gestión térmica |
Cerámica | Herramientas de corte, piezas de desgaste, balística |
El MIM permite utilizar materiales de altas prestaciones, como el titanio y las aleaciones de acero para herramientas, en diseños de componentes pequeños y complejos. Amplía las posibilidades de diseño de aplicaciones médicas, aeroespaciales, automovilísticas e industriales.
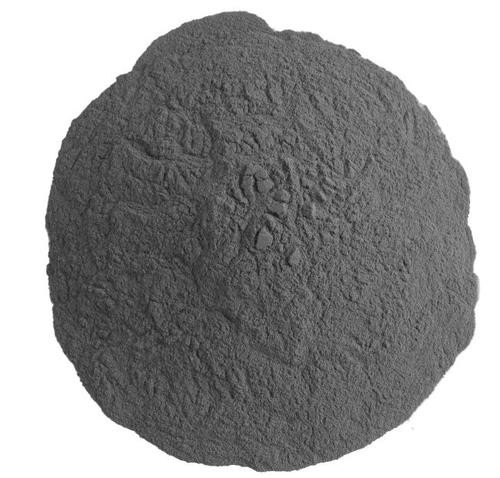
Operaciones de postprocesamiento
A menudo, tras la sinterización del MIM se requieren fases de procesamiento secundarias para obtener la pieza final:
- Recocido - Tratamiento térmico antiestrés
- Endurecimiento - Proceso de endurecimiento térmico como el austempering
- Mecanizado - Funciones de mecanizado CNC como diámetros de perforación de precisión
- Únase a - Soldadura por láser, soldadura o unión epoxídica de subcomponentes
- Acabado - Chapeado, pintado, pasivado u otro acabado superficial
En el cuadro siguiente se describen los procesos post-MIM más comunes y sus objetivos:
Post-proceso | Propósito |
---|---|
Recocido | Alivio de tensiones, ductilidad |
Endurecimiento | Mejora de la dureza y la resistencia |
Mecanizado | Dimensiones y ajustes críticos |
Únase a | Montaje de productos de varias piezas |
Acabado | Aspecto, resistencia a la corrosión |
El postprocesado amplía las opciones de mejora de propiedades y mecanizado de precisión. Esto amplía aún más la aplicabilidad del MIM en aplicaciones exigentes.
Control de calidad e inspección
La calidad constante y el control dimensional son fundamentales para los componentes MIM. Las pruebas de control de calidad típicas incluyen:
- Análisis químico - Para la composición mediante espectroscopia de emisión óptica o de fluorescencia de rayos X.
- Mediciones de densidad - Método de Arquímedes o picnometría de gas para determinar la densidad sinterizada
- Pruebas mecánicas: dureza, resistencia a la tracción y a la fatiga según las normas ASTM.
- Microscopía - Para análisis de microestructura, porosidad, tamaño de grano y defectos.
- Análisis dimensional - Escaneado óptico o por TC para dimensiones y conformidad con GD&T
- Análisis de superficies - Pruebas de rugosidad, corrosión y revestimiento, según proceda.
En la siguiente tabla se describen las principales pruebas de calidad realizadas durante las distintas fases del procesamiento del MIM:
Escenario | Pruebas de calidad típicas |
---|---|
Materia prima | Viscosidad, torsión, humedad |
Parte verde | Dimensiones, inspección de defectos |
Desbobinado | Pérdida de peso, residuos |
Sinterización | Densidad, ensayos químicos |
Acabado | Dimensiones, microscopía, propiedades mecánicas |
Para conseguir componentes sin defectos que cumplan los requisitos de la aplicación, es necesario un control de calidad y una inspección exhaustivos en todas las fases del proceso MIM.
Análisis de costes
Los siguientes factores determinan la rentabilidad del proceso MIM:
- Herramientas - El utillaje para matrices tiene unos costes iniciales elevados en función de las geometrías de las piezas. Las cavidades múltiples en las herramientas reparten los costes entre volúmenes mayores.
- Puesta en marcha - Importantes costes iniciales de configuración de la máquina y desarrollo del proceso.
- Material - Los metales en polvo representan 10-15% del coste total de la pieza. Elevado para materiales costosos como las aleaciones de titanio.
- Trabajo - Se necesita algo de mano de obra cualificada, pero menos que en el mecanizado CNC. Menor en volúmenes elevados.
