Introducción
En el mundo de la fabricación, los avances tecnológicos siguen ampliando los límites de lo posible. Una de las innovaciones que más atención ha suscitado es la tecnología de moldeo por inyección de metal (MIM). Tecnología MIM combina la versatilidad del moldeo por inyección de plástico con la durabilidad y resistencia del metal para crear piezas complejas y precisas. Este artículo profundiza en los entresijos de la tecnología MIM, explorando sus principios de funcionamiento, ventajas, aplicaciones, limitaciones y perspectivas de futuro.
¿Qué es la tecnología MIM?
La tecnología MIM, también conocida como moldeo por inyección de metal, es un proceso de fabricación que permite producir piezas metálicas complejas con gran precisión y exactitud. Consiste en combinar polvos metálicos finos con un material aglutinante termoplástico para crear una materia prima. A continuación, esta materia prima se inyecta en la cavidad de un molde, de forma similar al moldeo por inyección de plástico. La pieza resultante se somete a una serie de pasos de postprocesado, como el desligado y la sinterización, para eliminar el aglutinante y fusionar las partículas metálicas, respectivamente.
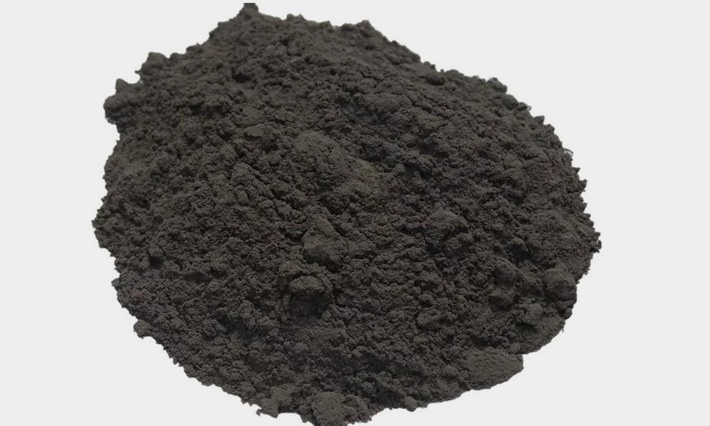
¿Cómo funciona la tecnología MIM?
Preparación de la materia prima
El primer paso del proceso MIM es la preparación de la materia prima. Se mezclan polvos metálicos finos, normalmente de un tamaño inferior a 20 micrómetros, con un material aglutinante termoplástico. Esta mezcla se somete a un proceso de amasado o extrusión para garantizar su homogeneidad. La materia prima resultante, con una elevada carga metálica de unos 60-70%, está lista para el moldeo.
Moldeo
Una vez preparada la materia prima, se inyecta en la cavidad de un molde utilizando un equipo de moldeo especializado. El molde está diseñado para reproducir la forma deseada de la pieza final. A alta presión, la materia prima llena el molde y adopta su forma. Tras enfriarse, se abre el molde y se retira la pieza verde, que aún contiene el aglutinante.
Desbobinado
La pieza verde obtenida del proceso de moldeo contiene una cantidad significativa de material aglutinante. Para eliminar el aglutinante, la pieza verde se somete a un proceso de desaglomerado. Esto puede hacerse mediante métodos térmicos o con disolventes. El desaglomerado térmico consiste en someter la pieza a un calentamiento cuidadosamente controlado para eliminar gradualmente el aglutinante, dejando tras de sí una estructura porosa denominada pieza marrón.
Sinterización
A continuación, la pieza marrón se somete a un proceso de sinterización. La sinterización consiste en calentar la pieza a una temperatura inferior a su punto de fusión, pero lo suficientemente alta como para provocar la difusión y la unión de las partículas metálicas. A medida que las partículas se fusionan, la pieza se contrae y densifica, lo que da lugar a un componente metálico final totalmente denso con las propiedades mecánicas deseadas.
