Polvo de acero de baja aleaciónLa pulvimetalurgia, piedra angular de la industria pulvimetalúrgica, ha revolucionado la fabricación de piezas metálicas complejas y de alto rendimiento. Pero, ¿se ha preguntado alguna vez cómo se forman estos diminutos gránulos metálicos? Abróchese el cinturón, porque vamos a adentrarnos en el mundo de los métodos de producción de polvo de acero de baja aleación, explorando sus complejidades y las propiedades únicas que confieren al producto final.
La esencia del polvo de acero de baja aleación
Antes de adentrarnos en los métodos de producción, establezcamos una imagen clara de lo que es el polvo de acero de baja aleación. Imaginemos que tomamos acero normal y lo descomponemos en partículas microscópicas que fluyen libremente. Estas partículas, que suelen tener entre 10 y 150 micrómetros de diámetro, tienen una composición ligeramente diferente a la de sus homólogas a granel. La magia reside en la parte de "baja aleación". Añadiendo cuidadosamente pequeñas cantidades de elementos como manganeso, cromo, níquel o molibdeno, los fabricantes pueden adaptar las propiedades mecánicas del polvo a aplicaciones específicas.
Este control preciso de la composición abre un tesoro de ventajas. El polvo de acero de baja aleación ofrece:
- Resistencia y dureza: La adición de elementos de aleación aumenta significativamente la resistencia y la dureza del producto final en comparación con el polvo de hierro puro.
- Maquinabilidad: A diferencia del acero conformado tradicionalmente, las piezas fabricadas con polvo de acero de baja aleación presentan una excelente maquinabilidad, lo que permite formas y características intrincadas.
- Complejidad de la forma: La naturaleza fluida del polvo permite crear geometrías complejas antes inimaginables con los métodos convencionales.
- Fabricación en forma próxima a la red: La PM permite fabricar piezas cercanas a sus dimensiones finales, minimizando el desperdicio de material y las necesidades de mecanizado.
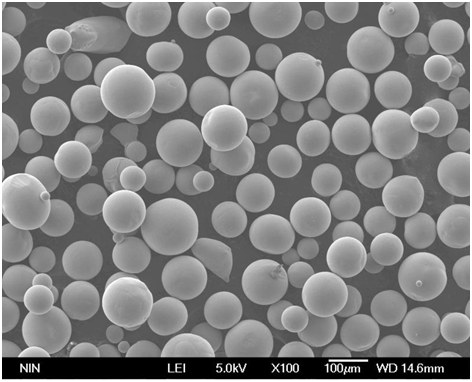
El centro neurálgico de la producción: Desvelando los métodos
Ahora vamos a desvelar los secretos que se esconden tras la producción de estas poderosas maravillas metálicas. He aquí los cuatro métodos principales empleados para crear polvo de acero de baja aleación:
1. El método de reducción: Transformación de óxidos en gemas metálicas
Imagine un cofre del tesoro oculto lleno de óxido de hierro, el primo oxidado del acero. El método de reducción abre este tesoro utilizando un agente reductor, como el hidrógeno o el monóxido de carbono, para eliminar el oxígeno del óxido de hierro y dejar partículas de hierro puro.
Pros:
- Tecnología madura y consolidada.
- Rentable para la producción a gran escala.
Contras:
- Control limitado de la composición final del polvo.
- Puede dar lugar a formas y tamaños de partículas irregulares.
2. El método de producción por atomización: Del metal fundido a las maravillas microscópicas
Piense en acero fundido cayendo y solidificándose en una lluvia de diminutas gotitas metálicas. Esa es la esencia de la atomización. En este método, el acero fundido aleado con los elementos deseados se vierte a través de una corriente de gas o agua a alta presión. El rápido enfriamiento rompe el metal fundido en un fino polvo de forma casi esférica.
Existen dos subtipos principales de atomización:
- Atomización de gases: Emplea gases inertes como nitrógeno o argón para un proceso más limpio y controlado, ideal para aplicaciones de alto rendimiento.
Pros:
- Excelente control del tamaño y la forma del polvo.
- Produce polvo esférico de alta calidad.
Contras:
- Más caro que el método de reducción.
- Atomización del agua: Utiliza agua como medio de atomización, lo que la convierte en una opción rentable. Sin embargo, se utiliza principalmente para aplicaciones menos críticas debido a posibles problemas de oxidación.
Pros:
- Menor coste de producción en comparación con la atomización con gas.
Contras:
- Mayor riesgo de oxidación en el polvo final.
- Menor control sobre el tamaño y la morfología del polvo.
