Visión general
Deposición de energía dirigida (DED) es una tecnología puntera de fabricación aditiva que deposita material con precisión, capa a capa, para crear piezas metálicas de alta calidad. Utiliza fuentes de energía focalizadas como láseres, haces de electrones o arcos de plasma para fundir el material, que luego se deposita sobre un sustrato o una pieza existente. La DED es famosa por su capacidad para producir geometrías complejas, reparar componentes dañados y crear piezas metálicas de alto rendimiento con propiedades mecánicas superiores.
El DED se utiliza ampliamente en diversos sectores, como el aeroespacial, la automoción, el médico y el energético, gracias a su versatilidad y eficacia. Esta tecnología ofrece ventajas significativas sobre los métodos de fabricación tradicionales, como la reducción del desperdicio de material, tiempos de producción más cortos y la capacidad de crear diseños intrincados que de otro modo serían difíciles de lograr.
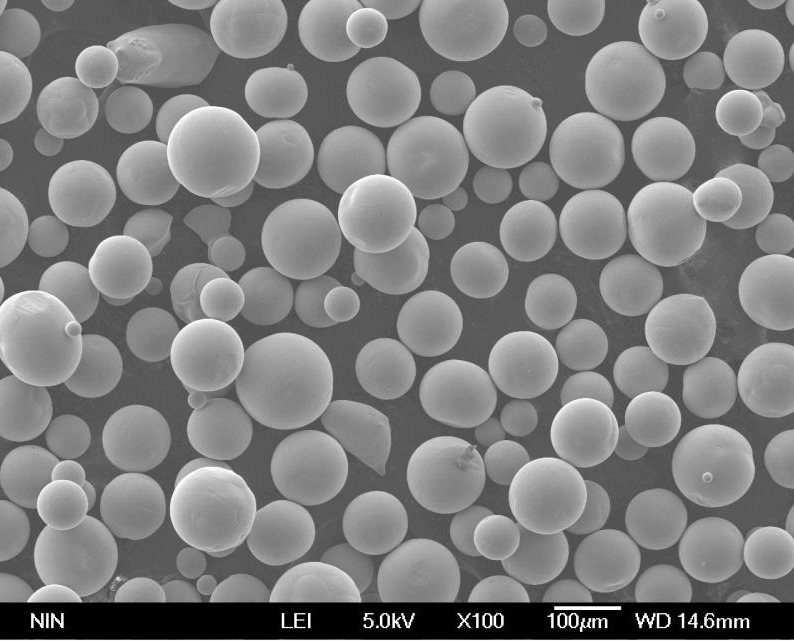
Tipos de polvos metálicos utilizados en DED
Polvos metálicos comunes para DED
Modelo de polvo metálico | Composición | Propiedades | Aplicaciones |
---|---|---|---|
Inconel 625 | Níquel, cromo, molibdeno | Alta resistencia, resistente a la corrosión | Industria aeroespacial, naval y química |
Ti-6Al-4V | Titanio, aluminio, vanadio | Elevada relación resistencia/peso, biocompatible | Aeroespacial, implantes médicos, automoción |
Acero inoxidable 316L | Hierro, cromo, níquel, molibdeno | Alta resistencia a la corrosión, buenas propiedades mecánicas | Procesado de alimentos, dispositivos médicos, aplicaciones marinas |
Hastelloy X | Níquel, molibdeno, cromo | Resistente a la oxidación y a altas temperaturas | Aeroespacial, turbinas de gas industriales |
CoCrMo | Cobalto, cromo, molibdeno | Resistente al desgaste, alta resistencia | Implantes médicos, prótesis dentales |
AlSi10Mg | Aluminio, silicio, magnesio | Ligero, buena conductividad térmica | Automoción, aeroespacial, electrónica |
Acero martensítico envejecido (18Ni-300) | Hierro, níquel, cobalto, molibdeno | Alta resistencia, excelente tenacidad | Utillaje, aeroespacial, piezas de alto rendimiento |
