Visión general del polvo de WC-12Co
WC-12Co en polvowC-12Co, abreviatura de polvo de carburo de tungsteno-cobalto, es un material especializado que se utiliza a menudo en revestimientos, fabricación y herramientas que requieren una resistencia extrema al desgaste, durabilidad y tenacidad. Conocido por su versatilidad y sus excepcionales propiedades mecánicas, el WC-12Co tiene importantes aplicaciones en sectores como el aeroespacial, la automoción, el petróleo y el gas, y la maquinaria pesada.
El carburo de wolframio (WC) mezclado con cobalto (Co) crea un compuesto robusto en el que el carburo de wolframio aporta dureza y el cobalto mejora la ductilidad. Los polvos de WC-12Co, que suelen utilizarse en revestimientos de pulverización térmica, son esenciales para superficies expuestas a abrasión, erosión y entornos de alta tensión.
Este artículo explora todo lo que necesita saber sobre el polvo de WC-12Co, incluida su composición, propiedades, aplicaciones, modelos, comparaciones y mucho más. Tanto si busca especificaciones técnicas, detalles sobre proveedores o información sobre rendimiento, esta guía le ofrece todo lo que necesita.
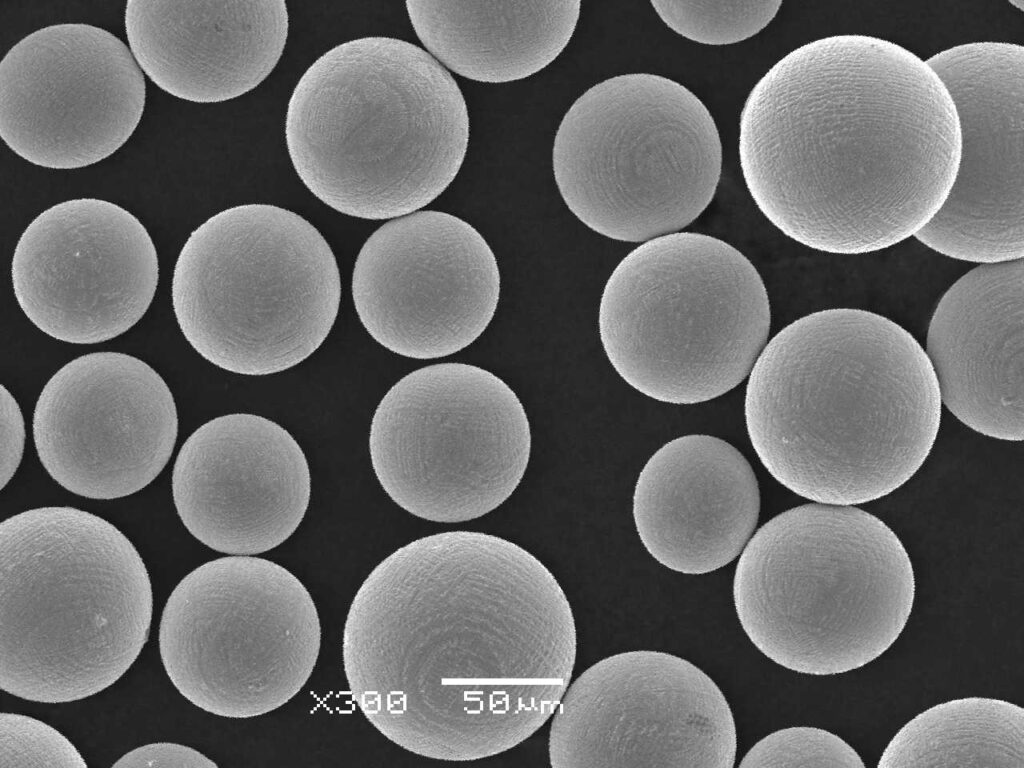
Composición de WC-12Co Polvo
Conocer la composición del material es vital, ya que influye en el comportamiento mecánico y químico del polvo.
Componente | Porcentaje | Propósito |
---|---|---|
Carburo de wolframio (WC) | 88% (en peso) | Proporciona dureza, resistencia a la abrasión |
Cobalto (Co) | 12% (en peso) | Añade ductilidad, tenacidad y adherencia |
Oligoelementos | <1% | Mejora las propiedades del polvo |
Información clave: La relación 88:12 WC-Co consigue un equilibrio entre dureza y flexibilidad, por lo que es superior para revestimientos resistentes al desgaste en comparación con alternativas como el WC-17Co.
