Descripción general del depósito de metales por láser (LMD)
Deposición de metales por láser (LMD) es una innovadora tecnología de fabricación aditiva (AM) que utiliza un láser de alta potencia para fundir y fusionar polvo o alambre metálico sobre un sustrato, capa a capa, para crear estructuras tridimensionales. Tanto si trabaja en el sector aeroespacial como en el de la automoción o la medicina, la LMD ofrece una solución sólida para piezas metálicas complejas que requieren precisión, durabilidad y eficiencia.
Imagine que necesita reparar un álabe de turbina desgastado o crear un implante a medida. Los métodos de fabricación tradicionales pueden ser demasiado lentos, costosos o, simplemente, poco precisos. El LMD entra en escena como un superhéroe, utilizando láseres para soldar polvos metálicos y darles la forma perfecta, capa a capa meticulosamente. ¿El resultado? Componentes muy precisos y resistentes que pueden incluso superar a los originales.
Pero, ¿cómo funciona? ¿Cuáles son los materiales utilizados? Y lo que es más importante, ¿cómo puede beneficiar a su negocio? En esta guía detallada, nos adentraremos en los entresijos del LMD, desde los polvos metálicos específicos que utiliza hasta sus pros y sus contras, pasando por una práctica sección de preguntas frecuentes para aclarar cualquier duda.
Abróchese el cinturón y explore el fascinante mundo del depósito de metales por láser.
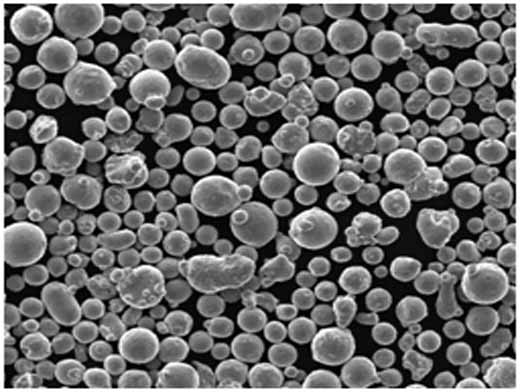
¿Qué es el depósito de metales por láser (LMD)?
LMD es un tipo de fabricación aditiva, también conocida como impresión 3D, en la que se añaden materiales en lugar de eliminarlos. El proceso consiste en utilizar un rayo láser focalizado para fundir polvo o alambre metálico, que luego se deposita sobre un sustrato. Esta tecnología permite un control preciso del material, lo que posibilita la creación de geometrías complejas y componentes metálicos de alto rendimiento.
¿Cómo funciona el depósito de metales por láser?
La deposición de metal por láser consiste en introducir polvo metálico a través de una boquilla en un rayo láser, que funde el polvo y lo fusiona con un material base (sustrato). A medida que el láser se mueve, va acumulando capas de metal para dar la forma deseada. Es como construir un muro, pero en lugar de ladrillos, se utilizan pequeños granos de metal, y en lugar de mortero, un láser de alta energía lo une todo.
- Fuente láser: El tipo y la potencia del láser determinan cómo se fundirá y solidificará el polvo metálico. Los láseres de fibra se utilizan habitualmente por su eficacia y precisión.
- Sistema de alimentación de polvo: Los polvos metálicos se introducen en el haz láser a través de una boquilla. La consistencia del flujo de polvo es crucial para conseguir capas uniformes.
- Control de movimiento: El movimiento del láser y del sistema de alimentación de polvo se controla con precisión, a menudo con sistemas CNC o robóticos, para crear la geometría deseada.
Esta precisión significa que el LMD no se limita a fabricar piezas nuevas. También puede reparar las existentes añadiendo material donde sea necesario, lo que resulta especialmente útil para componentes caros en industrias como la aeroespacial.
Aplicaciones de Deposición de metales por láser (LMD)
El depósito de metal por láser es un proceso versátil con una amplia gama de aplicaciones en diversos sectores. Desde la reparación de componentes de alto valor hasta la creación de piezas complejas de diseño personalizado, el LMD está causando sensación en la fabricación.
