Estudio sobre el revestimiento por láser de pintura en polvo a base de níquel
Introducción
Revestimiento láser es el uso de la tecnología láser para revestir la superficie del sustrato con el fin de obtener las propiedades requeridas. El sistema de aleación del revestimiento láser incluye principalmente la aleación con base de hierro, la aleación con base de níquel, la aleación con base de cobalto y el cermet. El revestimiento por láser de polvo de aleación con base de hierro es adecuado para piezas que requieren un desgaste parcial y son fáciles de deformar. El sustrato del revestimiento de aleación con base de hierro es principalmente hierro fundido y acero de bajo contenido en carbono. Los revestimientos de aleaciones con base de níquel son adecuados para componentes que requieren resistencia parcial al desgaste, resistencia a la corrosión por calor y resistencia a la fatiga térmica, y la densidad de potencia láser requerida es ligeramente superior a la del revestimiento de aleaciones con base de hierro. Los revestimientos de aleaciones con base de cobalto son adecuados para piezas que requieren resistencia al desgaste, a la corrosión y a la fatiga térmica. El revestimiento cerámico tiene una alta resistencia a altas temperaturas, buena estabilidad térmica, alta estabilidad química y una amplia gama de materiales de matriz. En este artículo se analizan los materiales en polvo de aleación autofusibles basados en níquel utilizados en el revestimiento por láser.
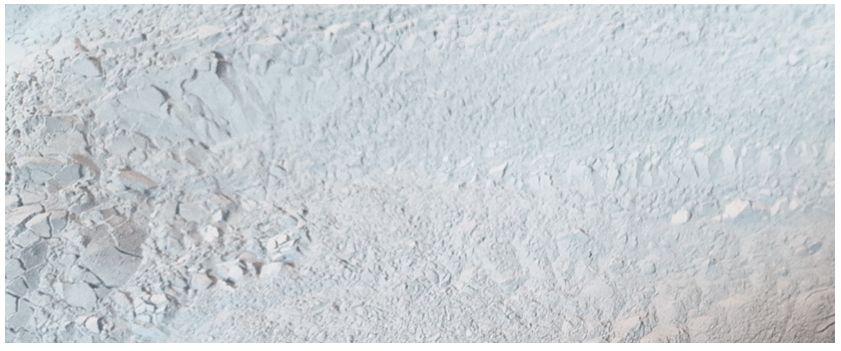
Materiales y métodos
En polvo de aleación de autofusión a base de níquel utilizado en este experimento se preparó y fundió mediante atomización con gas. Los factores a tener en cuenta en el diseño de la composición del polvo y en el diseño de la formulación de la materia prima de fundición incluyen principalmente:tanto el rendimiento del polvo como el proceso de revestimiento láser, el polvo debe tener un punto de fusión y un contenido de oxígeno bajos. Para evitar el agrietamiento del revestimiento, la capa de revestimiento y el sustrato deben coincidir en la medida de lo posible, es decir, el coeficiente de expansión térmica del revestimiento y del sustrato debe ser lo más parecido posible. La humectabilidad y la reacción del polvo deben ser buenas.
Basándose en los factores anteriores, mediante el diseño repetido de la composición del material y la prueba de rendimiento del proceso de soldadura por pulverización, el siguiente polvo de aleación autofusible a base de níquel BNi-3 (AMS 4778) con un tamaño de partícula de 45-105um se selecciona como material de revestimiento láser (fracción de masa %), su composición química se muestra en Cuadro 1. El material de base para el revestimiento láser es acero al carbono medio. El grosor de la capa de revestimiento es de 0,6 mm.
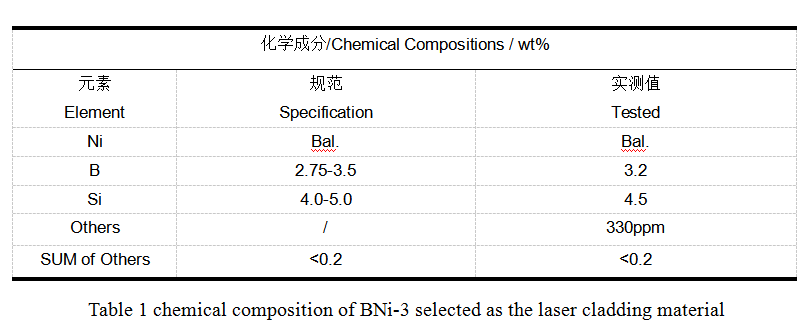
Figura 1 muestra la morfología de las partículas del BNi-3 seleccionado como material de revestimiento láser. Se puede observar que las partículas de polvo son esféricas. El polvo esférico hace que el polvo tenga una buena fluidez, de modo que el polvo puede llegar a la superficie de la pieza de trabajo de manera uniforme y sin problemas desde el alimentador de polvo sin bloquear la boquilla de polvo. Si la forma del polvo es compleja, la fluidez es deficiente, lo que provoca fácilmente el transporte por pulsación del polvo. Además, si la superficie del polvo aumenta, el polvo se oxidará cuando se caliente a alta temperatura, por lo que la calidad de la capa de revestimiento se verá afectada.