Características del polvo de WC-12Co
El polvo de WC-12Co destaca por sus excepcionales propiedades. He aquí un desglose de sus características principales:
Propiedad | Detalles |
---|---|
Dureza | Hasta 1500 HV (dureza Vickers) |
Dureza | Excelente resistencia a la fractura gracias al cobalto |
Densidad | 14.2 - 14,6 g/cm³ |
Conductividad térmica | Alta estabilidad térmica en condiciones extremas |
Resistencia a la corrosión | Bueno, pero puede mejorarse con aditivos |
Resistencia al desgaste | Excelente para entornos de alta abrasión |
Gama de tamaños de partículas | 5 - 45 µm (micrómetros) |
Por qué es importante:
La combinación de dureza y tenacidad hace que el polvo de WC-12Co sea ideal para superficies sometidas a grandes esfuerzos o desgaste abrasivo. Piense en él como en un blindaje, pero a un micronivel: resistente, fuerte y capaz de soportar un castigo extremo.
Tipos y modelos de polvo de WC-12Co
Existen varios modelos y grados de polvo de WC-12Co, cada uno adaptado a necesidades industriales específicas. A continuación se indican 10 modelos populares con sus descripciones:
Modelo/Grado | Descripción |
---|---|
Amperit 558.074 | Polvo de WC-12Co de grano fino adecuado para revestimientos de precisión por pulverización térmica. |
Metco 73F-NS | Polvo aglomerado y sinterizado; ofrece una fluidez y densidad de recubrimiento superiores. |
Praxair WC-12Co | Diseñado para aplicaciones HVOF (High-Velocity Oxygen Fuel); excelente adherencia. |
H.C. Starck P811 | Polvo esférico con una distribución uniforme del tamaño de las partículas para obtener resultados uniformes. |
Oerlikon Woka 3652 | Polvo de WC-Co aglomerado con alta resistencia al desgaste; ideal para máquinas herramienta. |
Kennametal K2132 | Grado altamente resistente a la abrasión para aplicaciones industriales críticas. |
Thermico WSP-88/12 | Optimizado para resistir la erosión y la corrosión en entornos extremos. |
Sandvik 12Co Elite | Especializada en revestimientos por pulverización térmica de calidad aeroespacial. |
Fuji Tech WCT12 | Polvo WC-12Co de ingeniería japonesa para tolerancias finas y acabados suaves. |
Jinzhou TuoHai | Opción rentable para protección antidesgaste estándar y herramientas industriales. |
