لمحة عامة
ترسيب الطاقة الموجهة (DED) هي تقنية تصنيع مضافة متطورة تقوم بترسيب المواد بدقة، طبقة تلو الأخرى، لإنشاء أجزاء معدنية عالية الجودة. وتستخدم مصادر طاقة مركزة مثل أشعة الليزر أو أشعة الإلكترون أو أقواس البلازما لإذابة المواد، ثم يتم ترسيبها على ركيزة أو جزء موجود. تشتهر تقنية DED بقدرتها على إنتاج أشكال هندسية معقدة وإصلاح المكونات التالفة وإنشاء أجزاء معدنية عالية الأداء ذات خصائص ميكانيكية فائقة.
تُستخدم تقنية DED على نطاق واسع في العديد من الصناعات، بما في ذلك صناعة الطيران والسيارات والطب والطاقة، نظرًا لتعدد استخداماتها وكفاءتها. وتوفر هذه التقنية مزايا كبيرة مقارنةً بطرق التصنيع التقليدية، مثل تقليل هدر المواد، وأوقات إنتاج أقصر، والقدرة على إنشاء تصميمات معقدة يصعب تحقيقها بخلاف ذلك.
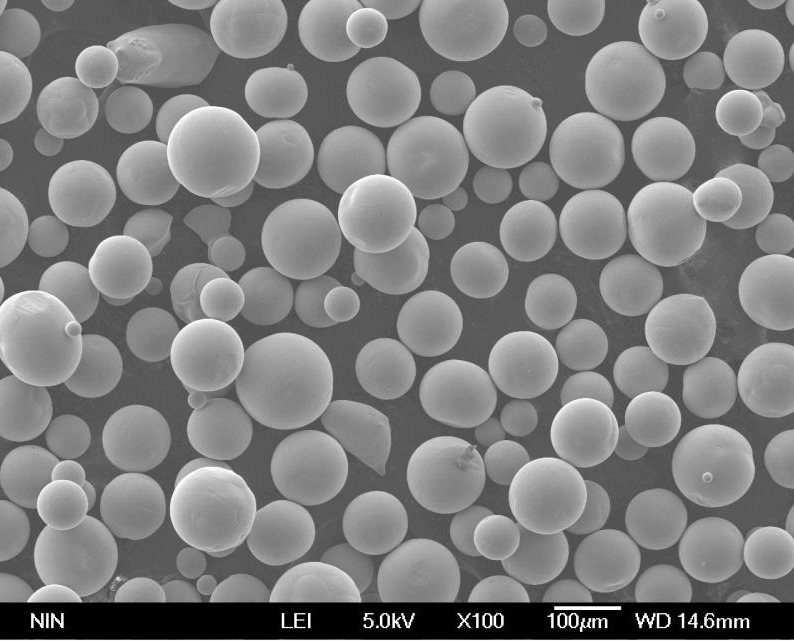
أنواع المساحيق المعدنية المستخدمة في DED
المساحيق المعدنية الشائعة ل DED
نموذج المسحوق المعدني | التركيب | الخصائص | التطبيقات |
---|---|---|---|
انكونيل 625 | النيكل والكروم والموليبدينوم والموليبدينوم | متانة عالية ومقاومة للتآكل | الفضاء الجوي والبحري والمعالجة الكيميائية |
Ti-6Al-4V | التيتانيوم، والألومنيوم، والفاناديوم | نسبة قوة إلى وزن عالية، متوافقة حيوياً | الفضاء، والغرسات الطبية، والسيارات |
فولاذ مقاوم للصدأ 316L | الحديد، الكروم، النيكل، النيكل، الموليبدينوم | مقاومة عالية للتآكل، وخصائص ميكانيكية جيدة | معالجة الأغذية، والأجهزة الطبية، والتطبيقات البحرية |
هاستيلوي إكس | النيكل، الموليبدينوم، الكروم | مقاوم للأكسدة ومقاوم لدرجات الحرارة العالية | الفضاء، التوربينات الغازية الصناعية |
CoCrMo | الكوبالت، والكروم، والموليبدينوم | مقاومة للاهتراء وقوة عالية | الغرسات الطبية، والأطراف الصناعية للأسنان |
AlSi10 ملغ | الألومنيوم والسيليكون والمغنيسيوم | خفيف الوزن وموصلية حرارية جيدة | السيارات، والفضاء، والإلكترونيات |
فولاذ مارينج (18Ni-300) | الحديد، والنيكل، والنيكل، والكوبالت، والموليبدينوم | قوة عالية وصلابة ممتازة | الأدوات، والفضاء، وقطع الغيار عالية الأداء |