- Tratamiento secundario - Puede aumentar significativamente los costes si es necesario un mecanizado o acabado exhaustivo.
- Volumen - Ideal para volúmenes de producción medios y altos, de 10.000 a millones de piezas. Proporciona una ventaja de costes óptima frente a otros procesos de esta gama.
En el cuadro siguiente se exponen los factores de coste indicativos de la fabricación de MIM:
Componente de coste MIM | Detalles |
---|---|
Herramientas | De $5.000 a $100.000+ en función de la complejidad de la pieza |
Puesta en marcha | $10.000 a $50.000 para el desarrollo de procesos |
Materiales | 10-15% del coste de la pieza, mayor para aleaciones costosas |
Trabajo | Menor contribución frente al mecanizado CNC |
Tratamiento secundario | $2 a $20 por pieza en función de las operaciones |
Volumen | Ideal para más de 10.000 piezas, menor coste que otras alternativas |
El MIM ofrece una ventaja económica sobre el mecanizado y la fundición para volúmenes de producción medios y altos, siempre que el procesamiento secundario sea mínimo. El proceso ofrece las mayores ventajas económicas para diseños complejos de varios componentes consolidados en una sola pieza MIM.
Elegir un proveedor o socio de MIM
La selección de un proveedor de MIM competente es clave para la producción rentable de componentes de alta calidad. Algunos criterios para evaluar a los proveedores de MIM:
- Experiencia - Número de años en el negocio y experiencia en MIM. Los operadores veteranos suelen ser más fiables.
- Materiales -Variedad de ofertas de materiales, incluidas las aleaciones clave necesarias. Los nanopolvos mejoran las propiedades.
- Calidad - Programa de calidad sólido y certificaciones como ISO 9001 e ISO 13485. Pruebas de controles de procesos.
- Capacidad de mecanizado - Ofrecer todo el utillaje en la propia empresa permite integrar mejor los costes y reducir los problemas.
- Tratamiento secundario - La disponibilidad de procesos complementarios como el mecanizado y el acabado CNC mejora la comodidad.
- Creación de prototipos - La capacidad de creación rápida de prototipos en MIM reduce los plazos y los costes.
- Competencia en I+D - Gran experiencia en investigación e ingeniería para la innovación de procesos.
Elegir un proveedor establecido con amplias capacidades internas proporciona una solución sólida y sin fisuras para proyectos MIM complejos. La proximidad geográfica también facilita la colaboración y la comunicación.
MIM comparado con otros procesos
MIM frente a mecanizado CNC
- Coste - MIM menor coste en volúmenes medios y altos, CNC rentable en volúmenes bajos
- Diseño - Mayor complejidad y mejor potencial de consolidación con MIM
- Materiales - MIM permite una gama de materiales más amplia, incluidos aceros para herramientas y aleaciones de titanio.
- Velocidad - Mayores índices de producción con MIM, tiempos de ciclo más lentos para el mecanizado CNC
- Residuos - Forma casi neta El MIM tiene menos desperdicio de material que el mecanizado CNC
MIM frente a fundición de metales
- Resolución - Mayor resolución y detalles más precisos gracias al MIM
- Complejidad - Mayor complejidad geométrica gracias al MIM
- Tolerancias - Tolerancias dimensionales mucho más ajustadas que con el MIM
- Coherencia - Propiedades de los materiales y rendimiento más homogéneos con el MIM
- Mecanizado secundario - Normalmente se necesita menos mecanizado secundario para las piezas MIM
MIM frente a impresión 3D
- Coste - En la actualidad, el MIM tiene un coste inferior para la producción de volúmenes medios o superiores
- Materiales - Gama más amplia de aleaciones de alto rendimiento, como aceros para herramientas, disponibles en MIM.
- Tolerancias - MIM permite tolerancias dimensionales más precisas
- Propiedades mecánicas - Propiedades generalmente mejores y más consistentes que los metales impresos en 3D
- Cualificación - El proceso MIM ya está cualificado para aplicaciones aeroespaciales y médicas, a diferencia de la impresión 3D
El MIM ofrece ventajas en complejidad, consistencia y coste frente a otros procesos de fabricación de metales para componentes pequeños de alta precisión fabricados en volúmenes medios o superiores.