Cada modelo está adaptado a aplicaciones industriales únicas: algunos destacan en la pulverización térmica, mientras que otros son mejores para entornos abrasivos. La elección del modelo adecuado depende de las necesidades específicas de su proyecto.
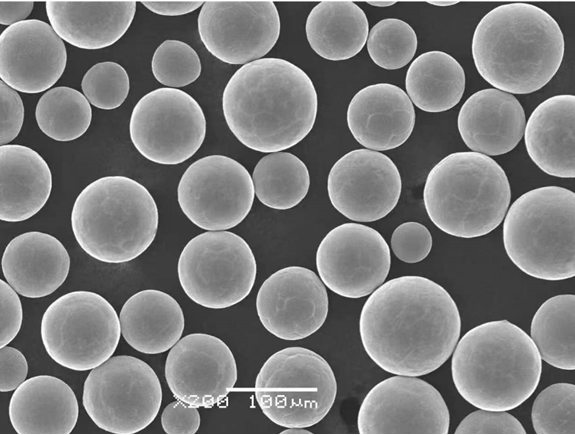
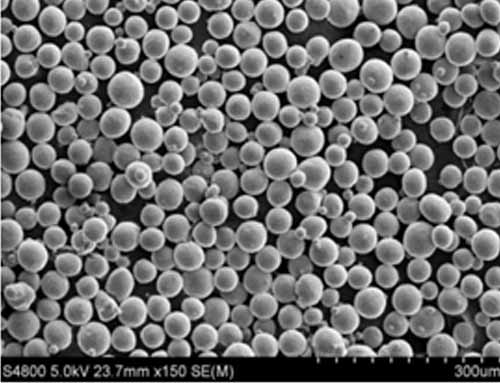
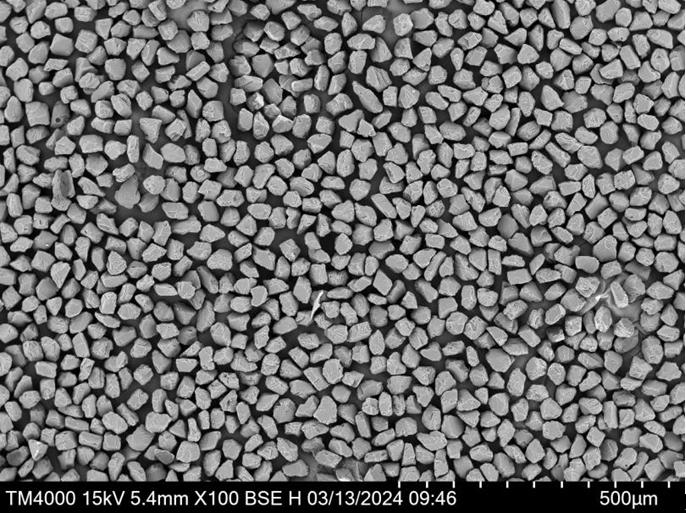
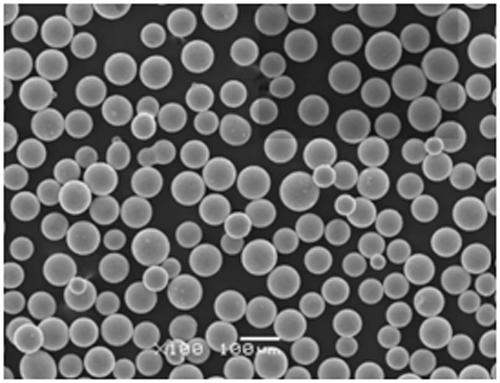
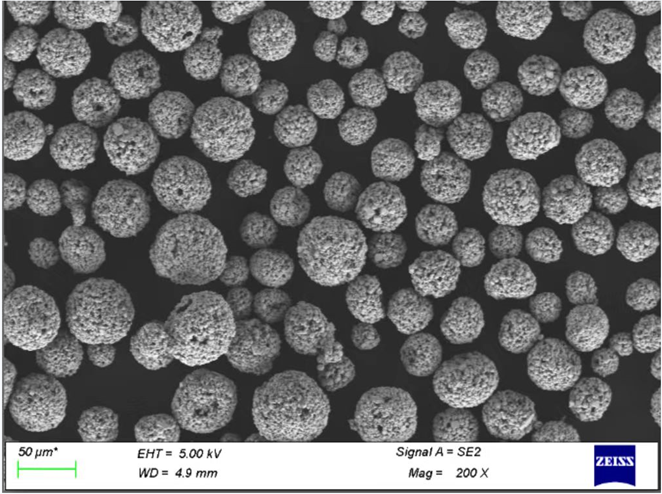
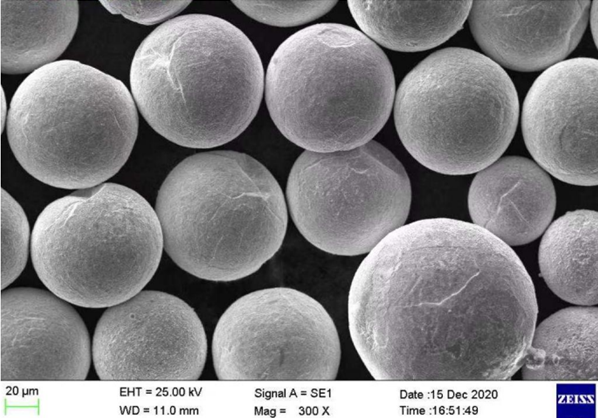
Aplicaciones de WC-12Co Polvo
El polvo de WC-12Co tiene diversas aplicaciones en distintos sectores. He aquí una instantánea de dónde brilla:
Industria | Solicitud |
---|---|
Aeroespacial | Revestimientos por pulverización térmica para álabes de turbina. |
Automotor | Componentes de motores, pistones y revestimientos de engranajes. |
Petróleo y gas | Brocas, asientos de válvulas y superficies resistentes a la erosión. |
Maquinaria pesada | Recubrimientos resistentes a la abrasión para piezas de maquinaria. |
Equipos de minería | Herramientas y fresas resistentes al desgaste. |
Defensa | Recubrimientos protectores para componentes sometidos a grandes esfuerzos. |
Generación de energía | Recubrimientos para turbinas de vapor y piezas hidroeléctricas. |
Ejemplo en acción:
Imagine una broca petrolífera sometida a una presión extrema y a un gran desgaste. Los revestimientos WC-12Co garantizan que estas herramientas no fallen prematuramente, ahorrando costes, tiempo y recursos.
Especificaciones, tamaños, calidades y normas
Especificación | Detalles |
---|---|
Tamaño de partícula | 5 - 45 µm |
Normas | ASTM B 777, ISO 1415, DIN EN 12716 |
Polvo | Aglomerados, sinterizados y esféricos |
Método de aplicación | HVOF, pulverización de plasma, pulverización en frío |
Proveedores y precios
Proveedor | Nombre del producto | Precios (USD/Kg) | Región |
---|---|---|---|
Oerlikon Metco | Woka 3652 | $75 - $120 | Global |
Kennametal | K2132 | $80 - $130 | Norteamérica |
Praxair Surface Tech | WC-12Co Polvo | $70 - $115 | Europa, Estados Unidos |
H.C. Starck | P811 | $85 - $125 | Global |
Fuji Tech | WCT12 | $65 - $105 | Asia-Pacífico |
Los precios varían en función del tamaño de las partículas, la forma y el volumen del pedido.