Aplicaciones clave:
Industria | Solicitud | Beneficios |
---|---|---|
Aeroespacial | Reparación de álabes de turbina, componentes de motor | Reducción de los tiempos de inactividad y prolongación de la vida útil de las piezas |
Automotor | Reparación de engranajes y cigüeñales, piezas a medida | Rendimiento mejorado, producción rentable |
Médico | Implantes a medida, componentes dentales | Alta precisión, biocompatibilidad |
Herramientas | Reparación de moldes, restauración de troqueles | Mayor vida útil de las herramientas, menor plazo de entrega |
Petróleo y gas | Asientos de válvulas, componentes de perforación | Resistencia a entornos agresivos, coste de sustitución reducido |
Generación de energía | Reparación de turbinas, fabricación de componentes | Mayor eficacia y menores costes de mantenimiento |
Defensa | Componentes de armamento, reparación de equipos críticos | Alta resistencia, durabilidad en condiciones extremas |
Energía | Componentes de turbinas eólicas, piezas de reactores nucleares | Sostenibilidad, alto rendimiento en operaciones críticas |
Construcción | Componentes estructurales a medida, reparación de maquinaria pesada | Resistencia, flexibilidad y rentabilidad |
Marina | Reparación de hélices, componentes de motores navales | Resistencia a la corrosión, longevidad en entornos marinos |
Cada una de estas industrias tiene requisitos únicos, y la flexibilidad de LMD le permite satisfacerlos todos con facilidad. Ya se trate de los materiales de alta resistencia necesarios para la industria aeroespacial o de los metales biocompatibles utilizados en implantes médicos, LMD puede encargarse de todo.
Polvos metálicos específicos utilizados en LMD
La elección del polvo metálico es crucial en LMD, ya que afecta directamente a la calidad, durabilidad y funcionalidad del producto final. A continuación, exploramos algunos de los polvos metálicos específicos que se utilizan habitualmente en LMD, junto con sus composiciones y características.
Los 10 mejores polvos metálicos para LMD:
Polvo metálico | Composición | Propiedades | Caracteristicas |
---|---|---|---|
Inconel 625 | Aleación de níquel-cromo-molibdeno-niobio | Alta resistencia, excelente resistencia a la corrosión | Utilizado en la industria aeroespacial, naval y química |
Titanio Ti-6Al-4V | Aleación de titanio-aluminio-vanadio | Elevada relación resistencia/peso, biocompatibilidad | Ideal para implantes médicos, aeroespacial |
Acero inoxidable 316L | Aleación de hierro, cromo, níquel y molibdeno | Resistencia a la corrosión, buenas propiedades mecánicas | Común en las industrias médica y alimentaria |
Cromo-cobalto (Co-Cr) | Aleación de cobalto-cromo | Resistencia al desgaste, biocompatibilidad | Utilizado en implantes dentales y ortopédicos |
Aluminio AlSi10Mg | Aleación de aluminio, silicio y magnesio | Ligero, buenas propiedades térmicas | Popular en aplicaciones aeroespaciales y de automoción |
Hastelloy X | Aleación de níquel, cromo, hierro y molibdeno | Resistencia al calor, resistencia a la oxidación | Adecuado para entornos de alta temperatura |
Acero martensítico envejecido 18Ni300 | Aleación de níquel-cobalto-molibdeno-titanio | Resistencia ultra alta, buena tenacidad | Utilizado en utillaje, aeroespacial |
Níquel 718 | Aleación de níquel, cromo y hierro | Alta resistencia a la tracción, resistencia a la fluencia | Ampliamente utilizado en motores de turbina, aeroespacial |
Acero para herramientas H13 | Aleación de cromo, molibdeno y vanadio | Gran dureza, resistencia al desgaste | Ideal para herramientas, moldes de fundición a presión |
Cobre-CrZr | Aleación de cobre, cromo y circonio | Excelente conductividad térmica, resistencia | Utilizado en intercambiadores de calor, componentes eléctricos |
Estos polvos metálicos se eligen cuidadosamente en función de los requisitos específicos de la aplicación, incluidos factores como la fuerza, la resistencia a la corrosión y la biocompatibilidad.