Cobre | Cobre puro | Excelente conductividad térmica y eléctrica | Componentes eléctricos, intercambiadores de calor |
Acero para herramientas (H13) | Hierro, Cromo, Molibdeno, Vanadio | Alta dureza, buena resistencia a la fatiga térmica | Herramientas, fundición a presión, moldeo por inyección |
Aleación de níquel 718 | Níquel, cromo, hierro | Alta resistencia, resistente a la corrosión | Aeroespacial, generación de energía, petróleo y gas |
Aplicaciones del DED
Aplicaciones habituales de la tecnología DED
Solicitud | Industria | Beneficios |
---|---|---|
Reparación de componentes | Aeroespacial, Automoción | Rentable, prolonga la vida útil de las piezas |
Creación de prototipos | Todas las industrias | Rápida iteración del diseño, plazo de entrega reducido |
Geometrías complejas | Medicina, aeroespacial | Permite diseños complejos y estructuras ligeras |
Piezas funcionales | Fabricación, Industria | Componentes personalizados de alto rendimiento |
Herramientas y moldes | Automoción, Fabricación | Herramientas duraderas y de alta precisión |
Investigación de materiales | Académico, Industrial | Propiedades de los materiales a medida, estudios experimentales |
Especificaciones y normas para DED
Especificaciones de los polvos metálicos más comunes en DED
Modelo de polvo metálico | Tamaño de las partículas (μm) | Densidad (g/cm³) | Punto de fusión (°C) | Norma ASTM |
---|---|---|---|---|
Inconel 625 | 15-45 | 8.44 | 1290-1350 | ASTM B443 |
Ti-6Al-4V | 15-45 | 4.43 | 1604-1660 | ASTM B348 |
Acero inoxidable 316L | 15-45 | 7.99 | 1375-1400 | ASTM A276 |
Hastelloy X | 15-45 | 8.22 | 1260-1355 | ASTM B435 |
CoCrMo | 15-45 | 8.29 | 1330-1390 | ASTM F75 |
AlSi10Mg | 15-45 | 2.67 | 570-580 | ISO 3522 |
Acero martensítico envejecido (18Ni-300) | 15-45 | 8.00 | 1413 | ASTM A538 |
Cobre | 15-45 | 8.96 | 1083 | ASTM B216 |
Acero para herramientas (H13) | 15-45 | 7.80 | 1426 | ASTM A681 |
Aleación de níquel 718 | 15-45 | 8.19 | 1260-1336 | ASTM B637 |
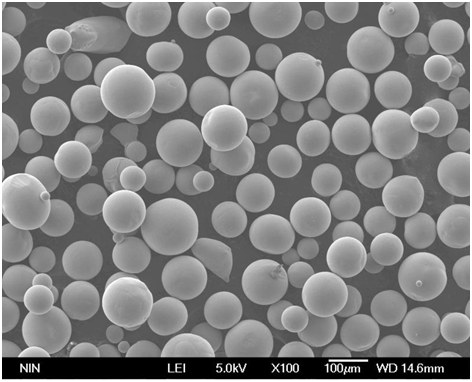
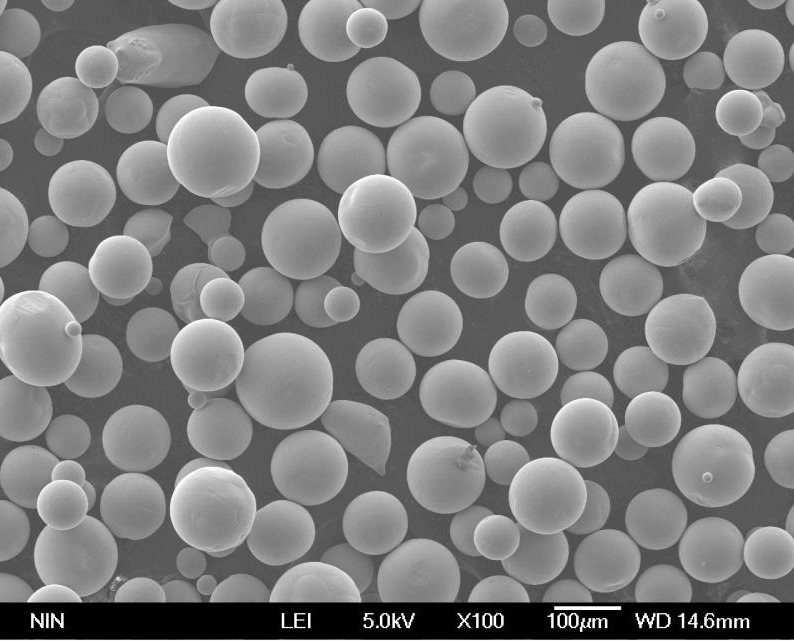
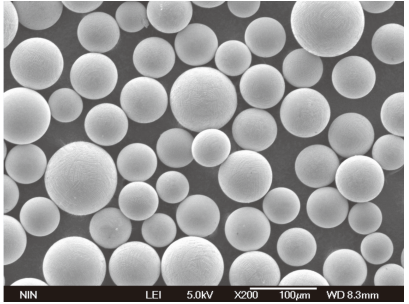
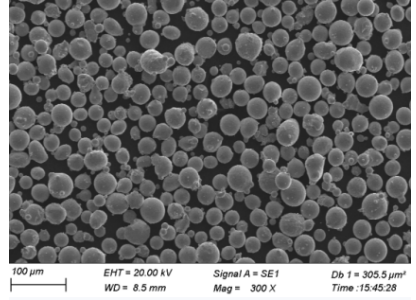
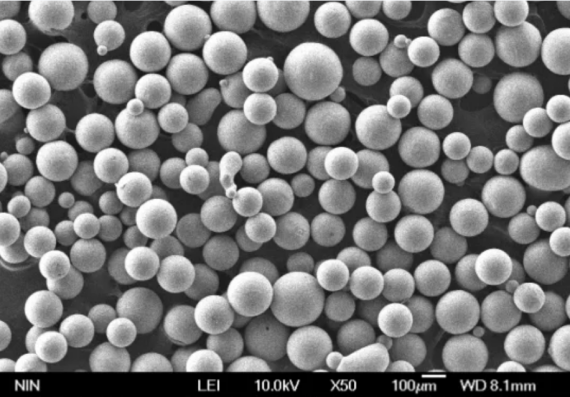
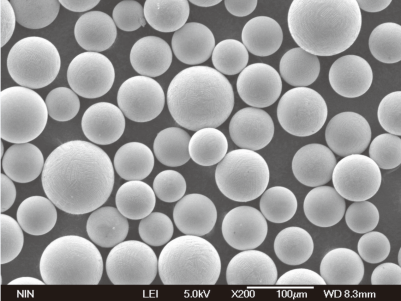
Proveedores y precios
Proveedores y precios de los polvos metálicos en DED
