Aleación CuCrZr (C18150) es una aleación endurecida por precipitación conocida por sus elevadas propiedades mecánicas, térmicas y eléctricas. La aleación se utiliza ampliamente en dispositivos de intercambio de calor y en el campo de la fusión nuclear.
Aleación CuCrZr es una aleación muy atractiva que puede sustituir al cobre puro en muchas aplicaciones, con Cr en el rango de 0,5 wt% a 1,2 wt%, Zr en el rango de 0,03 wt% a 0,3 wt%. Y es más fácil de fabricar, en comparación con el cobre puro, mediante la tecnología de fabricación aditiva basada en láser, que tiene propiedades mecánicas superiores y garantiza una conductividad térmica suficientemente alta que se considera una alternativa eficaz al cobre puro en muchas aplicaciones.
Para forjado Aleación CuCrZrlos principales tratamientos térmicos que pueden realizarse son el recocido en solución y el endurecimiento por envejecimiento, mientras que el recocido en solución puede omitirse en el caso de las aleaciones CuCrZr LPBF.
Recocido en solución: Este tratamiento se lleva a cabo calentando el material en una atmósfera protectora inerte (normalmente Ar) por encima de 900°C durante 30 minutos o varias horas. A continuación, el material se enfría rápidamente en agua o aire para sobresaturar la matriz de cobre con Cr y Zr. En el caso de las piezas LPBF, este tratamiento ya se ha completado durante el proceso LPBF porque el baño de fusión se enfría lo suficientemente rápido como para actuar como un enfriamiento rápido y producir una microestructura sobresaturada. Las piezas recocidas por disolución son muy blandas y sus propiedades mecánicas son demasiado débiles, por lo que no pueden considerarse un tratamiento térmico independiente.
Endurecimiento por envejecimiento: Normalmente, este tratamiento sigue al recocido en solución y se lleva a cabo a temperaturas más bajas durante un periodo de tiempo más largo (normalmente de 400°C a 600°C, hasta 6 horas en un entorno inerte (Ar, vacío, N2 y a veces también en atmósfera de H2). Este tratamiento está diseñado para permitir la precipitación controlada de fases intermetálicas duras en materiales sobresaturados para producir compuestos binarios o ternarios de Cu, Cr y Zr.
En este trabajo, sólo endurecimiento se estudia con la temperatura fijada en 550 ° C, se comprobaron tres duraciones diferentes. El objetivo era comprender cómo afecta la duración del tratamiento térmico al material y si el tratamiento de endurecimiento por envejecimiento es aplicable para cumplir los requisitos mecánicos del CuCrZr utilizando la fabricación aditiva para componentes de reactores de fusión.
En composición química, distribución del tamaño de las partículas (PSD) y forma de las partículas de los polvos utilizado en este estudio se muestra en el siguiente Certificado:
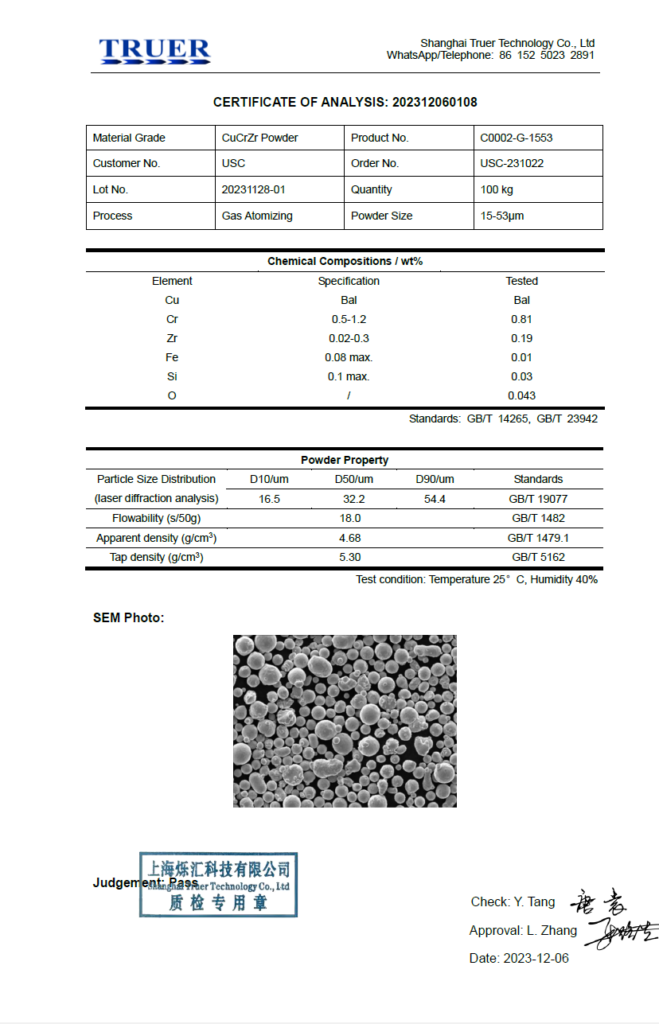
En este estudio, las muestras utilizadas para la investigación se imprimieron en geometrías cercanas a la forma de red. A continuación, la muestra se mecaniza para eliminar la piel rugosa y llevar la muestra a la geometría correcta para las pruebas de dureza.
