1. Introducción
El moldeo por inyección de metales (MiM) es un innovador proceso de fabricación que combina la versatilidad del moldeo por inyección de plásticos con la resistencia y durabilidad de los metales. El MiM ha ganado una gran popularidad en diversos sectores gracias a su capacidad para producir componentes metálicos complejos con una precisión excepcional. Este artículo se adentra en el mundo del Metales MiMEn este artículo se analizan las ventajas, el proceso de fabricación, las aplicaciones y las tendencias futuras.
2. ¿Qué son los metales MiM?
Los metales MiM son componentes metálicos fabricados mediante el proceso de moldeo por inyección de metales. El proceso consiste en mezclar polvos metálicos finos con un material aglutinante para crear una materia prima que pueda inyectarse en la cavidad de un molde. Tras el moldeo por inyección, el aglutinante se elimina mediante un proceso de desbobinado y la pieza metálica compactada restante se sinteriza para conseguir su resistencia y densidad finales. El resultado es un componente metálico totalmente denso con formas intrincadas y excelentes propiedades mecánicas.
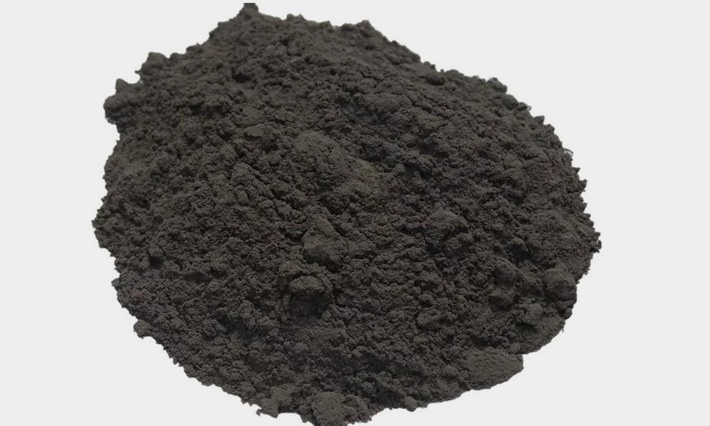
3. Ventajas de MiM Metals
3.1 Alta precisión
Los metales MiM ofrecen una exactitud dimensional excepcional y una gran precisión. El proceso de moldeo por inyección permite crear geometrías complejas y detalles intrincados difíciles de conseguir con los métodos de fabricación tradicionales. Este nivel de precisión hace que los metales MiM sean adecuados para aplicaciones que exigen tolerancias estrechas y diseños intrincados.
3.2 Geometrías complejas
MiM permite fabricar componentes metálicos complejos con formas intrincadas, como paredes delgadas, características finas y entalladuras. La capacidad de fabricar geometrías tan complejas abre nuevas posibilidades de diseño a los ingenieros y elimina la necesidad de operaciones de mecanizado secundarias. Los metales MiM ofrecen una mayor libertad de diseño y facilitan la producción de piezas que antes se consideraban inalcanzables.
3.3 Selección de materiales
Los metales MiM pueden fabricarse a partir de una amplia gama de materiales, como aceros inoxidables, aceros para herramientas, aceros de baja aleación y aleaciones de titanio, entre otros. La versatilidad en la selección de materiales permite a los ingenieros elegir el metal óptimo para los requisitos específicos de su aplicación, garantizando las propiedades mecánicas, la resistencia a la corrosión y la resistencia al calor deseadas.
