Visión general
Tratamiento posterior a la atomización de polvos metálicos es crucial en el proceso de fabricación de diversas industrias, desde la aeroespacial hasta la de dispositivos médicos. Este proceso mejora las propiedades de los polvos metálicos, haciéndolos más adecuados para aplicaciones específicas. El tratamiento suele implicar procesos como el recocido, el tamizado y la modificación de la superficie para mejorar la distribución del tamaño de las partículas, la morfología y la composición química.
¿Qué es el tratamiento post-atomización?
El tratamiento posterior a la atomización se refiere a los diversos métodos aplicados a los polvos metálicos después de que se hayan producido mediante atomización. La atomización es el proceso en el que el metal fundido se rompe en finas gotitas que luego se solidifican en partículas de polvo. Los tratamientos posteriores a la atomización son esenciales para mejorar las propiedades del polvo, garantizar su consistencia y mejorar su rendimiento en las aplicaciones finales.
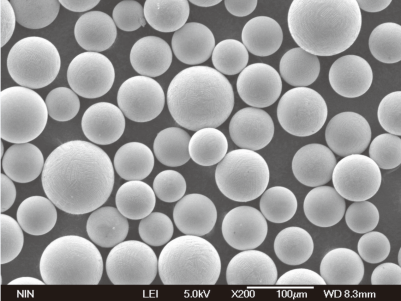
Tipos de polvos metálicos y su composición
Existen varios tipos de polvos metálicos, cada uno con una composición y unas propiedades únicas adaptadas a aplicaciones específicas. Estos son algunos de los polvos metálicos más utilizados y sus composiciones:
Polvo metálico | Composición | Propiedades |
---|---|---|
Acero inoxidable 316L | Fe, Cr, Ni, Mo | Resistencia a la corrosión, alta resistencia a la tracción |
Titanio Ti6Al4V | Ti, Al, V | Elevada relación resistencia/peso, resistencia a la corrosión |
Aluminio 6061 | Al, Mg, Si | Ligero, buenas propiedades mecánicas |
Aleación de cobalto-cromo | Co, Cr, Mo | Alta resistencia al desgaste, excelente biocompatibilidad |
Aleación de níquel 625 | Ni, Cr, Mo, Nb | Alta resistencia, excelente resistencia a la corrosión |
Acero martensítico envejecido 18Ni300 | Fe, Ni, Co, Mo | Alta resistencia, buena tenacidad |
Aleación de cobre C18150 | Cu, Cr, Zr | Alta conductividad, excelente resistencia al desgaste |
Carburo de tungsteno | WC, Co | Dureza extrema, resistencia al desgaste |
Inconel 718 | Ni, Cr, Fe, Nb, Mo | Alta resistencia, buena resistencia a la oxidación |
Aleación de bronce CuSn12 | Cu, Sn | Buena resistencia a la corrosión, excelente maquinabilidad |
Características del polvo para el tratamiento posterior a la atomización
Los tratamientos posteriores a la atomización están diseñados para mejorar diversas características de los polvos metálicos. He aquí algunas propiedades clave:
Característica | Descripción |
---|---|
Distribución del tamaño de las partículas | Garantiza la uniformidad, lo que afecta a la fluidez y a la densidad de empaquetado |