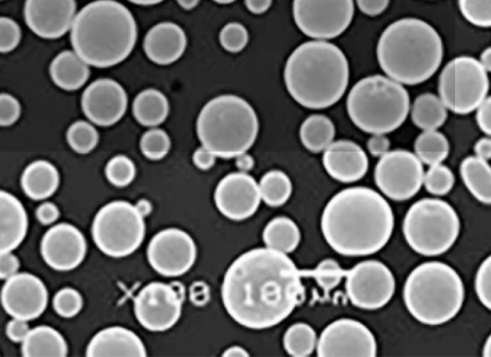
Ventajas de la tecnología MIM
La tecnología MIM ofrece varias ventajas sobre los métodos de fabricación tradicionales, lo que la convierte en una opción atractiva para diversas industrias. Algunas de las principales ventajas son:
Geometrías complejas
La tecnología MIM permite fabricar piezas con geometrías complejas, incluidos rasgos internos intrincados, rebajes y detalles finos. Elimina la necesidad de costosas operaciones secundarias, como el mecanizado o el montaje, que suelen ser necesarias con los métodos de fabricación tradicionales.
Versatilidad de materiales
La tecnología MIM admite una amplia gama de materiales, como acero inoxidable, aleaciones de titanio, aleaciones de cobalto-cromo y otros. Esta versatilidad permite a los fabricantes elegir el material óptimo para su aplicación específica, teniendo en cuenta factores como la solidez, la resistencia a la corrosión y la biocompatibilidad.
Eficiencia de costes
Al combinar varios pasos de fabricación en un único proceso, la tecnología MIM permite ahorrar costes en términos de reducción de mano de obra, ciclos de producción más cortos y mínimo desperdicio de material. Elimina la necesidad de costosas herramientas que suelen asociarse a otras técnicas de fabricación.
Alta precisión y exactitud
La tecnología MIM permite fabricar piezas con tolerancias estrechas y gran precisión dimensional. El uso de moldes garantiza la uniformidad y la repetibilidad, lo que se traduce en componentes fiables y precisos.
Acabado superficial
Las piezas MIM tienen un excelente acabado superficial nada más salir del proceso de moldeo, lo que reduce la necesidad de operaciones adicionales de pulido o acabado. Esto ahorra tiempo y costes a la hora de conseguir la calidad superficial deseada.
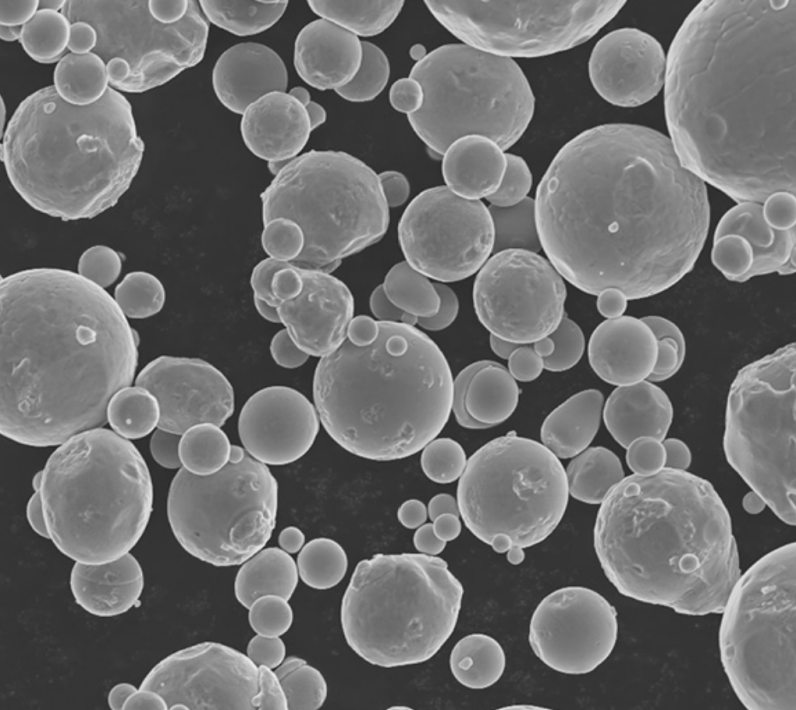
Aplicaciones de la tecnología MIM
La versatilidad y las capacidades de la tecnología MIM la hacen aplicable en diversas industrias. Algunas aplicaciones destacadas son:
Industria del automóvil
La tecnología MIM se utiliza ampliamente en la industria del automóvil para fabricar componentes como engranajes de transmisión, boquillas de inyección de combustible y sensores. Su capacidad para fabricar formas complejas y mantener la precisión dimensional la convierte en la opción ideal para piezas de automoción con requisitos exigentes.