النحاس | نحاس نقي | توصيل حراري وكهربائي ممتاز | المكونات الكهربائية، المبادلات الحرارية |
فولاذ الأدوات (H13) | الحديد، الكروم، الموليبدينوم، الموليبدينوم، الفاناديوم | صلابة عالية، مقاومة جيدة للإجهاد الحراري | تصنيع الأدوات، وصب القوالب، والقولبة بالحقن |
سبيكة النيكل 718 | النيكل، والكروم، والحديد | متانة عالية ومقاومة للتآكل | الفضاء، وتوليد الطاقة، والنفط والغاز، والفضاء، وتوليد الطاقة، والنفط والغاز |
تطبيقات DED
التطبيقات الشائعة لتقنية DED
طلب | الصناعة | المزايا |
---|---|---|
إصلاح المكونات | صناعة الطيران، السيارات | فعالة من حيث التكلفة، وتطيل عمر الأجزاء |
النماذج الأولية | جميع الصناعات | تكرار سريع للتصميم، وتقليل الوقت المستغرق |
الأشكال هندسية معقدة | الطب والفضاء والطيران | تمكّن التصميمات المعقدة والهياكل خفيفة الوزن |
الأجزاء الوظيفية | التصنيع، صناعي | مكونات عالية الأداء ومخصصة حسب الطلب |
الأدوات والقوالب | السيارات، التصنيع | أدوات متينة وعالية الدقة |
البحث عن المواد | أكاديمي، صناعي | خصائص المواد المخصصة، الدراسات التجريبية |
مواصفات ومعايير DED
مواصفات المساحيق المعدنية الشائعة في DED
نموذج المسحوق المعدني | حجم الجسيمات (ميكرومتر) | الكثافة (جم/سم مكعب) | درجة الانصهار (درجة مئوية) | معيار ASTM |
---|---|---|---|---|
انكونيل 625 | 15-45 | 8.44 | 1290-1350 | ASTM B443 |
Ti-6Al-4V | 15-45 | 4.43 | 1604-1660 | ASTM B348 |
فولاذ مقاوم للصدأ 316L | 15-45 | 7.99 | 1375-1400 | ASTM A276 |
هاستيلوي إكس | 15-45 | 8.22 | 1260-1355 | ASTM B435 |
CoCrMo | 15-45 | 8.29 | 1330-1390 | ASTM F75 |
AlSi10 ملغ | 15-45 | 2.67 | 570-580 | ISO 3522 |
فولاذ مارينج (18Ni-300) | 15-45 | 8.00 | 1413 | ASTM A538 |
النحاس | 15-45 | 8.96 | 1083 | ASTM B216 |
فولاذ الأدوات (H13) | 15-45 | 7.80 | 1426 | ASTM A681 |
سبيكة النيكل 718 | 15-45 | 8.19 | 1260-1336 | ASTM B637 |
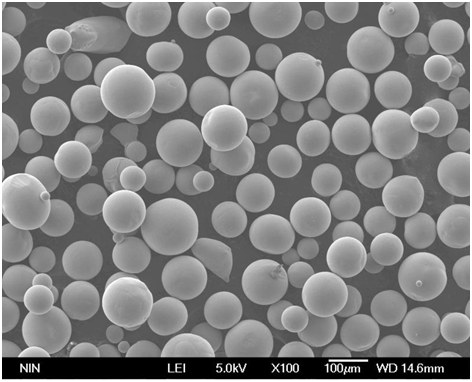
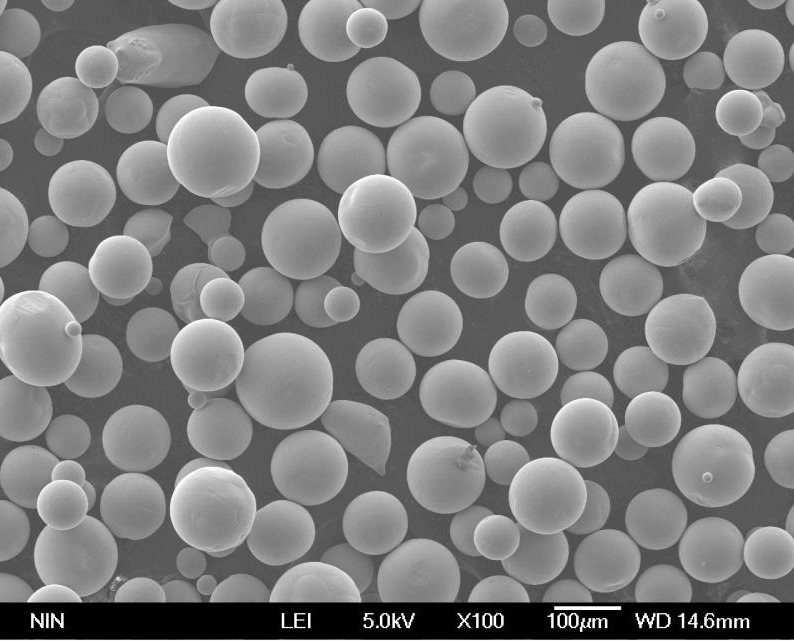
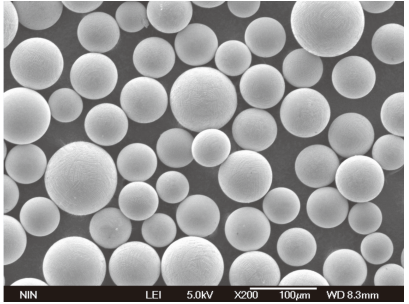