Morfología | Formas esféricas o irregulares que afectan al flujo y al empaquetamiento |
Superficie | Influye en la reactividad y el comportamiento de sinterización |
Pureza | Los altos niveles de pureza reducen el riesgo de contaminación |
Fluidez | Afecta a la facilidad de manipulación y procesamiento |
Densidad aparente | Impacta en la eficiencia del empaquetado y la sinterización |
Niveles de oxidación | La menor oxidación mejora el rendimiento en aplicaciones de alta temperatura |
Aplicaciones del polvo para Tratamiento posterior a la atomización
Las propiedades mejoradas de los polvos metálicos post-atomizados los hacen adecuados para una amplia gama de aplicaciones:
Solicitud | Descripción |
---|---|
Aeroespacial | Componentes ligeros y de alta resistencia |
Automotor | Piezas de motor, componentes de transmisión |
Productos sanitarios | Implantes, instrumental quirúrgico |
Sector de la energía | Álabes de turbina, pilas de combustible |
Electrónica | Tintas conductoras, gestión térmica |
Herramientas | Herramientas de corte, troqueles |
Fabricación aditiva (impresión 3D) | A medida, geometrías complejas, prototipos |
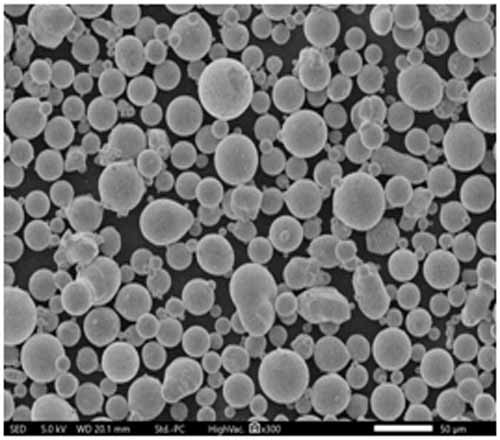
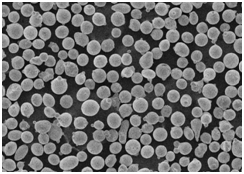
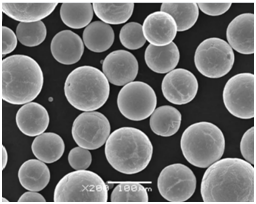
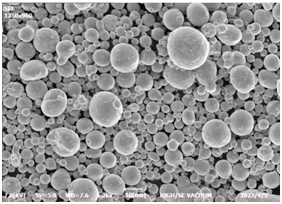
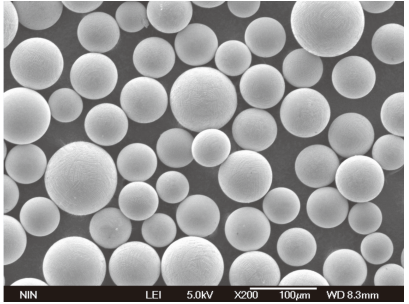
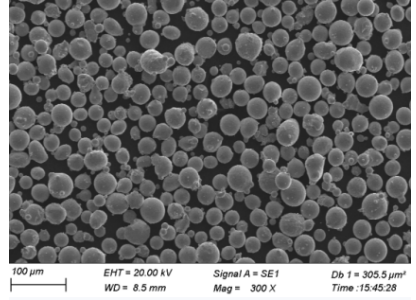
Especificaciones, tamaños, calidades y normas
Al seleccionar polvos metálicos para el tratamiento posterior a la atomización, es importante tener en cuenta las especificaciones, tamaños, grados y normas. Aquí tiene una tabla detallada como referencia:
Tipo de polvo | Gama de tamaños (µm) | Grado | Normas |
---|---|---|---|
Acero inoxidable 316L | 15-45, 45-105 | AISI 316L | ASTM A276, AMS 5653 |
Titanio Ti6Al4V | 15-45, 45-90 | 5º curso | ASTM B348, AMS 4928 |
Aluminio 6061 | 20-63, 63-125 | AA 6061 | ASTM B209, AMS 4027 |
Aleación de cobalto-cromo | 10-45, 45-90 | ASTM F75 | ISO 5832-4 |
Aleación de níquel 625 | 15-53, 53-150 | UNS N06625 | ASTM B446, AMS 5666 |
Acero martensítico envejecido 18Ni300 | 10-45, 45-105 | Grado 300 | AMS 6514, ASTM A538 |
Aleación de cobre C18150 | 20-53, 53-150 | UNS C18150 | ASTM B606, RWMA Clase 2 |
Carburo de tungsteno | 5-15, 15-45 | Certificación ISO 9001 | ISO 9001, ASTM B777 |
Inconel 718 | 15-45, 45-105 | UNS N07718 | ASTM B637, AMS 5662 |
Aleación de bronce CuSn12 | 20-63, 63-150 | UNS C90700 | ASTM B505, AMS 4880 |
Proveedores y precios
Elegir el proveedor adecuado es crucial para obtener polvos metálicos de alta calidad. He aquí algunos proveedores y sus precios:
Proveedor | Ubicación | Polvo metálico | Precio (USD/kg) |
---|---|---|---|
Höganäs AB | Suecia | Acero inoxidable 316L | $50 – $70 |
