Polvo de aleación se refiere a los polvos metálicos fabricados a partir de una aleación en lugar de un único metal puro. Las aleaciones son mezclas de dos o más elementos metálicos diseñadas para mejorar propiedades específicas como la fuerza, la resistencia a la corrosión o la maquinabilidad. Los polvos de aleación ofrecen ventajas únicas sobre los polvos de metal puro para aplicaciones pulvimetalúrgicas.
Polvo de aleación
El polvo de aleación ofrece propiedades que pueden adaptarse ajustando la composición. Esta tabla ofrece una visión general del polvo de aleación y sus características clave:
Parámetro | Detalles |
---|---|
Definición | Polvo metálico compuesto de una aleación en lugar de metal puro |
Composición | Mezcla de dos o más elementos metálicos |
Propiedades clave | Resistencia, resistencia a la corrosión, dureza, maquinabilidad, ductilidad, resistencia al desgaste, conductividad eléctrica, aspecto |
Ajustabilidad | Las propiedades pueden adaptarse modificando las proporciones de los elementos de aleación. |
Proceso de fabricación | Atomización de aleación fundida en polvo fino |
Forma de las partículas | Irregular, esférica, dendrítica dependiendo del proceso |
Sistemas de aleación comunes | Acero, acero inoxidable, aluminio, cobre, níquel, cobalto, titanio |
Aplicaciones | Piezas pulvimetalúrgicas, pulverización térmica, moldeo por inyección de metales (MIM), fabricación aditiva |
El polvo de aleación amplía las posibilidades de la pulvimetalurgia al ofrecer la posibilidad de diseñar materiales con propiedades específicas. Las principales características del polvo de aleación son:
- Composición - Los polvos de aleación contienen al menos dos elementos metálicos en proporciones variables para conseguir los atributos deseados. Los sistemas más comunes son las aleaciones de acero, aluminio y cobre.
- Propiedades ajustables - Cambiando los porcentajes de elementos de aleación, los materiales pueden adaptarse en cuanto a resistencia, resistencia a la corrosión, dureza, ductilidad, resistividad eléctrica y otras propiedades.
- Proceso de fabricación - El polvo de aleación se fabrica atomizando la aleación fundida para producir partículas de polvo esféricas y finas con buenas propiedades de flujo y empaquetamiento.
- Características de las partículas - La morfología, la distribución del tamaño y la pureza del polvo dependen del método de atomización. Los polvos pueden ser irregulares, esféricos o dendríticos.
- Sistemas de aleación - Existen cientos de composiciones de aleaciones normalizadas y personalizadas. Son habituales las aleaciones de acero, acero inoxidable, aluminio, cobre, níquel, cobalto y titanio.
- Aplicaciones - El polvo de aleación se utiliza para fabricar piezas PM, revestimientos de pulverización térmica, componentes metálicos moldeados por inyección y objetos impresos en 3D.
Con una gama tan amplia de propiedades ajustables, el polvo de aleación ofrece una importante herramienta de ingeniería de materiales para aplicaciones industriales. En las siguientes secciones se ofrecen más detalles sobre los tipos de polvo de aleación, los métodos de procesamiento y los usos.