3. Método de producción de la aleación mecánica: Agitación de un cóctel metálico
Imagine un molino de bolas de alta energía que actúa como una coctelera para polvos metálicos. Esa es la esencia de la aleación mecánica. En este método, los polvos prealeados o elementales se introducen en un entorno de molienda de alta energía. Las intensas colisiones entre las bolas y las partículas de polvo provocan fracturas, soldaduras y difusión, creando finalmente un polvo uniforme con la composición de aleación deseada.
Pros:
- Permite crear composiciones de aleación únicas y complejas.
- Excelente control de la microestructura y las propiedades.
Contras:
- Elevado consumo de energía y desgaste del equipo de molienda.
- Puede introducir contaminación de los medios de molienda.
4. Método de producción química: Una receta precisa para la perfección del polvo
Piense en preparar una poción con los ingredientes adecuados para lograr un resultado específico. El método de producción química se basa en un principio similar. En este caso, los compuestos precursores que contienen los elementos deseados se someten a reacciones químicas que, en última instancia, conducen a la formación de la sustancia deseada. polvo de acero de baja aleación.
Pros:
- Polvo muy puro y homogéneo con un control preciso de la composición.
Contras:
- Proceso complejo y a menudo costoso.
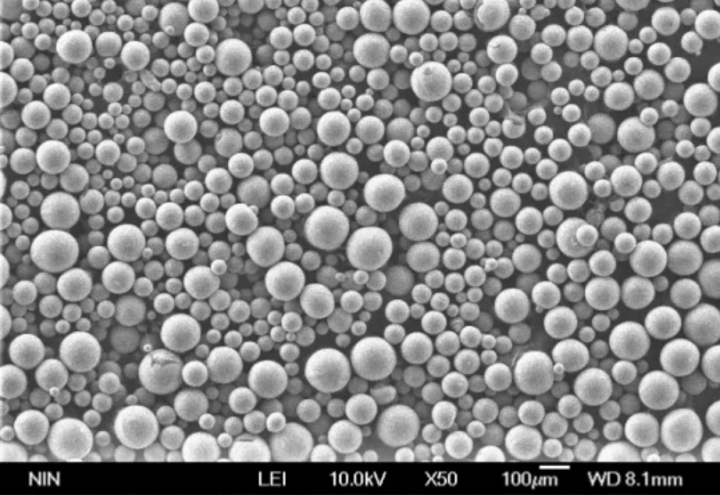
Modelos y aplicaciones específicas del polvo metálico
El mundo de polvo de acero de baja aleación cuenta con una amplia gama de opciones, cada una de ellas adaptada a aplicaciones específicas. Aquí tienes diez modelos destacados para abrirte el apetito:
1. Polvo de acero de baja aleación AISI 4140: Un versátil caballo de batalla conocido por su excelente equilibrio entre resistencia, tenacidad y mecanizabilidad. Se utiliza habitualmente en engranajes, ejes, fijaciones y otros componentes estructurales.
Pros:
- Buena combinación de resistencia, tenacidad y maquinabilidad.
- Material bien establecido con un historial probado.
Contras:
- No es ideal para aplicaciones de alta temperatura.
2. Polvo de acero de baja aleación AISI 4620: Ofrece una templabilidad superior a la del 4140, lo que lo convierte en la mejor opción para piezas que requieren una gran resistencia al desgaste. Piense en engranajes, ruedas dentadas y cojinetes.
Pros:
- Excelente templabilidad y resistencia al desgaste.
- Responde bien a los procesos de tratamiento térmico.
Contras:
- Menor ductilidad en comparación con el 4140.
3. Polvo de acero de baja aleación de níquel-cromo-molibdeno (Ni-Cr-Mo): Esta maravilla con infusión de cromo presenta una excepcional resistencia a la fluencia a temperaturas elevadas. Los componentes de generación de energía, las piezas de hornos y los recipientes a presión se benefician de su resistencia a las altas temperaturas.
Pros:
- Resistencia superior a la fluencia para aplicaciones de alta temperatura.
- Ofrece una buena resistencia a la oxidación.
Contras:
- Puede requerir técnicas de procesamiento específicas debido a la composición de su aleación.
4. Polvo de acero de baja aleación de cobre-cromo (Cu-Cr): Conocida por su mayor capacidad de mecanizado, esta maravilla con infusión de cobre permite ciclos de producción más rápidos y tolerancias más estrictas. Piense en componentes complejos de automoción, fijaciones y piezas electrónicas.
Pros:
- Excelente mecanizabilidad para la producción a alta velocidad.
- Ofrece una buena resistencia a la corrosión.