Tecnología LPW | REINO UNIDO | Titanio Ti6Al4V | $300 – $400 |
Tecnología Carpenter | EE.UU. | Aluminio 6061 | $25 – $40 |
Arcam AB (GE Additive) | Suecia | Aleación de cobalto-cromo | $250 – $350 |
Sandvik | Suecia | Aleación de níquel 625 | $100 – $150 |
GKN Hoeganaes | EE.UU. | Acero martensítico envejecido 18Ni300 | $150 – $200 |
Especialidades metálicas AMETEK | EE.UU. | Aleación de cobre C18150 | $30 – $50 |
Kennametal | EE.UU. | Carburo de tungsteno | $70 – $90 |
Polvo metálico y proceso | EE.UU. | Inconel 718 | $200 – $250 |
Fabricación de polvos metálicos | REINO UNIDO | Aleación de bronce CuSn12 | $20 – $35 |
Ventajas e inconvenientes del polvo para el tratamiento posterior a la atomización
Cada polvo metálico tiene sus propias ventajas y limitaciones. He aquí una comparativa:
Polvo metálico | Ventajas | Limitaciones |
---|---|---|
Acero inoxidable 316L | Resistente a la corrosión, alta resistencia | Mayor coste en comparación con otros aceros |
Titanio Ti6Al4V | Ligero, de gran resistencia | Caro, difícil de procesar |
Aluminio 6061 | Ligero, buenas propiedades mecánicas | Menor resistencia que el acero |
Aleación de cobalto-cromo | Alta resistencia al desgaste, biocompatible | Caro, difícil de mecanizar |
Aleación de níquel 625 | Excelente resistencia a la corrosión, alta resistencia | Caro, alta densidad |
Acero martensítico envejecido 18Ni300 | Alta resistencia, buena tenacidad | Caro, requiere tratamiento térmico |
Aleación de cobre C18150 | Alta conductividad, resistencia al desgaste | Propenso a la oxidación, menos resistente que el acero |
Carburo de tungsteno | Extremadamente duro, resistente al desgaste | Quebradizo, caro |
Inconel 718 | Alta resistencia, buena resistencia a la oxidación | Caro, difícil de mecanizar |
Aleación de bronce CuSn12 | Buena resistencia a la corrosión, mecanizable | Menor resistencia en comparación con otras aleaciones |
Ventajas del polvo para el tratamiento posterior a la atomización
El tratamiento posterior a la atomización ofrece numerosas ventajas que mejoran la calidad y el rendimiento de los polvos metálicos. A continuación se detallan sus ventajas:
Distribución mejorada del tamaño de las partículas
Los tratamientos posteriores a la atomización, como el tamizado y la clasificación, ayudan a conseguir una distribución uniforme del tamaño de las partículas, lo que es crucial para un rendimiento uniforme en aplicaciones como la fabricación aditiva y la pulvimetalurgia.
Morfología mejorada
Tratamientos como el recocido y el tratamiento térmico pueden mejorar la morfología de las partículas de polvo, haciéndolas más esféricas. Las partículas esféricas fluyen mejor, se empaquetan con mayor eficacia y dan lugar a productos acabados de mayor calidad.