Proveedor | Modelo de polvo metálico | Precio por kg (USD) | Ubicación | Póngase en contacto con |
---|---|---|---|---|
Tecnología Carpenter | Inconel 625 | $100 | EE.UU. | www.carpentertechnology.com |
Arcam AB | Ti-6Al-4V | $200 | Suecia | www.arcam.com |
GKN Hoeganaes | Acero inoxidable 316L | $50 | EE.UU. | www.gknpm.com |
HC Starck | Hastelloy X | $150 | Alemania | www.hcstarck.com |
Sandvik | CoCrMo | $120 | Suecia | www.materials.sandvik |
Tecnología LPW | AlSi10Mg | $80 | REINO UNIDO | www.lpwtechnology.com |
Aubert & Duval | Acero martensítico envejecido (18Ni-300) | $180 | Francia | www.aubertduval.com |
Tekna | Cobre | $60 | Canadá | www.tekna.com |
Hoganas AB | Acero para herramientas (H13) | $90 | Suecia | www.hoganas.com |
VSMPO-AVISMA | Aleación de níquel 718 | $170 | Rusia | www.vsmpo.ru |
Comparación de los pros y los contras de la tecnología DED
Ventajas y limitaciones de la tecnología DED
Aspecto | Ventajas | Limitaciones |
---|---|---|
Eficiencia material | Mínimo desperdicio, alto aprovechamiento del material | Alto coste inicial de los materiales |
Geometrías complejas | Capaz de crear diseños intrincados | Limitado por la resolución y precisión de la máquina |
Capacidad de reparación | Reparación eficaz de componentes de alto valor | Requiere operarios cualificados y un control preciso |
Velocidad de producción | Producción más rápida que con los métodos tradicionales | Más lento que otros métodos de fabricación aditiva |
Propiedades mecánicas | Propiedades personalizables de alto rendimiento | Potencial de tensiones residuales y defectos |
Versatilidad | Se puede utilizar una amplia gama de materiales | Limitado por la disponibilidad de materias primas |
Análisis detallado de los polvos metálicos para DED
Inconel 625
El Inconel 625 es una superaleación a base de níquel conocida por sus excelentes propiedades mecánicas y su resistencia a la corrosión, incluso a temperaturas elevadas. Su composición incluye cantidades significativas de níquel, cromo y molibdeno, que contribuyen a su resistencia y estabilidad. Este material es ideal para aplicaciones aeroespaciales, marinas y de procesamiento químico, en las que los componentes deben soportar entornos duros y grandes esfuerzos.