Composiciones y propiedades del polvo de aleación
Existen muchas formulaciones de aleaciones en polvo estandarizadas y patentadas. Esta tabla resume algunos de los sistemas de aleación más comunes y sus características generales:
Sistema de aleación | Composición típica | Propiedades clave | Aplicaciones |
---|---|---|---|
Acero inoxidable | Fe, Cr (10-20%), Ni | Resistencia a la corrosión, solidez, resistencia al desgaste | Válvulas, componentes marinos, equipos de procesamiento de alimentos |
Acero para herramientas | Fe, Cr, V, W, Mo | Gran dureza, resistencia y resistencia al desgaste | Herramientas de corte, troqueles, piezas de máquinas |
Acero de baja aleación | Fe + Mn, Si, Ni, Cr, Mo | Dureza, resistencia, templabilidad | Engranajes, piezas de motor, tornillería |
Aluminio | Al + Cu, Mg, Si, Zn | Ligereza, resistencia a la corrosión, maquinabilidad | Componentes aeroespaciales, piezas de automoción |
Cobre | Cu + Zn, Sn, Al | Conductividad eléctrica, resistencia a la corrosión, maquinabilidad | Contactos eléctricos, puntas de soldadura, rodamientos |
Níquel | Ni + Cr, Mo, Cu, Fe | Resistencia a la corrosión, resistencia a altas temperaturas | Palas de turbinas de gas, equipos químicos |
Cobalto | Co + Cr, Mo, Ni, W, C | Resistencia a altas temperaturas, biocompatibilidad | Implantes dentales, herramientas de corte, implantes ortopédicos |
Titanio | Ti + Al, V, Cu, Ni | Ligereza, resistencia a la corrosión, biocompatibilidad | Componentes aeroespaciales, implantes médicos |
Seleccionando los metales base y los elementos de aleación adecuados, pueden diseñarse aleaciones pulvimetalúrgicas con:
- Alta resistencia para aplicaciones de carga
- Dureza y resistencia al desgaste de las herramientas de corte y resistencia a la abrasión
- Resistencia a la corrosión en productos químicos y agua de mar
- Capacidad a altas temperaturas y resistencia a la fluencia
- Conductividad eléctrica a medida, desde aislamiento hasta alta conducción
- Biocompatibilidad de implantes y dispositivos médicos
- Combinaciones de estas propiedades inalcanzables en los metales puros
La flexibilidad de las composiciones de aleación permite diseñar materiales a medida para aplicaciones y condiciones de funcionamiento específicas.
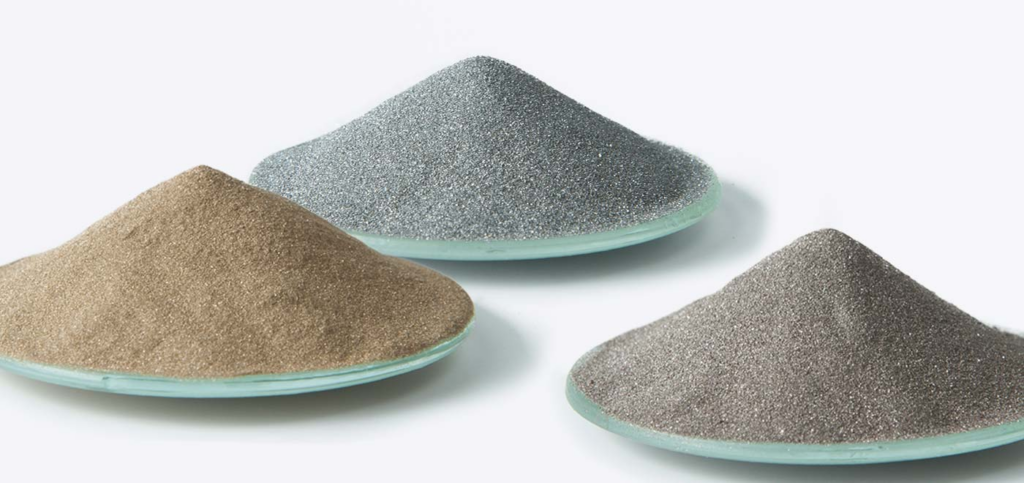
Métodos de fabricación de aleaciones en polvo
El polvo de aleación puede producirse utilizando varias técnicas de atomización para generar pequeñas partículas esféricas necesarias para la pulvimetalurgia. Los métodos típicos incluyen:
Método | Descripción | Características de las partículas | Capacidad de aleación |
---|---|---|---|
Atomización de gas | Chorro de metal fundido atomizado por chorros de gas inerte a alta presión | Polvo esférico fino, buena fluidez | La mayoría de las aleaciones |
Atomización del agua | Chorro de agua a alta velocidad rompe la corriente fundida | Partículas irregulares con formación de satélites | Limitado a aleaciones resistentes a la oxidación |
Electrodo giratorio | La fuerza centrífuga dispersa el metal fundido en finas gotas | Distribución relativamente gruesa del tamaño del polvo | Sólo para aleaciones conductoras de la electricidad |
Atomización por plasma | Polvo metálico evaporado en un plasma y recondensado | Partículas esféricas muy finas | Aleaciones de alto rendimiento |
La atomización con gas es el proceso más utilizado debido a su versatilidad y a la producción de polvo esférico fino. La atomización con agua es menos costosa, pero se limita a aleaciones resistentes a la oxidación, como los aceros inoxidables. Los métodos de plasma pueden producir polvos de aleación a nanoescala, pero tienen costes de capital más elevados.