Médico y dental
En los campos médico y odontológico, la tecnología MIM se emplea para fabricar instrumentos quirúrgicos, brackets de ortodoncia, implantes dentales y otros componentes críticos. La capacidad de producir diseños intrincados y personalizados con materiales biocompatibles es ventajosa para estas aplicaciones.
Electrónica
La tecnología MIM desempeña un papel vital en la industria electrónica al producir conectores, sensores y sistemas microelectromecánicos (MEMS). El proceso de fabricación, preciso y repetible, garantiza componentes de alta calidad que satisfacen las estrictas exigencias del mercado de la electrónica.
Armas de fuego
La tecnología MIM se utiliza ampliamente en la fabricación de armas de fuego para producir componentes como gatillos, martillos y piezas de cargadores. Este proceso permite producir de forma rentable piezas complejas de armas de fuego con una calidad y un rendimiento constantes.
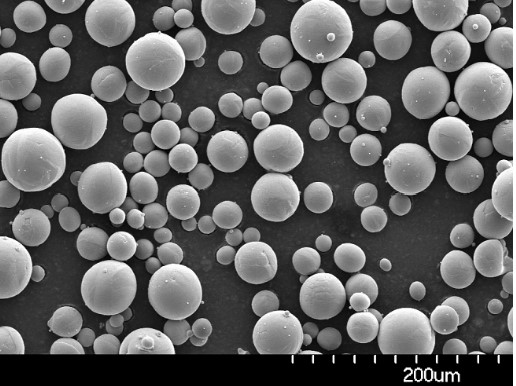
Limitaciones y retos de la tecnología MIM
Aunque la tecnología MIM ofrece numerosas ventajas, también se enfrenta a ciertas limitaciones y retos. Entre ellos cabe citar:
Selección de materiales
La disponibilidad de materias primas adecuadas es crucial para el éxito de la producción MIM. No todos los metales pueden procesarse mediante MIM, y las opciones son algo limitadas en comparación con los métodos de fabricación tradicionales.
Limitaciones de tamaño
La tecnología MIM es más adecuada para piezas pequeñas y medianas. A medida que aumenta el tamaño de la pieza, los problemas relacionados con la contracción y la distorsión se hacen más prominentes, lo que plantea retos a la hora de mantener la precisión dimensional.
Requisitos de postprocesamiento
Las etapas de desaglomerado y sinterización requieren un cuidadoso control de parámetros como la temperatura, el tiempo y la atmósfera. Estas etapas de postprocesado pueden llevar mucho tiempo y añadir complejidad al proceso de producción global.
Coste del equipo
La inversión inicial en equipos MIM puede ser considerable, sobre todo para las pequeñas y medianas empresas. Los costes asociados a los moldes, hornos de descortezado y hornos de sinterización deben considerarse detenidamente antes de implantar la tecnología MIM.
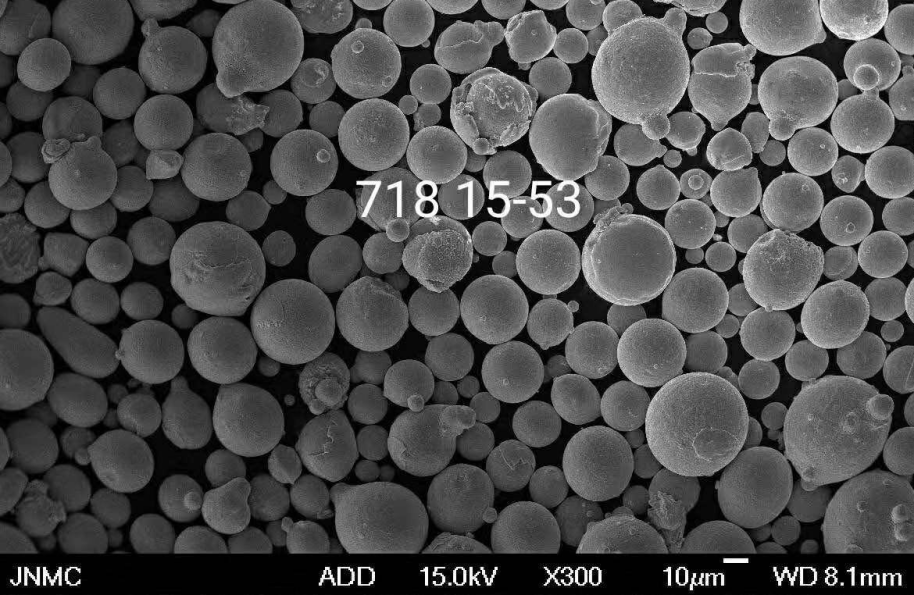
Perspectivas de futuro de la tecnología MIM
El futuro de la tecnología MIM parece prometedor, ya que los esfuerzos de investigación y desarrollo en curso pretenden abordar las limitaciones y retos de la tecnología actual. Algunas de las áreas de interés para el futuro de la tecnología MIM son:
- Expansión de materiales: Los investigadores están estudiando nuevos materiales y sistemas de aleación que puedan procesarse mediante MIM. Esto ampliará la gama de aplicaciones e industrias que pueden beneficiarse de la tecnología MIM.