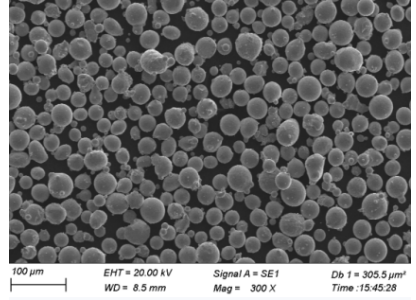
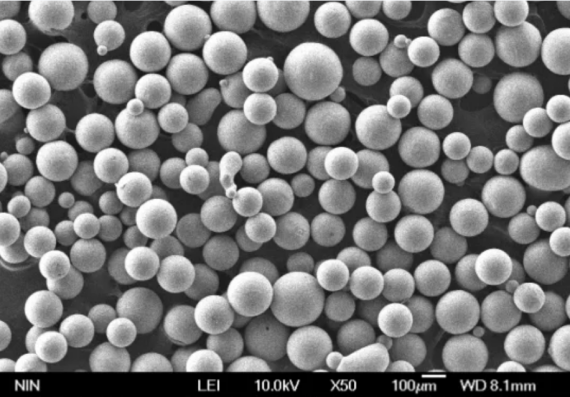
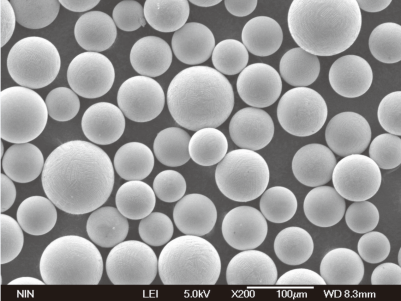
تفاصيل الموردين والأسعار
الموردون وأسعار مساحيق المعادن في DED
المورد | نموذج المسحوق المعدني | سعر الكيلوغرام (بالدولار الأمريكي) | الموقع | اتصل بنا |
---|---|---|---|---|
تكنولوجيا النجار | انكونيل 625 | $100 | الولايات المتحدة الأمريكية | www.carpentertechnology.com |
أركام إيه بي | Ti-6Al-4V | $200 | السويد | www.arcam.com |
GKN Hoeganaes | فولاذ مقاوم للصدأ 316L | $50 | الولايات المتحدة الأمريكية | www.gknpm.com |
إتش سي ستارك | هاستيلوي إكس | $150 | ألمانيا | www.hcstarck.com |
ساندفيك | CoCrMo | $120 | السويد | www.materials.sandvik |
تقنية LPW | AlSi10 ملغ | $80 | المملكة المتحدة | www.lpwtechnology.com |
أوبير ودوفال | فولاذ مارينج (18Ni-300) | $180 | فرنسا | www.aubertduval.com |
تكنا | النحاس | $60 | كندا | www.tekna.com |
هوغاناس إيه بي | فولاذ الأدوات (H13) | $90 | السويد | www.hoganas.com |
VSMPO-AVISMA | سبيكة النيكل 718 | $170 | روسيا | www.vsmpo.ru |
مقارنة إيجابيات تقنية DED وسلبياتها
مزايا تقنية DED ومحدودياتها
أسبكت | مزايا | محددات |
---|---|---|
كفاءة المواد | الحد الأدنى من النفايات، والاستخدام العالي للمواد | ارتفاع التكلفة الأولية للمواد |
الأشكال هندسية معقدة | قادرة على إنشاء تصميمات معقدة | مقيدة بدقة ودقة الماكينة |
قدرات الإصلاح | الإصلاح الفعال للمكونات عالية القيمة | يتطلب مشغلين مهرة وتحكمًا دقيقًا |
سرعة الإنتاج | إنتاج أسرع مقارنة بالطرق التقليدية | أبطأ من بعض طرق التصنيع المضافة الأخرى |
الخواص الميكانيكية | خصائص عالية الأداء وقابلة للتخصيص | احتمالية وجود إجهادات وعيوب متبقية |
تعدد الاستخدامات | يمكن استخدام مجموعة واسعة من المواد | محدودة بتوفر المواد الأولية للمواد الخام |
التحليل التفصيلي للمساحيق المعدنية ل DED
انكونيل 625