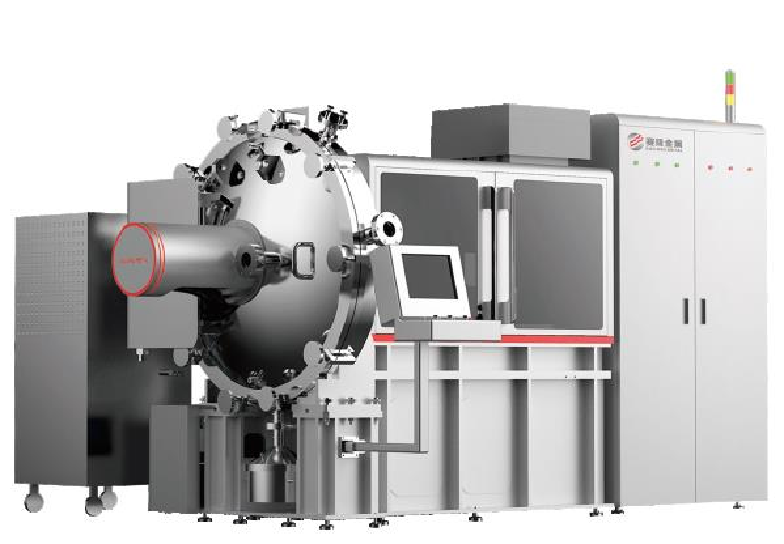
4. Proceso de fabricación de metales MiM
El proceso de fabricación de los metales MiM consta de varios pasos clave:
4.1 Preparación de la materia prima
En esta etapa, los polvos metálicos finos se mezclan con un material aglutinante para formar una materia prima homogénea. El tamaño del polvo metálico, la composición del aglutinante y los parámetros de mezcla se controlan cuidadosamente para obtener una materia prima homogénea con buenas propiedades de fluidez.
4.2 Moldeo por inyección
La materia prima se inyecta en la cavidad de un molde a alta presión y temperatura. El molde suele ser de acero para herramientas y tiene una cavidad que define la forma deseada del componente metálico final. La materia prima inyectada llena la cavidad del molde, tomando su forma y capturando todos los detalles intrincados.
4.3 Desbobinado
Tras el moldeo por inyección, es necesario eliminar el material aglutinante de la pieza moldeada. La eliminación del aglutinante suele realizarse mediante métodos térmicos o con disolventes. Este proceso elimina la mayor parte del aglutinante, dejando tras de sí una frágil pieza verde.
4.4 Sinterización
A continuación, la pieza en bruto se sinteriza en un horno, donde se somete a un proceso de calentamiento y enfriamiento cuidadosamente controlado. La sinterización hace que las partículas metálicas restantes se adhieran entre sí, dando lugar a un componente metálico totalmente denso con propiedades mecánicas mejoradas.
4.5 Operaciones de acabado
Una vez finalizado el proceso de sinterización, el componente MiM puede someterse a operaciones de acabado adicionales, como tratamiento térmico, tratamiento superficial, mecanizado y pulido, para conseguir el acabado superficial, la precisión dimensional y las propiedades funcionales deseadas.
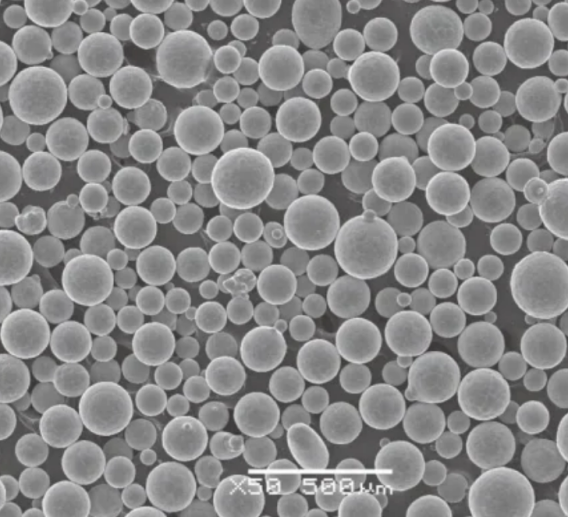
5. Aplicaciones de MiM Metals
Los metales MiM encuentran aplicaciones en diversas industrias, entre ellas:
5.1 Industria del automóvil
Los componentes MiM se utilizan en aplicaciones de automoción como piezas de motor, componentes de transmisión, sistemas de inyección de combustible y carcasas de sensores. La capacidad de producir formas complejas y lograr una alta precisión hace que los metales MiM sean valiosos para mejorar la eficiencia del motor, reducir el peso y mejorar el rendimiento general.