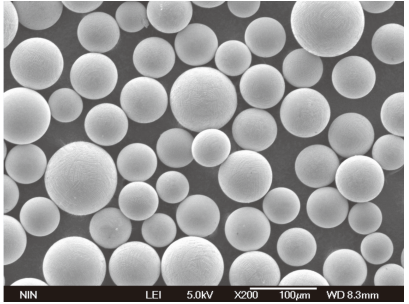
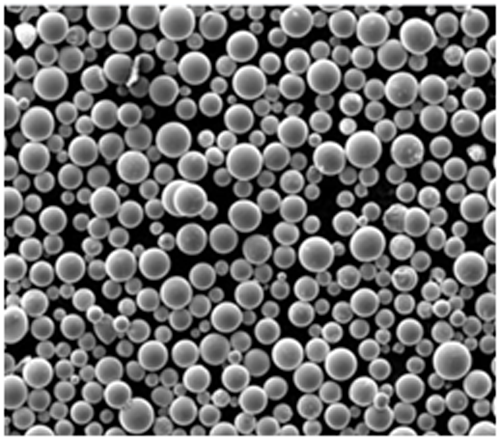
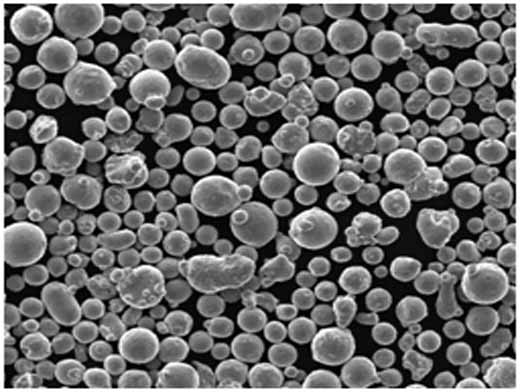
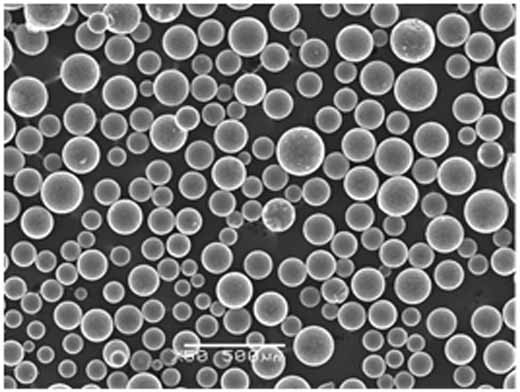
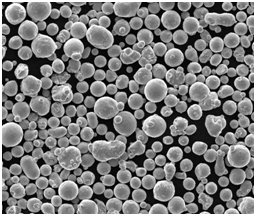
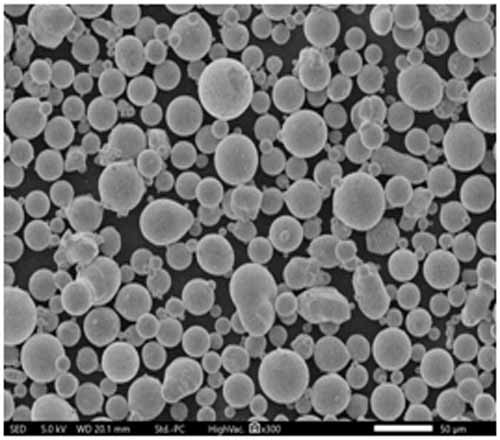
Propiedades y características de Deposición de metales por láser (LMD)
Comprender las propiedades y características del LMD es esencial para apreciar plenamente sus capacidades y posibles limitaciones. Desglosemos estos aspectos para hacernos una idea más clara de lo que hace funcionar a LMD.