Contaminación reducida
Los polvos de gran pureza con una contaminación mínima son esenciales para aplicaciones como dispositivos médicos y componentes aeroespaciales. Los tratamientos posteriores a la atomización garantizan que los polvos cumplan estrictos requisitos de pureza.
Fluidez optimizada
Una buena fluidez es fundamental para procesos como la impresión 3D y el moldeo por inyección de metales.
Los tratamientos posteriores a la atomización mejoran las características de fluidez de los polvos, garantizando un procesamiento suave y fiable.
Niveles de oxidación controlados
Controlar los niveles de oxidación de los polvos metálicos es esencial para las aplicaciones de alta temperatura. Los tratamientos posteriores a la atomización ayudan a reducir la oxidación, mejorando así el rendimiento y la vida útil de los productos finales.
Especificaciones, tamaños, calidades y normas del polvo para Tratamiento posterior a la atomización
Seleccionar el polvo metálico adecuado implica tener en cuenta diversas especificaciones, tamaños, grados y normas. He aquí un desglose detallado:
Polvo metálico | Gama de tamaños (µm) | Grado | Normas |
---|---|---|---|
Acero inoxidable 316L | 15-45, 45-105 | AISI 316L | ASTM A276, AMS 5653 |
Titanio Ti6Al4V | 15-45, 45-90 | 5º curso | ASTM B348, AMS 4928 |
Aluminio 6061 | 20-63, 63-125 | AA 6061 | ASTM B209, AMS 4027 |
Aleación de cobalto-cromo | 10-45, 45-90 | ASTM F75 | ISO 5832-4 |
Aleación de níquel 625 | 15-53, 53-150 | UNS N06625 | ASTM B446, AMS 5666 |
Acero martensítico envejecido 18Ni300 | 10-45, 45-105 | Grado 300 | AMS 6514, ASTM A538 |
Aleación de cobre C18150 | 20-53, 53-150 | UNS C18150 | ASTM B606, RWMA Clase 2 |
Carburo de tungsteno | 5-15, 15-45 | Certificación ISO 9001 | ISO 9001, ASTM B777 |
Inconel 718 | 15-45, 45-105 | UNS N07718 | ASTM B637, AMS 5662 |
Aleación de bronce CuSn12 | 20-63, 63-150 | UNS C90700 | ASTM B505, AMS 4880 |
Análisis comparativo: Tipos de polvo para el tratamiento posterior a la atomización
Profundicemos en una comparación detallada de varios polvos metálicos:
Acero inoxidable 316L frente a titanio Ti6Al4V
Acero inoxidable 316L es conocido por su resistencia a la corrosión y su solidez. Sin embargo, Titanio Ti6Al4V es más ligero y tiene una mayor relación resistencia-peso, lo que lo hace ideal para aplicaciones aeroespaciales y médicas en las que el peso es un factor crítico.
Aluminio 6061 frente a aleación de cobalto-cromo
Aluminio 6061 ofrece buenas propiedades mecánicas y es ligero, pero no alcanza la resistencia al desgaste y la biocompatibilidad del Aleación de cobalto-cromoque se prefiere para implantes médicos y aplicaciones dentales.
Aleación de níquel 625 frente a acero martensítico envejecido 18Ni300
Aleación de níquel 625 es excelente para ambientes corrosivos y de alta temperatura debido a su mayor resistencia a la oxidación. Por otra parte, Acero martensítico envejecido 18Ni300 proporciona una resistencia y una tenacidad excepcionales, por lo que resulta adecuado para aplicaciones de utillaje y estructurales.
Aleación de cobre C18150 frente a carburo de wolframio
Aleación de cobre C18150 destaca en conductividad eléctrica y resistencia al desgaste, por lo que es perfecto para contactos eléctricos. Por el contrario, Carburo de tungsteno es incomparable en dureza y resistencia al desgaste, ideal para herramientas de corte y piezas de desgaste.