إنكونيل 625 عبارة عن سبيكة فائقة أساسها النيكل معروفة بخصائصها الميكانيكية الممتازة ومقاومتها للتآكل، حتى في درجات الحرارة المرتفعة. تشتمل تركيبته على كميات كبيرة من النيكل والكروم والموليبدينوم، والتي تساهم في قوته وثباته. تُعد هذه المادة مثالية للتطبيقات الفضائية والبحرية وتطبيقات المعالجة الكيميائية، حيث يجب أن تتحمل المكونات البيئات القاسية والإجهاد العالي.
Ti-6Al-4V
يُعدّ Ti-6Al-4V، المعروف أيضاً باسم التيتانيوم من الدرجة 5، خياراً شائعاً في صناعة DED نظراً لارتفاع نسبة قوته إلى وزنه وتوافقه الحيوي. وتتألف هذه السبيكة من التيتانيوم والألومنيوم والفاناديوم، وتوفّر خصائص ميكانيكية ممتازة ومقاومة للتآكل، ما يجعلها مناسبة للفضاء والزراعات الطبية ومكونات السيارات.
فولاذ مقاوم للصدأ 316L
الفولاذ المقاوم للصدأ 316L هو فولاذ مقاوم للصدأ الأوستنيتي معروف بمقاومته العالية للتآكل وخصائصه الميكانيكية الجيدة. وتعزز إضافة الموليبدينوم من مقاومته للتآكل، خاصةً ضد الكلوريدات والمذيبات الصناعية الأخرى. يشيع استخدامه في معالجة الأغذية والأجهزة الطبية والتطبيقات البحرية.
هاستيلوي إكس
إن Hastelloy X عبارة عن سبيكة فائقة أساسها النيكل وتتميز بمقاومة فائقة للأكسدة وقوة عالية في درجات الحرارة العالية. تشتمل تركيبته على النيكل والموليبدينوم والكروم، والتي توفر خصائص ميكانيكية ممتازة في درجات الحرارة المرتفعة.
تُستخدم هذه المادة على نطاق واسع في توربينات الغاز الفضائية والصناعية.
CoCrMo
تشتهر سبيكة CoCrMo، أو سبيكة الكوبالت والكروم والموليبدينوم، بمقاومتها الاستثنائية للتآكل وقوتها العالية. تُستخدم هذه المادة بشكل شائع في الغرسات الطبية والأطراف الصناعية للأسنان بسبب توافقها الحيوي ومتانتها.
AlSi10 ملغ
AlSi10Mg عبارة عن سبيكة ألومنيوم ذات توصيل حراري جيد وخصائص خفيفة الوزن. تعمل إضافة السيليكون والمغنيسيوم على تحسين خواصها الميكانيكية، مما يجعلها مناسبة لتطبيقات السيارات والفضاء والإلكترونيات.
فولاذ مارينج (18Ni-300)
فولاذ الماراجينج (18Ni-300) عبارة عن سبيكة فولاذية عالية القوة ذات صلابة ومتانة ممتازة. ويتكون من الحديد والنيكل والكوبالت والموليبدينوم ويستخدم في صناعة الأدوات والفضاء والأجزاء عالية الأداء.