Contras:
- Menor resistencia en comparación con otras opciones de polvo de acero de baja aleación.
5. Polvo de acero inoxidable 316L de baja aleación: El rey de la resistencia a la corrosión, este polvo cuenta con las excepcionales propiedades del acero inoxidable 316L en un formato apto para PM. Ideal para aplicaciones que exigen resistencia a entornos agresivos, como equipos de procesamiento químico y componentes marinos.
Pros:
- Excelente resistencia a la corrosión para entornos exigentes.
- Biocompatible, lo que la hace adecuada para aplicaciones médicas.
Contras:
- Menor resistencia en comparación con algunas opciones de acero de baja aleación.
- Mayor coste debido a la presencia de cromo y níquel.
6. Polvo de acero de baja aleación AISI 9310: Esta maravilla de alta aleación ofrece una templabilidad y resistencia excepcionales, lo que la hace perfecta para componentes aeroespaciales, engranajes y herramientas de alto rendimiento.
Pros:
- Resistencia y templabilidad excepcionales.
- Excelente resistencia a la fatiga.
Contras:
- Requiere un control estricto de los procesos de tratamiento térmico.
- Menor ductilidad en comparación con otras opciones.
7. Polvo de acero de baja aleación con propiedades magnéticas blandas: Diseñados para una permeabilidad magnética óptima, estos polvos son los componentes básicos de transformadores, inductores y otros componentes electromagnéticos.
Pros:
- Adaptado para propiedades magnéticas específicas.
- Permite crear geometrías de núcleo magnético complejas.
Contras:
- Puede tener limitaciones de resistencia mecánica en comparación con otras opciones.
8. Polvo de acero de baja aleación para aplicaciones de alta densidad: Algunos polvos están diseñados específicamente para alcanzar una densidad cercana a la teórica en la pieza final de PM. Esto se traduce en propiedades mecánicas superiores para aplicaciones críticas como engranajes y cojinetes.
Pros:
- Alcanza una alta densidad para mejorar el rendimiento mecánico.
- Ofrece una buena estabilidad dimensional.
Contras:
- Puede requerir técnicas de procesado específicas para lograr una densificación completa.
9. Polvo de acero de baja aleación para fabricación aditiva: El mundo de la impresión 3D ha adoptado el poder de los PM. Estos polvos están optimizados para procesos de fabricación aditiva como el chorro de aglutinante y el sinterizado láser, lo que permite crear componentes complejos con formas cercanas a la red.
Pros:
- Adaptado a las tecnologías de fabricación aditiva.
- Permite crear geometrías complejas.
Contras:
- Puede requerir técnicas específicas de postratamiento para obtener propiedades óptimas.
10. Polvos de acero de baja aleación a medida: La belleza de la PM reside en su potencial de personalización. Los fabricantes pueden crear composiciones de polvo únicas para satisfacer las necesidades específicas de una aplicación. Esto abre las puertas a soluciones innovadoras en diversas industrias.
Pros:
- Control preciso de la composición del polvo para obtener propiedades a medida.
- Permite desarrollar soluciones específicas para cada aplicación.
Contras:
- El desarrollo y la cualificación de polvos personalizados puede llevar mucho tiempo y resultar caro.
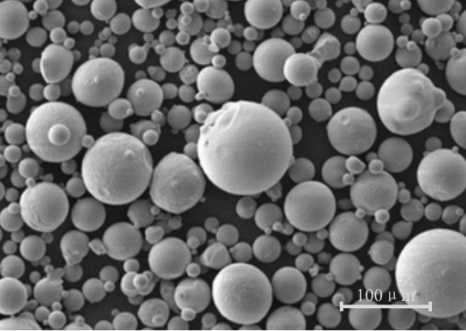
Ventajas y limitaciones de Polvo de acero de baja aleación
Sopesar los pros y los contras: una perspectiva equilibrada
El polvo de acero de baja aleación ofrece un atractivo paquete de ventajas, pero, como cualquier material, tiene sus propias limitaciones. Profundicemos en ambas caras de la moneda para ayudarle a tomar decisiones con conocimiento de causa.
Ventajas:
- Propiedades mecánicas superiores: El polvo de acero de baja aleación ofrece mayor resistencia, dureza y resistencia al desgaste que el polvo de hierro puro. Esto se traduce en piezas que pueden soportar aplicaciones exigentes.
- Flexibilidad de diseño: La naturaleza fluida del polvo permite crear geometrías complejas que serían difíciles o imposibles con los métodos de fabricación tradicionales. Esto abre las puertas al diseño de productos innovadores.