Propiedades del material:
Propiedad | Descripción |
---|---|
Densidad | Los componentes LMD suelen tener una alta densidad, comparable a la de las piezas forjadas. |
Microestructura | Se pueden conseguir microestructuras finas, lo que se traduce en una gran resistencia y tenacidad. |
Acabado superficial | El acabado superficial puede variar en función del polvo y de los parámetros del proceso, por lo que a menudo es necesario un tratamiento posterior. |
Porosidad | Se puede conseguir una porosidad mínima con parámetros optimizados, aunque esto puede variar en función del material y la aplicación. |
Tensiones residuales | El LMD puede introducir tensiones residuales, que puede ser necesario aliviar mediante tratamiento térmico. |
Características del proceso:
Característica | Detalles |
---|---|
Grosor de la capa | Normalmente oscila entre 50 y 500 micras, dependiendo de la aplicación. |
Tasa de deposición | Oscila entre 0,5 y 3 kg/hora, en función del material y de la potencia del láser. |
Precisión | Alta precisión con tolerancias del orden de ±0,1 mm o mejores. |
Flexibilidad | Capaz de manejar geometrías complejas y múltiples materiales en una sola construcción. |
Escalabilidad | Adecuado para componentes pequeños y grandes, desde prototipos hasta producción. |
La combinación de estas propiedades y características convierte al LMD en una potente herramienta para fabricar y reparar componentes metálicos de alto rendimiento.
Ventajas y limitaciones del depósito de metales por láser (LMD)
Como cualquier proceso de fabricación, el LMD tiene sus puntos fuertes y débiles. He aquí un desglose de las ventajas y limitaciones que le ayudará a determinar si el LMD se ajusta a sus necesidades.
Ventajas:
Ventaja | Explicación |
---|---|
Precisión y exactitud | LMD puede producir componentes muy detallados con tolerancias muy ajustadas. |
Eficiencia material | La generación de residuos es mínima, lo que la convierte en una opción rentable. |
Versatilidad | Capaz de procesar una amplia gama de materiales, incluidos metales difíciles de mecanizar. |
Capacidad de reparación | LMD destaca en la reparación de componentes de alto valor, prolongando su vida útil y reduciendo el tiempo de inactividad. |
Personalización | Fácilmente personalizable para pequeñas series o piezas a medida. |
Limitaciones:
Limitación | Explicación |
---|---|
Costes iniciales elevados | Los costes de equipamiento y puesta en marcha pueden ser importantes, lo que supone una inversión considerable. |
Acabado superficial | A menudo requiere un tratamiento posterior para conseguir una superficie lisa. |
Complejidad de la operación | Requiere operarios cualificados y un control preciso de los parámetros. |
Zonas afectadas por el calor | El láser puede introducir zonas afectadas por el calor que pueden alterar las propiedades del material. |
Limitaciones materiales | No todos los materiales son adecuados para el LMD, especialmente los que tienen una baja absorción del láser. |
Comprender estos pros y contras le ayudará a tomar una decisión informada cuando considere la LMD para sus necesidades de fabricación.
Parámetros del proceso que influyen en el depósito de metales por láser (LMD)
La calidad de los componentes fabricados mediante deposición de metales por láser depende en gran medida de varios parámetros del proceso. Estos parámetros deben controlarse cuidadosamente para garantizar las propiedades mecánicas deseadas, el acabado superficial y el rendimiento general del producto final.
Parámetros clave del proceso:
Parámetro | Descripción | Influencia en el producto final |
---|---|---|
Potencia láser | La cantidad de energía proporcionada por el láser, que suele medirse en vatios. | Una mayor potencia aumenta la velocidad de deposición, pero puede provocar un sobrecalentamiento. |
Velocidad de exploración | La velocidad a la que el láser se desplaza por el sustrato. | Las velocidades más rápidas pueden reducir el aporte de calor, pero pueden provocar una fusión incompleta. |
Velocidad de alimentación de polvo | La velocidad a la que se suministra el polvo metálico al baño de fusión. | Las tasas más altas aumentan la eficacia de la deposición, pero pueden provocar porosidad si no se controlan. |
Flujo de gas de protección | El caudal de gas inerte utilizado para proteger el baño de fusión de la oxidación. | Un blindaje adecuado evita la oxidación y la contaminación. |
Tamaño del punto láser | El diámetro del haz láser sobre el sustrato. | Un tamaño de punto más pequeño mejora la precisión, pero puede ralentizar el proceso. |
Ratio de solapamiento | El grado de solapamiento entre pasadas láser adyacentes. | Un solapamiento mayor garantiza la uniformidad, pero puede aumentar el tiempo de procesamiento. |
Precalentamiento del sustrato | La temperatura del sustrato antes de que comience la deposición. | El precalentamiento reduce las tensiones residuales y el agrietamiento. |
Cada uno de estos parámetros desempeña un papel fundamental a la hora de determinar la calidad y consistencia del proceso LMD. Por ejemplo, una potencia láser o una velocidad de escaneado inadecuadas pueden provocar defectos como porosidad, grietas o una mala adhesión entre capas.
