Visión general de Moldeo por inyección de metales (MIM)
El moldeo por inyección de metal (MIM) es un proceso de fabricación innovador que combina la versatilidad del moldeo por inyección de plástico con la resistencia y la integridad del metal. Se trata de una tecnología que ha revolucionado la producción de piezas metálicas pequeñas y complejas al ofrecer una solución rentable y de alta precisión.
Imagine la comodidad de producir en un solo paso componentes complejos que normalmente requieren varios procesos de mecanizado. Ésa es la magia del MIM. Este proceso es especialmente útil en sectores como el aeroespacial, los dispositivos médicos, la automoción y la electrónica de consumo, donde la precisión, la consistencia y el rendimiento no son negociables.
Pero, ¿qué es exactamente el moldeo por inyección de metales? ¿Cómo funciona? ¿Cuáles son los materiales utilizados y por qué está ganando popularidad en diversos sectores? Profundicemos en el mundo del MIM para descubrir los entresijos de esta innovadora tecnología.
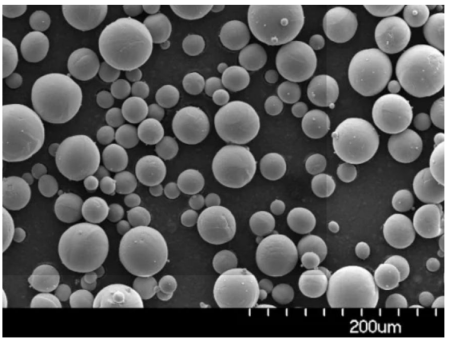
Explicación del proceso de moldeo por inyección de metales
Antes de entrar en detalles, dividamos el proceso MIM en partes digeribles:
- Preparación de la materia prima: El proceso comienza con la preparación de la materia prima. Los polvos metálicos se mezclan con un aglutinante termoplástico para formar una mezcla homogénea. A continuación, esta mezcla se granula en gránulos que pueden introducirse en la máquina de moldeo por inyección.
- Moldeo por inyección: Los gránulos de materia prima se calientan y se inyectan en la cavidad de un molde, donde toman la forma de la pieza deseada. Esta etapa es muy similar al moldeo por inyección de plástico tradicional, pero con el reto añadido de mantener la integridad de los polvos metálicos.
- Desbobinado: Una vez moldeada la pieza, hay que eliminar el aglutinante, que mantiene unidas las partículas metálicas. Esto se hace mediante un proceso llamado debinding, en el que la pieza se calienta en un entorno controlado para evaporar o disolver el aglutinante.
- Sinterización: La etapa final consiste en sinterizar la pieza a altas temperaturas para fusionar las partículas metálicas y obtener un componente metálico sólido y denso. El proceso de sinterización hace que la pieza se encoja, lo que se tiene muy en cuenta durante la fase de diseño para garantizar la precisión de las dimensiones finales.
- Tratamiento posterior: Dependiendo de la aplicación, las piezas sinterizadas pueden someterse a procesos adicionales como el mecanizado, el tratamiento superficial o el tratamiento térmico para mejorar sus propiedades o su acabado.
Ventajas de Moldeo por inyección de metales
¿Por qué el MIM se está convirtiendo en el proceso preferido de muchos fabricantes? He aquí algunas razones de peso:
- Complejidad y precisión: El MIM permite fabricar geometrías muy complejas con tolerancias muy ajustadas que serían difíciles o imposibles de conseguir con los métodos tradicionales de trabajo del metal.
- Variedad de materiales: En el MIM puede utilizarse una amplia gama de polvos metálicos, como aceros inoxidables, aceros para herramientas, titanio y superaleaciones. Esta flexibilidad permite a los fabricantes seleccionar el mejor material para su aplicación específica.
- Rentabilidad para grandes volúmenes: Aunque los costes iniciales de utillaje y preparación de la materia prima son elevados, el MIM resulta muy rentable cuando se producen grandes cantidades de piezas. La posibilidad de producir varias piezas en un solo ciclo de moldeo reduce aún más los costes.
- Residuos mínimos: El MIM es un proceso de forma casi neta, lo que significa que las piezas requieren poco o ningún mecanizado adicional. El resultado es un desperdicio mínimo de material, lo que lo convierte en una opción respetuosa con el medio ambiente.
- Propiedades mecánicas mejoradas: Las piezas MIM suelen presentar propiedades mecánicas superiores a las fabricadas mediante otros métodos de fabricación, gracias a la fina microestructura que se consigue durante la sinterización.