النحاس
يشتهر النحاس بموصلية حرارية وكهربائية ممتازة. في DED، يُستخدم النحاس النقي في المكونات الكهربائية والمبادلات الحرارية والتطبيقات الأخرى التي تتطلب توصيلية عالية.
فولاذ الأدوات (H13)
فولاذ الأدوات H13 عبارة عن فولاذ من الكروم والموليبدينوم والفاناديوم مع صلابة عالية ومقاومة جيدة للتعب الحراري. يُستخدم على نطاق واسع في صناعة الأدوات، وصب القوالب، وتطبيقات القولبة بالحقن.
سبيكة النيكل 718
سبيكة النيكل 718 هي سبيكة نيكل كروم معروفة بقوتها العالية ومقاومتها للتآكل. وتُستخدم عادةً في صناعات الطيران وتوليد الطاقة والنفط والغاز.
مزايا DED
لماذا تختار ترسيب الطاقة الموجهة?
- الكفاءة المادية: تستخدم DED المواد بكفاءة، مما يقلل من النفايات ويحسّن الاستخدام. وعلى عكس طرق الطرح التقليدية، التي غالبًا ما تؤدي إلى فقد كبير في المواد، فإن تقنية DED تضيف المواد فقط عند الحاجة إليها، مما يجعلها خيارًا أكثر استدامة.
- الأشكال الهندسية المعقدة: تسمح هذه التقنية بإنشاء تصميمات معقدة وأشكال هندسية معقدة يصعب أو يستحيل تحقيقها بطرق التصنيع التقليدية. وهذا يفتح إمكانيات جديدة لتصميمات مبتكرة وهياكل خفيفة الوزن.
- قدرات الإصلاح: تُعد تقنية DED فعّالة للغاية في إصلاح المكونات عالية القيمة، مثل شفرات التوربينات وأجزاء الطيران. يمكن أن يؤدي ذلك إلى إطالة عمر هذه المكونات بشكل كبير، مما يقلل من التكاليف ووقت التعطل.
- سرعة الإنتاج: بالمقارنة مع التصنيع التقليدي، يمكن أن تنتج DED الأجزاء بشكل أسرع، خاصةً بالنسبة للمكونات الصغيرة والمتوسطة الحجم. وهذا يقلل من المهل الزمنية ويسمح بإنتاج النماذج الأولية والتكرار السريع.
- الخواص الميكانيكية: وغالبًا ما تتميز الأجزاء التي يتم تصنيعها بتقنية DED بخصائص ميكانيكية فائقة، مثل القوة والمتانة العالية، وذلك بسبب التحكم الدقيق في عملية ترسيب المواد. وينتج عن ذلك قطع عالية الأداء تفي بمعايير الصناعة الصارمة.
- تعدد الاستخدامات: يمكن أن تعمل DED مع مجموعة واسعة من المواد، بما في ذلك المعادن والسيراميك والمواد المركبة. هذا التنوع يجعلها مناسبة لمختلف التطبيقات في العديد من الصناعات.
حدود DED
ما هي تحديات ترسيب الطاقة الموجهة؟
- التكاليف الأولية المرتفعة: يمكن أن يكون الاستثمار الأولي في معدات ومواد التخفيض المعتمد للانبعاثات الكهروضوئية مرتفعًا، وهو ما قد يشكل عائقًا لبعض الشركات. ومع ذلك، غالبًا ما تفوق الفوائد طويلة الأجل هذه التكاليف، خاصة بالنسبة للتطبيقات عالية القيمة.
- دقة ودقة الماكينة: على الرغم من أن تقنية DED يمكنها إنشاء أشكال هندسية معقدة، إلا أنها محدودة بسبب دقة الماكينات ودقة الماكينات. قد يكون تحقيق التفاصيل الدقيقة والتفاوتات الدقيقة أمرًا صعبًا.
- مطلوب مشغلين مهرة: يتطلب تشغيل أنظمة DED مشغلين مهرة يمكنهم التحكم بدقة في عملية الترسيب. وهذا يمكن أن يزيد من التكاليف التشغيلية والتعقيد.