Optimización de los parámetros LMD para obtener los mejores resultados
Para obtener los mejores resultados con LMD, es fundamental optimizar estos parámetros para cada aplicación y material específicos. Esto suele implicar una combinación de experimentación y simulación para encontrar el punto óptimo en el que el proceso sea eficiente y produzca piezas de alta calidad.
Por ejemplo, cuando se trabaja con una aleación de alta resistencia como Inconel 625, es esencial controlar la potencia del láser y la velocidad de exploración para evitar el sobrecalentamiento, que puede provocar cambios microestructurales no deseados. Por el contrario, cuando se utiliza un material más tolerante, como el acero inoxidable 316L, la atención se centra más en optimizar la velocidad de alimentación del polvo y el flujo de gas de protección para maximizar la eficacia de la deposición.
Materiales avanzados utilizados en el depósito de metales por láser
Además de los polvos metálicos comunes enumerados anteriormente, LMD también puede trabajar con materiales más especializados. Estos materiales avanzados se utilizan en aplicaciones en las que los metales estándar podrían no cumplir los criterios de rendimiento necesarios, como temperaturas extremas, entornos corrosivos o requisitos mecánicos específicos.
Polvos metálicos avanzados adicionales para LMD:
Polvo metálico | Composición | Propiedades | Caracteristicas |
---|---|---|---|
Aleación de níquel 263 | Aleación de níquel-cromo-cobalto-molibdeno | Resistencia a altas temperaturas y a la oxidación | Ideal para álabes de turbina, camisas de combustión |
Haynes 282 | Aleación de níquel-hierro-cromo-molibdeno-titanio | Alta resistencia a la fluencia, excelente soldabilidad | Se utiliza en la industria aeroespacial y la generación de energía |
Tántalo (Ta) | Tántalo puro | Excelente resistencia a la corrosión, biocompatibilidad | Adecuado para procesos químicos y productos sanitarios |
Niobio (Nb) | Niobio puro | Alto punto de fusión, buenas propiedades superconductoras | Utilizado en superconductores, componentes aeroespaciales |
Tungsteno (W) | Tungsteno puro | Punto de fusión extremadamente alto, alta densidad | Ideal para aplicaciones de alta temperatura |
Inconel 738 | Aleación de níquel-cromo-cobalto-aluminio | Excepcional resistencia a la oxidación, alta resistencia | Utilizado en componentes de turbinas de gas de sección caliente |
René 41 | Aleación de níquel-cromo-cobalto-aluminio | Resistencia superior a altas temperaturas y a la oxidación | Común en la industria aeroespacial, turbinas de gas |
Ti-5553 | Aleación de titanio-aluminio-molibdeno-vanadio-cromo | Alta resistencia, tenacidad, buena resistencia a la corrosión | Utilizado en aplicaciones aeroespaciales y militares |
Aleación de cobalto Stellite 6 | Aleación de cobalto-cromo-tungsteno-carbono | Excelente resistencia al desgaste, buena resistencia a la corrosión | Ideal para asientos de válvulas, herramientas de corte |
Ni-Cr-B-Si (Colmonoy 88) | Aleación de níquel-cromo-boro-silicio | Dureza, resistencia al desgaste, buena resistencia a la corrosión | Utilizado en revestimiento de superficies, aplicaciones de reparación |
Estos materiales avanzados se eligen por sus propiedades únicas, que los hacen idóneos para aplicaciones muy exigentes. Por ejemplo, la excelente resistencia a la corrosión del tántalo lo hace ideal para equipos de procesamiento químico, mientras que el punto de fusión extremo del tungsteno lo convierte en la mejor opción para componentes expuestos a temperaturas muy elevadas.