5.2 Industria médica y dental
Los metales MiM se utilizan ampliamente en los ámbitos médico y odontológico por su biocompatibilidad y sus excelentes propiedades mecánicas. Se utilizan en la producción de instrumentos quirúrgicos, implantes ortopédicos, brackets dentales y componentes protésicos. El MiM permite fabricar implantes específicos para cada paciente con geometrías complejas para un mejor ajuste y funcionalidad.
5.3 Industria electrónica
Los metales MiM se utilizan en la industria electrónica para fabricar conectores, carcasas de sensores y componentes de blindaje electromagnético. Su alta conductividad eléctrica y flexibilidad de diseño los hacen ideales para aplicaciones en las que el blindaje contra interferencias electromagnéticas (EMI) es crucial.
5.4 Industria aeroespacial
Los componentes MiM encuentran cada vez más aplicaciones en el sector aeroespacial, donde la reducción de peso, la eficiencia en el consumo de combustible y la fiabilidad son primordiales. Los metales MiM se utilizan en la fabricación de componentes de motores de aviación, soportes, carcasas y piezas estructurales, y ofrecen la solidez, la resistencia a la corrosión y la complejidad de diseño necesarias.
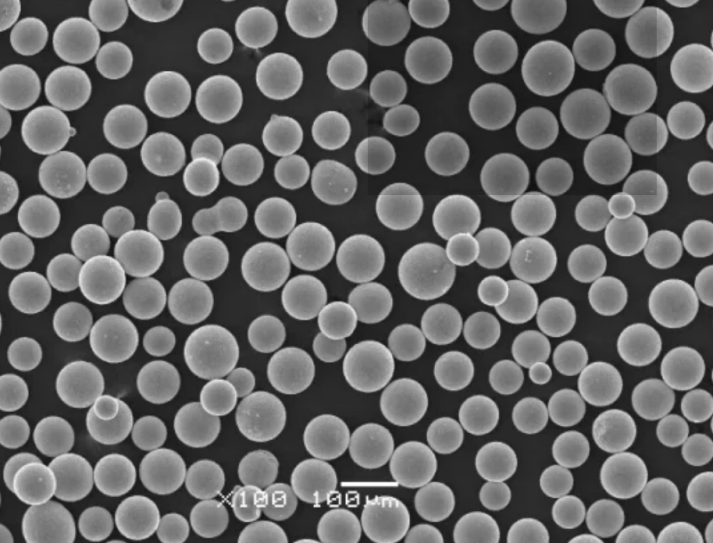
6. Comparación con otros métodos de fabricación
6.1 MiM frente al mecanizado convencional
A diferencia de los métodos de mecanizado convencionales, MiM permite producir formas complejas y detalles finos sin necesidad de retirar mucho material. MiM reduce el desperdicio de material y mejora la eficiencia de la producción, por lo que es una alternativa rentable para componentes metálicos intrincados.
6.2 MiM frente a la fundición a la cera perdida
El moldeo por inyección ofrece mayor flexibilidad de diseño y precisión dimensional que la fundición a la cera perdida. El proceso de moldeo por inyección permite crear características complejas, paredes finas y muescas que son difíciles de conseguir mediante fundición. MiM también elimina la necesidad de costosas herramientas y reduce los plazos de entrega.
6.3 MiM frente a la fundición a presión
MiM ofrece una mayor complejidad de diseño y una mayor precisión dimensional que la fundición a presión. La fundición a presión suele requerir operaciones de mecanizado secundarias para conseguir la geometría de pieza deseada, mientras que MiM puede producir formas complejas directamente del molde sin procesamiento adicional. Sin embargo, la fundición a presión puede ser más adecuada para la producción de grandes volúmenes.