Limitaciones y retos del MIM
Algunas de las principales limitaciones y desventajas del proceso MIM son:
- Los elevados costes iniciales de inversión en utillaje impiden la producción de series cortas
- Capacidad de tamaño limitada, no es ideal para piezas de más de 500 gramos
- Geometría restringida debido a la necesidad de descortezar y sinterizar los componentes
- El reto de lograr tolerancias muy ajustadas por debajo de ±0,5%
- No se recomienda para aleaciones exóticas difíciles de sinterizar
- Puede ser necesario un mecanizado secundario para conseguir ajustes y dimensiones críticos.
- Gran experiencia en el proceso necesaria para la prevención de defectos durante el moldeo
- Los costes de capital de la maquinaria MIM pueden ser considerables
Para superar las limitaciones del MIM hay que hacer concesiones en el diseño, los requisitos de tolerancia y las necesidades de procesamiento secundario. El proceso es más adecuado para componentes pequeños, complejos y de alta precisión que para geometrías muy grandes o básicas.
Desarrollos tecnológicos MIM
Entre los avances tecnológicos recientes en el ámbito del MIM que están ampliando las capacidades y la adopción se incluyen:
- Materias primas para nanopolvos - Mejora de la resistencia y la microestructura sinterizadas
- Utillaje rápido - Reducción de costes de moldes y plazos de entrega mediante insertos impresos en 3D
- Chorro aglomerante - Permitir la fabricación "imprimir y luego sinterizar" en la impresión 3D de metales
- MIM de titanio - Desarrollo de componentes de titanio rentables
- Inyección a baja presión - Para piezas MIM más grandes con tensiones de utillaje reducidas
- MIM de cerámica - Ampliación a cerámicas técnicas/estructurales más allá de la alúmina
- Integración de la Industria 4.0 - Automatización y optimización del control de calidad
La innovación constante en el proceso MIM está ayudando a superar limitaciones, ampliar las capacidades de los materiales y extender las aplicaciones a nuevos sectores. De este modo, el MIM puede competir eficazmente como tecnología de fabricación de componentes metálicos de precisión.
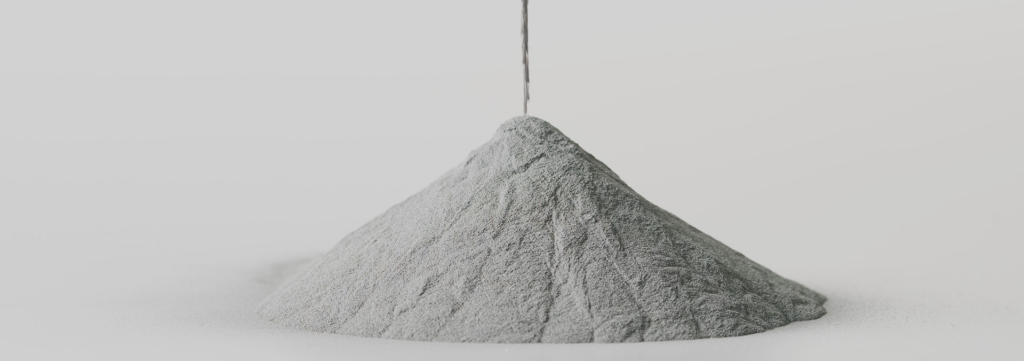
Preguntas más frecuentes
He aquí las respuestas a algunas preguntas frecuentes sobre el proceso de moldeo por inyección de metales:
P: ¿Qué tipos de metales pueden utilizarse en MIM?
R: La tecnología MIM permite procesar una amplia gama de metales y aleaciones, como aceros inoxidables, aceros para herramientas, aleaciones magnéticas, aleaciones de titanio, aleaciones pesadas de tungsteno y aleaciones de cobre. Los materiales más comunes son el acero inoxidable 316L y 17-4PH, el acero para herramientas H13 y el titanio Ti-6Al-4V.
P: ¿Qué tamaño de componentes pueden fabricarse mediante MIM?
R: El tamaño ideal del MIM oscila entre 0,5 y 500 gramos. Es posible fabricar piezas más pequeñas y más grandes, pero puede no resultar económico. Las piezas en miniatura de menos de 0,5 gramos pueden plantear problemas de manipulación y procesamiento secundario. Las piezas más grandes, por encima de 500 gramos, requieren mayores esfuerzos de utillaje y tiempos de ciclo más largos.
P: ¿Qué precisión dimensional y tolerancias son posibles con el MIM?