Comparación de materiales avanzados
La comparación de estos materiales avanzados revela cómo determinadas aleaciones pueden superar a otras en determinadas condiciones, lo que las hace más adecuadas para aplicaciones concretas.
Material | Fuerza | Resistencia a la temperatura | Resistencia a la corrosión | Resistencia al desgaste | Idoneidad de la aplicación |
---|---|---|---|---|---|
Aleación de níquel 263 | Alta | Excelente | Moderado | Bien | Turbinas, componentes de alta temperatura |
Tantalio | Moderado | Alta | Excelente | Moderado | Procesamiento químico, productos sanitarios |
Tungsteno | Extremadamente alto | Destacado | Moderado | Excelente | Aplicaciones de alta temperatura, aeroespacial |
Aleación de cobalto Stellite 6 | Moderado | Bien | Bien | Excelente | Herramientas de corte, asientos de válvulas |
Inconel 738 | Muy alta | Excelente | Bien | Moderado | Componentes de turbinas de gas, aeroespacial |
Estas comparaciones pueden ayudar a los fabricantes a elegir el material adecuado en función de sus necesidades específicas, equilibrando factores como la solidez, la resistencia a la temperatura y el coste.
Aplicaciones de materiales avanzados en LMD
El uso de materiales avanzados en LMD amplía su aplicabilidad a campos altamente especializados en los que fallarían los métodos de fabricación o los materiales tradicionales. Estos materiales pueden cumplir requisitos estrictos, ofreciendo un mayor rendimiento, longevidad y fiabilidad en aplicaciones críticas.
Aplicaciones especializadas:
Industria | Solicitud | Material utilizado | Ventajas |
---|---|---|---|
Aeroespacial | Camisas de cámara de combustión, álabes de turbina | Aleación de níquel 263, Haynes 282 | Resistencia a altas temperaturas, excelentes propiedades mecánicas |
Médico | Implantes a medida, herramientas quirúrgicas | Tántalo, Cobalto-Cromo (Co-Cr) | Biocompatibilidad, resistencia a la corrosión |
Energía | Componentes de reactores nucleares, ejes de turbinas eólicas | Tungsteno, René 41 | Resistencia a la radiación, resistencia bajo tensión |
Defensa | Vehículos blindados, material militar | Ti-5553, Tungsteno | Alta resistencia, tenacidad y reducción de peso |
Automotor | Componentes de motores de alto rendimiento, intercambiadores de calor | Inconel 738, Titanio Ti-6Al-4V | Resistencia al calor, solidez, peso reducido |
Petróleo y gas | Herramientas de fondo de pozo, asientos de válvulas | Aleación de cobalto Stellite 6, Ni-Cr-B-Si | Resistencia al desgaste, durabilidad en entornos difíciles |
Electrónica | Componentes semiconductores, disipadores de calor | Niobio, Tungsteno | Conductividad térmica, capacidad para altas temperaturas |
Cada aplicación se beneficia de las propiedades específicas de los materiales avanzados utilizados. Por ejemplo, en la industria aeroespacial, la resistencia a altas temperaturas de la aleación de níquel 263 garantiza que los álabes de las turbinas mantengan su integridad incluso en condiciones de funcionamiento extremas.
Normas y especificaciones para materiales LMD
Al seleccionar los materiales para Deposición de metales por láserEl cumplimiento de las normas y especificaciones industriales es esencial para garantizar la calidad, el rendimiento y la seguridad. Los distintos sectores tienen requisitos específicos que deben cumplir los materiales, y estas normas guían el proceso de selección.