La optimización de los parámetros se lleva a cabo para conseguir la mayor densidad de muestras con la combinación de espaciado de barrido (en el rango de 0,06-0,1 mm), velocidad del láser (de 350 a 650 mm/s) y potencia del láser mantenida en 370 W, la anchura de la franja fijada en 5 mm y el grosor de la capa fijado en 0,03 mm para todas las capas. En cada capa, la dirección de las franjas cambia con una rotación de 67°. La orientación vertical en este proyecto es la misma que la orientación del edificio. Diagramado en Figura 1:
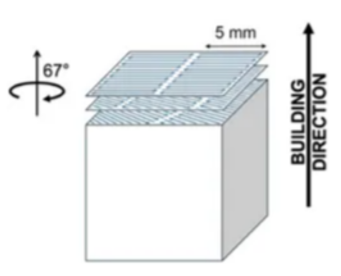
Figura 1. Diagrama esquemático del proceso de fabricación aditiva Diagrama esquemático del proceso de fabricación aditiva
Se fabricaron 40 cubos (10 mm x 10 mm x 10 mm) con diferentes combinaciones de espaciado y velocidad de barrido. A continuación se mide su densidad por el método de Arquímedes.
Las muestras as-built fueron tratadas por tres envejecimiento endurecimiento duración a 550 °C durante 1 h, 3 h y 6 h en atmósfera de nitrógeno con una pendiente de calentamiento y enfriamiento de 150 °C/h (enfriamiento en estufa y en atmósfera protectora).
El histograma en Figura 2 muestra la densidad relativa media de todas las combinaciones de parámetros del proceso de estudio medidas por el método de Arquímedes. La densidad de referencia es igual a 8,8869 g/cm3. Este valor se utiliza a continuación para calcular la densidad relativa de la muestra fabricada aditivamente.
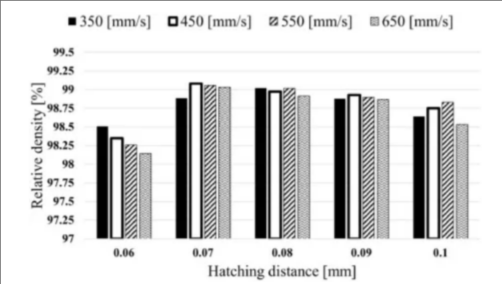
Figura 2. Densidad relativa de las muestras en función de los parámetros del proceso Densidad relativa de las muestras en función de los parámetros del proceso
La densidad relativa más alta (99,15%) se obtuvo utilizando el siguiente conjunto de parámetros de proceso: potencia láser 370 W, espaciado de escaneado (distancia de eclosión) 0,07 mm, velocidad de escaneado 450 mm/s y anchura de banda 5 mm. Con una distancia de barrido de 0,07 mm, no se produjo ningún cambio significativo en la densidad relativa con diferentes velocidades de barrido.
Una separación de barrido de 0,06 mm no es buena para la densidad, lo que da lugar a valores de densidad del orden del 98-98,5%. Esto puede deberse a la acumulación de calor que provoca un sobrecalentamiento que reduce la densidad final.