Ti-6Al-4V
El Ti-6Al-4V, también conocido como titanio de grado 5, es una opción popular para DED por su elevada relación resistencia-peso y su biocompatibilidad. Compuesta de titanio, aluminio y vanadio, esta aleación ofrece excelentes propiedades mecánicas y resistencia a la corrosión, por lo que es adecuada para componentes aeroespaciales, implantes médicos y automoción.
Acero inoxidable 316L
El acero inoxidable 316L es un acero inoxidable austenítico conocido por su gran resistencia a la corrosión y sus buenas propiedades mecánicas. La adición de molibdeno mejora su resistencia a la corrosión, especialmente frente a cloruros y otros disolventes industriales. Se suele utilizar en la elaboración de alimentos, dispositivos médicos y aplicaciones marinas.
Hastelloy X
Hastelloy X es una superaleación a base de níquel con una excelente resistencia a la oxidación y a altas temperaturas. Su composición incluye níquel, molibdeno y cromo, que le confieren excelentes propiedades mecánicas a temperaturas elevadas.
Este material se utiliza ampliamente en turbinas de gas aeroespaciales e industriales.
CoCrMo
El CoCrMo, o aleación de cobalto, cromo y molibdeno, es conocido por su excepcional resistencia al desgaste y su gran solidez. Este material se utiliza habitualmente en implantes médicos y prótesis dentales por su biocompatibilidad y durabilidad.
AlSi10Mg
AlSi10Mg es una aleación de aluminio con buena conductividad térmica y propiedades ligeras. La adición de silicio y magnesio mejora sus propiedades mecánicas, lo que la hace adecuada para aplicaciones de automoción, aeroespaciales y electrónicas.
Acero martensítico envejecido (18Ni-300)
El acero martensítico envejecido (18Ni-300) es una aleación de acero de alta resistencia con excelente tenacidad y dureza. Se compone de hierro, níquel, cobalto y molibdeno, y se utiliza en utillaje, aeronáutica y piezas de alto rendimiento.
Cobre
El cobre es conocido por su excelente conductividad térmica y eléctrica. En DED, el cobre puro se utiliza para componentes eléctricos, intercambiadores de calor y otras aplicaciones que requieren una alta conductividad.
Acero para herramientas (H13)
El acero para herramientas H13 es un acero al cromo-molibdeno-vanadio de gran dureza y buena resistencia a la fatiga térmica. Se utiliza ampliamente en aplicaciones de utillaje, fundición a presión y moldeo por inyección.
Aleación de níquel 718
La aleación de níquel 718 es una aleación de níquel y cromo conocida por su gran resistencia a la corrosión. Se utiliza habitualmente en la industria aeroespacial, la generación de energía y la industria del petróleo y el gas.
Ventajas del DED
Por qué elegir Deposición de energía dirigida?
- Eficiencia del material: El DED utiliza los materiales de forma eficiente, minimizando los residuos y optimizando su utilización. A diferencia de los métodos sustractivos tradicionales, que suelen dar lugar a importantes pérdidas de material, el DED añade material solo donde es necesario, lo que lo convierte en una opción más sostenible.
- Geometrías complejas: Esta tecnología permite crear diseños intrincados y geometrías complejas que son difíciles o imposibles de conseguir con los métodos de fabricación tradicionales. Esto abre nuevas posibilidades para diseños innovadores y estructuras ligeras.
- Capacidad de reparación: La DED es muy eficaz para reparar componentes de gran valor, como álabes de turbinas y piezas aeroespaciales. Esto puede alargar considerablemente la vida útil de estos componentes, reduciendo costes y tiempos de inactividad.
- Velocidad de producción: En comparación con la fabricación tradicional, la DED puede producir piezas más rápidamente, especialmente para componentes de tamaño pequeño y mediano. Esto reduce los plazos de entrega y permite la creación rápida de prototipos y la iteración.
- Propiedades mecánicas: Las piezas DED suelen presentar propiedades mecánicas superiores, como mayor resistencia y durabilidad, gracias al control preciso del proceso de deposición del material. El resultado son piezas de alto rendimiento que cumplen las estrictas normas del sector.
- Versatilidad: El DED puede trabajar con una amplia gama de materiales, como metales, cerámica y materiales compuestos. Esta versatilidad lo hace adecuado para diversas aplicaciones en múltiples sectores.