Normas industriales para materiales LMD:
Material | Norma/Especificación | Industria | Requisitos clave |
---|---|---|---|
Inconel 625 | ASTM B443, AMS 5599 | Aeroespacial, petróleo y gas | Alta temperatura, resistencia a la corrosión, propiedades mecánicas |
Titanio Ti-6Al-4V | ASTM F136, AMS 4911 | Medicina, aeroespacial | Biocompatibilidad, resistencia mecánica, resistencia a la fatiga |
Acero inoxidable 316L | ASTM A240, ISO 5832-1 | Medicina, procesamiento de alimentos | Resistencia a la corrosión, propiedades mecánicas |
Cromo-cobalto (Co-Cr) | ASTM F75, ISO 5832-4 | Médico | Resistencia al desgaste, biocompatibilidad |
Tungsteno (W) | ASTM B777, MIL-T-21014 | Defensa, Aeroespacial | Alta densidad, resistencia a altas temperaturas |
Aluminio AlSi10Mg | ASTM B209, EN 485 | Automoción, aeroespacial | Ligero, buena conductividad térmica |
Aleación de níquel 263 | AMS 5872, ASTM B637 | Aeroespacial | Resistencia a la oxidación, alta resistencia a temperaturas elevadas |
René 41 | AMS 5545, ASTM B435 | Aeroespacial | Propiedades mecánicas a altas temperaturas |
Niobio (Nb) | ASTM B392, AMS 7850 | Electrónica, aeroespacial | Superconductividad, estabilidad térmica |
Tántalo (Ta) | ASTM B708, AMS 7831 | Medicina, procesamiento químico | Resistencia a la corrosión, biocompatibilidad |
Estas normas garantizan que los materiales utilizados en LMD son de calidad constante y cumplen los criterios de rendimiento necesarios para sus aplicaciones previstas. Por ejemplo, la norma ASTM F136 garantiza que el titanio Ti-6Al-4V utilizado en implantes médicos es seguro y eficaz para su uso a largo plazo en el cuerpo humano.
Elección del polvo metálico adecuado para el depósito de metales por láser
La selección del polvo metálico adecuado es un paso fundamental en el proceso de LMD. La elección del polvo afecta directamente a la calidad, el rendimiento y el coste del producto final. Factores como las propiedades del material, los requisitos de la aplicación y los costes influyen en el proceso de toma de decisiones.
Factores a tener en cuenta:
Factor | Descripción | Impacto en la selección |
---|---|---|
Requisitos de solicitud | Las necesidades específicas del producto final, incluidas las propiedades mecánicas, las condiciones ambientales y la vida útil. | Dicta la selección de materiales en función de criterios de rendimiento. |
Propiedades de los materiales | Propiedades como el punto de fusión, la conductividad térmica y la resistencia. | Determina los parámetros del proceso y la calidad final de la pieza. |
Morfología de polvo | La forma y la distribución del tamaño de las partículas de polvo. | Afecta a la fluidez, la densidad de empaquetamiento y la uniformidad de la capa. |
Consideraciones económicas | El coste del polvo metálico en relación con el presupuesto del proyecto. | Equilibra el rendimiento material con la viabilidad económica. |
Disponibilidad de proveedores | La disponibilidad del polvo metálico de proveedores fiables. | Garantiza un suministro y una calidad constantes para la producción. |
Cumplimiento de las normas | Cumplimiento de las normas y especificaciones del sector. | Garantiza la calidad y la seguridad del producto final. |
Tomar una decisión informada sobre el polvo metálico requiere un equilibrio entre los requisitos técnicos y el coste. Por ejemplo, aunque el tungsteno ofrece una resistencia superior a la temperatura, también es más caro que otras opciones como el acero inoxidable 316L, lo que lo hace más adecuado para aplicaciones de gama alta en las que el rendimiento justifica el coste.
Proveedores y precios de los polvos metálicos LMD
Obtener el polvo metálico adecuado de un proveedor fiable es crucial para el éxito de la LMD. Los proveedores ofrecen una amplia gama de polvos con precios variables en función de factores como la composición del material, la pureza y la distribución del tamaño de las partículas.