Figura 3 muestra la microestructura de las muestras después de 1h y 6h de tratamiento de envejecimiento. Se observa que una mayor duración del endurecimiento por envejecimiento no altera las características microestructurales que pueden observarse a bajo aumento, con una duración de 1h en comparación con una duración de 6h.
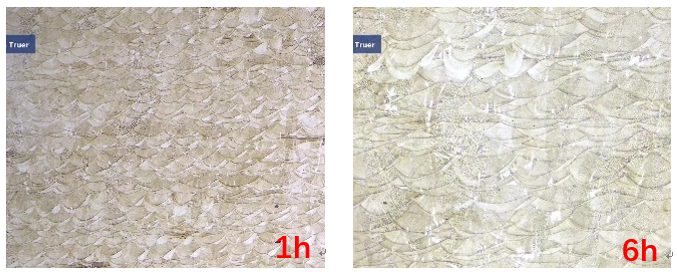
Figura 3. Microestructuras de las muestras 1h y 6h
Figura 4 muestra micrografías SEM de la muestra 6h. Se observan muchas partículas circulares (especialmente en la Figura 5c) en granos columnares, que pueden ser partículas nanoendurecidas. Una investigación posterior por EDS de estos precipitados de tamaño nanométrico mostró que se trata de pequeños precipitados de Cr o Zr de unos pocos a 50 nanómetros dispersos uniformemente en el interior del material.
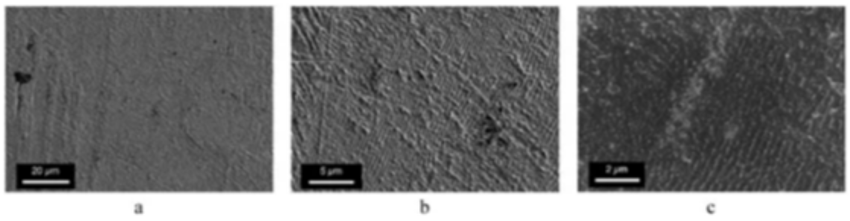
Figura 4 Imágenes SEM de electrones secundarios a diferentes aumentos tras envejecimiento a 550 °C durante 6 h
También se observaron defectos en las muestras estudiadas. Gráfico 5 muestra algunos defectos típicos de las piezas AM, como la falta de fusión (LoF) y la porosidad creada principalmente por el atrapamiento de gas.
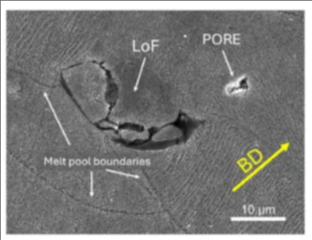
Figura 5 Defectos encontrados en la sección transversal de la muestra as-built de LPBF
Figura 6 son los valores de microdureza Vickers para las muestras as-built y tratadas térmicamente. Es fácil comprender que la dureza es inferior en las condiciones as-built en comparación con las muestras envejecidas: 1h de envejecimiento a 550 °C mejora significativamente esta dureza (165 HV, el doble del valor de 84 HV en las muestras as-built). Después de 3 h de envejecimiento, la dureza de la muestra empezó a reducirse (144 HV de media) y después de 6 horas de tratamiento, el material se ablandó aún más, pero en este caso también se produjo una mejora con respecto al estado as-built. Esto significa que la duración de 6 h es demasiado larga, lo que provoca un engrosamiento de los precipitados. Se puede observar que 1 hora ya es efectiva para aumentar la dureza del material en comparación con las condiciones as-built. Esto significa que el material ha sufrido un sobreenvejecimiento después de 1 h.
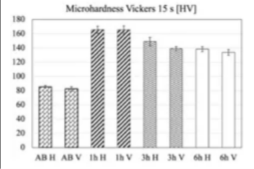
Figura 6 Valores de microdureza Vickers de las muestras tal cual y envejecidas
En resumen, desde un punto de vista mecánico, el tratamiento de envejecimiento es prometedor para la mejora de las propiedades mecánicas de la aleación LPBF CuCrZr. Sin embargo, es necesario realizar algunas investigaciones para encontrar la combinación previa de las propiedades del polvo, los parámetros LPBF y el proceso de envejecimiento.