Los parámetros del proceso de atomización, como el caudal de gas, la velocidad de vertido del metal y la velocidad de enfriamiento, pueden optimizarse para obtener la distribución del tamaño de partícula, la morfología, la pureza y la microestructura deseadas. El proceso de fabricación de polvo de aleación se adapta a la composición específica para producir materia prima en polvo de alta calidad para la fabricación de piezas de PM.
Características del polvo de aleación
Además de la composición, las propiedades y el rendimiento del polvo de aleación vienen determinados por características como:
Parámetro | Descripción |
---|---|
Distribución granulométrica | Gama de diámetros de partículas en el polvo; controlada por el proceso de atomización. |
Forma de las partículas | Esférico, irregular o dendrítico; afecta al flujo y empaquetado del polvo |
Morfología de la superficie de las partículas | Presencia de satélites, suavidad de la superficie, porosidad interna |
Composición química | Relación de elementos de aleación; puede diferir del nominal debido a la segregación. |
Fases presentes | Fases formadas en el polvo debido a la solidificación rápida; afecta a las propiedades. |
Impurezas | Contaminantes como oxígeno, nitrógeno o carbono recogidos durante la atomización. |
Densidad aparente | Densidad de empaquetamiento del polvo bajo una presión de compactación especificada |
Caudal | Capacidad del polvo para fluir, relacionada con la forma y la distribución del tamaño de las partículas. |
Estas características del polvo influyen en el comportamiento de la fabricación en procesos como el prensado, la sinterización, el moldeo por inyección de metal y la fabricación aditiva. Por ejemplo, las partículas de polvo irregulares degradan el llenado de la matriz y la resistencia en verde en el prensado de polvo. Los elementos químicamente reactivos, como el titanio, son sensibles a la captación de oxígeno durante la atomización.
El control y ensayo minuciosos de la química de las aleaciones y de las propiedades físicas del polvo garantizan una materia prima de alta calidad para el posterior procesamiento pulvimetalúrgico. Entre los métodos de ensayo se incluyen la microscopía óptica y electrónica, el análisis granulométrico por difracción láser, la medición de la densidad de toma, la reología del polvo y el análisis químico.
Aplicaciones del polvo de aleación
Gracias a sus propiedades únicas, las composiciones de aleaciones en polvo se utilizan en una amplia gama de aplicaciones pulvimetalúrgicas:
Piezas de prensa de polvo y sinterización
- Componentes estructurales de automoción: aceros aleados para mayor resistencia
- Válvulas, accesorios y filtros de acero inoxidable: resistencia a la corrosión
- Contactos y conectores de aleación de cobre: conductividad eléctrica
- Piezas mecánicas ferrosas y no ferrosas: solidez, resistencia al desgaste
Componentes moldeados por inyección de metal
- Implantes ortopédicos de acero inoxidable: biocompatibilidad, resistencia
- Palas de turbina de superaleación de cobalto: resistencia a altas temperaturas
- Piezas electrónicas de aleación de cobre: conductividad térmica
- Piezas de aleación de aluminio para armas de fuego: peso ligero
- Engranajes de acero de baja aleación: tenacidad, resistencia a la fatiga
Revestimientos por pulverización térmica
- Revestimientos de acero inoxidable: resistencia a la corrosión y al desgaste
- Recubrimientos de aleación de cobalto: dureza a altas temperaturas, resistencia al desgaste
- Recubrimientos de aleación de níquel: resistencia a la corrosión
- Revestimientos reforzados con carburo: resistencia extrema al desgaste
Polvos de fabricación aditiva
- Aleaciones de titanio para piezas aeroespaciales: resistencia y ligereza
- Aleaciones de cromo-cobalto para puentes dentales: resistencia, biocompatibilidad
- Acero para herramientas de moldes - alta dureza, estabilidad térmica
- Aleaciones de aluminio para automoción: ligereza y resistencia a la corrosión
Otras aplicaciones
- Bielas forjadas en polvo, engranajes - aleación de acero, aluminio
- Aleaciones de soldadura fuerte, pastas de soldadura - aleaciones de cobre, plata, níquel
- Aleaciones de recargue duro - hierro, cobalto, mezclas de carburo
Las composiciones de polvo de aleación permiten diseñar materiales para estas aplicaciones y condiciones de funcionamiento específicas.