Principales proveedores y precios:
Proveedor | Polvo metálico | Gama de precios (por kg) | Características especiales |
---|---|---|---|
Tecnología Carpenter | Aleación de níquel 263, Haynes 282 | $300 – $500 | Polvos de grado aeroespacial de alta calidad, tamaño de partícula consistente. |
Höganäs AB | Acero inoxidable 316L, Inconel 625 | $50 – $200 | Amplia gama de aleaciones, excelente fluidez. |
Tecnología LPW | Titanio Ti-6Al-4V, Aluminio AlSi10Mg | $250 – $450 | Polvos personalizados, estricto control de calidad para la fabricación aditiva. |
Oerlikon Metco | Aleación de cobalto Stellite 6, Rene 41 | $400 – $600 | Polvos de alto rendimiento, optimizados para la resistencia al desgaste. |
AP&C (Aditivo GE) | Ti-5553, Tántalo | $500 – $800 | Polvos de grado aeroespacial y médico, biocompatibilidad. |
Sandvik | Inconel 738, Tungsteno | $200 – $700 | Aleaciones de alta temperatura, pruebas exhaustivas y certificación. |
Tecnología de polvos Praxis | Niobio, Cobalto-Cromo (Co-Cr) | $300 – $600 | Polvos especializados para aplicaciones médicas y electrónicas. |
Aditivos GKN | Aleación de níquel 263, Haynes 282 | $300 – $500 | Mezclas de polvo personalizadas, excelente resistencia a la oxidación. |
Tekna | Aluminio AlSi10Mg, acero inoxidable 316L | $50 – $150 | Polvos esféricos, optimizados para la fabricación aditiva. |
VIGA | Tantalio, wolframio | $500 – $900 | Polvos de gran pureza, adaptados a aplicaciones específicas. |
Los precios varían mucho según el material y el proveedor, reflejando las diferencias de pureza, método de producción y demanda del mercado. Por ejemplo, los polvos de tantalio y wolframio se sitúan en el extremo superior del espectro de precios debido a su complejo procesamiento y a su gran demanda en industrias especializadas.
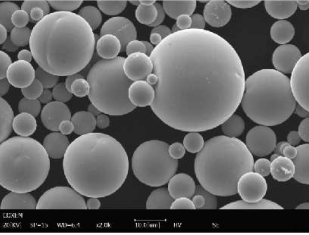
Comparación de Deposición de metales por láser a otras técnicas de fabricación aditiva
El depósito de metal por láser es sólo una de las muchas técnicas de fabricación aditiva disponibles en la actualidad. Comprender cómo se compara LMD con otros métodos puede ayudarle a elegir el mejor proceso para sus necesidades específicas.
Comparación con otras técnicas de fabricación aditiva:
Técnica | Flexibilidad del material | Acabado superficial | Velocidad | Precisión | Coste | Aplicaciones |
---|---|---|---|---|---|---|
Deposición de metales por láser | Alta | Moderado | Medio | Alta | Alta | Aeroespacial, reparación, geometrías complejas |
Sinterización selectiva por láser (SLS) | Alta | Moderado | Medio | Alta | Moderado | Creación de prototipos, producción de pequeños lotes |
Fusión por haz de electrones (EBM) | Medio | Moderado | Medio | Alta | Alta | Aeroespacial, implantes médicos |
Modelado por deposición fundida (FDM) | Bajo | Bajo | Alta | Bajo | Bajo | Prototipos, productos de consumo |
Sinterización directa de metales por láser (DMLS) | Alta | Alta | Medio | Muy alta | Alta | Medicina, aeroespacial, piezas complejas |
Chorro aglomerante | Medio | Bajo | Alta | Medio | Moderado | Piezas grandes, moldes de fundición |
Deposición de energía dirigida (DED) | Alta | Moderado | Medio | Alta | Alta | Reparación, grandes componentes, aeroespacial |
El LMD destaca por su capacidad para trabajar con una amplia gama de materiales y su precisión a la hora de crear geometrías complejas. Sin embargo, suele ser más caro y lento en comparación con otras técnicas como la FDM, más adecuada para la creación rápida de prototipos con requisitos de material menos exigentes.