Tipos de polvos metálicos utilizados en MIM
La elección del polvo metálico es crucial en el proceso MIM, ya que influye directamente en las propiedades mecánicas, el acabado superficial y el rendimiento general de la pieza final. Estos son algunos de los polvos metálicos más utilizados en MIM:
Polvo metálico | Composición | Propiedades | Aplicaciones |
---|---|---|---|
Acero inoxidable 316L | Fe-Cr-Ni-Mo | Alta resistencia a la corrosión, buena resistencia mecánica | Dispositivos médicos, componentes de relojes, equipos de procesamiento de alimentos |
Acero inoxidable 17-4 PH | Fe-Cr-Ni-Cu | Alta resistencia, excelente resistencia a la corrosión, buena dureza | Aeroespacial, armas de fuego, instrumentos quirúrgicos |
Acero inoxidable 440C | Fe-Cr-C | Alta dureza, buena resistencia al desgaste, resistencia moderada a la corrosión | Rodamientos, cuchillas, válvulas |
Acero para herramientas M2 | Fe-Cr-Mo-W-V | Alta dureza, excelente resistencia al desgaste, estabilidad a altas temperaturas | Herramientas de corte, troqueles, moldes |
Inconel 718 | Ni-Cr-Fe-Nb-Mo-Ti | Resistencia a altas temperaturas, excelente resistencia mecánica | Aeroespacial, álabes de turbina, reactores nucleares |
Titanio Ti-6Al-4V | Ti-Al-V | Elevada relación resistencia/peso, excelente resistencia a la corrosión, biocompatibilidad | Implantes médicos, aplicaciones aeroespaciales y marinas |
Cobre (C11000) | Cu | Alta conductividad eléctrica, buena conductividad térmica, excelente maleabilidad | Conectores eléctricos, intercambiadores de calor, fontanería |
Kovar (FeNiCo) | Fe-Ni-Co | Baja expansión térmica, buenas propiedades magnéticas | Electrónica, juntas vidrio-metal, envasado de semiconductores |
Tungsteno (W) | W | Alta densidad, alto punto de fusión, buena conductividad térmica y eléctrica | Protección contra radiaciones, hornos de alta temperatura, componentes aeroespaciales |
Cobalto-cromo (Co-Cr) | Co-Cr-Mo | Alta resistencia al desgaste, excelente biocompatibilidad, buenas propiedades mecánicas | Implantes ortopédicos, prótesis dentales, álabes de turbina |
Estos polvos metálicos se seleccionan en función de su compatibilidad con el proceso MIM y de los requisitos específicos de la pieza final. Por ejemplo, los aceros inoxidables son populares por su resistencia a la corrosión, mientras que los aceros para herramientas se eligen por su dureza y resistencia al desgaste.
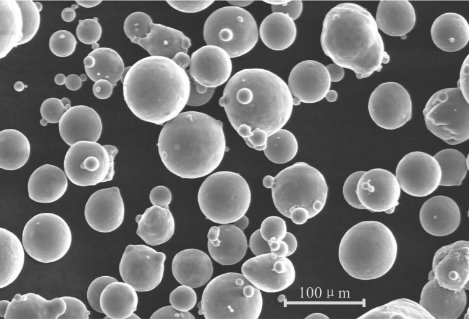
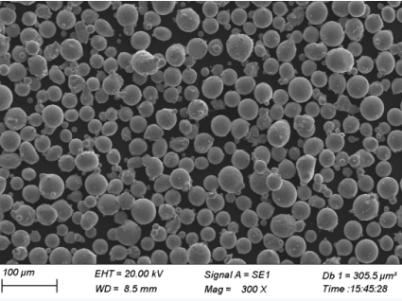
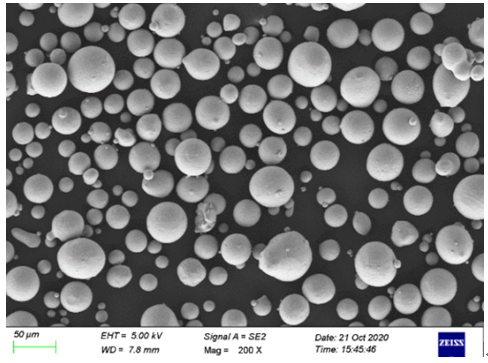
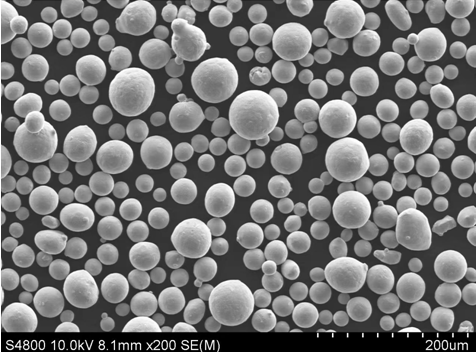
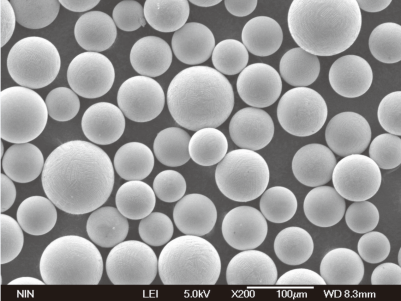
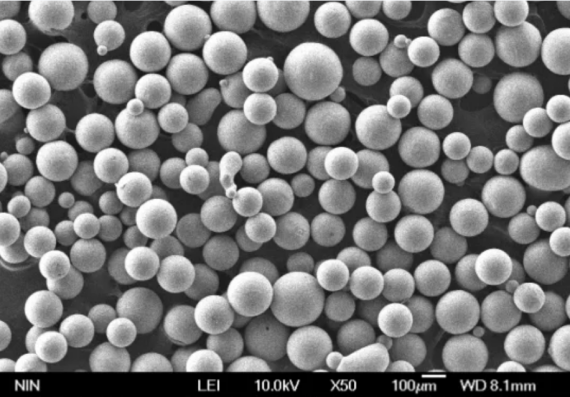
Composición y características de los materiales MIM
La composición de la mezcla de polvo metálico y aglutinante desempeña un papel fundamental en la determinación de las propiedades de la pieza MIM final. A continuación se describen las principales características de los materiales MIM:
Característica | Descripción |
---|---|
Tamaño de partícula | En el MIM se utilizan polvos finos con partículas de un tamaño comprendido entre 2 y 20 micras. Las partículas más pequeñas mejoran la sinterización, pero pueden requerir procesos de desbobinado más complejos. |
Sistema de encuadernación | El sistema aglutinante suele ser una mezcla de polímeros y ceras que mantiene unido el polvo metálico durante el moldeo. El aglutinante debe formularse cuidadosamente para garantizar que pueda eliminarse sin dañar la pieza. |