7. Limitaciones de MiM Metals
Aunque los metales MiM ofrecen numerosas ventajas, hay que tener en cuenta algunas limitaciones:
7.1 Limitaciones en la selección de materiales
No todos los materiales son adecuados para la MiM. Algunos materiales pueden tener una disponibilidad limitada en forma de polvo o presentar dificultades durante los procesos de desaglomeración y sinterización. Las limitaciones en la selección de materiales deben tenerse en cuenta durante la fase de diseño para garantizar la compatibilidad del material elegido con el proceso MiM.
7.2 Consideraciones económicas
La MiM puede resultar rentable para fabricar componentes metálicos intrincados y complejos. Sin embargo, puede no ser adecuada para la producción de grandes volúmenes debido a los costes asociados a la selección de herramientas y materiales. Debe realizarse un análisis de costes para determinar la viabilidad de la MiM para una aplicación específica.
7.3 Limitaciones de tamaño y peso
MiM es más eficaz para componentes de tamaño pequeño o mediano debido a las limitaciones del proceso de moldeo por inyección y la capacidad del horno de sinterización. Las piezas grandes o pesadas pueden resultar difíciles de fabricar con MiM. Las consideraciones de tamaño y peso deben tenerse en cuenta a la hora de determinar la viabilidad del uso de MiM para un componente concreto.
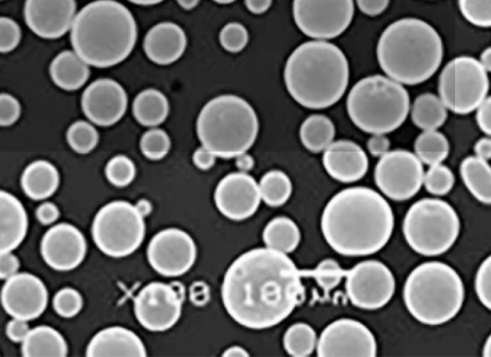
8. Tendencias futuras de la tecnología MiM Metal
El campo de los metales MiM sigue evolucionando, con una investigación y un desarrollo continuos centrados en mejorar el proceso y ampliar sus capacidades. Algunas de las tendencias futuras de la tecnología de metales MiM son:
- Materiales avanzados: Los investigadores están explorando nuevas aleaciones metálicas y materiales compuestos que puedan procesarse con MiM, ampliando la gama de aplicaciones y mejorando las propiedades de los materiales.
- Optimización de procesos: Se están realizando esfuerzos para optimizar el proceso de fabricación de MiM, incluida la formulación de la materia prima, los parámetros de moldeo por inyección, las técnicas de desbobinado y las condiciones de sinterización. Estas optimizaciones pretenden mejorar la eficiencia, reducir los costes y mejorar la calidad de las piezas.
- Ampliación y producción a gran escala: La industria está trabajando en la ampliación del proceso MiM para dar cabida a mayores volúmenes de producción. Esto implica avances en el utillaje, la automatización y el control de procesos para satisfacer las demandas de las industrias que requieren una producción en masa.
- Integración con la fabricación aditiva: La integración de la MiM con técnicas de fabricación aditiva, como la impresión 3D, es prometedora para crear componentes híbridos que combinen las ventajas de ambos procesos. Esta integración puede permitir la producción de piezas complejas con propiedades de material a medida.
- Acabado superficial y tratamiento posterior: Los investigadores están explorando técnicas para mejorar el acabado superficial de los componentes MiM, reduciendo la necesidad de extensas operaciones de postprocesado. Esto incluye avances en los métodos de pulido, revestimiento y tratamiento de superficies.