Ventajas y limitaciones del polvo de WC-12Co
Ventajas | Limitaciones |
---|---|
Dureza y tenacidad excepcionales | Coste relativamente elevado |
Excelente resistencia al desgaste y a la erosión | Resistencia limitada a la corrosión en ambientes ácidos |
Aplicación versátil en todos los sectores | Requiere técnicas de aplicación especializadas |
Rendimiento duradero | Peso pesado en comparación con otras alternativas |
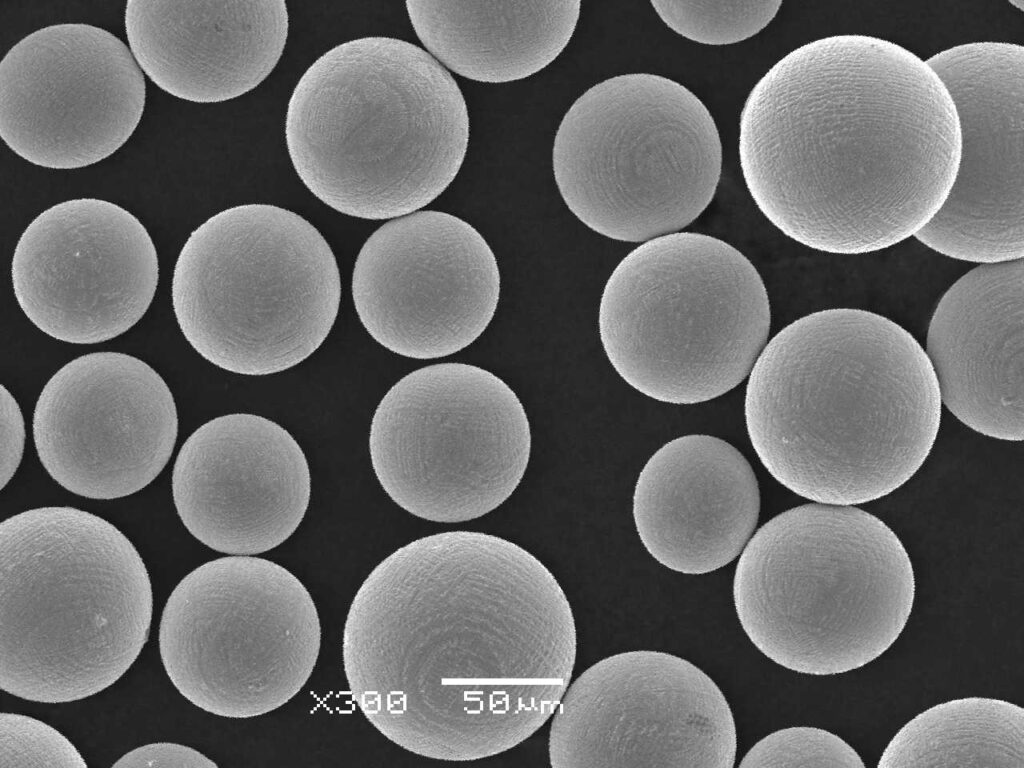
preguntas frecuentes
Pregunta | Respuesta |
---|---|
¿Para qué se utiliza el polvo de WC-12Co? | Principalmente para revestimientos resistentes al desgaste en entornos sometidos a grandes esfuerzos. |
¿Qué industrias utilizan revestimientos de WC-12Co? | Sectores aeroespacial, automoción, petróleo & gas, minería y defensa. |
¿Cuál es la dureza del polvo de WC-12Co? | Hasta 1500 HV (dureza Vickers). |
¿Cómo se aplica el polvo WC-12Co? | Mediante técnicas HVOF, pulverización por plasma o pulverización en frío. |
¿En qué se diferencia el WC-12Co del WC-17Co? | El WC-12Co ofrece mejor tenacidad, mientras que el WC-17Co ofrece una dureza ligeramente superior. |
Conclusión
WC-12Co en polvo es un material fundamental para aplicaciones que exigen durabilidad, solidez y resistencia al desgaste. Desde las turbinas aeroespaciales hasta las herramientas de minería, su equilibrio entre dureza y tenacidad garantiza un rendimiento inigualable. Elegir el modelo adecuado, conocer sus propiedades y aprovechar sus ventajas puede elevar la eficiencia y la longevidad industriales.