- Escalado de tamaño: Se están realizando esfuerzos para optimizar el proceso MIM para piezas más grandes. Mediante el perfeccionamiento de los procesos de desbobinado y sinterización y el desarrollo de innovadores diseños de moldes, pueden superarse las limitaciones de tamaño del MIM, permitiendo la producción de componentes de mayor tamaño.
- Optimización del proceso: La investigación en curso tiene como objetivo mejorar la eficiencia y el control de cada etapa del proceso MIM. Esto incluye avances en la preparación de la materia prima, técnicas de moldeo y métodos de postprocesado, lo que se traduce en una mejora de la calidad de las piezas y una reducción del tiempo de producción.
- Reducción de costes: A medida que se generalice la adopción de la tecnología MIM y aumente la demanda de componentes MIM, las economías de escala reducirán los costes generales asociados a la producción MIM. Esto hará que la tecnología MIM sea más accesible a una gama más amplia de industrias y fabricantes.
- Integración con otras tecnologías: La tecnología MIM puede combinarse con otros procesos de fabricación aditiva, como la impresión 3D y la deposición de metales, para crear soluciones de fabricación híbridas. Estos enfoques integrados tienen el potencial de ampliar aún más las posibilidades y capacidades de diseño de la tecnología MIM.
En conclusión, la tecnología MIM está revolucionando la industria manufacturera al permitir la producción de piezas metálicas complejas con gran precisión y eficacia. Sus ventajas, como la capacidad de producir geometrías intrincadas, la versatilidad de materiales, la rentabilidad y el excelente acabado superficial, la convierten en la opción preferida para diversos sectores, como el de la automoción, la medicina, la electrónica y las armas de fuego. Aunque la tecnología MIM se enfrenta a ciertas limitaciones y desafíos, los esfuerzos de investigación y desarrollo en curso están allanando el camino para futuros avances y una adopción más amplia. Con la innovación continua, se espera que la tecnología MIM desempeñe un papel cada vez más importante en el panorama de la fabricación.
preguntas frecuentes
¿Qué materiales pueden utilizarse en la tecnología MIM? La tecnología MIM admite una amplia gama de materiales, como acero inoxidable, aleaciones de titanio, aleaciones de cobalto-cromo, etc.
¿Es adecuada la tecnología MIM para la producción a gran escala? Aunque la tecnología MIM es más adecuada para piezas pequeñas y medianas, las investigaciones en curso pretenden optimizar el proceso para componentes de mayor tamaño.
¿Son las piezas MIM tan resistentes como las de fabricación tradicional? Sí, las piezas MIM presentan una resistencia comparable a la de las piezas fabricadas tradicionalmente, gracias a la estructura metálica densa y uniforme que se consigue mediante el proceso de sinterización.
¿Cómo se compara el MIM con otros procesos de fabricación aditiva? El MIM ofrece claras ventajas, como una gran precisión dimensional y acabado superficial, que lo hacen adecuado para producir piezas metálicas complejas. Otros procesos de fabricación aditiva, como la impresión 3D, pueden tener puntos fuertes y aplicaciones diferentes.
¿Puede utilizarse la tecnología MIM para la creación de prototipos? Sí, la tecnología MIM puede utilizarse para la creación de prototipos, lo que permite a ingenieros y diseñadores evaluar la forma, el ajuste y la función de los componentes metálicos antes de pasar a la producción en serie.