Comportamiento de la sinterización | La temperatura y el tiempo de sinterización son parámetros cruciales que influyen en la densidad final, el tamaño de grano y las propiedades mecánicas de la pieza. Los distintos metales requieren condiciones de sinterización diferentes. |
Densidad | Las piezas MIM suelen alcanzar densidades entre 95% y 99% de la densidad teórica del metal base. A mayores densidades, mejores propiedades mecánicas. |
Contracción | Las piezas suelen encoger entre 15 y 20% durante la sinterización. La predicción y el control precisos de la contracción son esenciales para lograr las dimensiones finales deseadas. |
Propiedades mecánicas | Las piezas MIM pueden alcanzar propiedades mecánicas comparables a las de los materiales forjados, como alta resistencia a la tracción, dureza y ductilidad. |
Acabado superficial | El acabado superficial de las piezas MIM suele ser liso, con valores típicos de rugosidad (Ra) del orden de 1-5 micras. El postprocesado puede mejorar aún más el acabado. |
Aplicaciones de Moldeo por inyección de metales
El MIM es una tecnología versátil con aplicaciones en diversos sectores. He aquí algunos de los usos más comunes:
Industria | Solicitud | Ejemplos |
---|---|---|
Aeroespacial | Componentes ligeros y de alta resistencia | Álabes de turbina, toberas de combustible, fijaciones |
Médico | Implantes y herramientas quirúrgicas biocompatibles | Implantes ortopédicos, aparatos dentales, instrumentos endoscópicos |
Automotor | Componentes de precisión para motores y transmisiones | Engranajes, sensores, inyectores de combustible |
Electrónica de consumo | Piezas pequeñas y complejas de gran durabilidad | Componentes de teléfonos inteligentes, objetivos de cámaras, conectores |
Armas de fuego | Componentes de alta resistencia con tolerancias estrictas | Gatillos, martillos, disparadores de corredera |
Industrial | Herramientas y piezas de maquinaria resistentes al desgaste | Herramientas de corte, componentes de bombas, cojinetes |
Joyería | Piezas complejas y decorativas | Cajas de reloj, cierres, diseños intrincados |
Especificaciones, tamaños, calidades y normas del MIM
Cuando se trata de MIM, existen normas y especificaciones específicas que los fabricantes deben cumplir para garantizar que los productos finales cumplan los requisitos de la industria. He aquí un resumen:
Especificaciones | Descripción | Materiales aplicables |
---|---|---|
Norma MPIF 35 | Proporciona directrices sobre las propiedades mecánicas de las piezas MIM | Diversos aceros inoxidables, aceros para herramientas y superaleaciones |
ASTM B883 | Especificación estándar para piezas MIM utilizadas en productos sanitarios | Titanio, acero inoxidable |
ISO 22068 | Norma internacional para el ensayo de piezas MIM | Todos los materiales MIM |
ASME B31.3 | Normas para piezas MIM utilizadas en entornos de alta presión | Acero inoxidable, aleaciones de níquel |
DIN 17440 | Norma europea para piezas MIM en aplicaciones de automoción | Aceros para herramientas, aceros inoxidables |
Comparación del moldeo por inyección de metales con otros procesos de fabricación
¿Cómo se compara el moldeo por inyección de metales con otros métodos de fabricación como la pulvimetalurgia tradicional, el mecanizado CNC o la fundición? Explorémoslo:
Parámetro | MIM | Pulvimetalurgia tradicional | Mecanizado CNC | Fundición |
---|---|---|---|---|
Complejidad | Alta complejidad alcanzable | Complejidad moderada | Alta complejidad, pero con costes más elevados | Alta complejidad, pero limitada por el diseño del molde |
Residuos materiales | Residuos mínimos (forma casi de red) | Pocos residuos | Grandes residuos (formación de virutas) | Residuos moderados |
Volumen de producción | Más adecuado para grandes volúmenes | Adecuado para volúmenes moderados | Rentable para volúmenes reducidos | Adecuado para grandes volúmenes |
Tolerancias | Tolerancias muy ajustadas | Menos preciso que el MIM | Tolerancias muy ajustadas | Depende de la precisión del molde |
Acabado superficial | Acabado liso | Acabado rugoso, requiere operaciones secundarias | Excelente acabado | Varía, pero en general es duro |
Coste | Alto coste inicial, bajo coste por pieza | Coste moderado | Coste elevado, especialmente para piezas complejas | Coste de moderado a elevado |
Proveedores y precios de los servicios de moldeo por inyección de metales
Elegir el proveedor adecuado de servicios MIM es crucial, ya que influye directamente en la calidad, el coste y el plazo de entrega de las piezas finales. A continuación presentamos algunos de los principales proveedores y sus precios:
Proveedor | Ubicación | Especialidades | Precios (por pieza) |
---|---|---|---|
Productos avanzados en polvo | EE.UU. | Dispositivos médicos, componentes aeroespaciales | $5 – $50 |
Grupo ARC en el mundo | EE.UU. | Automoción, armas de fuego, aplicaciones industriales | $1 – $30 |
Indo-MIM | India | Producción de gran volumen, diversos materiales | $0.50 – $20 |
Parmaco | Suiza | Componentes de precisión, piezas pequeñas | $2 – $40 |
Sistemas Elnik | Alemania | Herramientas, aleaciones personalizadas | $10 – $100 |
Empresas ATW | EE.UU. | Medicina, automoción, productos de consumo | $3 – $25 |
Tecnologías CMG | REINO UNIDO | Soluciones MIM personalizadas, creación de prototipos | $2 – $35 |

preguntas frecuentes
Pregunta | Respuesta |
---|---|
¿Cuáles son los plazos de entrega habituales de las piezas MIM? | Los plazos pueden variar en función de la complejidad de la pieza y el volumen requerido. Por lo general, se tarda entre 8 y 12 semanas desde el diseño hasta la producción de una pieza nueva. |
¿Puede utilizarse el MIM para la producción de bajo volumen? | Aunque el MIM es más rentable para la producción de grandes volúmenes, también puede utilizarse para series pequeñas si la complejidad de la pieza y los requisitos de material justifican los costes iniciales. |
¿Cuáles son las limitaciones del MIM? | El MIM no es adecuado para piezas muy grandes debido a la elevada contracción que se produce durante la sinterización. También es menos eficaz para piezas que requieren tolerancias extremadamente estrechas sin postprocesado. |
¿En qué se diferencia el MIM de la fabricación aditiva (impresión 3D)? | El MIM ofrece mejores propiedades de los materiales y es más rentable para la producción de grandes volúmenes que la fabricación aditiva, que es más adecuada para la creación de prototipos y piezas de bajo volumen y muy personalizadas. |
¿Qué materiales no pueden utilizarse en MIM? | Los materiales con puntos de fusión muy altos o los que no pueden sinterizarse eficazmente, como el tungsteno puro o determinadas cerámicas, no son adecuados para el MIM. |