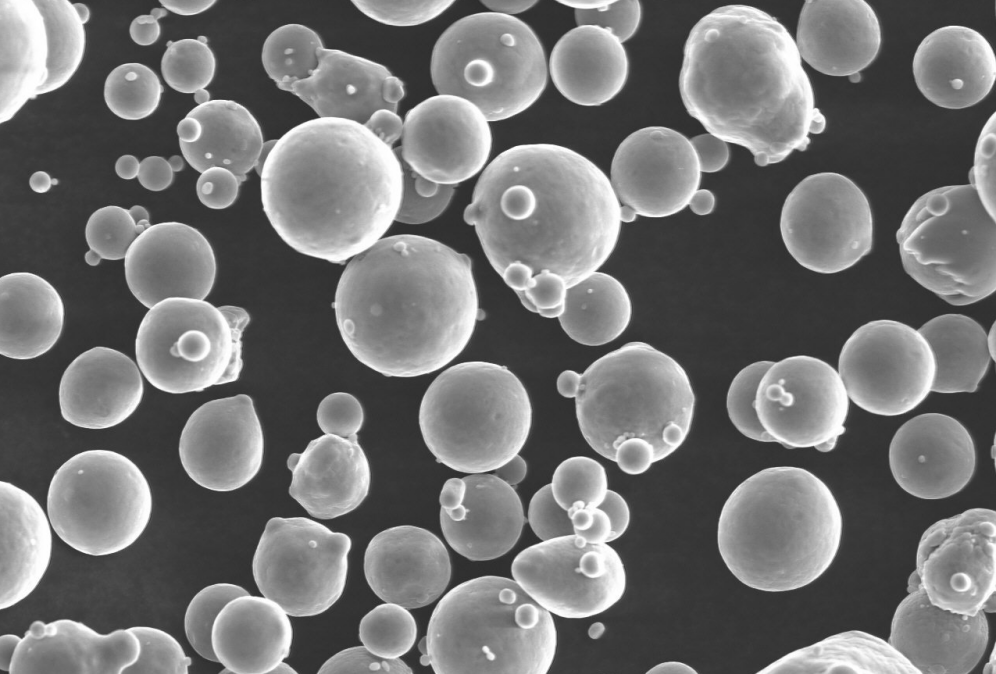
9. Conclusión
Los metales MiM han revolucionado la fabricación de metales al ofrecer una precisión excepcional, geometrías complejas y una amplia gama de opciones de materiales. El proceso MiM, desde la preparación de la materia prima hasta las operaciones de acabado, permite fabricar intrincados componentes metálicos para diversas industrias, como la automovilística, la médica, la electrónica y la aeroespacial. Aunque el proceso MiM tiene sus limitaciones, la investigación y el desarrollo en curso están abordando estos retos y allanando el camino para futuros avances en este campo. A medida que avanza la tecnología, se espera que la MiM desempeñe un papel cada vez más importante en la producción de componentes metálicos.
FAQs (Preguntas más frecuentes)
- Q: ¿Pueden utilizarse los metales MiM para aplicaciones sometidas a grandes esfuerzos? A: Sí, los metales MiM pueden presentar una gran resistencia mecánica y son adecuados para aplicaciones sometidas a grandes esfuerzos, como los componentes aeroespaciales y de automoción.
- Q: ¿Son rentables los metales MiM en comparación con los métodos de fabricación tradicionales? A: La MiM puede ser rentable para producir piezas complejas e intrincadas, pero las consideraciones de coste dependen de factores como el volumen, la selección de materiales y la complejidad de la pieza.
- Q: ¿Cuáles son las principales ventajas de utilizar metales MiM en la industria médica? A: Los metales MiM ofrecen biocompatibilidad, alta precisión y la posibilidad de fabricar implantes específicos para cada paciente con geometrías complejas, lo que aumenta su idoneidad para aplicaciones médicas.
- Q: ¿Se pueden reciclar los metales MiM? A: Sí, los metales MiM pueden reciclarse reprocesando la chatarra y las materias primas no utilizadas, lo que reduce los residuos de materiales y fomenta la sostenibilidad.
- Q: ¿Existen limitaciones de tamaño para los componentes producidos por MiM? A: MiM es más adecuado para componentes de tamaño pequeño o mediano debido a las limitaciones del proceso de moldeo por inyección y la capacidad del horno de sinterización. Las piezas más grandes o pesadas pueden plantear problemas.