Proveedores y costes de la aleación en polvo
Muchos de los principales proveedores de polvo metálico cuentan con amplios inventarios de polvo de aleación y capacidades de aleación personalizada. Estos son algunos de los principales proveedores mundiales de polvo de aleación atomizado con gas:
Compañía | Ubicación de la sede |
---|---|
Sandvik | Suecia |
Hoganas | Suecia |
Polvos metálicos de Río Tinto | Canadá |
Pometon | Italia |
Acero JFE | Japón |
BASF | Alemania |
CNPC Polvo | China |
El coste del polvo de aleación depende de la composición específica, las características del polvo, el tamaño del lote y la cantidad de compra. Algunos ejemplos de precios son:
Polvo de aleación | Coste aproximado (USD/kg) |
---|---|
Acero inoxidable | $12 – $60 |
Acero para herramientas | $9 – $30 |
Aleación de aluminio | $10 – $50 |
Aleación de cobre | $20 – $60 |
Aleación de cobalto | $80 – $220 |
Aleación de titanio | $100 – $500 |
Los precios varían mucho en función del tipo de aleación, la distribución del tamaño de las partículas, el método de producción (atomización con gas o con agua) y el volumen del pedido. Las aleaciones personalizadas cuestan más que las composiciones estándar. Los metales preciosos, como las aleaciones de cobalto y titanio, son más caros.
Cómo seleccionar un proveedor de aleaciones en polvo
Elegir un proveedor de polvo de aleación de confianza es fundamental para obtener materias primas de alta calidad. Estos son los factores clave a la hora de seleccionar un proveedor:
- Experiencia en la fabricación de la composición de aleación específica necesaria
- Pruebas rigurosas de control de calidad de cada lote de polvo
- Documentación de análisis químicos y características del polvo
- Inventario de composiciones estándar para una entrega rápida
- Posibilidad de personalizar la composición de la aleación según las necesidades
- Personal de asistencia técnica bien informado
- Precios competitivos, especialmente para grandes pedidos
- Disponibilidad para suministrar pequeñas cantidades de prueba
- Capacidad de respuesta a las consultas y solicitudes de presupuesto
- Reputación consolidada de coherencia y fiabilidad de los productos
El proveedor debe poder proporcionar un certificado de análisis que detalle la composición química, la distribución del tamaño de las partículas, la morfología, la densidad aparente, la velocidad de flujo y otras propiedades del polvo. También se recomienda probar muestras y validar el rendimiento real del polvo durante la cualificación inicial.
Cómo almacenar y manipular el polvo de aleación
El almacenamiento y la manipulación adecuados evitan la contaminación del polvo de aleación o cambios en sus propiedades. Las prácticas recomendadas incluyen:
- Almacenar los envases sellados en un ambiente fresco, seco y limpio, lejos de fuentes de humedad, aceites o vapores corrosivos.
- Limitar las fluctuaciones de temperatura durante el almacenamiento para evitar la condensación en el interior de los recipientes.