- Fabricación en forma próxima a la red: La PM permite fabricar piezas cercanas a sus dimensiones finales, lo que reduce significativamente el desperdicio de material y las necesidades de mecanizado. Esto se traduce en un ahorro de costes y una mayor eficiencia de la producción.
- Eficiencia del material: El polvo de acero de baja aleación ofrece un excelente aprovechamiento del material. A diferencia de los métodos tradicionales que generan chatarra, el PM permite una utilización casi completa del material de partida.
- Precisión dimensional: Los procesos de PM permiten fabricar piezas con tolerancias estrictas, lo que reduce al mínimo la necesidad de realizar extensos pasos de postprocesado.
- Propiedades a medida: Controlando cuidadosamente los elementos de aleación, los fabricantes pueden crear polvos con propiedades específicamente adaptadas a la aplicación de destino.
Limitaciones:
- Coste de producción: En comparación con el procesamiento tradicional de metales a granel, la PM puede ser una propuesta más costosa, especialmente para series de producción de gran volumen. A ello contribuyen el coste del propio polvo y los equipos especializados necesarios.
- Limitaciones del tamaño de las piezas: La tecnología actual de PM tiene limitaciones en cuanto al tamaño de las piezas que pueden producirse de forma económica. Aunque se pueden lograr formas intrincadas, los componentes a gran escala podrían ser más adecuados para los métodos tradicionales.
- Segregación del polvo: Durante la manipulación y el almacenamiento, las partículas de polvo más finas pueden separarse de las más gruesas. Esto puede provocar incoherencias en las propiedades finales de la pieza y requiere técnicas de manipulación cuidadosas.
- Complejidad del proceso: La PM implica una serie de pasos, desde la producción de polvo hasta la compactación y sinterización. Cada paso debe controlarse con precisión para conseguir las propiedades deseadas en la pieza final.
- Requisitos de postprocesamiento: Dependiendo de la aplicación, las piezas PM pueden requerir etapas adicionales de postprocesado, como tratamiento térmico o mecanizado, para lograr un rendimiento óptimo.
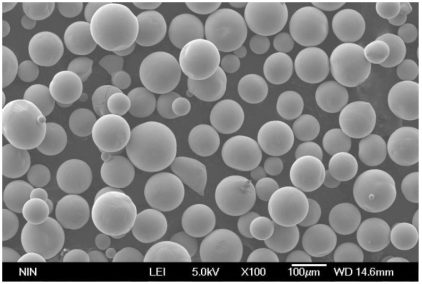
Preguntas más frecuentes
Aquí respondemos a algunas preguntas frecuentes para arrojar más luz sobre el mundo del polvo de acero de baja aleación:
P: ¿Cuáles son los tamaños típicos de las partículas de polvo de acero de baja aleación?
R: Las partículas de polvo de acero de baja aleación suelen tener entre 10 y 150 micrómetros de diámetro. Sin embargo, la distribución específica del tamaño puede variar en función de la aplicación deseada y del método de producción.
P: ¿Qué resistencia tienen las piezas fabricadas con polvo de acero de baja aleación?
R: La resistencia de las piezas fabricadas con polvo de acero de baja aleación depende de la composición específica del polvo y de los parámetros de procesamiento. No obstante, pueden alcanzar resistencias a la tracción superiores a 1000 MPa, lo que las hace adecuadas para aplicaciones exigentes.
P: ¿Se pueden reciclar las piezas de polvo de acero de baja aleación?
R: Sí, una ventaja significativa de la PM es su reciclabilidad inherente. Las piezas de desecho o el polvo sobrante pueden reintroducirse en el ciclo de producción, minimizando los residuos y fomentando la sostenibilidad.
P: ¿Cuáles son algunas de las nuevas aplicaciones del polvo de acero de baja aleación?
R: El futuro depara un inmenso potencial para el polvo de acero de baja aleación. Ámbitos como la fabricación aditiva, el moldeo por inyección de metales (MIM) y los implantes biocompatibles están experimentando interesantes avances gracias a las propiedades únicas del PM.
En conclusión
El polvo de acero de baja aleación es una propuesta atractiva para una amplia gama de aplicaciones. Si conoce sus métodos de producción, propiedades y limitaciones, podrá tomar decisiones informadas sobre su idoneidad para sus necesidades específicas. Desde su flexibilidad de diseño hasta su capacidad de fabricación de formas casi netas, el polvo de acero de baja aleación sigue revolucionando la forma en que fabricamos piezas metálicas complejas y de alto rendimiento. A medida que avanza la tecnología y se profundiza en la investigación, el futuro de este versátil material promete posibilidades aún más brillantes.