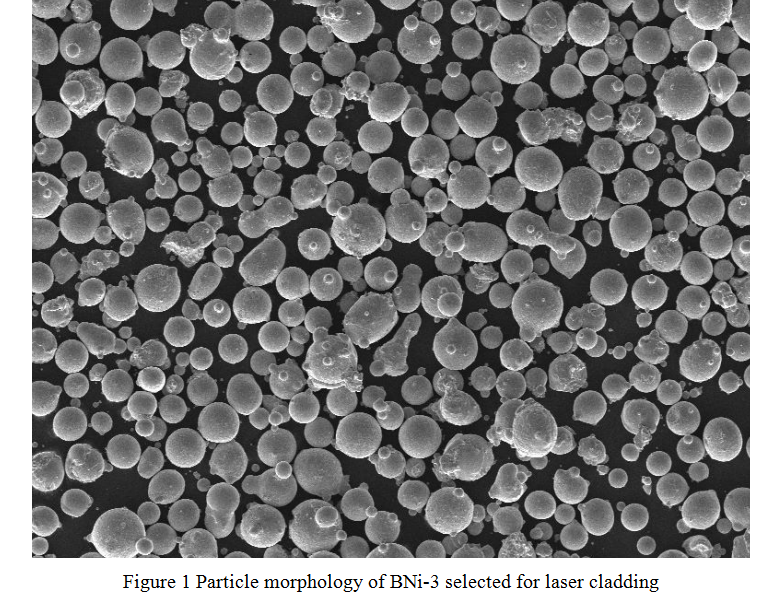
Las pruebas de proceso muestran que el níquel hace que el polvo tenga un buen rendimiento en el proceso de revestimiento, y puede mejorar el rendimiento a alta temperatura y la resistencia al agrietamiento del polvo. El silicio y el boro pueden hacer que el polvo de aleación sea autofusible. En el polvo de aleación autofusible, el boro y el silicio pueden formar escoria por sí mismos, lo que tiene un efecto de autoprotección. El análisis muestra que a partir del boro y el níquel se forman Ni2B y Ni3B con bajo punto de fusión, lo que reduce el punto de fusión de la aleación y mejora el rendimiento del proceso del polvo. Sin embargo, si el contenido de boro en la aleación es demasiado alto, habrá más compuestos de boro y compuestos de óxido de silicato quebradizos en el límite de grano, por lo que se reducirán la plasticidad y la tenacidad del revestimiento, aumentará la fragilidad y la capa de revestimiento será propensa a las grietas, por lo que el contenido de boro debe controlarse dentro del rango adecuado.
Figura 2 muestra la sección transversal de la capa de revestimiento. Desde la capa superficial hasta el núcleo, se suceden la zona de la capa de revestimiento, la zona afectada por el calor y la matriz. La zona de la capa de revestimiento es una zona brillante muy estrecha, que es más estrecha que la zona de unión metalúrgica obtenida por pulverización térmica, soldadura de superficie y otros métodos. La zona afectada por el calor es equivalente al tratamiento térmico debido a la conducción del calor. Con el aumento de la distancia desde la zona de la capa de revestimiento, la temperatura de calentamiento disminuye continuamente, por lo que desde la zona de transición de fase, parte de la zona de transición de fase, y finalmente a la estructura original de la matriz.
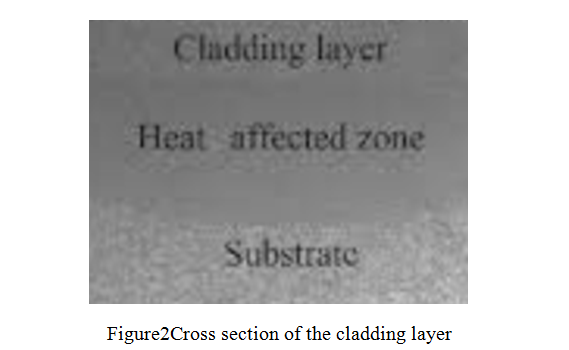
En este proyecto, la resistencia al desgaste de la muestra recubierta con este polvo se comparó con el bloque de prueba estándar AISI 52100 con 62 HRC en las condiciones de prueba de la máquina de pruebas de desgaste MM-200 doméstica, a velocidad 380 r/min, fricción seca, tiempo 1,5 h. La resistencia al desgaste se determina midiendo la pérdida de peso de las muestras después del desgaste. Los resultados mostraron que la resistencia al desgaste de la capa de refuerzo de la superficie de revestimiento láser del polvo de BNi-3 a base de níquel es mejor que el de AISI 52100, por lo que la vida útil de las piezas resistentes al desgaste mejorará considerablemente.