- Rotar las existencias para utilizar primero las más antiguas
- Proteger el polvo de la exposición al aire durante la manipulación para evitar la oxidación
- Evitar mezclar polvos de diferentes aleaciones o distribuciones de tamaño
- Manipule los recipientes con cuidado para evitar que se caigan y se derramen
- Utilice cucharas y equipos limpios y secos para transferir el polvo
- Cerrar los envases inmediatamente después de retirar el polvo
- Medir y registrar la masa de polvo eliminada para mantener un balance de materiales.
- Limpiar a fondo el equipo entre lotes de procesamiento para evitar la contaminación cruzada.
El cuidado en la manipulación, el almacenamiento y el mantenimiento de registros garantiza que el polvo de aleación conserve su forma, composición y propiedades para su posterior procesamiento.
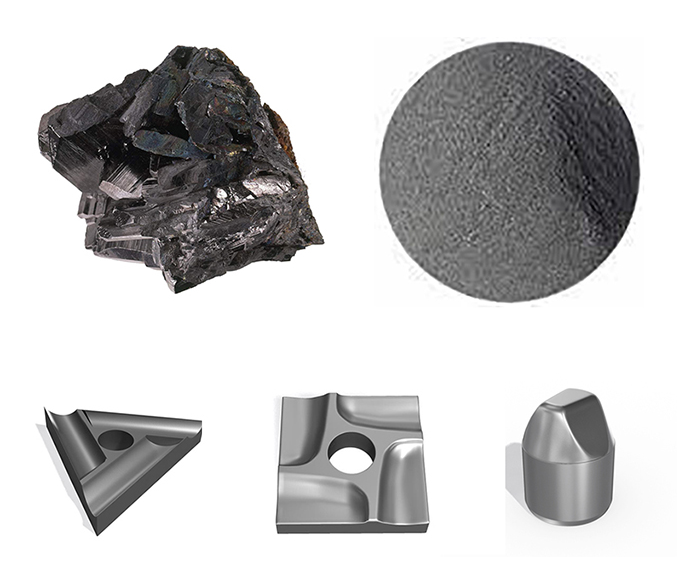
Consideraciones sobre el mantenimiento del polvo de aleación
Una vez puestos en servicio los componentes pulvimetalúrgicos de aleación, puede ser necesario un mantenimiento ocasional. Esta tabla enumera algunos aspectos de mantenimiento específicos de las aleaciones:
Consideración | Detalles |
---|---|
Corrosión galvánica | Las combinaciones de aleaciones disímiles pueden aumentar la corrosión si se humedecen. Evite ensamblar aleaciones disímiles en contacto directo. |
Corrosión bajo tensión | Las aleaciones sensibles, como el acero inoxidable austenítico, pueden agrietarse si se exponen a cloruros bajo tensión. Evite su uso en estas condiciones. |
Propiedades a temperaturas elevadas | La fuerza y la resistencia a la fluencia pueden disminuir en algunas aleaciones a temperaturas más altas. Compruebe que no se superan los límites de diseño. |
Resistencia de contacto | Pueden ser necesarios revestimientos conductores para evitar la caída de tensión en las interfaces entre las aleaciones de cobre y el acero. |
Bioincrustaciones | Las aleaciones de cobre resisten de forma natural la bioincrustación en entornos marinos. Otras aleaciones pueden requerir revestimientos protectores. |
Resistencia de las juntas | Las aleaciones de soldadura fuerte o blanda deben coincidir con la composición del material base para garantizar la integridad de la unión. |
Tenga en cuenta los factores medioambientales y las compatibilidades de las aleaciones cuando realice el mantenimiento de equipos que contengan componentes pulvimetalúrgicos de aleación. Puede ser necesario inspeccionar, lubricar, limpiar y apretar las juntas periódicamente.