Inconel 718 frente a la aleación de bronce CuSn12
Inconel 718 se prefiere por su alta resistencia y su buena resistencia a la oxidación en entornos extremos. Aleación de bronce CuSn12con su excelente maquinabilidad y resistencia a la corrosión, se utiliza habitualmente en cojinetes y casquillos.
Opiniones de expertos y estudios
Los estudios y las opiniones de los expertos refuerzan la importancia del tratamiento posterior a la atomización para conseguir las propiedades deseadas de los polvos metálicos. Las investigaciones indican que la distribución optimizada del tamaño de las partículas y la morfología influyen significativamente en el rendimiento de los polvos en la fabricación aditiva y otras aplicaciones.
Por ejemplo, un estudio de la American Society for Testing and Materials (ASTM) destaca el papel de los tratamientos posteriores a la atomización para reducir la porosidad y mejorar las propiedades mecánicas de las piezas impresas en 3D. Del mismo modo, expertos de la Federación de Industrias de Polvos Metálicos (MPIF) subrayan la necesidad de polvos de gran pureza en aplicaciones críticas como los dispositivos aeroespaciales y médicos.
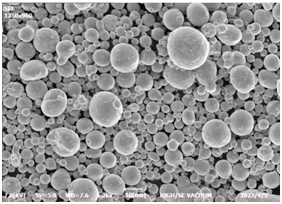
preguntas frecuentes
Pregunta | Respuesta |
---|---|
¿Qué es el tratamiento post-atomización? | El tratamiento posterior a la atomización se refiere a procesos como el recocido, el tamizado y la modificación de la superficie aplicados a los polvos metálicos tras la atomización para mejorar sus propiedades. |
¿Por qué es importante la distribución del tamaño de las partículas? | La distribución uniforme del tamaño de las partículas garantiza una fluidez, una densidad de empaquetamiento y un rendimiento general uniformes en diversas aplicaciones como la impresión 3D y la pulvimetalurgia. |
¿Cuáles son las ventajas de la morfología esférica del polvo? | Los polvos esféricos fluyen mejor, se empaquetan con mayor eficacia y dan lugar a productos acabados de mayor calidad que los polvos de forma irregular. |
¿Cómo reduce la contaminación el tratamiento posterior a la atomización? | Tratamientos como el tamizado y el tratamiento térmico ayudan a eliminar impurezas y contaminantes, garantizando polvos de gran pureza adecuados para aplicaciones críticas. |
¿Qué polvo metálico es mejor para aplicaciones aeroespaciales? | El titanio Ti6Al4V es el preferido por su elevada relación resistencia-peso y su excelente resistencia a la corrosión, lo que lo hace ideal para componentes aeroespaciales. |
¿Cuáles son las principales ventajas de utilizar la aleación de níquel 625? | La aleación de níquel 625 ofrece una gran solidez y una excelente resistencia a la corrosión, especialmente en entornos corrosivos y de altas temperaturas. |
¿Cómo se mejora la fluidez de los polvos metálicos? | Los tratamientos posteriores a la atomización, como el tamizado y el recocido, mejoran las características de fluidez de los polvos, lo que facilita su manipulación y procesamiento. |
¿Qué importancia tienen los niveles de oxidación en los polvos metálicos? | Los bajos niveles de oxidación son cruciales para las aplicaciones de alta temperatura, ya que mejoran el rendimiento y la vida útil de los productos finales. |
¿Pueden los tratamientos posteriores a la atomización mejorar las propiedades mecánicas? | Sí, tratamientos como el recocido y el tratamiento térmico pueden mejorar las propiedades mecánicas de los polvos metálicos, haciéndolos más adecuados para aplicaciones específicas. |
¿Qué polvo metálico es mejor para los implantes médicos? | La aleación de cromo-cobalto se utiliza habitualmente para implantes médicos por su gran resistencia al desgaste y su excelente biocompatibilidad. |