Limitaciones del DED
¿Cuáles son los retos de la deposición de energía dirigida?
- Costes iniciales elevados: La inversión inicial en equipos y materiales de DED puede ser elevada, lo que puede suponer un obstáculo para algunas empresas. Sin embargo, los beneficios a largo plazo suelen compensar estos costes, sobre todo en aplicaciones de gran valor.
- Resolución y precisión de la máquina: Aunque el DED puede crear geometrías complejas, está limitado por la resolución y precisión de las máquinas. Conseguir detalles finos y tolerancias ajustadas puede ser todo un reto.
- Se necesitan operarios cualificados: El funcionamiento de los sistemas DED requiere operarios cualificados que puedan controlar con precisión el proceso de deposición. Esto puede aumentar los costes operativos y la complejidad.
- Tensiones residuales potenciales: Los rápidos ciclos de calentamiento y enfriamiento en DED pueden provocar tensiones residuales y posibles defectos en las piezas. Para mitigar estos problemas es necesario un control adecuado del proceso y técnicas de postprocesado.
- Disponibilidad de materia prima: Aunque la DED puede funcionar con una amplia gama de materiales, la disponibilidad de materias primas específicas puede ser limitada. Esto puede restringir la elección de materiales para determinadas aplicaciones.
- Más lento que algunos métodos aditivos: En comparación con otros métodos de fabricación aditiva, como la fusión de lechos de polvo, la DED puede ser más lenta para determinadas aplicaciones. Esto puede afectar a su idoneidad para la producción de grandes volúmenes.
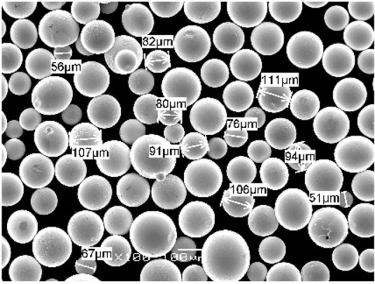
Preguntas más frecuentes
Pregunta | Respuesta |
---|---|
¿Qué es la deposición de energía dirigida (DED)? | La deposición de energía dirigida (DED) es un proceso de fabricación aditiva que utiliza energía focalizada para fundir y depositar material, capa a capa, para crear piezas. |
¿Qué materiales pueden utilizarse en DED? | DED puede trabajar con una gran variedad de materiales, incluidos metales, cerámica y materiales compuestos. Los metales más comunes son Inconel 625, Ti-6Al-4V, acero inoxidable 316L, etc. |
¿Cuáles son las ventajas de la DED? | Entre las ventajas del DED se encuentran la eficiencia de los materiales, la capacidad de crear geometrías complejas, la eficacia de las reparaciones, la rapidez de producción y el alto rendimiento de las piezas. |
¿Cuáles son las limitaciones del DED? | Entre sus limitaciones figuran los elevados costes iniciales, las limitaciones de resolución y precisión de la máquina, la necesidad de operarios cualificados, las posibles tensiones residuales y la disponibilidad de materia prima. |
¿Qué industrias utilizan DED? | Las industrias que utilizan DED son la aeroespacial, automovilística, médica, energética y manufacturera, entre otras. |
¿Cómo se compara la DED con otros métodos de fabricación aditiva? | El DED ofrece ventajas en cuanto a eficacia del material y capacidad de reparación, pero puede resultar más lento y costoso que otros métodos aditivos, como la fusión de lecho de polvo. |
¿Puede el DED reparar los componentes existentes? | Sí, la DED es muy eficaz para reparar componentes existentes de gran valor, prolongar su vida útil y reducir costes. |
¿Es el DED adecuado para la producción a gran escala? | Aunque la DED es excelente para la creación de prototipos, componentes de tamaño pequeño a mediano y reparaciones, puede ser menos adecuada para la producción de grandes volúmenes en comparación con otros métodos. |
¿Cuál es el futuro de la tecnología DED? | El futuro de la tecnología DED parece prometedor, ya que los continuos avances en materiales, control de procesos y capacidades de las máquinas impulsan su adopción en diversos sectores. |
¿Cómo elegir el polvo metálico adecuado para DED? | La elección del polvo metálico adecuado depende de los requisitos específicos de la aplicación, como las propiedades mecánicas, la resistencia a la corrosión y la compatibilidad con el proceso DED. Consultar a proveedores y expertos puede ayudar a tomar la mejor decisión. |