Ventajas e inconvenientes de la aleación en polvo
El polvo de aleación tiene muchas ventajas, pero también algunos inconvenientes inherentes en relación con el polvo de metal puro:
Ventajas del polvo de aleación
- Propiedades a medida como fuerza, resistencia al desgaste, conductividad
- Más resistente a la corrosión que el hierro puro o el acero en polvo
- Menos propensos al gripado que los metales puros
- Puede reforzarse para aplicaciones de carga
- Opciones de alta dureza, tenacidad o biocompatibilidad
- Composición homogénea a partir de desechos de producción reciclados
Desventajas del polvo de aleación
- Mayor coste que los polvos de hierro, cobre o aluminio puros
- Número limitado de composiciones normalizadas disponibles
- El desarrollo de aleaciones personalizadas es caro y lleva mucho tiempo
- La segregación puede provocar desviaciones de la química nominal
- Los elementos reactivos como el cromo pueden oxidarse durante la atomización
- La reutilización del polvo es limitada, ya que las composiciones de las aleaciones no pueden entremezclarse.
- Los elementos de aleación pueden plantear problemas de procesamiento en P/M
Para muchas aplicaciones, las ventajas de las propiedades de las aleaciones a medida compensan el aumento del coste y la complejidad del procesamiento en comparación con los polvos metálicos puros. Pero es necesario evaluar la viabilidad cuando se sustituyen aleaciones en un diseño de pieza de P/M existente.
Polvo de aleación frente a polvo de acero prealeado
El polvo de aleación difiere del polvo de acero prealeado en su composición y producción:
Parámetro | Polvo de aleación | Polvo de acero prealeado |
---|---|---|
Composición básica | Varios sistemas metálicos, por ejemplo, acero inoxidable, acero para herramientas, aleaciones de níquel | Hierro o hierro + carbono (acero) |
Elementos de aleación | Uno o varios metales añadidos para adaptar las propiedades | Carbono + elementos de aleación traza como Mn, Ni, Mo |
Método de producción | Atomización de la aleación fundida | Premezcla de polvos de hierro y grafito |
Distribución de las aleaciones | Uniforme en toda la partícula de polvo | Elementos de aleación sólo en la superficie del polvo |
Estructura sinterizada | Homogéneo, fases formadas durante la solidificación | Heterogéneo, fases formadas durante la sinterización |
Coste | Mayor debido a las adiciones de aleación | Más bajo, ya que el carbono es barato |
El polvo de acero prealeado tiene un coste de producción más bajo, pero su contenido de aleación es limitado. El polvo de aleación tiene mayor flexibilidad de composición pero mayores gastos en materias primas. La elección de la composición depende del equilibrio entre las necesidades de rendimiento y los objetivos de coste de la aplicación.
Cómo afectan los elementos de aleación a las propiedades
Los distintos elementos de aleación influyen de diversas maneras en las propiedades pulvimetalúrgicas:
Elemento de aleación | Efectos clave |
---|---|
Carbono | Aumenta la resistencia y la dureza, pero reduce la ductilidad y la resistencia a la corrosión |
Cromo | Mejora la resistencia a la corrosión y la templabilidad de los aceros |
Níquel | Mejora la tenacidad, la resistencia a la tracción y las propiedades a temperaturas elevadas |
Molibdeno | Aumenta la resistencia a altas temperaturas, la resistencia a la fluencia y la templabilidad |
Manganeso | Aumenta la templabilidad y la resistencia a la tracción al tiempo que reduce el coste frente al níquel |
Silicio | Mejora la fluidez durante la sinterización pero disminuye la ductilidad y el acabado superficial |
Cobre | Refuerza los aceros de baja aleación y los bronces; también contribuye a la resistencia a la corrosión. |
Aluminio | Elemento de aleación ligero que aumenta la fuerza y la resistencia a la corrosión de los aceros. |
Vanadio | Formador de carburo fino para aumentar significativamente la resistencia al desgaste y la dureza |
Tungsteno | Forma carburos de wolframio muy duros para la resistencia a la abrasión en aceros para herramientas. |
Al comprender los efectos de cada adición, los ingenieros de materiales pueden modelar y optimizar las composiciones para conseguir las propiedades deseadas con el polvo de aleación. Pequeñas variaciones en el contenido de aleación pueden afectar significativamente al rendimiento.