- الضغوط المتبقية المحتملة: يمكن أن تؤدي دورات التسخين والتبريد السريعة في DED إلى ضغوط متبقية وعيوب محتملة في الأجزاء. وتعد تقنيات التحكم السليم في العملية وتقنيات ما بعد المعالجة ضرورية للتخفيف من هذه المشكلات.
- توافر المواد الأولية للمواد الخام: بينما يمكن أن تعمل تقنية DED مع مجموعة واسعة من المواد، إلا أن توافر مواد وسيطة محددة قد يكون محدودًا. وهذا يمكن أن يقيد اختيار المواد لتطبيقات معينة.
- أبطأ من بعض الطرق المضافة: بالمقارنة مع بعض طرق التصنيع المضافة الأخرى، مثل اندماج طبقة المسحوق، يمكن أن تكون تقنية DED أبطأ في بعض التطبيقات. وقد يؤثر ذلك على ملاءمتها للإنتاج بكميات كبيرة.
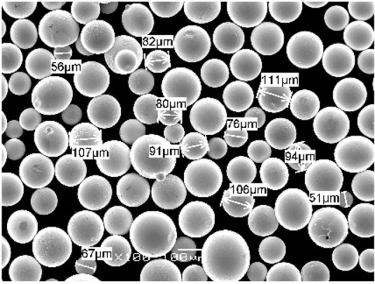
التعليمات
سؤال | الإجابة |
---|---|
ما هو ترسيب الطاقة الموجهة (DED)؟ | الترسيب بالطاقة الموجهة (DED) هي عملية تصنيع مضافة تستخدم الطاقة المركزة لصهر وترسيب المواد، طبقة تلو الأخرى، لإنشاء الأجزاء. |
ما هي المواد التي يمكن استخدامها في DED؟ | يمكن أن تعمل DED مع مجموعة متنوعة من المواد، بما في ذلك المعادن والسيراميك والمواد المركبة. تشمل المعادن الشائعة Inconel 625، وTi-6Al-4V، والفولاذ المقاوم للصدأ 316L، وغيرها. |
ما هي فوائد DED؟ | وتشمل مزايا تقنية DED كفاءة المواد، والقدرة على إنشاء أشكال هندسية معقدة، وقدرات إصلاح فعالة، وسرعات إنتاج سريعة، وقطع عالية الأداء. |
ما هي حدود DED؟ | تشمل القيود التكاليف الأولية المرتفعة، وقيود دقة الماكينة ودقة دقتها والحاجة إلى مشغلين مهرة، والضغوط المتبقية المحتملة، وتوافر المواد الأولية للمواد. |
ما هي الصناعات التي تستخدم DED؟ | تشمل الصناعات التي تستخدم تقنية DED صناعة الطيران والسيارات والطب والطاقة والتصنيع وغيرها. |
كيف يمكن مقارنة DED بطرق التصنيع المضافة الأخرى؟ | توفر تقنية DED مزايا في كفاءة المواد وقدرات الإصلاح ولكنها قد تكون أبطأ وأكثر تكلفة مقارنةً ببعض الطرق المضافة الأخرى مثل دمج طبقة المسحوق. |
هل يمكن لـ DED إصلاح المكونات الموجودة؟ | نعم، إن إزالة التعطيل المستمر للبطاريات فعالة للغاية في إصلاح المكونات الحالية عالية القيمة وإطالة عمرها الافتراضي وتقليل التكاليف. |
هل DED مناسب للإنتاج على نطاق واسع؟ | على الرغم من أن تقنية DED ممتازة للنماذج الأولية والمكونات الصغيرة والمتوسطة الحجم والإصلاحات، إلا أنها قد تكون أقل ملاءمة للإنتاج بكميات كبيرة مقارنة بالطرق الأخرى. |
ما هو مستقبل تكنولوجيا DED؟ | يبدو مستقبل تقنية DED واعدًا، مع التطورات المستمرة في المواد والتحكم في العمليات وقدرات الآلات التي تدفع إلى اعتمادها في مختلف الصناعات. |
كيف يمكنني اختيار المسحوق المعدني المناسب ل DED؟ | ويعتمد اختيار المسحوق المعدني المناسب على متطلبات التطبيق المحددة، مثل الخواص الميكانيكية ومقاومة التآكل والتوافق مع عملية التفكيك القابل للذوبان. يمكن أن يساعد التشاور مع الموردين والخبراء في اتخاذ أفضل خيار. |