R: El MIM puede conseguir tolerancias dimensionales muy buenas de hasta ±0,1% de las dimensiones. Sin embargo, ±0,5% es más típico para componentes de tolerancia media. Las tolerancias inferiores a ±0,005 pulgadas (+/- 0,127 mm) requieren un mecanizado secundario. Hay que tener en cuenta la contracción por sinterización.
P: ¿En qué se diferencia el MIM del moldeo por inyección de plástico?
R: El proceso MIM se basa en el moldeo por inyección de plástico, pero utiliza materias primas metálicas en polvo en lugar de resinas plásticas. El MIM permite fabricar componentes metálicos complejos de alta resistencia mediante este proceso adaptado de moldeo por inyección con un paso adicional de sinterización.
P: ¿Qué acabados superficiales pueden producirse en las piezas MIM?
R: El MIM es capaz de producir acabados superficiales finos de hasta 0,5 micras Ra, comparables a las superficies mecanizadas. Factores como el sistema de aglutinante, el acabado de la herramienta de moldeo, la geometría y el procesamiento secundario determinan la rugosidad superficial final alcanzable.
P: ¿Qué tipos de geometrías complejas puede fabricar el MIM?
R: Las geometrías complejas con paredes finas, ángulos de desmoldeo negativos, entalladuras, cavidades ciegas y formas poco convencionales pueden moldearse fácilmente con MIM, ya que la mezcla de polvo y aglutinante fluye como un líquido en el molde.
P: ¿Es bueno el MIM para fabricar prototipos?
R: El MIM no es ideal para la creación de prototipos debido a los elevados costes de las herramientas y los plazos de entrega. Otros procesos como el mecanizado CNC, la impresión 3D o el moldeo por inyección de aluminio son más adecuados para piezas prototipo de bajo volumen antes de comprometerse con el mecanizado MIM.
conocer más procesos de impresión 3D
Frequently Asked Questions (Supplemental)
1) What feedstock solids loading is optimal in the MIM Process?
- Typically 58–64 vol% metal powder in the binder. Higher loading reduces shrinkage and distortion but increases viscosity; tune via capillary rheometry.
2) How do I control shrinkage and dimensional scatter in sintering?
- Use consistent PSD (D50 ≈ 12–20 μm), spherical morphology, tight O/N/H limits, uniform debind, and sinter setters/fixtures. Apply SPC on green density and use master shrinkage curves per alloy.
3) Can MIM achieve medical and aerospace qualifications?
- Yes. Implement ISO 13485 or AS9100 QMS, material traceability, validated debind/sinter cycles, and biocompatibility testing (ISO 10993) for relevant alloys; report properties per ASTM F2885 and F3122.
4) When is HIP recommended for MIM parts?
- For fatigue‑critical, leak‑tight, or thick‑section components (e.g., 17‑4PH, Ti‑6Al‑4V). HIP raises density to ≥99.7%, reducing internal porosity; follow with appropriate aging/anneal.
5) What are common root causes of MIM defects and how to mitigate?
- Jetting/short shots: adjust gate, viscosity, mold temps. Blisters/cracks: incomplete debind—extend solvent or thermal stage. Warpage: unbalanced cooling or nonuniform green density—optimize tooling, packing, and fixtures.
2025 Industry Trends and Data
- Digital powder passports: Chemistry, PSD, O/N/H, apparent/tap density, and lot history are now standard in RFQs, reducing incoming variability.
- Micro‑MIM growth: Wearables and micro‑mechanisms drive use of ultra‑fine powders (D50 5–10 μm) with low‑viscosity binders and precision tooling vents.
- Sustainability focus: Solvent recovery loops, lower‑energy sintering profiles, and recycled powder content disclosures (15–30%) gain traction.
- In‑process analytics: Cavity pressure/temperature sensors and inline viscosity checks cut scrap by double digits.
- Hybrid routes: Print‑then‑sinter (binder jet) and MIM share furnaces/inspection cells for mixed‑technology factories.