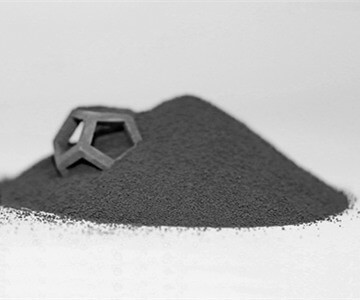
Consideraciones sobre el diseño con polvo de aleación
A la hora de diseñar piezas pulvimetalúrgicas con polvo de aleación deben tenerse en cuenta varios factores:
- Coste - Las adiciones de aleación aumentan el coste de la materia prima en comparación con el hierro puro o el acero en polvo. Equilibrar el rendimiento con las limitaciones presupuestarias.
- Tratamiento posterior al sinterizado - Las aleaciones deben ser compatibles con cualquier operación secundaria como el tratamiento térmico, el mecanizado, la soldadura o el acabado superficial.
- Resistencia a la corrosión - La composición de la aleación puede ajustarse para soportar el entorno de funcionamiento. Utilice acero inoxidable en el agua, por ejemplo.
- Propiedades mecánicas - La resistencia, dureza, resistencia al desgaste, etc. requeridas determinarán el sistema de aleación y la cantidad de carburos o fases de refuerzo.
- Control dimensional - Un mayor contenido de aleación puede aumentar la contracción por sinterización. Téngalo en cuenta en las dimensiones del utillaje.
- Capacidad técnica - Asegúrese de que el fabricante de P/M tiene experiencia con la composición de la aleación en cuestión.
- Integración parcial - El desajuste de aleaciones entre conjuntos puede provocar corrosión galvánica. Estandarice las familias de aleaciones siempre que sea posible.
La selección minuciosa de la aleación es esencial al principio del diseño para producir un componente pulvimetalúrgico robusto y competitivo en costes.
Ejemplos de aplicaciones de aleaciones en polvo
He aquí algunas aplicaciones ilustrativas del polvo de aleación en diversas industrias:
Automotor
- Árboles de levas - Fabricados a partir de polvo de acero sinterizado de baja aleación para obtener una gran solidez y resistencia al desgaste. La composición de la aleación está optimizada para la dureza y la resistencia a la fractura necesarias en el accionamiento de las válvulas del motor.
- Bielas - Forjadas o sinterizadas a partir de polvo de acero aleado para obtener la mayor resistencia a la tracción necesaria minimizando el peso. La aleación con níquel, molibdeno y otros elementos proporciona propiedades mecánicas adecuadas.
- Engranajes - El polvo de acero aleado con adiciones de cromo, níquel y molibdeno permite que los engranajes sinterizados de la cadena cinemática alcancen la resistencia a la fatiga y la tenacidad a la fractura necesarias bajo cargas cíclicas en automoción. La composición adaptada de la aleación reduce el desgaste.
- Ruedas de turbocompresor - Las superaleaciones de alto rendimiento, como Inconel 718, se utilizan en forma de polvo para la fabricación aditiva de ruedas de compresor de turbocompresor capaces de soportar tensiones centrífugas y temperaturas extremas. Esta aleación a base de níquel proporciona solidez y resistencia a la fluencia.
- Válvulas de motor - El polvo de una aleación de acero inoxidable que contiene cromo y níquel permite fabricar válvulas de escape resistentes a la corrosión que soportan el ataque de los gases de escape calientes durante largos periodos de funcionamiento. La aleación se mantiene fuerte y estable incluso a altas temperaturas.
- Discos de freno - A veces se incorpora polvo de aleación de cobre en las fórmulas de los discos de freno para mejorar la conductividad térmica, la amortiguación y la resistencia al desgaste sin añadir un peso excesivo. La mayor disipación del calor reduce el desvanecimiento en frenadas repetidas.
Las composiciones de aleaciones en polvo permiten optimizar las propiedades de los componentes de la cadena cinemática del automóvil, como la resistencia, la dureza, la resistencia a la corrosión, la resistencia a la fatiga y la estabilidad a altas temperaturas, mediante técnicas pulvimetalúrgicas.