KPI (MIM Process Performance), 2025 | 2023 Baseline | 2025 Typical/Target | Why it matters | Sources/Notes |
---|---|---|---|---|
Solids loading (vol%) | 56–62 | 58–64 | Shrinkage control, strength | Vendor guides; rheometry |
Hausner ratio (–) | 1.22–1.28 | 1.12–1.20 | Flow stability | ASTM B212/B213 |
Oxygen in 316L MIM powder (wt%) | 0.25–0.45 | 0.15–0.30 | Corrosion, density | ASTM E1019 |
Green density Cpk | 1.1–1.3 | ≥1.5 | Dimensional capability | Plant SPC |
Post‑HIP density (%) | 99.5–99.7 | 99.7–99.9 | Fatigue/leak‑tightness | OEM data |
Scrap reduction with cavity sensing | - | 10-20% | Yield improvement | Vendor app notes |
Recycled content disclosed (%) | Limitado | 15–30 | ESG, cost | EPD/LCA reports |
Standards and references:
- ASTM F2885 (MIM components), ASTM B212/B213/B214/B822 (density/flow/PSD), ASTM E1019 (O/N/H), ASTM F3122 (mechanical property reporting): https://www.astm.org
- ISO 22068 (MIM powders/components), ISO 13485 (medical QMS): https://www.iso.org
- EPMA MIM Guide and Design for MIM: https://www.epma.com
- ASM Handbook, Powder Metallurgy and MIM: https://dl.asminternational.org
Latest Research Cases
Case Study 1: Micro‑MIM 17‑4PH Latching Mechanism with Cavity Pressure Control (2025)
- Background: A wearable OEM required sub‑2 mm latches with tight tolerances and high fatigue strength.
- Solution: Spherical 17‑4PH powder (D50 ≈ 9 μm, O = 0.18 wt%); low‑viscosity binder; multi‑cavity mold with cavity pressure sensors; two‑step debind; vacuum sinter + H900 aging; optional HIP.
- Results: Post‑HIP density 99.85%; dimensional Cpk 1.7 on critical features; fatigue life +28% vs. 2023 baseline; scrap −19%.
Case Study 2: Solvent‑Recovery Debind and Low‑Energy Sintering of 316L MIM Surgical Components (2024)
- Background: A medical supplier targeted ESG goals while maintaining corrosion resistance.
- Solution: Closed‑loop solvent debind with >95% solvent recovery; optimized ramp‑hold sintering profile in H2 to limit grain growth; passivation per ASTM A967.
- Results: Energy use −14% per kg; density 98.8–99.2%; pitting potential improved 10% vs. prior cycle; annual solvent purchases −60%.
Expert Opinions
- Prof. Randall M. German, Powder Metallurgy Scholar and Author
- Viewpoint: “In the MIM Process, packing—set by powder PSD and solids loading—drives shrinkage predictability more than marginal sintering tweaks.”
- Dr. Martina Zimmermann, Head of Additive Materials, Fraunhofer IWM
- Viewpoint: “Lot‑level powder passports and in‑mold sensing are now essential for regulated sectors, cutting qualification time and scrap.”
- Dr. Paul J. Davies, EPMA MIM Expert Group
- Viewpoint: “Micro‑MIM success hinges on ultra‑fine powders with tight oxygen control and tooling vent design to prevent binder‑rich defects.”
Affiliation links:
- Fraunhofer IWM: https://www.iwm.fraunhofer.de
- EPMA: https://www.epma.com
- ASM International: https://www.asminternational.org
Practical Tools/Resources
- QC/Standards: ASTM F2885, ISO 22068, ASTM B212/B213/B214/B822, ASTM E1019
- Metrology: LECO inert‑gas fusion (https://www.leco.com); laser diffraction PSD; helium pycnometry (ASTM B923); CT for internal defects; surface profilometry
- Process control: Capillary rheometers; cavity pressure/temperature sensors; SPC templates for shrinkage and dimensions
- Design: EPMA Design for MIM guide; MPIF standards (https://www.mpif.org); ASM Handbook MIM chapters
- Costing/DFM: aPriori for MIM cost models; vendor DFM checklists for gate/runner, venting, and ejection
Last updated: 2025-08-22
Changelog: Added 5 supplemental FAQs; inserted 2025 KPI table and trend notes; included two case studies (micro‑MIM 17‑4PH latch; ESG‑focused 316L flow); added expert viewpoints with affiliations; compiled standards, metrology, process control, and design resources for the MIM Process.
Next review date & triggers: 2026-02-01 or earlier if ASTM/ISO standards update, major suppliers change O/N/H or PSD specs, or new datasets on micro‑MIM capability and solvent‑recovery debinding are published.